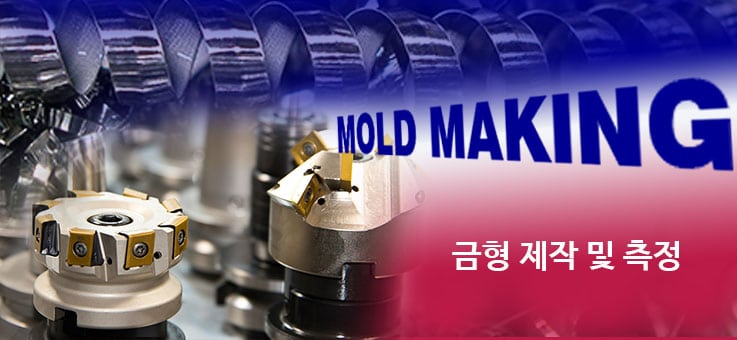
금형 제작 2
제2장 드릴링
1. 드릴의 종류와 특성
(1) 개요
드릴은 드릴링 머신의 주축에 구멍을 뚫는 절삭공구로서 고속도강으로 만들며 절삭날 부분에만 초경합금을 붙인 것도 있음.
드릴은 날 부분과 자루 부분으로 되어 있고 자루부는 직선형인 곧은 자루와 모스 테이퍼로 된 테이퍼 자루가 있음.
곧은 자루 드릴은 Φ13mm 이하의 작은 것으로 드릴 척에 고정하고 드릴 척을 주축 테이퍼 구멍에 꽂아서 사용하며 테이퍼 자루 드릴은 Φ75mm까지의 큰 드릴로 스핀들의 테이퍼 구멍에 꽂아서 사용하고 테이퍼가 맞지 않을 경우에는 슬리브 또는 소켓을 이용함.
(2) 드릴의 종류
1) 트위스트 드릴
나선형의 홈이 2개인 것으로 가장 널리 사용되며 홈이 비틀어져 있어 절삭성이 좋고 칩 배출이 좋음.
2) 특수 드릴
(가) 직선 홈 드릴
직선 홈 드릴은 홈이 직선으로 된 드릴로 선단 끝각이 0˚이므로 절삭성은 떨어지나 황동 등 앏은 판의 구멍 뚫기에 사용됨.
(나) 평 드릴
평 드릴은 절삭날이 납작하여 형태가 간단하고 드릴을 만들기 쉬운 장점이 있으나 트위스트 드릴에 비해 강도가 약하고 칩 제거가 곤란하며 날 끝의 안내가 없어 구멍이 휘어지기 쉽고 정밀도가 떨어지므로 깊은 구멍 속 바닥면의 가공이나 황동 박판의 구멍 뚫기에 사용함.
(다) 센터 드릴
센터 드릴은 선반 등의 가공 시 일감을 센터로 지지할 때 센터의 테이퍼와 동일한 원추각을 가진 구멍을 일감에 가공하기 위해 사용함.
(라) 스텝 드릴
스텝 드릴은 2개의 날을 가진 드릴 선단부를 외경보다 가늘게 하여 2단부를 평면 또는 경사면으로 만든 드릴이며 카운터 보링, 스폿 페이싱에 이용함.
(마) 롱 드릴
롱 드릴은 자루 길이를 길게 하여 주축단으로부터 멀리 떨어진 위치에 구멍을 뚫을 때 사용함.
(마) 셀 드릴
셀 드릴은 드릴의 지름이 생크부의 날부를 별도로 하여 탈착이 가능하도록 한 드릴.
(바) 코어 드릴
코어 드릴은 이미 뚫은 구멍을 넓힐 때 사용함.
3) 심공 드릴
(가) 건 드릴
건 드릴은 비교적 지름이 작은 것(Φ3 ~ Φ20mm)의 깊은 구멍 드릴 가공에 사용되며 절삭유를 드릴에 뚫린 구멍에 통과시키고 헤드 쪽으로 압력을 주어 칩이 드릴 외부의 홈을 따라 절삭유와 함께 배출됨.
(나) BTA 드릴
BTA 드릴은 지름이 큰 것(Φ20 ~ Φ800mm)의 깊은 구멍 드릴 가공에 사용되며 절삭유를 드릴 튜브와 가공되는 구멍 사이로 압송함으로써 칩이 드릴 튜브를 통해 흘러나오게 하는 것임.
(3) 드릴의 각도와 클리어런스
1) 드릴 각도
(가) 드릴 날끝각
드릴의 표준 날끝각은 118˚이며 일감의 경도가 높으면 각도를 크게 하고 경도가 낮으면 각도를 작게 함.
(나) 날 여유각
절삭날이 방해를 받지 않고 재료에 먹어 들어가도록 절삭날에 주어진 각도이고 일반적으로 날 여유각은 12˚ ~ 15˚이며 경도가 큰 니켈강 등의 날 여유각은 10˚ 이하임.
(다) 웨브각
좌우로 등을 대고 있는 2개의 폼 사이 얇은 단면을 웨브라 하며 드릴의 날끝점 직선의 각도 135˚를 표준으로 함.
2) 드릴 클리어런스
(가) 보디 클리어런스
① 정의
뚫어진 구멍의 내면과 드릴 몸체의 마찰을 방지하기 위해서 드릴 선단에서 자루쪽으로 가면서 지름이 조금씩 가늘어지도록 한 것을 보디 클리어런스라 함.
② 클리어런스의 양
클리어런스가 클수록 마찰은 적어지나 너무 커지면 가공 시에 드릴이 흔들리므로 길이 100mm에 대하여 약 0.04 ~ 0.1mm 정도로 함.
드릴 지름 Φ5mm 이하에서는 클리어런스를 주지 않음.
(나) 랜드 클리어런스
드릴의 원주 부분과 뚫린 구멍의 마찰을 일으키지 않도록 클리어런스를 두는데 드릴의 홈에 따라서 앞부분에 좁은 날을 밴드 모양으로 만든 것을 랜드라 하고 랜드 이외의 부분은 가공된 구멍 내면과 접촉이 되지 않도록 깍아내며 이 부분을 랜드 클리어런스라 함.
랜드는 뚫린 구멍의 벽면을 안내로 해서 드릴을 똑바로 진행시키는 역할을 함.
(다) 립 클리어런스
바이트의 여유각과 동일한 성질의 것으로 드릴 선단의 날이 구멍의 바닥 면을 절삭해서 뚫고 들어갈 때 뚫리는 구멍의 바닥면과 드릴의 선단면이 접촉되는 것을 방지하기 위한 것임.
2. 드릴 및 일감의 고정 방법
(1) 개요
드릴은 주축에 고정하여 사용하며 일감은 정확한 드릴링 작업을 위해 테이블 또는 베이스에 정확하고 견고하게 고정함.
동일한 가공이 많고 한 일감에 여러 개의 구멍을 뚫을 때는 드릴을 안내하는 지그를 사용하여 작업하면 신속하고 정확하게 구멍을 뚫을 수 있음.
(2) 드릴 고정 방법
1) 드릴을 직접 주축에 고정하는 방법
드릴 자루부의 테이퍼와 주축의 테이퍼 구멍이 맞을 때 직접 드릴의 자루를 주축에 끼워 고정함.
2) 소켓 또는 슬리브를 사용하는 방법
드릴 자루가 주축 구멍에 맞지 않거나 또는 드릴의 길이가 짧아서 연장시킬 필요가 있을 때 드릴의 테이퍼 자루와 맞는 슬리브 또는 소켓을 주축에 삽입하고 거기에 드릴을 끼워 고정함.
3) 드릴 척을 사용하는 방법
지름이 작은 직선 자루 드릴은 주축에 맞는 드릴 척의 자루를 주축에 꽂아서 고정한 다음 드릴을 척에 고정.
일반적으로 자콥스 드릴 척이 많이 사용됨.
(3) 일감의 고정 방법
1) 고정 구를 사용하는 방법
고정 나사에 의한 고정.
링크, 캠에 의한 고정.
유압, 공압에 의한 고정.
2) 머신 바이스를 사용하는 방법
3) 드릴 지그를 사용하는 방법
3. 드릴의 절삭속도와 이송 및 소요동력
(1) 개요
드릴의 절삭속도는 드릴의 바깥 둘레의 속도로 나타내며 이송은 드릴 1회전마다 드릴이 축 방향으로 이동한 거리로 나타냄.
드릴과 일감의 재질에 따라 알맞은 크기로 해야 하며 드릴 가공이 진행되어 구멍이 깊어지면 칩의 배출이 곤란하므로 절삭속도와 이송은 줄여야 함.
절삭속도는 절삭날의 마모 상태에 따라 경제적인 것이 정해지며 이송속도는 웨브의 마모상태에 따라 정하고 드릴링 시에 공급되는 동력은 주절삭력과 이송에 대한 일에 소비됨.
(2) 절삭속도
탄소 공구강 드릴의 절삭 속도는 고속도강 절삭속도의 40 ~ 50%로 할 것.
(3) 이송
드릴 구멍 깊이가 지름의 3배가 되면 이송과 절삭속도는 10% 정도로 감소시킬 것.
(4) 소요동력
전체 소요동력 N은 드릴링을 위한 정미 소요 동력이고 실제로 드릴링 머신에 공급되는 동력은 손실되는 동력을 더해야 함.
4. 드릴링 머신
(1) 개요
드릴링 머신은 회전하는 주축에 드릴 및 탭 등의 절삭공구를 장치하고 회전시킴과 동시에 상하 운동을 이용하여 구멍을 뚫거나 나사를 가공하는 기계.
(2) 종류
1) 탁상 드릴링 머신
테이블 위에 공작물, 주축에 드릴을 레버로 상하 운동 시켜 구멍을 뚫는 방식으로 기어식과 풀리식이 있음.
소형 모터를 사용한 것을 말하며, 지름 Φ13mm 이하 구멍 뚫기에 사용하며 작은 부품 구멍가공, 태핑 등에 사용됨.
베이스, 칼럼, 헤드, 주축, 테이블로 구성되어 있음.
크기는 가공할 수 있는 구멍의 최대 크기 및 테이블에 설치할 수 있는 공작물의 최대 크기로 나타냄.
2) 레이디얼 드릴링 머신
대형 공작물의 드릴링 가공에 사용됨.
주축 헤드가 암에 설치되어 안내면을 따라 수평 방향으로 이동할 수 있고 암은 칼럼에 끼워져 있어 상하 방향으로 움직이고 회전함.
여러 개의 구멍을 공작물 고정 후 이동 없이 순차적으로 가공이 가능.
수직 구멍만 뚫을 수 있는 보통형(플레인 타입) 과 암과 스핀들 헤드의 선회가 가능하여 경사진 구멍도 뚫을 수 있는 만능형(유니버셜 타입) 등이 있음.
크기는 가공할 수 있는 구멍의 최대 크기와 칼럼의 표면으로부터 주축 중심까지의 최대 거리로 나타냄.
3) 다축 드릴링 머신
구멍 뚫기 작업을 능률적으로 하기 위해 주축의 회전을 여러 개의 스핀들에 전달하는 구조로 되어 있는 드릴링 머신.
