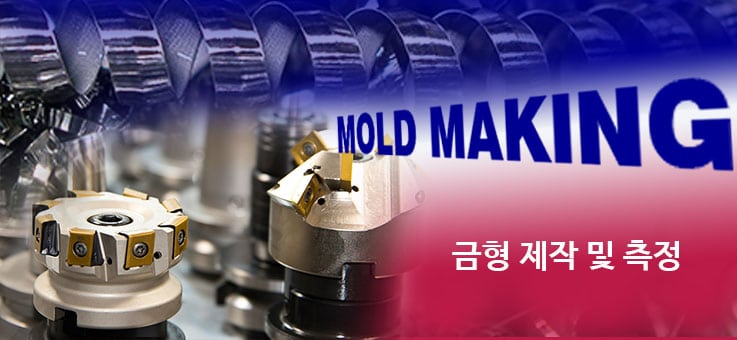
금형 제작 5
제5장 방전가공
1. 방전가공의 원리
(1) 개요
방전가공은 방전 현상을 인공적으로 설정하고 불꽃 방전에 의하여 재료를 미량 씩 용해•기화시켜서 가공용 전극의 형상에 따라 구멍 뚫기, 조각, 절단 등을 하는 것으로 주로 금형의 제작과 수리에 이용되고 있음.
(2) 방전가공의 특징
1) 장점
재료의 경도와 인성에 관계없이 전기 도체면을 쉽게 가공함.
비접촉성으로 기계적인 힘이 가해지지 않음.
다듬질면은 방향성이 없고 균일함.
복잡한 표면 형상이나 미세한 가공이 가능함.
가공 표면의 열변질층 두께가 균일하며 마무리 가공이 쉬움.
가공성이 높고 설계의 유연성이 큼.
2) 단점
가공 상의 전극 소재에 제한이 있음.
가공속도가 느림.
전극 소모가 있으며 화재 발생에 유의해야 함.
(3) 방전가공의 진행 과정
1) 암류
전극과 일감에 서로 다른 극성의 전기를 가해 전압을 점점 높이면 + 극성에는 – 이온이, – 극성에는 + 이온이 끌리게 되는데 이때 전극을 일감에 접근시키면 방전이 되어 미세 전류가 흐르는 상태가 됨.
전류의 양은 이온의 수이며 가하는 전압에 따라 변하고 많은 이온이 점점 중화•소멸되면서 균형을 이루게 되는데 이러한 상태를 암류라고 함.
2) 코로나 방전
암류 상태에서 더욱 전압을 높이면 전압이 걸린 부분은 부분적으로 절연이 파괴되는데 이 상태를 코로나 방전이라고 함.
3) 불꽃 방전
코로나 방전 이후에도 전압을 계속 높이면 금속 중의 자유 전자가 강하게 끌려 나와 확산되어 이온의 이동속도가 빨라지는데 이렇게 확산된 전자와 이온이 극간 중의 물질에 닿으면 이 물질이 이온화되고 이온 양이 증가함에 따라 순간적으로 전류도 급격히 증가하여 온도가 비정상적으로 높아지며 전류 밀도도 비정상적으로 증가하기 때문에 1,000℃가 넘는 열이 절연파괴를 일으키는데 이를 불꽃 방전이라고 함.
4) 아크 방전
불꽃 방전이 지나면 전류의 변화는 거의 없으며 정상적으로 전류가 흐르는 상태가 되는 데 이를 아크 방전이라고 함.
2. 방전가공기
(1) 개요
방전가공기는 기계 본체인 기계부, 방전 상태를 안정되고 지속적으로 유지하기 위한 전원공급 장치 그리고 가공액을 공급하는 가공액 공급 장치로 구성되어 있음.
방전가공기에 따라서는 기능을 고급화시킨 자동전극교환 장치, 가공 현상을 최적화하는 적응제어 기능을 가진 것도 있음.
방전가공기의 크기는 가공탱크의 크기, 일감의 최대 중량, 전원 용량 등으로 표시됨.
(2) 방전가공기의 구성 및 특징
1) 기계부
(가) 헤드
방전가공용 전극을 설치하는 부분으로 서보기구에 의해 상하로 작동됨.
(나) 서보기구
서보모터의 회전 운동을 직선 운동으로 전환시켜 헤드를 상하로 이동시키는 장치로서 방전 현상에 의해 가공된 일감의 표면과 전극의 간격을 적절하게 유지시킴.
(다) 가공탱크
일감을 넣고 가공하는 용기로서 가공액을 저장하는 역할을 하며 가공액이 공급되는 파이프, 사용된 가공액을 배출시키는 드레인 밸브 등으로 구성됨.
(라) 테이블
가공물의 위치를 조정하는 것으로서 X축, Y축으로 구성됨.
2) 전원공급 장치
(가) 트랜스부
전원을 공급받아서 배분하는 장치.
(나) 펄스발생 장치
① 콘덴서 방식
– 방전가공에 필요한 고주파 전원을 얻기 위하여 콘덴서를 사용하여 전하를 충전한 후 이를 방전하는 방식이며 가공전류가 높고 방전시간이 짧아 방전전류를 얻기 쉬움.
– 가공전류와 방전시간의 조절이 어렵고 때문에 다듬질 가공, 미소 가공 등의 제한된 분야에 쓰임.
② 트랜지스터 방식
– 트랜지스터를 사용하여 방전가공 전원을 단속적으로 흘려보내는 방식으로 가공전류와 방전시간을 제어하기가 수월하므로 현재 가장 널리 쓰임.
– 스위치 회로가 있기 때문에 강제적으로 전류를 차단할 수 있어 방전이 소멸된 후 전원으로부터의 에너지 유입이 없고 극간의 절연 회복이 쉬움.
3) 가공액 공급 장치
구성요소 | 기능 |
---|---|
탱크 | 가공액을 저장 |
펌프 | 가공액을 방전가공 부위에 공급 |
필터 | 사용된 가공액 중의 가공 칩을 여과 |
3. 방전가공의 조건
(1) 개요
방전가공의 가공 특성을 나타내는 기준은 가공속도, 다듬질면 거칠기, 클리어런스, 전극 소모비 등을 들 수 있음.
(2) 방전가공 조건
1) 방전가공 속도
현재 널리 쓰이고 있는 방전가공기의 최대 가공속도는 약 50g(3kg/h) 정도임.
방전가공 속도는 일반 공작기계의 가공속도에 비해 매우 느리며 난삭재나 어려운 작업에 국한됨.
일반적으로 방전가공 속도가 빠르면 가공 표면이 거칠어짐.
2) 가공전류와 방전시간
단발 방전 에너지의 크기는 가공전류와 방전시간에 비례하여 커지며 방전 에너지가 클수록 가공속도는 빠르나 표면이 거칠어지고 클리어런스가 커짐.
3) 휴지시간
단발 방전과 단발 방전 사이의 시간을 휴지시간이라 하며 방전가공은 무수한 단발 방전이 반복되면서 이루어짐.
휴지시간을 짧게 하면 단위시간당 방전횟수가 증가하여 가공속도가 빨라지나 너무 짧을 경우에는 아크 방전이 발생할 우려가 있음.
4) 극성
가공할 일감을 + 전극을 -로 하여 가공하는 것을 정극성이라 하고 그 반대의 경우를 역극성이라 함.
극성의 선택은 가공조건(전극 및 일감의 재질, 가공면의 거칠기)에 따라 선택해야 함.
역극성일 경우 전극 소모가 적으며 탄소강의 경우에는 역극성, 초경합금의 경우에는 정극성으로 가공해야 함.
극성의 선택이 잘못되면 전극의 소모가 크거나 방전가공이 어려우므로 유의해야 함.
5) 칩의 배출
가공된 칩은 방전가공에 많은 영향을 끼치게 되며 칩의 배출이 원활하지 않으면 다음과 같은 문제점이 발생함.
– 가공속도가 느려지고 가공면의 정밀도가 떨어짐.
– 가공 칩에 의한 이상 방전으로 전극의 소모가 많아짐.
– 아크 현상으로 인해 전극과 일감을 손상시킴.
4. 방전가공의 제어 및 가공 기술
(1) 개요
방전가공기를 제어하여 데이터의 입•출력을 행하는 CNC 장치가 대표적인 방전가공기의 제어장치이지만 이 밖에 여러 가지 제어 기술이 채용되어 새로운 가공 기술이 가능하게 되었음.
(2) 적용제어
1) 제어 방식
아크의 발생을 사전에 감지하여 극간의 상태가 좋아질 때까지 펄스의 발진을 휴지시키는 방식으로 방전 현상을 제어함.
아크 발생 전에 구동 현상의 표출 방식을 검출 및 기억하고 각 펄스마다 에너지나 휴지시간 등의 가공조건을 약간 변형시킬 때 나타나는 현상과 기억된 조건을 비교하여 좋은 조건을 선택하는 방식.
2) 특징
다듬질면의 거칠기나 전극 소모비가 일정함.
가공면적이나 가공길이의 변화에도 최적 가공조건을 선택.
가공능률이 극대화됨.
(3) 전극 이송제어
1) 제어 방식
가공 중 극간의 평균전압이나 전류의 평균치, 방전 시 휴지시간 등을 기준치와 비교하여 그 차이가 0이 되도록 극과 극의 간격을 항상 최적의 상태로 일정하게 유지하도록 제어하며 모터서보 방식과 유압서보 방식이 사용됨.
2) 유압서보 방식의 특징
모터서보 방식에 비해 응답성이 높음.
속도의 가변 범위가 넓음.
무거운 전극도 보다 효율적으로 제어할 수 있음.
(4) 요동 방전가공
1) 제어 방식
보통의 방전가공에서는 Z축 방향으로 이동하여 가공길이만 증대되는 것에 비해 요동 방전가공은 전극과 가공물의 상대 위치를 X축, Y축 방향으로 바꿈으로써 종래의 방전가공으로 할 수 없는 여러 가지 형상을 가공할 수 있음.
요동 장치는 방전가공기의 헤드에 X Y 크로스 테이블을 고정하여 X축 및 Y축을 각각 별개의 모터에 의해 구동하는 방식을 취함.
2) 특징
가공형상의 종류를 확대할 수 있음.
1개의 전극으로 거친 가공 및 다듬질 가공을 할 수 있음.(클리어런스의 차이를 없앨 수 있음.)
깊은 구멍 가공 시 가공시간을 단축할 수 있음.(요동 운동을 통해 측면 간극을 넓힐 수 있고 가공액의 흐름도 원활하게 하여 칩의 배출이 용이함.)
5. 방전가공의 전극 소모비
(1) 개요
방전가공의 단점은 전극 공구의 소모로서 이를 방전 회로를 개량함으로써 많은 개선이 있었지만 저전극 소모 방전가공 조건은 필연적으로 다른 가공 특성의 저하를 수반하게 됨.
또한 전극의 소모가 적은 방전가공은 펄스 폭이 긴 조건을 사용하기 때문에 일반적으로 두꺼운 열변질층을 만듦.
(2) 전극 소모비
1) 중량 소모비
중량 소모비는 측정이 간단하고 정확하므로 가장 많이 쓰이며 가공물과 전극의 비중이 비슷한 경우에 적당함.
2) 체적 소모비
체적 소모비는 Ag-W, Al 전극과 같이 가공물과 전극의 비중 차이가 큰 재질인 경우에 사용됨.
3) 형상 소모비(길이 소모비)
형상 소모비는 사각 단면의 전극으로 일정한 가공물의 두께를 관통할 경우 단면, 측면, 각각 부분의 소모비로 표시함.
(3) 저전극 소모 방전가공
스파크 방전 및 아크 방전을 단극성으로 하고 펄스 방전을 반복할 것.
방전 지속시간을 비교적 길게 하고 충격계수를 크게 할 것.
전극 공구를 + 가공 재료를 -로 하는 역극성 접속을 할 것.
6. 방전가공에서의 전극 재료와 가공 조건
(1) 방전 제거 현상
전극 소모의 메커니즘은 양극에는 전자, 음극에는 양이온이 충돌하여 증발•용융에 의해 전극이 소모됨.
전자, 양이온의 양, 질량, 속도가 다르기 때문에 극성에 의한 제거량에 차이가 발생하며 융점이 높고 열이나 온도의 전도성이 좋은 재료는 제거량이 작음.
(2) 극간 에너지 배분
음극의 전자•전류 밀도가 작은 조건에서는 음극의 제거량이 많아 역극성 가공에 유리함.
음극의 전자 방출이 용이한 재료에서는 전자•전류 밀도가 커지게 되어 음극의 제거량이 작아 정극성 가공에 유리함.
(3) 전극 재료와 가공 조건
1) 동 전극
동 전극은 형 조각 방전가공에 가장 많이 사용되고 있으며 역극성 가공에서 양호한 결과를 얻을 수 있음.
2) 흑연 전극
흑연 전극은 가공 에너지를 크게 한 황삭 가공 영역에서 동 전극보다 유리하며 전극이 음인 정극성 가공에서 가공속도 및 가공면의 거칠기가 유리함.
흑연 전극은 고유 저항값이 금속 재료보다 크기 때문에 지속 방전이나 집중 방전이 발생하기 쉬움.