여러 개의 구멍을 동시에 가공할 수 있음.
스핀들의 위치는 고정형과 조절형으로 나뉨.
4) 다두 드릴링 머신
직립 드릴링 머신의 상부 기구를 같은 베드 위에 여러 개 나란히 장치한 것과 같은 구조이고 드릴, 리머, 탭 가공 등을 순서에 따라 연속적으로 능률적으로 작업할 수 있음.
5) 드릴 가공의 종류
(가) 드릴링
최초의 구멍을 가공.
(나) 보링
1차 가공된 구멍의 크기를 확대 가공.
(다) 리밍
1차 가공된 구멍 작업 후 정확한 치수로 가공.
(라) 태핑
1차 가공된 구멍의 내면에 암나사를 가공.
(마) 스폿 페이싱
단조나 주조품의 경우 표면이 균일하지 못해 볼트나 너트가 닿는 구멍 주위의 부분만을 평탄하게 가공하여 나사로 체결이 잘 되도록 하는 가공.
(바) 카운터 싱킹
나사 머리의 모양이 접시 모양일 때 테이퍼 원통형으로 절삭하는 가공.
(사) 카운터 보링
볼트 또는 너트의 머리 부분이 가공물 안으로 묻히도록 드릴과 동심원의 2단 구멍을 절삭하는 가공.
5. 드릴의 연삭과 특수 드릴 가공 방법
(1) 개요
드릴 가공 시 절삭에 의해 드릴이 마모되면 절삭능률이 떨어지고 가공면의 정밀도 불량, 드릴 손상 등 많은 문제가 발생되므로 적절한 시기에 재연삭을 시행해야 함.
드릴의 연삭은 손으로 연삭하는 방법과 공구 연삭기로 연삭하는 방법이 있음.
드릴 가공 시에는 드릴 구멍을 뚫을 위치에 금긋기를 하여 구멍의 중심 위치를 정하고 펀치로 중심에 자리를 낸 뒤 드릴을 이 펀치 자리에 맞추어 구멍을 뚫어야 함.
날의 각도가 다른 경우에는 각도가 큰 쪽에서만 절삭이 되어 진직도 불량이 발생하고 날의 좌우 길이가 다른 경우에는 가공된 구멍이 드릴 직경보다 커짐.
(2) 드릴 연삭
1) 드릴 연삭 시 주의사항
절삭날의 길이는 좌우가 동일해야 함.
절삭날의 중심선과 이루는 날끝 반각을 같게 해야 함.
절삭날의 여유각은 일감의 재질에 맞게 해야 함.
2) 시닝
드릴은 생크 쪽으로 갈수록 웨브의 두께가 증가하여 절삭성이 나빠지는데 웨브는 드릴 가공 시 이송을 줄 때 추력이 일어나는 원인이 되며 드릴 연삭 시 웨브의 두께를 처음 두께 상태로 얇게 연삭하는 것을 시닝이라고 함.
(3) 특수 드릴 가공 방법
1) 박판의 드릴 가공
드릴 날끝각이 120˚보다 큰 드릴을 사용하고 드릴의 날끝은 중심과 외주면이 공작물에 동시에 닿도록 만든 특수 드릴을 사용함.
2) 경사 면의 드릴 가공
경사면이나 뾰족한 주물 제품의 정점에 드릴 가공할 때에는 드릴이 미끄러져 작업이 어려우므로 미리 돌출된 평면을 만들어 주거나 평면 자리를 가공한 뒤 구멍을 뚫음.
3) 겹친 구멍의 드릴 가공
1개의 구멍을 뚫고 여기에 같은 종류의 재료를 메운 다음 다른 1개의 구멍을 뚫고 메운 것을 빼내는 가공.
4) 깊은 구멍의 드릴 가공
건 드릴이나 BTA 드릴을 사용하여 총신, 중공 주축, 사출기의 실린더 등을 가공하며 일반 드릴 가공 시에는 절삭유 공급을 충분히 하고 수시로 드릴을 빼내어 칩을 제거하면서 작업을 시행함.
6. 드릴의 파손 및 가공 구멍의 불량 원인
(1) 개요
드릴로 구멍을 뚫을 때 드릴이 부러지거나 날끝이 손상되는 경우가 발생되며 이럴 경우에는 계속적인 작업을 할 수 없게 됨.
또한 드릴, 일감, 드릴링 머신에 의한 요인으로 구멍의 불량이 발생되며 이에 따른 원인을 알고 대책이 강구되어야 함.
(2) 드릴의 파손 현상과 원인
1) 드릴의 파손
구멍에 칩이 너무 충전되어 토크가 과대할 때.
이송이 너무 커서 절삭저항이 과대해질 때.
절삭날이 연삭 불량으로 국부적으로 절삭력이 작용할 때.
일감의 고정이 불량하고 날끝이 예리하지 않을 때.
드릴의 고정 불량.
2) 날끝의 모서리가 강함
일감의 경도가 과도하게 높을 때.
절삭속도가 빠를 때.
절삭유가 불충분할 때.
3) 날끝 직선부의 파손
이송이 지나치게 많을 때.
여유각이 너무 클 때.
(3) 구멍 불량의 현상과 원인
1) 드릴 지름보다 큰 구멍
절삭날의 길이와 각도가 드릴의 중심에 대하여 대칭이 아닐 때.
주축의 베어링 틈새가 과도하게 커서 가공 시 흔들림이 발생할 때.
드릴 고정 시 테이퍼가 정확하지 않을 때.
2) 경사된 구멍
일감의 고정이 불량할 때.
스핀들이 테이블에 대해 직각이 아닐 때.
3) 굽어진 구멍
- 일감의 재질이 불균일하거나 기공이 있으면 절삭저항이 작은 쪽으로 드릴이 굽어져 들어갈 때.
7. 보링 머신에 의한 가공
(1) 개요
보링은 주조할 때 뚫린 구멍이나 드릴로 뚫은 구멍을 깎아서 크게 하거나 정밀도를 높게 하기 위한 가공임.
보링 머신은 보링 바에 바이트를 설치하여 이것을 주축과 같이 회전시키고 주축 또는 공작물을 이송시켜 보링이나 면 깎기 외에 구멍 뚫기, 엔드밀 깍기, 바깥지름 깎기, 나사 깎기, 탭핑 등과 같은 여러 가지 작업을 수행할 수 있음.
(2) 보링 머신의 종류
1) 수평 보링 머신
(가) 특징
수평 보링 머신은 일반적으로 널리 사용되는 것으로서 주축이 수평 방향으로 설치되어 있으며 주축과 구동 장치가 들어 있는 상자형의 주축 헤드가 칼럼에 설치되어 칼럼 안내면을 따라 상하로 이동되며 주축에 보링 바를 끼워 고정함.
(나) 분류
구분 | 용도 |
---|---|
테이블 형 | 보링 가공 및 기계가공 병행, 중형 이하의 가공물 |
플레이너 형 | 중량이 큰 일감의 정밀가공 |
플로어 형 | 테이블형에서 가공이 어려운 대형 일감 |
이동 형 | 이동 작업, 기계 수리용 |
2) 정밀 보링 머신
(가) 특징
고속경 절삭으로 정밀한 보링을 하는 것으로 주로 다이아몬드 또는 초경합금 공구를 사용하며 가공한 구멍과 진원도, 진직도가 매우 높음.
실린더, 베어링 부시, 라이너 등의 다듬질 가공에 사용됨.
(나) 분류
구분 | 형식 |
---|---|
주축 형식 | 수직형, 수평형 |
운동 방식 | 주축 헤드 이동형, 테이블 이동형 |
(다) 지그 보링 머신
- 각종 지그의 제작과 기타 정밀한 구멍 가공을 위한 보링 머신으로서 정밀도가 매우 높으므로 항온실에 설치하며 정밀가공을 위해 나사식 측정장치, 표준봉 게이지, 광학적 측정장치, 다이얼 게이지 등을 갖추고 있음.
3) 보링 머신의 크기
테이블의 크기.
주축의 지름.
주축의 이동 거리.
주축 머리의 상하 이동 거리 및 테이블의 이동 거리.
4) 보링 공구
(가) 보링 바이트
보링 바이트는 선방용 바이트와 거의 같은 구조이나 일반적으로 여러 가지 형태의 보링 바에 직접 나사로 고정하여 사용하는데 큰 구멍에 대해서는 커터를 직접 보링 바에 고정할 수 없으므로 보링 헤드 또는 블록형 커터를 이용하고 여기에 3개 이상의 바이트를 고정해 마멸에 의한 정밀도의 저하를 방지해야 함.
(나) 보링 바
보링 바는 바이트를 고정하여 주축과 보링 바 베어링에 의해서 양단을 지지하고 회전시키면서 공작물에 이송을 주어 구멍을 가공하는 것.
(다) 보링 헤드
지름이 큰 구멍을 가공할 때 바이트 고정이 보링 바로는 어려우므로 보링 헤드에 바이트를 고정하여 보링 바에 끼우고 절삭해야 함.
8. 드릴 지그
(1) 개요
드릴 가공 시 같은 위치에 반복적으로 구멍을 뚫거나 한 일감에 많은 구멍을 뚫을 때 일감에 붙여서 가공할 부분의 위치를 정하거나 공구의 안내를 위하여 사용되는 생산용 특수공구를 지그라 하며 공작물을 설치하는 데 사용되는 고정구와 구별됨.
지그는 일감을 정확하고 확실하게 고정하는 동시에 공구의 절삭운동을 방해하지 않고 정확한 위치로 안내해야 함.
드릴 또는 리머의 지그는 일감을 일정한 위치에 놓고 고정시킨 후 구멍이 뚫어진 위치에 부시가 설치되어 있어 이 부시를 통하여 드릴 작업을 하도록 한 것.
(2) 지그 사용의 효과
작업이 간편해짐.
대량생산을 통해 원가를 절감할 수 있음.
정확한 가공으로 호환성이 보장됨.
(3) 지그 및 부시의 종류
1) 지그
(가) 개방형 지그
개방형 지그는 일감의 한쪽 면에만 구멍을 뚫을 때 사용함.
(나) 밀폐형 지그
밀폐형 지그는 일감의 여러 면에 구멍을 뚫을 때 사용하며 일감은 상자형으로 만든 지그에 나사 또는 지지구로 정확히 고정하도록 되어 있음.
2) 부시
(가) 고정 부시
고정 부시는 지그 본체에 압입하고 일단 고정한 후 제거할 필요가 없을 때 사용함.
고정 부시는 플랜지가 있는 것과 없는 것이 있으며 치수는 KS에 규정되어 있음.
(나) 삽입 부시
삽입 부시는 드릴로 뚫은 구멍을 리머로 다듬질하는 경우와 같이 같은 위치의 구멍을 순차적으로 크게 뚫을 때 그 구멍에 적합한 삽입 부시를 순차적으로 이용함.
삽입 부시는 지그에서 고정과 물림이 쉽게 되나 절삭공구와 부시와의 끼워맞춤 관계가 적절하지 않으면 부시가 회전할 염려가 있으며 이것을 방지하기 위해 노치형 부시를 사용해야 함.