3) 강 전극
강 전극은 프레스 트리밍 다이 가공 등에 제한적으로 사용되며 가공속도가 빠르고 전극 소모율이 낮음.
용융 상태의 강은 점성이 크고 용융 잔류층이 전극 방전면의 표면 거칠기를 나쁘게 함.
4) 동-텅스텐. 은-텅스텐 전극
미세 가공에서 동보다 기계적 강도가 크고 가공성이 양호하여 초경합금과 같은 내열성이 높은 재료 가공에 유리함.
가공 에너지 공급 밀도를 크게 할 수 있으며 전류 피크값이 크고 방전시간이 짧은 조건에 사용함.
(4) 전극 재료의 조건
방전에 의한 소모가 적어야 함.
필요한 형상으로 가공이 쉬워야 함.
전기 저항이 적고 기계적인 강도가 커야 함.
가격이 저렴해야 함.
밀도가 높고 비열이 크며 융점이 높아야 함.
7. 방전가공의 변질층
(1) 개요
방전가공 시에는 다소의 차이는 있지만 표면 변질층이 발생하게 되는데 이러한 변질층의 영향으로 금형에 균열을 초래할 수 있으며 따라서 방전가공한 금형은 뜨임 처리를 하거나 샌드블라스트, 숏 피닝 등을 통해 변질층을 제거해야 함.
특히 냉간단조와 같이 금형의 강도가 엄격히 요구되는 경우에는 반드시 연마 가공을 하여 방전면에 발생한 헤어 크랙을 제거해야 함.
(2) 변질층 방지 대책
표면 변질층의 두께는 피크전류가 많을수록, 펄스폭이 넓을수록 크지만 10μs 이하가 되면 피크전류에 관계없이 변질층의 두께가 작아져 거의 같은 상태가 됨.
표면 변질층의 생성을 방지하려면 펄스 폭을 좁혀서 주파수(방전 반복수 즉 전극의 유 소모 조건)를 높이는 것이 효과적임.
방전 에너지(피크전류 x 펄스폭 x 아크전압)가 동일하다 하더라도 펄스폭을 좁게 하고 피크전류를 높게 하면 전류의 영향이 거의 나타나지 않아 헤어 크랙이 발생하는 않음.
8. 가공액
(1) 가공액의 역할
방전가공 시 생기는 용융 금속을 비산 시킴.
방전가공 시 발생된 열을 냉각시킴.
전극의 소모를 방지함.
극간의 절연을 회복시킴.
가공 칩을 배출시킴.
(2) 가공액의 구비 조건
절연성이 높아야 함.
기화점, 인화점이 높아야 함.
점도가 낮고 냉각 능력이 우수해야 함.
산화 안정성이 좋고 냄새가 없어야 함.
값이 저렴하고 구하기 쉬워야 함.
(3) 가공액의 공급 및 제거 방법
1) 분출법
분출법은 전극과 가공물 사이에 가공액을 분출시켜 가공 칩을 제거하는 방식.
관통 가공일 경우에 액압을 낮게 하여 가공물 아래 구멍에서 가공액을 분출시키고 바닥 붙임 가공일 경우에는 가공면적이 넓어서 액압을 높게 해야 함.
2) 흡인법
흡인법은 가공 칩을 전극이나 테이블에 연결된 관을 통하여 흡입시키는 방식.
주로 가공물의 측면 구배를 작게 가공할 경우에 이용됨.
흡인압력 설정이 중요하여 흡인압이 높으면 전극이 진동하고 가공속도가 저하되며 반대인 경우에는 용기 내의 가스가 폭발하여 전극 또는 가공물의 위치를 어긋나게 함.
가공물 위에 공급되는 가공액이 더러우면 2차 방전이 되어 구배가 생기므로 가공액의 청결을 유지해야 함.
3) 분사법
분사법 전극과 가공물 사이에 분사노즐을 이용하여 가공액을 분사하여 가공 칩을 제거하는 방식이며 가공깊이가 깊을 때는 적당하지 않음.
각인 가공, 깊은 리브 가공 등에서 가공액 공급 구멍이 없을 경우에 사용함.
분출법, 흡인법에 비해 가공액 배출 능력이 작아 분사각도 등의 위치결정이 중요함.
이상으로 비절삭가공 중 방전가공에 대한 연재를 마치고 다음에는 와이어 방전가공에 대한 연재를 시작할 예정입니다.
2020년 09월 27일
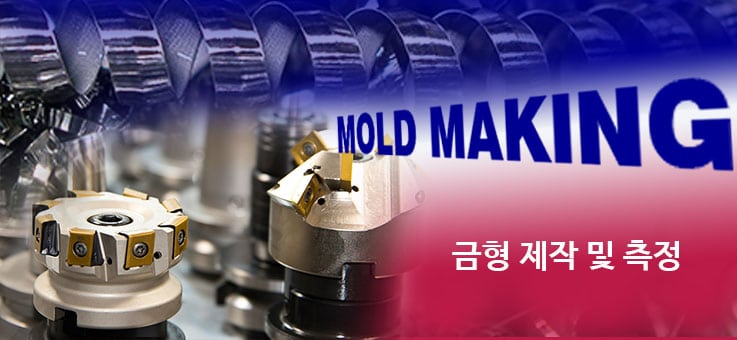
금형 제작 5
제5장 방전가공
1. 방전가공의 원리
(1) 개요
방전가공은 방전 현상을 인공적으로 설정하고 불꽃 방전에 의하여 재료를 미량 씩 용해•기화시켜서 가공용 전극의 형상에 따라 구멍 뚫기, 조각, 절단 등을 하는 것으로 주로 금형의 제작과 수리에 이용되고 있음.
(2) 방전가공의 특징
1) 장점
재료의 경도와 인성에 관계없이 전기 도체면을 쉽게 가공함.
비접촉성으로 기계적인 힘이 가해지지 않음.
다듬질면은 방향성이 없고 균일함.
복잡한 표면 형상이나 미세한 가공이 가능함.
가공 표면의 열변질층 두께가 균일하며 마무리 가공이 쉬움.
가공성이 높고 설계의 유연성이 큼.
2) 단점
가공 상의 전극 소재에 제한이 있음.
가공속도가 느림.
전극 소모가 있으며 화재 발생에 유의해야 함.
(3) 방전가공의 진행 과정
1) 암류
전극과 일감에 서로 다른 극성의 전기를 가해 전압을 점점 높이면 + 극성에는 – 이온이, – 극성에는 + 이온이 끌리게 되는데 이때 전극을 일감에 접근시키면 방전이 되어 미세 전류가 흐르는 상태가 됨.
전류의 양은 이온의 수이며 가하는 전압에 따라 변하고 많은 이온이 점점 중화•소멸되면서 균형을 이루게 되는데 이러한 상태를 암류라고 함.
2) 코로나 방전
암류 상태에서 더욱 전압을 높이면 전압이 걸린 부분은 부분적으로 절연이 파괴되는데 이 상태를 코로나 방전이라고 함.
3) 불꽃 방전
코로나 방전 이후에도 전압을 계속 높이면 금속 중의 자유 전자가 강하게 끌려 나와 확산되어 이온의 이동속도가 빨라지는데 이렇게 확산된 전자와 이온이 극간 중의 물질에 닿으면 이 물질이 이온화되고 이온 양이 증가함에 따라 순간적으로 전류도 급격히 증가하여 온도가 비정상적으로 높아지며 전류 밀도도 비정상적으로 증가하기 때문에 1,000℃가 넘는 열이 절연파괴를 일으키는데 이를 불꽃 방전이라고 함.
4) 아크 방전
불꽃 방전이 지나면 전류의 변화는 거의 없으며 정상적으로 전류가 흐르는 상태가 되는 데 이를 아크 방전이라고 함.
2. 방전가공기
(1) 개요
방전가공기는 기계 본체인 기계부, 방전 상태를 안정되고 지속적으로 유지하기 위한 전원공급 장치 그리고 가공액을 공급하는 가공액 공급 장치로 구성되어 있음.
방전가공기에 따라서는 기능을 고급화시킨 자동전극교환 장치, 가공 현상을 최적화하는 적응제어 기능을 가진 것도 있음.
방전가공기의 크기는 가공탱크의 크기, 일감의 최대 중량, 전원 용량 등으로 표시됨.
(2) 방전가공기의 구성 및 특징
1) 기계부
(가) 헤드
방전가공용 전극을 설치하는 부분으로 서보기구에 의해 상하로 작동됨.
(나) 서보기구
서보모터의 회전 운동을 직선 운동으로 전환시켜 헤드를 상하로 이동시키는 장치로서 방전 현상에 의해 가공된 일감의 표면과 전극의 간격을 적절하게 유지시킴.
(다) 가공탱크
일감을 넣고 가공하는 용기로서 가공액을 저장하는 역할을 하며 가공액이 공급되는 파이프, 사용된 가공액을 배출시키는 드레인 밸브 등으로 구성됨.
(라) 테이블
가공물의 위치를 조정하는 것으로서 X축, Y축으로 구성됨.
2) 전원공급 장치
(가) 트랜스부
전원을 공급받아서 배분하는 장치.
(나) 펄스발생 장치
① 콘덴서 방식
– 방전가공에 필요한 고주파 전원을 얻기 위하여 콘덴서를 사용하여 전하를 충전한 후 이를 방전하는 방식이며 가공전류가 높고 방전시간이 짧아 방전전류를 얻기 쉬움.
– 가공전류와 방전시간의 조절이 어렵고 때문에 다듬질 가공, 미소 가공 등의 제한된 분야에 쓰임.
② 트랜지스터 방식
– 트랜지스터를 사용하여 방전가공 전원을 단속적으로 흘려보내는 방식으로 가공전류와 방전시간을 제어하기가 수월하므로 현재 가장 널리 쓰임.
– 스위치 회로가 있기 때문에 강제적으로 전류를 차단할 수 있어 방전이 소멸된 후 전원으로부터의 에너지 유입이 없고 극간의 절연 회복이 쉬움.
3) 가공액 공급 장치
구성요소 | 기능 |
---|---|
탱크 | 가공액을 저장 |
펌프 | 가공액을 방전가공 부위에 공급 |
필터 | 사용된 가공액 중의 가공 칩을 여과 |
3. 방전가공의 조건
(1) 개요
방전가공의 가공 특성을 나타내는 기준은 가공속도, 다듬질면 거칠기, 클리어런스, 전극 소모비 등을 들 수 있음.
(2) 방전가공 조건
1) 방전가공 속도
현재 널리 쓰이고 있는 방전가공기의 최대 가공속도는 약 50g(3kg/h) 정도임.
방전가공 속도는 일반 공작기계의 가공속도에 비해 매우 느리며 난삭재나 어려운 작업에 국한됨.
일반적으로 방전가공 속도가 빠르면 가공 표면이 거칠어짐.
2) 가공전류와 방전시간
단발 방전 에너지의 크기는 가공전류와 방전시간에 비례하여 커지며 방전 에너지가 클수록 가공속도는 빠르나 표면이 거칠어지고 클리어런스가 커짐.
3) 휴지시간
단발 방전과 단발 방전 사이의 시간을 휴지시간이라 하며 방전가공은 무수한 단발 방전이 반복되면서 이루어짐.
휴지시간을 짧게 하면 단위시간당 방전횟수가 증가하여 가공속도가 빨라지나 너무 짧을 경우에는 아크 방전이 발생할 우려가 있음.
4) 극성
가공할 일감을 + 전극을 -로 하여 가공하는 것을 정극성이라 하고 그 반대의 경우를 역극성이라 함.
극성의 선택은 가공조건(전극 및 일감의 재질, 가공면의 거칠기)에 따라 선택해야 함.
역극성일 경우 전극 소모가 적으며 탄소강의 경우에는 역극성, 초경합금의 경우에는 정극성으로 가공해야 함.
극성의 선택이 잘못되면 전극의 소모가 크거나 방전가공이 어려우므로 유의해야 함.
5) 칩의 배출
가공된 칩은 방전가공에 많은 영향을 끼치게 되며 칩의 배출이 원활하지 않으면 다음과 같은 문제점이 발생함.
– 가공속도가 느려지고 가공면의 정밀도가 떨어짐.
– 가공 칩에 의한 이상 방전으로 전극의 소모가 많아짐.
– 아크 현상으로 인해 전극과 일감을 손상시킴.
4. 방전가공의 제어 및 가공 기술
(1) 개요
방전가공기를 제어하여 데이터의 입•출력을 행하는 CNC 장치가 대표적인 방전가공기의 제어장치이지만 이 밖에 여러 가지 제어 기술이 채용되어 새로운 가공 기술이 가능하게 되었음.
(2) 적용제어
1) 제어 방식
아크의 발생을 사전에 감지하여 극간의 상태가 좋아질 때까지 펄스의 발진을 휴지시키는 방식으로 방전 현상을 제어함.
아크 발생 전에 구동 현상의 표출 방식을 검출 및 기억하고 각 펄스마다 에너지나 휴지시간 등의 가공조건을 약간 변형시킬 때 나타나는 현상과 기억된 조건을 비교하여 좋은 조건을 선택하는 방식.