(다) 안내 부시
삽입 부시는 가끔 부시를 끼우거나 풀어야하므로 지그 본체의 구멍이 마멸되기 쉽기 때문에 지그 본체에 안내 부시를 고정하여 사용하고 여기에 삽입 부시를 넣어야 함.
안내 부시는 라이너 부시라고도 하며 플랜지가 있는 것을 사용하기도 함.
(4) 지그의 구성 요소
지그는 위치결정구, 고정장치, 기타 요소인 지그 부시, 일감공급장치, 일감제거장치, 지그 다리 등으로 구성됨.
9. 건 드릴
(1) 개요
심공 드릴링은 일반적으로 구멍 지름 (공구의 지름)의 5배 이상의 깊이로 가공하는 경우를 의미함.
일반적인 드릴 가공은 칩의 배출, 절삭유 공급, 드릴의 휨 등의 문제점으로 인해 심공 드릴링이 어려운데 건 드릴을 이용하면 구멍 지름의 50 ~ 100배의 깊이로 스텝 피드 없이 고정도 고능률로 가공할 수 있음.
(2) 건 드릴의 구조 및 주변 기기
1) 구조
(가) 초경날부
초경날부는 특수한 형상의 초경 1매 날로 되어 있고 외측 절삭날과 내측 절삭날로 되어 있으며 이 두 절삭날에서 나오는 칩이 서로 간섭하여 각각을 전단하고 고압의 냉각수에 의해 칩이 휘감기지 않고 배출됨.
배출되는 칩은 생크부의 V 홈을 통해 쿨런트와 함께 연속적으로 칩 박스로 회수되고 이러한 시스템으로 인해 건 드릴 가공은 스텝 피드 없이 구멍 지름의 50 ~ 100배 정도로 깊은 구멍을 가공할 수 있음.
(나) 생크
생크는 초경날부와 경납땜으로 연결되어 일체를 이루는 부분으로서 회전과 이송을 원활하게 선단의 절삭날 부위로 전달하는 역할을 함.
따라서 생크는 높은 인성과 강도를 필요로 하게 됨.
(다) 드라이버부
드라이버부는 건 드릴을 스핀들에 고정하는 부분으로서 회전과 이송, 냉각수를 스핀들에서 생크와 절삭날부로 전달하는 역할을 함.
절삭날과 안내 패드에 공급되는 냉각수는 순환장치에 의해 가동되며 냉각과 윤활, 칩의 배출 등을 수행함.
드릴링 시에는 절삭저항을 받기 때문에 드릴 헤드 부분에는 안내 패드가 부착되며 안내 패드는 구멍의 내면에 강하게 압착되어 버니싱 효과를 일으켜 드릴 가공면의 표면 거칠기를 향상시킬 수 있음.
2) 건 드릴의 주변 기기
(가) 고회전 및 고압 냉각수 장치
스핀들 회전수는 6000 ~ 12000rpm으로 회전하며 최고 압력 11Mpa의 고압으로 냉각수를 공급.
(나) 칩 배제 및 쿨런트의 여과 냉각 장치
공작물은 칩 박스에 강압하는 상태에서 세팅하고 칩과 냉각수는 칩 박스에서 회수되어 분리되며 1차, 2차 탱크를 거치면서 냉각수의 여과와 냉각이 이루어짐.
(다) 드릴 부시
가공 정밀도를 확보하기 위해 드릴 부시를 설치하는데 부시와 드릴의 클리어런스는 5 ~ 15μm 정도임.
건 드릴은 1매 날이고 구심성이 없기 때문에 센터가 결정될 때까지 드릴 부시를 안내하여 드릴링을 해야 함.
(라) 방진구
가늘고 긴 건 드릴은 고속 회전과 절삭저항에 의해 휨과 진동이 발생할 수 있으며 드릴의 중간부를 지지하는 방진구가 필요함.
(마) 공작물 회전 장치
높은 진직도를 요구하는 가공일 경우 공작물 회전 장치에 의해 공작물을 건 드릴과 반대 방향으로 회전시켜 가공 구멍의 중심 이탈을 30% 정도로 억제할 수 있음.
(3) 건 드릴 가공의 절삭 조건
1) 절삭속도
일반적으로 절삭속도가 증가할수록 가공면의 표면 거칠기가 양호해지는데 고압 다량의 냉각수가 공급되기 때문에 구성인선이 성장하지 않음.
그러나 절삭속도가 너무 크면 공구 수명이 짧아지기 때문에 적절한 절삭속도를 유지해야 함.
2) 이송속도
이송속도가 공구 수명에 미치는 영향은 절삭속도의 영향에 비해 작음.
이송속도가 작을수록 가공면의 표면 거칠기가 향상되지만 알루미늄 가공의 경우에는 고속 이송에서 오히려 표면 거칠기가 향상되는 경향이 있는데 이는 재료의 피삭성이 양호하기 때문에 저속 이송을 하면 드릴의 미세한 진동이 그대로 피삭재에 전달되기 때문임.
(4) 건 드릴의 응용
디젤 엔진의 분사노즐 등 자동차 부품의 가공.
의료기기 및 계측기의 가공.
금형 가공.
10. BTA.(Boring and Trepanning Association System) 드릴
(1) 개요
심공 드릴링으로 건 드릴에 의한 가공과 BTA 방식에 의한 가공으로 크게 나눌 수 있고 차이점은 건 드릴은 Φ3 ~ Φ20mm 정도로 구멍 가공 범위가 작으며 생산성이 낮으나 BTA 드릴은 Φ20 ~ Φ800mm 정도로 비교적 큰 지름의 구멍을 가공하는데 이용함.
(2) 건 드릴과 BTA 드릴의 차이점
건 드릴 방식은 절삭날부의 안내 패드를 가지고 절삭유 분사 방식의 공구인 건 드릴을 사용하여 공구 내부로 절삭유를 공급하나 BTA 드릴 방식은 공구 외부에서 절삭유를 고압으로 분사하여 공구 내부로 절삭유와 칩이 배출되는 방식이며 건 드릴 방식보다 절삭능률이 좋고 비교적 큰 구멍을 가공하는데 적합하며 구멍의 정도, 표면 거칠기, 진직도가 양호하고 일반적으로 직경의 200배 정도까지 가공이 가능함.
(3) BTA 드릴 방식의 가공방법
1) 솔리드 드릴링
한번의 가공으로 소요 구멍을 뚫는 방식으로 보통 Φ150mm까지 가능하나 절삭동력 관계로 Φ65mm 정도가 일반적임.
2) 트레 패닝(TREPANNING)
단일 작업으로 한번에 소요 구멍을 뚫기 힘든 경우 코어를 남기는 방식으로 지름이 큰 구멍을 뚫는데 적합하며 소요동력이 솔리드 드릴링 보다 적게 소요되므로 Φ550mm 정도까지 가공이 가능함.
3) 카운터 보링(COUNTER BORING)
동력에 제한을 받아 한번에 필요한 구멍을 뚫을 수 없을 경우 사용되며 내면을 정밀하게 가공하기 위한 방법.
4) 적용 사례
사출기 등의 유압 실린더, 압연기의 롤러, 공작기계 주축, 선박의 추진축, 자동차와 항공기 부품의 정밀 구멍 가공, 유화 플랜트, 발전소 및 담수 설비 등의 주요 기기인 열교환기의 핵심 부품인 밸브시트 구멍 가공에 적용.
이상으로 절삭 가공 중 드릴링에 대한 연재를 마치고 다음에는 선삭에 대한 연재를 시작할 예정입니다.
2020년 09월 21일
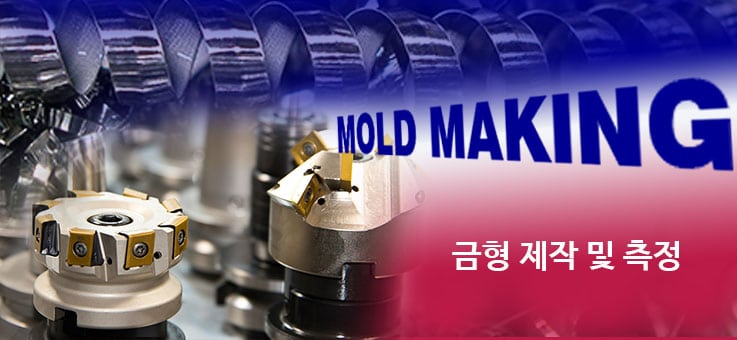
금형 제작 2
제2장 드릴링
1. 드릴의 종류와 특성
(1) 개요
드릴은 드릴링 머신의 주축에 구멍을 뚫는 절삭공구로서 고속도강으로 만들며 절삭날 부분에만 초경합금을 붙인 것도 있음.
드릴은 날 부분과 자루 부분으로 되어 있고 자루부는 직선형인 곧은 자루와 모스 테이퍼로 된 테이퍼 자루가 있음.
곧은 자루 드릴은 Φ13mm 이하의 작은 것으로 드릴 척에 고정하고 드릴 척을 주축 테이퍼 구멍에 꽂아서 사용하며 테이퍼 자루 드릴은 Φ75mm까지의 큰 드릴로 스핀들의 테이퍼 구멍에 꽂아서 사용하고 테이퍼가 맞지 않을 경우에는 슬리브 또는 소켓을 이용함.
(2) 드릴의 종류
1) 트위스트 드릴
나선형의 홈이 2개인 것으로 가장 널리 사용되며 홈이 비틀어져 있어 절삭성이 좋고 칩 배출이 좋음.
2) 특수 드릴
(가) 직선 홈 드릴
직선 홈 드릴은 홈이 직선으로 된 드릴로 선단 끝각이 0˚이므로 절삭성은 떨어지나 황동 등 앏은 판의 구멍 뚫기에 사용됨.
(나) 평 드릴
평 드릴은 절삭날이 납작하여 형태가 간단하고 드릴을 만들기 쉬운 장점이 있으나 트위스트 드릴에 비해 강도가 약하고 칩 제거가 곤란하며 날 끝의 안내가 없어 구멍이 휘어지기 쉽고 정밀도가 떨어지므로 깊은 구멍 속 바닥면의 가공이나 황동 박판의 구멍 뚫기에 사용함.
(다) 센터 드릴
센터 드릴은 선반 등의 가공 시 일감을 센터로 지지할 때 센터의 테이퍼와 동일한 원추각을 가진 구멍을 일감에 가공하기 위해 사용함.
(라) 스텝 드릴
스텝 드릴은 2개의 날을 가진 드릴 선단부를 외경보다 가늘게 하여 2단부를 평면 또는 경사면으로 만든 드릴이며 카운터 보링, 스폿 페이싱에 이용함.
(마) 롱 드릴
롱 드릴은 자루 길이를 길게 하여 주축단으로부터 멀리 떨어진 위치에 구멍을 뚫을 때 사용함.
(마) 셀 드릴
셀 드릴은 드릴의 지름이 생크부의 날부를 별도로 하여 탈착이 가능하도록 한 드릴.
(바) 코어 드릴
코어 드릴은 이미 뚫은 구멍을 넓힐 때 사용함.