2) 특징
다듬질면의 거칠기나 전극 소모비가 일정함.
가공면적이나 가공길이의 변화에도 최적 가공조건을 선택.
가공능률이 극대화됨.
(3) 전극 이송제어
1) 제어 방식
가공 중 극간의 평균전압이나 전류의 평균치, 방전 시 휴지시간 등을 기준치와 비교하여 그 차이가 0이 되도록 극과 극의 간격을 항상 최적의 상태로 일정하게 유지하도록 제어하며 모터서보 방식과 유압서보 방식이 사용됨.
2) 유압서보 방식의 특징
모터서보 방식에 비해 응답성이 높음.
속도의 가변 범위가 넓음.
무거운 전극도 보다 효율적으로 제어할 수 있음.
(4) 요동 방전가공
1) 제어 방식
보통의 방전가공에서는 Z축 방향으로 이동하여 가공길이만 증대되는 것에 비해 요동 방전가공은 전극과 가공물의 상대 위치를 X축, Y축 방향으로 바꿈으로써 종래의 방전가공으로 할 수 없는 여러 가지 형상을 가공할 수 있음.
요동 장치는 방전가공기의 헤드에 X Y 크로스 테이블을 고정하여 X축 및 Y축을 각각 별개의 모터에 의해 구동하는 방식을 취함.
2) 특징
가공형상의 종류를 확대할 수 있음.
1개의 전극으로 거친 가공 및 다듬질 가공을 할 수 있음.(클리어런스의 차이를 없앨 수 있음.)
깊은 구멍 가공 시 가공시간을 단축할 수 있음.(요동 운동을 통해 측면 간극을 넓힐 수 있고 가공액의 흐름도 원활하게 하여 칩의 배출이 용이함.)
5. 방전가공의 전극 소모비
(1) 개요
방전가공의 단점은 전극 공구의 소모로서 이를 방전 회로를 개량함으로써 많은 개선이 있었지만 저전극 소모 방전가공 조건은 필연적으로 다른 가공 특성의 저하를 수반하게 됨.
또한 전극의 소모가 적은 방전가공은 펄스 폭이 긴 조건을 사용하기 때문에 일반적으로 두꺼운 열변질층을 만듦.
(2) 전극 소모비
1) 중량 소모비
중량 소모비는 측정이 간단하고 정확하므로 가장 많이 쓰이며 가공물과 전극의 비중이 비슷한 경우에 적당함.
2) 체적 소모비
체적 소모비는 Ag-W, Al 전극과 같이 가공물과 전극의 비중 차이가 큰 재질인 경우에 사용됨.
3) 형상 소모비(길이 소모비)
형상 소모비는 사각 단면의 전극으로 일정한 가공물의 두께를 관통할 경우 단면, 측면, 각각 부분의 소모비로 표시함.
(3) 저전극 소모 방전가공
스파크 방전 및 아크 방전을 단극성으로 하고 펄스 방전을 반복할 것.
방전 지속시간을 비교적 길게 하고 충격계수를 크게 할 것.
전극 공구를 + 가공 재료를 -로 하는 역극성 접속을 할 것.
6. 방전가공에서의 전극 재료와 가공 조건
(1) 방전 제거 현상
전극 소모의 메커니즘은 양극에는 전자, 음극에는 양이온이 충돌하여 증발•용융에 의해 전극이 소모됨.
전자, 양이온의 양, 질량, 속도가 다르기 때문에 극성에 의한 제거량에 차이가 발생하며 융점이 높고 열이나 온도의 전도성이 좋은 재료는 제거량이 작음.
(2) 극간 에너지 배분
음극의 전자•전류 밀도가 작은 조건에서는 음극의 제거량이 많아 역극성 가공에 유리함.
음극의 전자 방출이 용이한 재료에서는 전자•전류 밀도가 커지게 되어 음극의 제거량이 작아 정극성 가공에 유리함.
(3) 전극 재료와 가공 조건
1) 동 전극
동 전극은 형 조각 방전가공에 가장 많이 사용되고 있으며 역극성 가공에서 양호한 결과를 얻을 수 있음.
2) 흑연 전극
흑연 전극은 가공 에너지를 크게 한 황삭 가공 영역에서 동 전극보다 유리하며 전극이 음인 정극성 가공에서 가공속도 및 가공면의 거칠기가 유리함.
흑연 전극은 고유 저항값이 금속 재료보다 크기 때문에 지속 방전이나 집중 방전이 발생하기 쉬움.
3) 강 전극
강 전극은 프레스 트리밍 다이 가공 등에 제한적으로 사용되며 가공속도가 빠르고 전극 소모율이 낮음.
용융 상태의 강은 점성이 크고 용융 잔류층이 전극 방전면의 표면 거칠기를 나쁘게 함.
4) 동-텅스텐. 은-텅스텐 전극
미세 가공에서 동보다 기계적 강도가 크고 가공성이 양호하여 초경합금과 같은 내열성이 높은 재료 가공에 유리함.
가공 에너지 공급 밀도를 크게 할 수 있으며 전류 피크값이 크고 방전시간이 짧은 조건에 사용함.
(4) 전극 재료의 조건
방전에 의한 소모가 적어야 함.
필요한 형상으로 가공이 쉬워야 함.
전기 저항이 적고 기계적인 강도가 커야 함.
가격이 저렴해야 함.
밀도가 높고 비열이 크며 융점이 높아야 함.
7. 방전가공의 변질층
(1) 개요
방전가공 시에는 다소의 차이는 있지만 표면 변질층이 발생하게 되는데 이러한 변질층의 영향으로 금형에 균열을 초래할 수 있으며 따라서 방전가공한 금형은 뜨임 처리를 하거나 샌드블라스트, 숏 피닝 등을 통해 변질층을 제거해야 함.
특히 냉간단조와 같이 금형의 강도가 엄격히 요구되는 경우에는 반드시 연마 가공을 하여 방전면에 발생한 헤어 크랙을 제거해야 함.
(2) 변질층 방지 대책
표면 변질층의 두께는 피크전류가 많을수록, 펄스폭이 넓을수록 크지만 10μs 이하가 되면 피크전류에 관계없이 변질층의 두께가 작아져 거의 같은 상태가 됨.
표면 변질층의 생성을 방지하려면 펄스 폭을 좁혀서 주파수(방전 반복수 즉 전극의 유 소모 조건)를 높이는 것이 효과적임.
방전 에너지(피크전류 x 펄스폭 x 아크전압)가 동일하다 하더라도 펄스폭을 좁게 하고 피크전류를 높게 하면 전류의 영향이 거의 나타나지 않아 헤어 크랙이 발생하는 않음.
8. 가공액
(1) 가공액의 역할
방전가공 시 생기는 용융 금속을 비산 시킴.
방전가공 시 발생된 열을 냉각시킴.
전극의 소모를 방지함.
극간의 절연을 회복시킴.
가공 칩을 배출시킴.
(2) 가공액의 구비 조건
절연성이 높아야 함.
기화점, 인화점이 높아야 함.
점도가 낮고 냉각 능력이 우수해야 함.
산화 안정성이 좋고 냄새가 없어야 함.
값이 저렴하고 구하기 쉬워야 함.
(3) 가공액의 공급 및 제거 방법
1) 분출법
분출법은 전극과 가공물 사이에 가공액을 분출시켜 가공 칩을 제거하는 방식.
관통 가공일 경우에 액압을 낮게 하여 가공물 아래 구멍에서 가공액을 분출시키고 바닥 붙임 가공일 경우에는 가공면적이 넓어서 액압을 높게 해야 함.
2) 흡인법
흡인법은 가공 칩을 전극이나 테이블에 연결된 관을 통하여 흡입시키는 방식.
주로 가공물의 측면 구배를 작게 가공할 경우에 이용됨.
흡인압력 설정이 중요하여 흡인압이 높으면 전극이 진동하고 가공속도가 저하되며 반대인 경우에는 용기 내의 가스가 폭발하여 전극 또는 가공물의 위치를 어긋나게 함.
가공물 위에 공급되는 가공액이 더러우면 2차 방전이 되어 구배가 생기므로 가공액의 청결을 유지해야 함.
3) 분사법
분사법 전극과 가공물 사이에 분사노즐을 이용하여 가공액을 분사하여 가공 칩을 제거하는 방식이며 가공깊이가 깊을 때는 적당하지 않음.
각인 가공, 깊은 리브 가공 등에서 가공액 공급 구멍이 없을 경우에 사용함.
분출법, 흡인법에 비해 가공액 배출 능력이 작아 분사각도 등의 위치결정이 중요함.
이상으로 비절삭가공 중 방전가공에 대한 연재를 마치고 다음에는 와이어 방전가공에 대한 연재를 시작할 예정입니다.
2020년 09월 27일
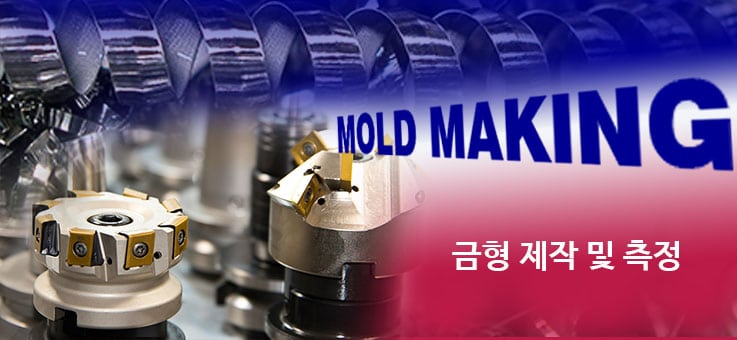
금형 제작 5
제5장 방전가공
1. 방전가공의 원리
(1) 개요
방전가공은 방전 현상을 인공적으로 설정하고 불꽃 방전에 의하여 재료를 미량 씩 용해•기화시켜서 가공용 전극의 형상에 따라 구멍 뚫기, 조각, 절단 등을 하는 것으로 주로 금형의 제작과 수리에 이용되고 있음.
(2) 방전가공의 특징
1) 장점
재료의 경도와 인성에 관계없이 전기 도체면을 쉽게 가공함.
비접촉성으로 기계적인 힘이 가해지지 않음.
다듬질면은 방향성이 없고 균일함.
복잡한 표면 형상이나 미세한 가공이 가능함.
가공 표면의 열변질층 두께가 균일하며 마무리 가공이 쉬움.
가공성이 높고 설계의 유연성이 큼.
2) 단점
가공 상의 전극 소재에 제한이 있음.
가공속도가 느림.
전극 소모가 있으며 화재 발생에 유의해야 함.
(3) 방전가공의 진행 과정
1) 암류
전극과 일감에 서로 다른 극성의 전기를 가해 전압을 점점 높이면 + 극성에는 – 이온이, – 극성에는 + 이온이 끌리게 되는데 이때 전극을 일감에 접근시키면 방전이 되어 미세 전류가 흐르는 상태가 됨.
전류의 양은 이온의 수이며 가하는 전압에 따라 변하고 많은 이온이 점점 중화•소멸되면서 균형을 이루게 되는데 이러한 상태를 암류라고 함.
2) 코로나 방전
암류 상태에서 더욱 전압을 높이면 전압이 걸린 부분은 부분적으로 절연이 파괴되는데 이 상태를 코로나 방전이라고 함.
3) 불꽃 방전
코로나 방전 이후에도 전압을 계속 높이면 금속 중의 자유 전자가 강하게 끌려 나와 확산되어 이온의 이동속도가 빨라지는데 이렇게 확산된 전자와 이온이 극간 중의 물질에 닿으면 이 물질이 이온화되고 이온 양이 증가함에 따라 순간적으로 전류도 급격히 증가하여 온도가 비정상적으로 높아지며 전류 밀도도 비정상적으로 증가하기 때문에 1,000℃가 넘는 열이 절연파괴를 일으키는데 이를 불꽃 방전이라고 함.
4) 아크 방전
불꽃 방전이 지나면 전류의 변화는 거의 없으며 정상적으로 전류가 흐르는 상태가 되는 데 이를 아크 방전이라고 함.
2. 방전가공기
(1) 개요
방전가공기는 기계 본체인 기계부, 방전 상태를 안정되고 지속적으로 유지하기 위한 전원공급 장치 그리고 가공액을 공급하는 가공액 공급 장치로 구성되어 있음.
방전가공기에 따라서는 기능을 고급화시킨 자동전극교환 장치, 가공 현상을 최적화하는 적응제어 기능을 가진 것도 있음.
방전가공기의 크기는 가공탱크의 크기, 일감의 최대 중량, 전원 용량 등으로 표시됨.
(2) 방전가공기의 구성 및 특징
1) 기계부
(가) 헤드
방전가공용 전극을 설치하는 부분으로 서보기구에 의해 상하로 작동됨.
(나) 서보기구
서보모터의 회전 운동을 직선 운동으로 전환시켜 헤드를 상하로 이동시키는 장치로서 방전 현상에 의해 가공된 일감의 표면과 전극의 간격을 적절하게 유지시킴.