3) 심공 드릴
(가) 건 드릴
건 드릴은 비교적 지름이 작은 것(Φ3 ~ Φ20mm)의 깊은 구멍 드릴 가공에 사용되며 절삭유를 드릴에 뚫린 구멍에 통과시키고 헤드 쪽으로 압력을 주어 칩이 드릴 외부의 홈을 따라 절삭유와 함께 배출됨.
(나) BTA 드릴
BTA 드릴은 지름이 큰 것(Φ20 ~ Φ800mm)의 깊은 구멍 드릴 가공에 사용되며 절삭유를 드릴 튜브와 가공되는 구멍 사이로 압송함으로써 칩이 드릴 튜브를 통해 흘러나오게 하는 것임.
(3) 드릴의 각도와 클리어런스
1) 드릴 각도
(가) 드릴 날끝각
드릴의 표준 날끝각은 118˚이며 일감의 경도가 높으면 각도를 크게 하고 경도가 낮으면 각도를 작게 함.
(나) 날 여유각
절삭날이 방해를 받지 않고 재료에 먹어 들어가도록 절삭날에 주어진 각도이고 일반적으로 날 여유각은 12˚ ~ 15˚이며 경도가 큰 니켈강 등의 날 여유각은 10˚ 이하임.
(다) 웨브각
좌우로 등을 대고 있는 2개의 폼 사이 얇은 단면을 웨브라 하며 드릴의 날끝점 직선의 각도 135˚를 표준으로 함.
2) 드릴 클리어런스
(가) 보디 클리어런스
① 정의
뚫어진 구멍의 내면과 드릴 몸체의 마찰을 방지하기 위해서 드릴 선단에서 자루쪽으로 가면서 지름이 조금씩 가늘어지도록 한 것을 보디 클리어런스라 함.
② 클리어런스의 양
클리어런스가 클수록 마찰은 적어지나 너무 커지면 가공 시에 드릴이 흔들리므로 길이 100mm에 대하여 약 0.04 ~ 0.1mm 정도로 함.
드릴 지름 Φ5mm 이하에서는 클리어런스를 주지 않음.
(나) 랜드 클리어런스
드릴의 원주 부분과 뚫린 구멍의 마찰을 일으키지 않도록 클리어런스를 두는데 드릴의 홈에 따라서 앞부분에 좁은 날을 밴드 모양으로 만든 것을 랜드라 하고 랜드 이외의 부분은 가공된 구멍 내면과 접촉이 되지 않도록 깍아내며 이 부분을 랜드 클리어런스라 함.
랜드는 뚫린 구멍의 벽면을 안내로 해서 드릴을 똑바로 진행시키는 역할을 함.
(다) 립 클리어런스
바이트의 여유각과 동일한 성질의 것으로 드릴 선단의 날이 구멍의 바닥 면을 절삭해서 뚫고 들어갈 때 뚫리는 구멍의 바닥면과 드릴의 선단면이 접촉되는 것을 방지하기 위한 것임.
2. 드릴 및 일감의 고정 방법
(1) 개요
드릴은 주축에 고정하여 사용하며 일감은 정확한 드릴링 작업을 위해 테이블 또는 베이스에 정확하고 견고하게 고정함.
동일한 가공이 많고 한 일감에 여러 개의 구멍을 뚫을 때는 드릴을 안내하는 지그를 사용하여 작업하면 신속하고 정확하게 구멍을 뚫을 수 있음.
(2) 드릴 고정 방법
1) 드릴을 직접 주축에 고정하는 방법
드릴 자루부의 테이퍼와 주축의 테이퍼 구멍이 맞을 때 직접 드릴의 자루를 주축에 끼워 고정함.
2) 소켓 또는 슬리브를 사용하는 방법
드릴 자루가 주축 구멍에 맞지 않거나 또는 드릴의 길이가 짧아서 연장시킬 필요가 있을 때 드릴의 테이퍼 자루와 맞는 슬리브 또는 소켓을 주축에 삽입하고 거기에 드릴을 끼워 고정함.
3) 드릴 척을 사용하는 방법
지름이 작은 직선 자루 드릴은 주축에 맞는 드릴 척의 자루를 주축에 꽂아서 고정한 다음 드릴을 척에 고정.
일반적으로 자콥스 드릴 척이 많이 사용됨.
(3) 일감의 고정 방법
1) 고정 구를 사용하는 방법
고정 나사에 의한 고정.
링크, 캠에 의한 고정.
유압, 공압에 의한 고정.
2) 머신 바이스를 사용하는 방법
3) 드릴 지그를 사용하는 방법
3. 드릴의 절삭속도와 이송 및 소요동력
(1) 개요
드릴의 절삭속도는 드릴의 바깥 둘레의 속도로 나타내며 이송은 드릴 1회전마다 드릴이 축 방향으로 이동한 거리로 나타냄.
드릴과 일감의 재질에 따라 알맞은 크기로 해야 하며 드릴 가공이 진행되어 구멍이 깊어지면 칩의 배출이 곤란하므로 절삭속도와 이송은 줄여야 함.
절삭속도는 절삭날의 마모 상태에 따라 경제적인 것이 정해지며 이송속도는 웨브의 마모상태에 따라 정하고 드릴링 시에 공급되는 동력은 주절삭력과 이송에 대한 일에 소비됨.
(2) 절삭속도
탄소 공구강 드릴의 절삭 속도는 고속도강 절삭속도의 40 ~ 50%로 할 것.
(3) 이송
드릴 구멍 깊이가 지름의 3배가 되면 이송과 절삭속도는 10% 정도로 감소시킬 것.
(4) 소요동력
전체 소요동력 N은 드릴링을 위한 정미 소요 동력이고 실제로 드릴링 머신에 공급되는 동력은 손실되는 동력을 더해야 함.
4. 드릴링 머신
(1) 개요
드릴링 머신은 회전하는 주축에 드릴 및 탭 등의 절삭공구를 장치하고 회전시킴과 동시에 상하 운동을 이용하여 구멍을 뚫거나 나사를 가공하는 기계.
(2) 종류
1) 탁상 드릴링 머신
테이블 위에 공작물, 주축에 드릴을 레버로 상하 운동 시켜 구멍을 뚫는 방식으로 기어식과 풀리식이 있음.
소형 모터를 사용한 것을 말하며, 지름 Φ13mm 이하 구멍 뚫기에 사용하며 작은 부품 구멍가공, 태핑 등에 사용됨.
베이스, 칼럼, 헤드, 주축, 테이블로 구성되어 있음.
크기는 가공할 수 있는 구멍의 최대 크기 및 테이블에 설치할 수 있는 공작물의 최대 크기로 나타냄.
2) 레이디얼 드릴링 머신
대형 공작물의 드릴링 가공에 사용됨.
주축 헤드가 암에 설치되어 안내면을 따라 수평 방향으로 이동할 수 있고 암은 칼럼에 끼워져 있어 상하 방향으로 움직이고 회전함.
여러 개의 구멍을 공작물 고정 후 이동 없이 순차적으로 가공이 가능.
수직 구멍만 뚫을 수 있는 보통형(플레인 타입) 과 암과 스핀들 헤드의 선회가 가능하여 경사진 구멍도 뚫을 수 있는 만능형(유니버셜 타입) 등이 있음.
크기는 가공할 수 있는 구멍의 최대 크기와 칼럼의 표면으로부터 주축 중심까지의 최대 거리로 나타냄.
3) 다축 드릴링 머신
구멍 뚫기 작업을 능률적으로 하기 위해 주축의 회전을 여러 개의 스핀들에 전달하는 구조로 되어 있는 드릴링 머신.
여러 개의 구멍을 동시에 가공할 수 있음.
스핀들의 위치는 고정형과 조절형으로 나뉨.
4) 다두 드릴링 머신
직립 드릴링 머신의 상부 기구를 같은 베드 위에 여러 개 나란히 장치한 것과 같은 구조이고 드릴, 리머, 탭 가공 등을 순서에 따라 연속적으로 능률적으로 작업할 수 있음.
5) 드릴 가공의 종류
(가) 드릴링
최초의 구멍을 가공.
(나) 보링
1차 가공된 구멍의 크기를 확대 가공.
(다) 리밍
1차 가공된 구멍 작업 후 정확한 치수로 가공.
(라) 태핑
1차 가공된 구멍의 내면에 암나사를 가공.
(마) 스폿 페이싱
단조나 주조품의 경우 표면이 균일하지 못해 볼트나 너트가 닿는 구멍 주위의 부분만을 평탄하게 가공하여 나사로 체결이 잘 되도록 하는 가공.
(바) 카운터 싱킹
나사 머리의 모양이 접시 모양일 때 테이퍼 원통형으로 절삭하는 가공.
(사) 카운터 보링
볼트 또는 너트의 머리 부분이 가공물 안으로 묻히도록 드릴과 동심원의 2단 구멍을 절삭하는 가공.
5. 드릴의 연삭과 특수 드릴 가공 방법
(1) 개요
드릴 가공 시 절삭에 의해 드릴이 마모되면 절삭능률이 떨어지고 가공면의 정밀도 불량, 드릴 손상 등 많은 문제가 발생되므로 적절한 시기에 재연삭을 시행해야 함.
드릴의 연삭은 손으로 연삭하는 방법과 공구 연삭기로 연삭하는 방법이 있음.
드릴 가공 시에는 드릴 구멍을 뚫을 위치에 금긋기를 하여 구멍의 중심 위치를 정하고 펀치로 중심에 자리를 낸 뒤 드릴을 이 펀치 자리에 맞추어 구멍을 뚫어야 함.
날의 각도가 다른 경우에는 각도가 큰 쪽에서만 절삭이 되어 진직도 불량이 발생하고 날의 좌우 길이가 다른 경우에는 가공된 구멍이 드릴 직경보다 커짐.
(2) 드릴 연삭
1) 드릴 연삭 시 주의사항
절삭날의 길이는 좌우가 동일해야 함.
절삭날의 중심선과 이루는 날끝 반각을 같게 해야 함.
절삭날의 여유각은 일감의 재질에 맞게 해야 함.
2) 시닝
드릴은 생크 쪽으로 갈수록 웨브의 두께가 증가하여 절삭성이 나빠지는데 웨브는 드릴 가공 시 이송을 줄 때 추력이 일어나는 원인이 되며 드릴 연삭 시 웨브의 두께를 처음 두께 상태로 얇게 연삭하는 것을 시닝이라고 함.
(3) 특수 드릴 가공 방법
1) 박판의 드릴 가공
드릴 날끝각이 120˚보다 큰 드릴을 사용하고 드릴의 날끝은 중심과 외주면이 공작물에 동시에 닿도록 만든 특수 드릴을 사용함.
2) 경사 면의 드릴 가공
경사면이나 뾰족한 주물 제품의 정점에 드릴 가공할 때에는 드릴이 미끄러져 작업이 어려우므로 미리 돌출된 평면을 만들어 주거나 평면 자리를 가공한 뒤 구멍을 뚫음.
3) 겹친 구멍의 드릴 가공
1개의 구멍을 뚫고 여기에 같은 종류의 재료를 메운 다음 다른 1개의 구멍을 뚫고 메운 것을 빼내는 가공.