(다) 가공탱크
일감을 넣고 가공하는 용기로서 가공액을 저장하는 역할을 하며 가공액이 공급되는 파이프, 사용된 가공액을 배출시키는 드레인 밸브 등으로 구성됨.
(라) 테이블
가공물의 위치를 조정하는 것으로서 X축, Y축으로 구성됨.
2) 전원공급 장치
(가) 트랜스부
전원을 공급받아서 배분하는 장치.
(나) 펄스발생 장치
① 콘덴서 방식
– 방전가공에 필요한 고주파 전원을 얻기 위하여 콘덴서를 사용하여 전하를 충전한 후 이를 방전하는 방식이며 가공전류가 높고 방전시간이 짧아 방전전류를 얻기 쉬움.
– 가공전류와 방전시간의 조절이 어렵고 때문에 다듬질 가공, 미소 가공 등의 제한된 분야에 쓰임.
② 트랜지스터 방식
– 트랜지스터를 사용하여 방전가공 전원을 단속적으로 흘려보내는 방식으로 가공전류와 방전시간을 제어하기가 수월하므로 현재 가장 널리 쓰임.
– 스위치 회로가 있기 때문에 강제적으로 전류를 차단할 수 있어 방전이 소멸된 후 전원으로부터의 에너지 유입이 없고 극간의 절연 회복이 쉬움.
3) 가공액 공급 장치
구성요소 | 기능 |
---|---|
탱크 | 가공액을 저장 |
펌프 | 가공액을 방전가공 부위에 공급 |
필터 | 사용된 가공액 중의 가공 칩을 여과 |
3. 방전가공의 조건
(1) 개요
방전가공의 가공 특성을 나타내는 기준은 가공속도, 다듬질면 거칠기, 클리어런스, 전극 소모비 등을 들 수 있음.
(2) 방전가공 조건
1) 방전가공 속도
현재 널리 쓰이고 있는 방전가공기의 최대 가공속도는 약 50g(3kg/h) 정도임.
방전가공 속도는 일반 공작기계의 가공속도에 비해 매우 느리며 난삭재나 어려운 작업에 국한됨.
일반적으로 방전가공 속도가 빠르면 가공 표면이 거칠어짐.
2) 가공전류와 방전시간
단발 방전 에너지의 크기는 가공전류와 방전시간에 비례하여 커지며 방전 에너지가 클수록 가공속도는 빠르나 표면이 거칠어지고 클리어런스가 커짐.
3) 휴지시간
단발 방전과 단발 방전 사이의 시간을 휴지시간이라 하며 방전가공은 무수한 단발 방전이 반복되면서 이루어짐.
휴지시간을 짧게 하면 단위시간당 방전횟수가 증가하여 가공속도가 빨라지나 너무 짧을 경우에는 아크 방전이 발생할 우려가 있음.
4) 극성
가공할 일감을 + 전극을 -로 하여 가공하는 것을 정극성이라 하고 그 반대의 경우를 역극성이라 함.
극성의 선택은 가공조건(전극 및 일감의 재질, 가공면의 거칠기)에 따라 선택해야 함.
역극성일 경우 전극 소모가 적으며 탄소강의 경우에는 역극성, 초경합금의 경우에는 정극성으로 가공해야 함.
극성의 선택이 잘못되면 전극의 소모가 크거나 방전가공이 어려우므로 유의해야 함.
5) 칩의 배출
가공된 칩은 방전가공에 많은 영향을 끼치게 되며 칩의 배출이 원활하지 않으면 다음과 같은 문제점이 발생함.
– 가공속도가 느려지고 가공면의 정밀도가 떨어짐.
– 가공 칩에 의한 이상 방전으로 전극의 소모가 많아짐.
– 아크 현상으로 인해 전극과 일감을 손상시킴.
4. 방전가공의 제어 및 가공 기술
(1) 개요
방전가공기를 제어하여 데이터의 입•출력을 행하는 CNC 장치가 대표적인 방전가공기의 제어장치이지만 이 밖에 여러 가지 제어 기술이 채용되어 새로운 가공 기술이 가능하게 되었음.
(2) 적용제어
1) 제어 방식
아크의 발생을 사전에 감지하여 극간의 상태가 좋아질 때까지 펄스의 발진을 휴지시키는 방식으로 방전 현상을 제어함.
아크 발생 전에 구동 현상의 표출 방식을 검출 및 기억하고 각 펄스마다 에너지나 휴지시간 등의 가공조건을 약간 변형시킬 때 나타나는 현상과 기억된 조건을 비교하여 좋은 조건을 선택하는 방식.
2) 특징
다듬질면의 거칠기나 전극 소모비가 일정함.
가공면적이나 가공길이의 변화에도 최적 가공조건을 선택.
가공능률이 극대화됨.
(3) 전극 이송제어
1) 제어 방식
가공 중 극간의 평균전압이나 전류의 평균치, 방전 시 휴지시간 등을 기준치와 비교하여 그 차이가 0이 되도록 극과 극의 간격을 항상 최적의 상태로 일정하게 유지하도록 제어하며 모터서보 방식과 유압서보 방식이 사용됨.
2) 유압서보 방식의 특징
모터서보 방식에 비해 응답성이 높음.
속도의 가변 범위가 넓음.
무거운 전극도 보다 효율적으로 제어할 수 있음.
(4) 요동 방전가공
1) 제어 방식
보통의 방전가공에서는 Z축 방향으로 이동하여 가공길이만 증대되는 것에 비해 요동 방전가공은 전극과 가공물의 상대 위치를 X축, Y축 방향으로 바꿈으로써 종래의 방전가공으로 할 수 없는 여러 가지 형상을 가공할 수 있음.
요동 장치는 방전가공기의 헤드에 X Y 크로스 테이블을 고정하여 X축 및 Y축을 각각 별개의 모터에 의해 구동하는 방식을 취함.
2) 특징
가공형상의 종류를 확대할 수 있음.
1개의 전극으로 거친 가공 및 다듬질 가공을 할 수 있음.(클리어런스의 차이를 없앨 수 있음.)
깊은 구멍 가공 시 가공시간을 단축할 수 있음.(요동 운동을 통해 측면 간극을 넓힐 수 있고 가공액의 흐름도 원활하게 하여 칩의 배출이 용이함.)
5. 방전가공의 전극 소모비
(1) 개요
방전가공의 단점은 전극 공구의 소모로서 이를 방전 회로를 개량함으로써 많은 개선이 있었지만 저전극 소모 방전가공 조건은 필연적으로 다른 가공 특성의 저하를 수반하게 됨.
또한 전극의 소모가 적은 방전가공은 펄스 폭이 긴 조건을 사용하기 때문에 일반적으로 두꺼운 열변질층을 만듦.