4) 깊은 구멍의 드릴 가공
건 드릴이나 BTA 드릴을 사용하여 총신, 중공 주축, 사출기의 실린더 등을 가공하며 일반 드릴 가공 시에는 절삭유 공급을 충분히 하고 수시로 드릴을 빼내어 칩을 제거하면서 작업을 시행함.
6. 드릴의 파손 및 가공 구멍의 불량 원인
(1) 개요
드릴로 구멍을 뚫을 때 드릴이 부러지거나 날끝이 손상되는 경우가 발생되며 이럴 경우에는 계속적인 작업을 할 수 없게 됨.
또한 드릴, 일감, 드릴링 머신에 의한 요인으로 구멍의 불량이 발생되며 이에 따른 원인을 알고 대책이 강구되어야 함.
(2) 드릴의 파손 현상과 원인
1) 드릴의 파손
구멍에 칩이 너무 충전되어 토크가 과대할 때.
이송이 너무 커서 절삭저항이 과대해질 때.
절삭날이 연삭 불량으로 국부적으로 절삭력이 작용할 때.
일감의 고정이 불량하고 날끝이 예리하지 않을 때.
드릴의 고정 불량.
2) 날끝의 모서리가 강함
일감의 경도가 과도하게 높을 때.
절삭속도가 빠를 때.
절삭유가 불충분할 때.
3) 날끝 직선부의 파손
이송이 지나치게 많을 때.
여유각이 너무 클 때.
(3) 구멍 불량의 현상과 원인
1) 드릴 지름보다 큰 구멍
절삭날의 길이와 각도가 드릴의 중심에 대하여 대칭이 아닐 때.
주축의 베어링 틈새가 과도하게 커서 가공 시 흔들림이 발생할 때.
드릴 고정 시 테이퍼가 정확하지 않을 때.
2) 경사된 구멍
일감의 고정이 불량할 때.
스핀들이 테이블에 대해 직각이 아닐 때.
3) 굽어진 구멍
- 일감의 재질이 불균일하거나 기공이 있으면 절삭저항이 작은 쪽으로 드릴이 굽어져 들어갈 때.
7. 보링 머신에 의한 가공
(1) 개요
보링은 주조할 때 뚫린 구멍이나 드릴로 뚫은 구멍을 깎아서 크게 하거나 정밀도를 높게 하기 위한 가공임.
보링 머신은 보링 바에 바이트를 설치하여 이것을 주축과 같이 회전시키고 주축 또는 공작물을 이송시켜 보링이나 면 깎기 외에 구멍 뚫기, 엔드밀 깍기, 바깥지름 깎기, 나사 깎기, 탭핑 등과 같은 여러 가지 작업을 수행할 수 있음.
(2) 보링 머신의 종류
1) 수평 보링 머신
(가) 특징
수평 보링 머신은 일반적으로 널리 사용되는 것으로서 주축이 수평 방향으로 설치되어 있으며 주축과 구동 장치가 들어 있는 상자형의 주축 헤드가 칼럼에 설치되어 칼럼 안내면을 따라 상하로 이동되며 주축에 보링 바를 끼워 고정함.
(나) 분류
구분 | 용도 |
---|---|
테이블 형 | 보링 가공 및 기계가공 병행, 중형 이하의 가공물 |
플레이너 형 | 중량이 큰 일감의 정밀가공 |
플로어 형 | 테이블형에서 가공이 어려운 대형 일감 |
이동 형 | 이동 작업, 기계 수리용 |
2) 정밀 보링 머신
(가) 특징
고속경 절삭으로 정밀한 보링을 하는 것으로 주로 다이아몬드 또는 초경합금 공구를 사용하며 가공한 구멍과 진원도, 진직도가 매우 높음.
실린더, 베어링 부시, 라이너 등의 다듬질 가공에 사용됨.
(나) 분류
구분 | 형식 |
---|---|
주축 형식 | 수직형, 수평형 |
운동 방식 | 주축 헤드 이동형, 테이블 이동형 |
(다) 지그 보링 머신
- 각종 지그의 제작과 기타 정밀한 구멍 가공을 위한 보링 머신으로서 정밀도가 매우 높으므로 항온실에 설치하며 정밀가공을 위해 나사식 측정장치, 표준봉 게이지, 광학적 측정장치, 다이얼 게이지 등을 갖추고 있음.
3) 보링 머신의 크기
테이블의 크기.
주축의 지름.
주축의 이동 거리.
주축 머리의 상하 이동 거리 및 테이블의 이동 거리.
4) 보링 공구
(가) 보링 바이트
보링 바이트는 선방용 바이트와 거의 같은 구조이나 일반적으로 여러 가지 형태의 보링 바에 직접 나사로 고정하여 사용하는데 큰 구멍에 대해서는 커터를 직접 보링 바에 고정할 수 없으므로 보링 헤드 또는 블록형 커터를 이용하고 여기에 3개 이상의 바이트를 고정해 마멸에 의한 정밀도의 저하를 방지해야 함.
(나) 보링 바
보링 바는 바이트를 고정하여 주축과 보링 바 베어링에 의해서 양단을 지지하고 회전시키면서 공작물에 이송을 주어 구멍을 가공하는 것.
(다) 보링 헤드
지름이 큰 구멍을 가공할 때 바이트 고정이 보링 바로는 어려우므로 보링 헤드에 바이트를 고정하여 보링 바에 끼우고 절삭해야 함.
8. 드릴 지그
(1) 개요
드릴 가공 시 같은 위치에 반복적으로 구멍을 뚫거나 한 일감에 많은 구멍을 뚫을 때 일감에 붙여서 가공할 부분의 위치를 정하거나 공구의 안내를 위하여 사용되는 생산용 특수공구를 지그라 하며 공작물을 설치하는 데 사용되는 고정구와 구별됨.
지그는 일감을 정확하고 확실하게 고정하는 동시에 공구의 절삭운동을 방해하지 않고 정확한 위치로 안내해야 함.
드릴 또는 리머의 지그는 일감을 일정한 위치에 놓고 고정시킨 후 구멍이 뚫어진 위치에 부시가 설치되어 있어 이 부시를 통하여 드릴 작업을 하도록 한 것.
(2) 지그 사용의 효과
작업이 간편해짐.
대량생산을 통해 원가를 절감할 수 있음.
정확한 가공으로 호환성이 보장됨.
(3) 지그 및 부시의 종류
1) 지그
(가) 개방형 지그
개방형 지그는 일감의 한쪽 면에만 구멍을 뚫을 때 사용함.
(나) 밀폐형 지그
밀폐형 지그는 일감의 여러 면에 구멍을 뚫을 때 사용하며 일감은 상자형으로 만든 지그에 나사 또는 지지구로 정확히 고정하도록 되어 있음.
2) 부시
(가) 고정 부시
고정 부시는 지그 본체에 압입하고 일단 고정한 후 제거할 필요가 없을 때 사용함.
고정 부시는 플랜지가 있는 것과 없는 것이 있으며 치수는 KS에 규정되어 있음.
(나) 삽입 부시
삽입 부시는 드릴로 뚫은 구멍을 리머로 다듬질하는 경우와 같이 같은 위치의 구멍을 순차적으로 크게 뚫을 때 그 구멍에 적합한 삽입 부시를 순차적으로 이용함.
삽입 부시는 지그에서 고정과 물림이 쉽게 되나 절삭공구와 부시와의 끼워맞춤 관계가 적절하지 않으면 부시가 회전할 염려가 있으며 이것을 방지하기 위해 노치형 부시를 사용해야 함.
(다) 안내 부시
삽입 부시는 가끔 부시를 끼우거나 풀어야하므로 지그 본체의 구멍이 마멸되기 쉽기 때문에 지그 본체에 안내 부시를 고정하여 사용하고 여기에 삽입 부시를 넣어야 함.
안내 부시는 라이너 부시라고도 하며 플랜지가 있는 것을 사용하기도 함.
(4) 지그의 구성 요소
지그는 위치결정구, 고정장치, 기타 요소인 지그 부시, 일감공급장치, 일감제거장치, 지그 다리 등으로 구성됨.
9. 건 드릴
(1) 개요
심공 드릴링은 일반적으로 구멍 지름 (공구의 지름)의 5배 이상의 깊이로 가공하는 경우를 의미함.
일반적인 드릴 가공은 칩의 배출, 절삭유 공급, 드릴의 휨 등의 문제점으로 인해 심공 드릴링이 어려운데 건 드릴을 이용하면 구멍 지름의 50 ~ 100배의 깊이로 스텝 피드 없이 고정도 고능률로 가공할 수 있음.
(2) 건 드릴의 구조 및 주변 기기
1) 구조
(가) 초경날부
초경날부는 특수한 형상의 초경 1매 날로 되어 있고 외측 절삭날과 내측 절삭날로 되어 있으며 이 두 절삭날에서 나오는 칩이 서로 간섭하여 각각을 전단하고 고압의 냉각수에 의해 칩이 휘감기지 않고 배출됨.
배출되는 칩은 생크부의 V 홈을 통해 쿨런트와 함께 연속적으로 칩 박스로 회수되고 이러한 시스템으로 인해 건 드릴 가공은 스텝 피드 없이 구멍 지름의 50 ~ 100배 정도로 깊은 구멍을 가공할 수 있음.
(나) 생크
생크는 초경날부와 경납땜으로 연결되어 일체를 이루는 부분으로서 회전과 이송을 원활하게 선단의 절삭날 부위로 전달하는 역할을 함.
따라서 생크는 높은 인성과 강도를 필요로 하게 됨.
(다) 드라이버부
드라이버부는 건 드릴을 스핀들에 고정하는 부분으로서 회전과 이송, 냉각수를 스핀들에서 생크와 절삭날부로 전달하는 역할을 함.
절삭날과 안내 패드에 공급되는 냉각수는 순환장치에 의해 가동되며 냉각과 윤활, 칩의 배출 등을 수행함.
드릴링 시에는 절삭저항을 받기 때문에 드릴 헤드 부분에는 안내 패드가 부착되며 안내 패드는 구멍의 내면에 강하게 압착되어 버니싱 효과를 일으켜 드릴 가공면의 표면 거칠기를 향상시킬 수 있음.
2) 건 드릴의 주변 기기
(가) 고회전 및 고압 냉각수 장치
스핀들 회전수는 6000 ~ 12000rpm으로 회전하며 최고 압력 11Mpa의 고압으로 냉각수를 공급.
(나) 칩 배제 및 쿨런트의 여과 냉각 장치
공작물은 칩 박스에 강압하는 상태에서 세팅하고 칩과 냉각수는 칩 박스에서 회수되어 분리되며 1차, 2차 탱크를 거치면서 냉각수의 여과와 냉각이 이루어짐.
(다) 드릴 부시
가공 정밀도를 확보하기 위해 드릴 부시를 설치하는데 부시와 드릴의 클리어런스는 5 ~ 15μm 정도임.
건 드릴은 1매 날이고 구심성이 없기 때문에 센터가 결정될 때까지 드릴 부시를 안내하여 드릴링을 해야 함.
(라) 방진구
가늘고 긴 건 드릴은 고속 회전과 절삭저항에 의해 휨과 진동이 발생할 수 있으며 드릴의 중간부를 지지하는 방진구가 필요함.