(2) 전극 소모비
1) 중량 소모비
중량 소모비는 측정이 간단하고 정확하므로 가장 많이 쓰이며 가공물과 전극의 비중이 비슷한 경우에 적당함.
2) 체적 소모비
체적 소모비는 Ag-W, Al 전극과 같이 가공물과 전극의 비중 차이가 큰 재질인 경우에 사용됨.
3) 형상 소모비(길이 소모비)
형상 소모비는 사각 단면의 전극으로 일정한 가공물의 두께를 관통할 경우 단면, 측면, 각각 부분의 소모비로 표시함.
(3) 저전극 소모 방전가공
스파크 방전 및 아크 방전을 단극성으로 하고 펄스 방전을 반복할 것.
방전 지속시간을 비교적 길게 하고 충격계수를 크게 할 것.
전극 공구를 + 가공 재료를 -로 하는 역극성 접속을 할 것.
6. 방전가공에서의 전극 재료와 가공 조건
(1) 방전 제거 현상
전극 소모의 메커니즘은 양극에는 전자, 음극에는 양이온이 충돌하여 증발•용융에 의해 전극이 소모됨.
전자, 양이온의 양, 질량, 속도가 다르기 때문에 극성에 의한 제거량에 차이가 발생하며 융점이 높고 열이나 온도의 전도성이 좋은 재료는 제거량이 작음.
(2) 극간 에너지 배분
음극의 전자•전류 밀도가 작은 조건에서는 음극의 제거량이 많아 역극성 가공에 유리함.
음극의 전자 방출이 용이한 재료에서는 전자•전류 밀도가 커지게 되어 음극의 제거량이 작아 정극성 가공에 유리함.
(3) 전극 재료와 가공 조건
1) 동 전극
동 전극은 형 조각 방전가공에 가장 많이 사용되고 있으며 역극성 가공에서 양호한 결과를 얻을 수 있음.
2) 흑연 전극
흑연 전극은 가공 에너지를 크게 한 황삭 가공 영역에서 동 전극보다 유리하며 전극이 음인 정극성 가공에서 가공속도 및 가공면의 거칠기가 유리함.
흑연 전극은 고유 저항값이 금속 재료보다 크기 때문에 지속 방전이나 집중 방전이 발생하기 쉬움.
3) 강 전극
강 전극은 프레스 트리밍 다이 가공 등에 제한적으로 사용되며 가공속도가 빠르고 전극 소모율이 낮음.
용융 상태의 강은 점성이 크고 용융 잔류층이 전극 방전면의 표면 거칠기를 나쁘게 함.
4) 동-텅스텐. 은-텅스텐 전극
미세 가공에서 동보다 기계적 강도가 크고 가공성이 양호하여 초경합금과 같은 내열성이 높은 재료 가공에 유리함.
가공 에너지 공급 밀도를 크게 할 수 있으며 전류 피크값이 크고 방전시간이 짧은 조건에 사용함.
(4) 전극 재료의 조건
방전에 의한 소모가 적어야 함.
필요한 형상으로 가공이 쉬워야 함.
전기 저항이 적고 기계적인 강도가 커야 함.
가격이 저렴해야 함.
밀도가 높고 비열이 크며 융점이 높아야 함.
7. 방전가공의 변질층
(1) 개요
방전가공 시에는 다소의 차이는 있지만 표면 변질층이 발생하게 되는데 이러한 변질층의 영향으로 금형에 균열을 초래할 수 있으며 따라서 방전가공한 금형은 뜨임 처리를 하거나 샌드블라스트, 숏 피닝 등을 통해 변질층을 제거해야 함.
특히 냉간단조와 같이 금형의 강도가 엄격히 요구되는 경우에는 반드시 연마 가공을 하여 방전면에 발생한 헤어 크랙을 제거해야 함.
(2) 변질층 방지 대책
표면 변질층의 두께는 피크전류가 많을수록, 펄스폭이 넓을수록 크지만 10μs 이하가 되면 피크전류에 관계없이 변질층의 두께가 작아져 거의 같은 상태가 됨.
표면 변질층의 생성을 방지하려면 펄스 폭을 좁혀서 주파수(방전 반복수 즉 전극의 유 소모 조건)를 높이는 것이 효과적임.
방전 에너지(피크전류 x 펄스폭 x 아크전압)가 동일하다 하더라도 펄스폭을 좁게 하고 피크전류를 높게 하면 전류의 영향이 거의 나타나지 않아 헤어 크랙이 발생하는 않음.
8. 가공액
(1) 가공액의 역할
방전가공 시 생기는 용융 금속을 비산 시킴.
방전가공 시 발생된 열을 냉각시킴.
전극의 소모를 방지함.
극간의 절연을 회복시킴.
가공 칩을 배출시킴.
(2) 가공액의 구비 조건
절연성이 높아야 함.
기화점, 인화점이 높아야 함.
점도가 낮고 냉각 능력이 우수해야 함.
산화 안정성이 좋고 냄새가 없어야 함.
값이 저렴하고 구하기 쉬워야 함.
(3) 가공액의 공급 및 제거 방법
1) 분출법
분출법은 전극과 가공물 사이에 가공액을 분출시켜 가공 칩을 제거하는 방식.
관통 가공일 경우에 액압을 낮게 하여 가공물 아래 구멍에서 가공액을 분출시키고 바닥 붙임 가공일 경우에는 가공면적이 넓어서 액압을 높게 해야 함.
2) 흡인법
흡인법은 가공 칩을 전극이나 테이블에 연결된 관을 통하여 흡입시키는 방식.
주로 가공물의 측면 구배를 작게 가공할 경우에 이용됨.
흡인압력 설정이 중요하여 흡인압이 높으면 전극이 진동하고 가공속도가 저하되며 반대인 경우에는 용기 내의 가스가 폭발하여 전극 또는 가공물의 위치를 어긋나게 함.
가공물 위에 공급되는 가공액이 더러우면 2차 방전이 되어 구배가 생기므로 가공액의 청결을 유지해야 함.
3) 분사법
분사법 전극과 가공물 사이에 분사노즐을 이용하여 가공액을 분사하여 가공 칩을 제거하는 방식이며 가공깊이가 깊을 때는 적당하지 않음.
각인 가공, 깊은 리브 가공 등에서 가공액 공급 구멍이 없을 경우에 사용함.
분출법, 흡인법에 비해 가공액 배출 능력이 작아 분사각도 등의 위치결정이 중요함.
이상으로 비절삭가공 중 방전가공에 대한 연재를 마치고 다음에는 와이어 방전가공에 대한 연재를 시작할 예정입니다.
2020년 09월 27일