(마) 공작물 회전 장치
높은 진직도를 요구하는 가공일 경우 공작물 회전 장치에 의해 공작물을 건 드릴과 반대 방향으로 회전시켜 가공 구멍의 중심 이탈을 30% 정도로 억제할 수 있음.
(3) 건 드릴 가공의 절삭 조건
1) 절삭속도
일반적으로 절삭속도가 증가할수록 가공면의 표면 거칠기가 양호해지는데 고압 다량의 냉각수가 공급되기 때문에 구성인선이 성장하지 않음.
그러나 절삭속도가 너무 크면 공구 수명이 짧아지기 때문에 적절한 절삭속도를 유지해야 함.
2) 이송속도
이송속도가 공구 수명에 미치는 영향은 절삭속도의 영향에 비해 작음.
이송속도가 작을수록 가공면의 표면 거칠기가 향상되지만 알루미늄 가공의 경우에는 고속 이송에서 오히려 표면 거칠기가 향상되는 경향이 있는데 이는 재료의 피삭성이 양호하기 때문에 저속 이송을 하면 드릴의 미세한 진동이 그대로 피삭재에 전달되기 때문임.
(4) 건 드릴의 응용
디젤 엔진의 분사노즐 등 자동차 부품의 가공.
의료기기 및 계측기의 가공.
금형 가공.
10. BTA.(Boring and Trepanning Association System) 드릴
(1) 개요
심공 드릴링으로 건 드릴에 의한 가공과 BTA 방식에 의한 가공으로 크게 나눌 수 있고 차이점은 건 드릴은 Φ3 ~ Φ20mm 정도로 구멍 가공 범위가 작으며 생산성이 낮으나 BTA 드릴은 Φ20 ~ Φ800mm 정도로 비교적 큰 지름의 구멍을 가공하는데 이용함.
(2) 건 드릴과 BTA 드릴의 차이점
건 드릴 방식은 절삭날부의 안내 패드를 가지고 절삭유 분사 방식의 공구인 건 드릴을 사용하여 공구 내부로 절삭유를 공급하나 BTA 드릴 방식은 공구 외부에서 절삭유를 고압으로 분사하여 공구 내부로 절삭유와 칩이 배출되는 방식이며 건 드릴 방식보다 절삭능률이 좋고 비교적 큰 구멍을 가공하는데 적합하며 구멍의 정도, 표면 거칠기, 진직도가 양호하고 일반적으로 직경의 200배 정도까지 가공이 가능함.
(3) BTA 드릴 방식의 가공방법
1) 솔리드 드릴링
한번의 가공으로 소요 구멍을 뚫는 방식으로 보통 Φ150mm까지 가능하나 절삭동력 관계로 Φ65mm 정도가 일반적임.
2) 트레 패닝(TREPANNING)
단일 작업으로 한번에 소요 구멍을 뚫기 힘든 경우 코어를 남기는 방식으로 지름이 큰 구멍을 뚫는데 적합하며 소요동력이 솔리드 드릴링 보다 적게 소요되므로 Φ550mm 정도까지 가공이 가능함.
3) 카운터 보링(COUNTER BORING)
동력에 제한을 받아 한번에 필요한 구멍을 뚫을 수 없을 경우 사용되며 내면을 정밀하게 가공하기 위한 방법.
4) 적용 사례
사출기 등의 유압 실린더, 압연기의 롤러, 공작기계 주축, 선박의 추진축, 자동차와 항공기 부품의 정밀 구멍 가공, 유화 플랜트, 발전소 및 담수 설비 등의 주요 기기인 열교환기의 핵심 부품인 밸브시트 구멍 가공에 적용.
이상으로 절삭 가공 중 드릴링에 대한 연재를 마치고 다음에는 선삭에 대한 연재를 시작할 예정입니다.
2020년 09월 21일
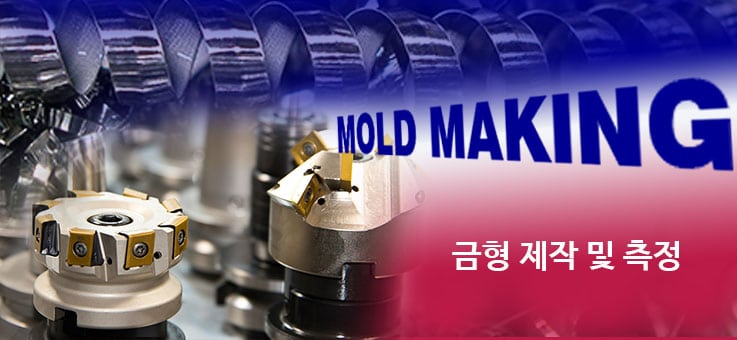
금형 제작 2
제2장 드릴링
1. 드릴의 종류와 특성
(1) 개요
드릴은 드릴링 머신의 주축에 구멍을 뚫는 절삭공구로서 고속도강으로 만들며 절삭날 부분에만 초경합금을 붙인 것도 있음.
드릴은 날 부분과 자루 부분으로 되어 있고 자루부는 직선형인 곧은 자루와 모스 테이퍼로 된 테이퍼 자루가 있음.
곧은 자루 드릴은 Φ13mm 이하의 작은 것으로 드릴 척에 고정하고 드릴 척을 주축 테이퍼 구멍에 꽂아서 사용하며 테이퍼 자루 드릴은 Φ75mm까지의 큰 드릴로 스핀들의 테이퍼 구멍에 꽂아서 사용하고 테이퍼가 맞지 않을 경우에는 슬리브 또는 소켓을 이용함.
(2) 드릴의 종류
1) 트위스트 드릴
나선형의 홈이 2개인 것으로 가장 널리 사용되며 홈이 비틀어져 있어 절삭성이 좋고 칩 배출이 좋음.
2) 특수 드릴
(가) 직선 홈 드릴
직선 홈 드릴은 홈이 직선으로 된 드릴로 선단 끝각이 0˚이므로 절삭성은 떨어지나 황동 등 앏은 판의 구멍 뚫기에 사용됨.
(나) 평 드릴
평 드릴은 절삭날이 납작하여 형태가 간단하고 드릴을 만들기 쉬운 장점이 있으나 트위스트 드릴에 비해 강도가 약하고 칩 제거가 곤란하며 날 끝의 안내가 없어 구멍이 휘어지기 쉽고 정밀도가 떨어지므로 깊은 구멍 속 바닥면의 가공이나 황동 박판의 구멍 뚫기에 사용함.
(다) 센터 드릴
센터 드릴은 선반 등의 가공 시 일감을 센터로 지지할 때 센터의 테이퍼와 동일한 원추각을 가진 구멍을 일감에 가공하기 위해 사용함.
(라) 스텝 드릴
스텝 드릴은 2개의 날을 가진 드릴 선단부를 외경보다 가늘게 하여 2단부를 평면 또는 경사면으로 만든 드릴이며 카운터 보링, 스폿 페이싱에 이용함.
(마) 롱 드릴
롱 드릴은 자루 길이를 길게 하여 주축단으로부터 멀리 떨어진 위치에 구멍을 뚫을 때 사용함.
(마) 셀 드릴
셀 드릴은 드릴의 지름이 생크부의 날부를 별도로 하여 탈착이 가능하도록 한 드릴.
(바) 코어 드릴
코어 드릴은 이미 뚫은 구멍을 넓힐 때 사용함.
3) 심공 드릴
(가) 건 드릴
건 드릴은 비교적 지름이 작은 것(Φ3 ~ Φ20mm)의 깊은 구멍 드릴 가공에 사용되며 절삭유를 드릴에 뚫린 구멍에 통과시키고 헤드 쪽으로 압력을 주어 칩이 드릴 외부의 홈을 따라 절삭유와 함께 배출됨.
(나) BTA 드릴
BTA 드릴은 지름이 큰 것(Φ20 ~ Φ800mm)의 깊은 구멍 드릴 가공에 사용되며 절삭유를 드릴 튜브와 가공되는 구멍 사이로 압송함으로써 칩이 드릴 튜브를 통해 흘러나오게 하는 것임.
(3) 드릴의 각도와 클리어런스
1) 드릴 각도
(가) 드릴 날끝각
드릴의 표준 날끝각은 118˚이며 일감의 경도가 높으면 각도를 크게 하고 경도가 낮으면 각도를 작게 함.
(나) 날 여유각
절삭날이 방해를 받지 않고 재료에 먹어 들어가도록 절삭날에 주어진 각도이고 일반적으로 날 여유각은 12˚ ~ 15˚이며 경도가 큰 니켈강 등의 날 여유각은 10˚ 이하임.
(다) 웨브각
좌우로 등을 대고 있는 2개의 폼 사이 얇은 단면을 웨브라 하며 드릴의 날끝점 직선의 각도 135˚를 표준으로 함.
2) 드릴 클리어런스
(가) 보디 클리어런스
① 정의
뚫어진 구멍의 내면과 드릴 몸체의 마찰을 방지하기 위해서 드릴 선단에서 자루쪽으로 가면서 지름이 조금씩 가늘어지도록 한 것을 보디 클리어런스라 함.
② 클리어런스의 양
클리어런스가 클수록 마찰은 적어지나 너무 커지면 가공 시에 드릴이 흔들리므로 길이 100mm에 대하여 약 0.04 ~ 0.1mm 정도로 함.
드릴 지름 Φ5mm 이하에서는 클리어런스를 주지 않음.
(나) 랜드 클리어런스
드릴의 원주 부분과 뚫린 구멍의 마찰을 일으키지 않도록 클리어런스를 두는데 드릴의 홈에 따라서 앞부분에 좁은 날을 밴드 모양으로 만든 것을 랜드라 하고 랜드 이외의 부분은 가공된 구멍 내면과 접촉이 되지 않도록 깍아내며 이 부분을 랜드 클리어런스라 함.
랜드는 뚫린 구멍의 벽면을 안내로 해서 드릴을 똑바로 진행시키는 역할을 함.
(다) 립 클리어런스
바이트의 여유각과 동일한 성질의 것으로 드릴 선단의 날이 구멍의 바닥 면을 절삭해서 뚫고 들어갈 때 뚫리는 구멍의 바닥면과 드릴의 선단면이 접촉되는 것을 방지하기 위한 것임.
2. 드릴 및 일감의 고정 방법
(1) 개요
드릴은 주축에 고정하여 사용하며 일감은 정확한 드릴링 작업을 위해 테이블 또는 베이스에 정확하고 견고하게 고정함.
동일한 가공이 많고 한 일감에 여러 개의 구멍을 뚫을 때는 드릴을 안내하는 지그를 사용하여 작업하면 신속하고 정확하게 구멍을 뚫을 수 있음.
(2) 드릴 고정 방법
1) 드릴을 직접 주축에 고정하는 방법
드릴 자루부의 테이퍼와 주축의 테이퍼 구멍이 맞을 때 직접 드릴의 자루를 주축에 끼워 고정함.
2) 소켓 또는 슬리브를 사용하는 방법
드릴 자루가 주축 구멍에 맞지 않거나 또는 드릴의 길이가 짧아서 연장시킬 필요가 있을 때 드릴의 테이퍼 자루와 맞는 슬리브 또는 소켓을 주축에 삽입하고 거기에 드릴을 끼워 고정함.
3) 드릴 척을 사용하는 방법
지름이 작은 직선 자루 드릴은 주축에 맞는 드릴 척의 자루를 주축에 꽂아서 고정한 다음 드릴을 척에 고정.
일반적으로 자콥스 드릴 척이 많이 사용됨.
(3) 일감의 고정 방법
1) 고정 구를 사용하는 방법
고정 나사에 의한 고정.
링크, 캠에 의한 고정.
유압, 공압에 의한 고정.
2) 머신 바이스를 사용하는 방법
3) 드릴 지그를 사용하는 방법
3. 드릴의 절삭속도와 이송 및 소요동력
(1) 개요
드릴의 절삭속도는 드릴의 바깥 둘레의 속도로 나타내며 이송은 드릴 1회전마다 드릴이 축 방향으로 이동한 거리로 나타냄.
드릴과 일감의 재질에 따라 알맞은 크기로 해야 하며 드릴 가공이 진행되어 구멍이 깊어지면 칩의 배출이 곤란하므로 절삭속도와 이송은 줄여야 함.
절삭속도는 절삭날의 마모 상태에 따라 경제적인 것이 정해지며 이송속도는 웨브의 마모상태에 따라 정하고 드릴링 시에 공급되는 동력은 주절삭력과 이송에 대한 일에 소비됨.
(2) 절삭속도
탄소 공구강 드릴의 절삭 속도는 고속도강 절삭속도의 40 ~ 50%로 할 것.
(3) 이송
드릴 구멍 깊이가 지름의 3배가 되면 이송과 절삭속도는 10% 정도로 감소시킬 것.
(4) 소요동력
전체 소요동력 N은 드릴링을 위한 정미 소요 동력이고 실제로 드릴링 머신에 공급되는 동력은 손실되는 동력을 더해야 함.
4. 드릴링 머신
(1) 개요
드릴링 머신은 회전하는 주축에 드릴 및 탭 등의 절삭공구를 장치하고 회전시킴과 동시에 상하 운동을 이용하여 구멍을 뚫거나 나사를 가공하는 기계.
(2) 종류
1) 탁상 드릴링 머신
테이블 위에 공작물, 주축에 드릴을 레버로 상하 운동 시켜 구멍을 뚫는 방식으로 기어식과 풀리식이 있음.
소형 모터를 사용한 것을 말하며, 지름 Φ13mm 이하 구멍 뚫기에 사용하며 작은 부품 구멍가공, 태핑 등에 사용됨.
베이스, 칼럼, 헤드, 주축, 테이블로 구성되어 있음.
크기는 가공할 수 있는 구멍의 최대 크기 및 테이블에 설치할 수 있는 공작물의 최대 크기로 나타냄.
2) 레이디얼 드릴링 머신
대형 공작물의 드릴링 가공에 사용됨.
주축 헤드가 암에 설치되어 안내면을 따라 수평 방향으로 이동할 수 있고 암은 칼럼에 끼워져 있어 상하 방향으로 움직이고 회전함.
여러 개의 구멍을 공작물 고정 후 이동 없이 순차적으로 가공이 가능.
수직 구멍만 뚫을 수 있는 보통형(플레인 타입) 과 암과 스핀들 헤드의 선회가 가능하여 경사진 구멍도 뚫을 수 있는 만능형(유니버셜 타입) 등이 있음.
크기는 가공할 수 있는 구멍의 최대 크기와 칼럼의 표면으로부터 주축 중심까지의 최대 거리로 나타냄.
3) 다축 드릴링 머신
구멍 뚫기 작업을 능률적으로 하기 위해 주축의 회전을 여러 개의 스핀들에 전달하는 구조로 되어 있는 드릴링 머신.
여러 개의 구멍을 동시에 가공할 수 있음.
스핀들의 위치는 고정형과 조절형으로 나뉨.
4) 다두 드릴링 머신
직립 드릴링 머신의 상부 기구를 같은 베드 위에 여러 개 나란히 장치한 것과 같은 구조이고 드릴, 리머, 탭 가공 등을 순서에 따라 연속적으로 능률적으로 작업할 수 있음.
5) 드릴 가공의 종류
(가) 드릴링
최초의 구멍을 가공.
(나) 보링
1차 가공된 구멍의 크기를 확대 가공.
(다) 리밍
1차 가공된 구멍 작업 후 정확한 치수로 가공.
(라) 태핑
1차 가공된 구멍의 내면에 암나사를 가공.
(마) 스폿 페이싱
단조나 주조품의 경우 표면이 균일하지 못해 볼트나 너트가 닿는 구멍 주위의 부분만을 평탄하게 가공하여 나사로 체결이 잘 되도록 하는 가공.
(바) 카운터 싱킹
나사 머리의 모양이 접시 모양일 때 테이퍼 원통형으로 절삭하는 가공.
(사) 카운터 보링
볼트 또는 너트의 머리 부분이 가공물 안으로 묻히도록 드릴과 동심원의 2단 구멍을 절삭하는 가공.
5. 드릴의 연삭과 특수 드릴 가공 방법
(1) 개요
드릴 가공 시 절삭에 의해 드릴이 마모되면 절삭능률이 떨어지고 가공면의 정밀도 불량, 드릴 손상 등 많은 문제가 발생되므로 적절한 시기에 재연삭을 시행해야 함.
드릴의 연삭은 손으로 연삭하는 방법과 공구 연삭기로 연삭하는 방법이 있음.
드릴 가공 시에는 드릴 구멍을 뚫을 위치에 금긋기를 하여 구멍의 중심 위치를 정하고 펀치로 중심에 자리를 낸 뒤 드릴을 이 펀치 자리에 맞추어 구멍을 뚫어야 함.
날의 각도가 다른 경우에는 각도가 큰 쪽에서만 절삭이 되어 진직도 불량이 발생하고 날의 좌우 길이가 다른 경우에는 가공된 구멍이 드릴 직경보다 커짐.
(2) 드릴 연삭
1) 드릴 연삭 시 주의사항
절삭날의 길이는 좌우가 동일해야 함.
절삭날의 중심선과 이루는 날끝 반각을 같게 해야 함.
절삭날의 여유각은 일감의 재질에 맞게 해야 함.
2) 시닝
드릴은 생크 쪽으로 갈수록 웨브의 두께가 증가하여 절삭성이 나빠지는데 웨브는 드릴 가공 시 이송을 줄 때 추력이 일어나는 원인이 되며 드릴 연삭 시 웨브의 두께를 처음 두께 상태로 얇게 연삭하는 것을 시닝이라고 함.
(3) 특수 드릴 가공 방법
1) 박판의 드릴 가공
드릴 날끝각이 120˚보다 큰 드릴을 사용하고 드릴의 날끝은 중심과 외주면이 공작물에 동시에 닿도록 만든 특수 드릴을 사용함.
2) 경사 면의 드릴 가공
경사면이나 뾰족한 주물 제품의 정점에 드릴 가공할 때에는 드릴이 미끄러져 작업이 어려우므로 미리 돌출된 평면을 만들어 주거나 평면 자리를 가공한 뒤 구멍을 뚫음.
3) 겹친 구멍의 드릴 가공
1개의 구멍을 뚫고 여기에 같은 종류의 재료를 메운 다음 다른 1개의 구멍을 뚫고 메운 것을 빼내는 가공.
4) 깊은 구멍의 드릴 가공
건 드릴이나 BTA 드릴을 사용하여 총신, 중공 주축, 사출기의 실린더 등을 가공하며 일반 드릴 가공 시에는 절삭유 공급을 충분히 하고 수시로 드릴을 빼내어 칩을 제거하면서 작업을 시행함.
6. 드릴의 파손 및 가공 구멍의 불량 원인
(1) 개요
드릴로 구멍을 뚫을 때 드릴이 부러지거나 날끝이 손상되는 경우가 발생되며 이럴 경우에는 계속적인 작업을 할 수 없게 됨.
또한 드릴, 일감, 드릴링 머신에 의한 요인으로 구멍의 불량이 발생되며 이에 따른 원인을 알고 대책이 강구되어야 함.
(2) 드릴의 파손 현상과 원인
1) 드릴의 파손
구멍에 칩이 너무 충전되어 토크가 과대할 때.
이송이 너무 커서 절삭저항이 과대해질 때.
절삭날이 연삭 불량으로 국부적으로 절삭력이 작용할 때.
일감의 고정이 불량하고 날끝이 예리하지 않을 때.
드릴의 고정 불량.
2) 날끝의 모서리가 강함
일감의 경도가 과도하게 높을 때.
절삭속도가 빠를 때.
절삭유가 불충분할 때.
3) 날끝 직선부의 파손
이송이 지나치게 많을 때.
여유각이 너무 클 때.
(3) 구멍 불량의 현상과 원인
1) 드릴 지름보다 큰 구멍
절삭날의 길이와 각도가 드릴의 중심에 대하여 대칭이 아닐 때.
주축의 베어링 틈새가 과도하게 커서 가공 시 흔들림이 발생할 때.
드릴 고정 시 테이퍼가 정확하지 않을 때.
2) 경사된 구멍
일감의 고정이 불량할 때.
스핀들이 테이블에 대해 직각이 아닐 때.
3) 굽어진 구멍
- 일감의 재질이 불균일하거나 기공이 있으면 절삭저항이 작은 쪽으로 드릴이 굽어져 들어갈 때.
7. 보링 머신에 의한 가공
(1) 개요
보링은 주조할 때 뚫린 구멍이나 드릴로 뚫은 구멍을 깎아서 크게 하거나 정밀도를 높게 하기 위한 가공임.
보링 머신은 보링 바에 바이트를 설치하여 이것을 주축과 같이 회전시키고 주축 또는 공작물을 이송시켜 보링이나 면 깎기 외에 구멍 뚫기, 엔드밀 깍기, 바깥지름 깎기, 나사 깎기, 탭핑 등과 같은 여러 가지 작업을 수행할 수 있음.
(2) 보링 머신의 종류
1) 수평 보링 머신
(가) 특징
수평 보링 머신은 일반적으로 널리 사용되는 것으로서 주축이 수평 방향으로 설치되어 있으며 주축과 구동 장치가 들어 있는 상자형의 주축 헤드가 칼럼에 설치되어 칼럼 안내면을 따라 상하로 이동되며 주축에 보링 바를 끼워 고정함.
(나) 분류
구분 | 용도 |
---|---|
테이블 형 | 보링 가공 및 기계가공 병행, 중형 이하의 가공물 |
플레이너 형 | 중량이 큰 일감의 정밀가공 |
플로어 형 | 테이블형에서 가공이 어려운 대형 일감 |
이동 형 | 이동 작업, 기계 수리용 |
2) 정밀 보링 머신
(가) 특징
고속경 절삭으로 정밀한 보링을 하는 것으로 주로 다이아몬드 또는 초경합금 공구를 사용하며 가공한 구멍과 진원도, 진직도가 매우 높음.
실린더, 베어링 부시, 라이너 등의 다듬질 가공에 사용됨.
(나) 분류
구분 | 형식 |
---|---|
주축 형식 | 수직형, 수평형 |
운동 방식 | 주축 헤드 이동형, 테이블 이동형 |
(다) 지그 보링 머신
- 각종 지그의 제작과 기타 정밀한 구멍 가공을 위한 보링 머신으로서 정밀도가 매우 높으므로 항온실에 설치하며 정밀가공을 위해 나사식 측정장치, 표준봉 게이지, 광학적 측정장치, 다이얼 게이지 등을 갖추고 있음.
3) 보링 머신의 크기
테이블의 크기.
주축의 지름.
주축의 이동 거리.
주축 머리의 상하 이동 거리 및 테이블의 이동 거리.
4) 보링 공구
(가) 보링 바이트
보링 바이트는 선방용 바이트와 거의 같은 구조이나 일반적으로 여러 가지 형태의 보링 바에 직접 나사로 고정하여 사용하는데 큰 구멍에 대해서는 커터를 직접 보링 바에 고정할 수 없으므로 보링 헤드 또는 블록형 커터를 이용하고 여기에 3개 이상의 바이트를 고정해 마멸에 의한 정밀도의 저하를 방지해야 함.
(나) 보링 바
보링 바는 바이트를 고정하여 주축과 보링 바 베어링에 의해서 양단을 지지하고 회전시키면서 공작물에 이송을 주어 구멍을 가공하는 것.
(다) 보링 헤드
지름이 큰 구멍을 가공할 때 바이트 고정이 보링 바로는 어려우므로 보링 헤드에 바이트를 고정하여 보링 바에 끼우고 절삭해야 함.
8. 드릴 지그
(1) 개요
드릴 가공 시 같은 위치에 반복적으로 구멍을 뚫거나 한 일감에 많은 구멍을 뚫을 때 일감에 붙여서 가공할 부분의 위치를 정하거나 공구의 안내를 위하여 사용되는 생산용 특수공구를 지그라 하며 공작물을 설치하는 데 사용되는 고정구와 구별됨.
지그는 일감을 정확하고 확실하게 고정하는 동시에 공구의 절삭운동을 방해하지 않고 정확한 위치로 안내해야 함.
드릴 또는 리머의 지그는 일감을 일정한 위치에 놓고 고정시킨 후 구멍이 뚫어진 위치에 부시가 설치되어 있어 이 부시를 통하여 드릴 작업을 하도록 한 것.
(2) 지그 사용의 효과
작업이 간편해짐.
대량생산을 통해 원가를 절감할 수 있음.
정확한 가공으로 호환성이 보장됨.
(3) 지그 및 부시의 종류
1) 지그
(가) 개방형 지그
개방형 지그는 일감의 한쪽 면에만 구멍을 뚫을 때 사용함.
(나) 밀폐형 지그
밀폐형 지그는 일감의 여러 면에 구멍을 뚫을 때 사용하며 일감은 상자형으로 만든 지그에 나사 또는 지지구로 정확히 고정하도록 되어 있음.
2) 부시
(가) 고정 부시
고정 부시는 지그 본체에 압입하고 일단 고정한 후 제거할 필요가 없을 때 사용함.
고정 부시는 플랜지가 있는 것과 없는 것이 있으며 치수는 KS에 규정되어 있음.
(나) 삽입 부시
삽입 부시는 드릴로 뚫은 구멍을 리머로 다듬질하는 경우와 같이 같은 위치의 구멍을 순차적으로 크게 뚫을 때 그 구멍에 적합한 삽입 부시를 순차적으로 이용함.
삽입 부시는 지그에서 고정과 물림이 쉽게 되나 절삭공구와 부시와의 끼워맞춤 관계가 적절하지 않으면 부시가 회전할 염려가 있으며 이것을 방지하기 위해 노치형 부시를 사용해야 함.
(다) 안내 부시
삽입 부시는 가끔 부시를 끼우거나 풀어야하므로 지그 본체의 구멍이 마멸되기 쉽기 때문에 지그 본체에 안내 부시를 고정하여 사용하고 여기에 삽입 부시를 넣어야 함.
안내 부시는 라이너 부시라고도 하며 플랜지가 있는 것을 사용하기도 함.
(4) 지그의 구성 요소
지그는 위치결정구, 고정장치, 기타 요소인 지그 부시, 일감공급장치, 일감제거장치, 지그 다리 등으로 구성됨.
9. 건 드릴
(1) 개요
심공 드릴링은 일반적으로 구멍 지름 (공구의 지름)의 5배 이상의 깊이로 가공하는 경우를 의미함.
일반적인 드릴 가공은 칩의 배출, 절삭유 공급, 드릴의 휨 등의 문제점으로 인해 심공 드릴링이 어려운데 건 드릴을 이용하면 구멍 지름의 50 ~ 100배의 깊이로 스텝 피드 없이 고정도 고능률로 가공할 수 있음.
(2) 건 드릴의 구조 및 주변 기기
1) 구조
(가) 초경날부
초경날부는 특수한 형상의 초경 1매 날로 되어 있고 외측 절삭날과 내측 절삭날로 되어 있으며 이 두 절삭날에서 나오는 칩이 서로 간섭하여 각각을 전단하고 고압의 냉각수에 의해 칩이 휘감기지 않고 배출됨.
배출되는 칩은 생크부의 V 홈을 통해 쿨런트와 함께 연속적으로 칩 박스로 회수되고 이러한 시스템으로 인해 건 드릴 가공은 스텝 피드 없이 구멍 지름의 50 ~ 100배 정도로 깊은 구멍을 가공할 수 있음.
(나) 생크
생크는 초경날부와 경납땜으로 연결되어 일체를 이루는 부분으로서 회전과 이송을 원활하게 선단의 절삭날 부위로 전달하는 역할을 함.
따라서 생크는 높은 인성과 강도를 필요로 하게 됨.
(다) 드라이버부
드라이버부는 건 드릴을 스핀들에 고정하는 부분으로서 회전과 이송, 냉각수를 스핀들에서 생크와 절삭날부로 전달하는 역할을 함.
절삭날과 안내 패드에 공급되는 냉각수는 순환장치에 의해 가동되며 냉각과 윤활, 칩의 배출 등을 수행함.
드릴링 시에는 절삭저항을 받기 때문에 드릴 헤드 부분에는 안내 패드가 부착되며 안내 패드는 구멍의 내면에 강하게 압착되어 버니싱 효과를 일으켜 드릴 가공면의 표면 거칠기를 향상시킬 수 있음.
2) 건 드릴의 주변 기기
(가) 고회전 및 고압 냉각수 장치
스핀들 회전수는 6000 ~ 12000rpm으로 회전하며 최고 압력 11Mpa의 고압으로 냉각수를 공급.
(나) 칩 배제 및 쿨런트의 여과 냉각 장치
공작물은 칩 박스에 강압하는 상태에서 세팅하고 칩과 냉각수는 칩 박스에서 회수되어 분리되며 1차, 2차 탱크를 거치면서 냉각수의 여과와 냉각이 이루어짐.
(다) 드릴 부시
가공 정밀도를 확보하기 위해 드릴 부시를 설치하는데 부시와 드릴의 클리어런스는 5 ~ 15μm 정도임.
건 드릴은 1매 날이고 구심성이 없기 때문에 센터가 결정될 때까지 드릴 부시를 안내하여 드릴링을 해야 함.
(라) 방진구
가늘고 긴 건 드릴은 고속 회전과 절삭저항에 의해 휨과 진동이 발생할 수 있으며 드릴의 중간부를 지지하는 방진구가 필요함.
(마) 공작물 회전 장치
높은 진직도를 요구하는 가공일 경우 공작물 회전 장치에 의해 공작물을 건 드릴과 반대 방향으로 회전시켜 가공 구멍의 중심 이탈을 30% 정도로 억제할 수 있음.
(3) 건 드릴 가공의 절삭 조건
1) 절삭속도
일반적으로 절삭속도가 증가할수록 가공면의 표면 거칠기가 양호해지는데 고압 다량의 냉각수가 공급되기 때문에 구성인선이 성장하지 않음.
그러나 절삭속도가 너무 크면 공구 수명이 짧아지기 때문에 적절한 절삭속도를 유지해야 함.
2) 이송속도
이송속도가 공구 수명에 미치는 영향은 절삭속도의 영향에 비해 작음.
이송속도가 작을수록 가공면의 표면 거칠기가 향상되지만 알루미늄 가공의 경우에는 고속 이송에서 오히려 표면 거칠기가 향상되는 경향이 있는데 이는 재료의 피삭성이 양호하기 때문에 저속 이송을 하면 드릴의 미세한 진동이 그대로 피삭재에 전달되기 때문임.
(4) 건 드릴의 응용
디젤 엔진의 분사노즐 등 자동차 부품의 가공.
의료기기 및 계측기의 가공.
금형 가공.
10. BTA.(Boring and Trepanning Association System) 드릴
(1) 개요
심공 드릴링으로 건 드릴에 의한 가공과 BTA 방식에 의한 가공으로 크게 나눌 수 있고 차이점은 건 드릴은 Φ3 ~ Φ20mm 정도로 구멍 가공 범위가 작으며 생산성이 낮으나 BTA 드릴은 Φ20 ~ Φ800mm 정도로 비교적 큰 지름의 구멍을 가공하는데 이용함.
(2) 건 드릴과 BTA 드릴의 차이점
건 드릴 방식은 절삭날부의 안내 패드를 가지고 절삭유 분사 방식의 공구인 건 드릴을 사용하여 공구 내부로 절삭유를 공급하나 BTA 드릴 방식은 공구 외부에서 절삭유를 고압으로 분사하여 공구 내부로 절삭유와 칩이 배출되는 방식이며 건 드릴 방식보다 절삭능률이 좋고 비교적 큰 구멍을 가공하는데 적합하며 구멍의 정도, 표면 거칠기, 진직도가 양호하고 일반적으로 직경의 200배 정도까지 가공이 가능함.
(3) BTA 드릴 방식의 가공방법
1) 솔리드 드릴링
한번의 가공으로 소요 구멍을 뚫는 방식으로 보통 Φ150mm까지 가능하나 절삭동력 관계로 Φ65mm 정도가 일반적임.
2) 트레 패닝(TREPANNING)
단일 작업으로 한번에 소요 구멍을 뚫기 힘든 경우 코어를 남기는 방식으로 지름이 큰 구멍을 뚫는데 적합하며 소요동력이 솔리드 드릴링 보다 적게 소요되므로 Φ550mm 정도까지 가공이 가능함.
3) 카운터 보링(COUNTER BORING)
동력에 제한을 받아 한번에 필요한 구멍을 뚫을 수 없을 경우 사용되며 내면을 정밀하게 가공하기 위한 방법.
4) 적용 사례
사출기 등의 유압 실린더, 압연기의 롤러, 공작기계 주축, 선박의 추진축, 자동차와 항공기 부품의 정밀 구멍 가공, 유화 플랜트, 발전소 및 담수 설비 등의 주요 기기인 열교환기의 핵심 부품인 밸브시트 구멍 가공에 적용.
이상으로 절삭 가공 중 드릴링에 대한 연재를 마치고 다음에는 선삭에 대한 연재를 시작할 예정입니다.
2020년 09월 21일