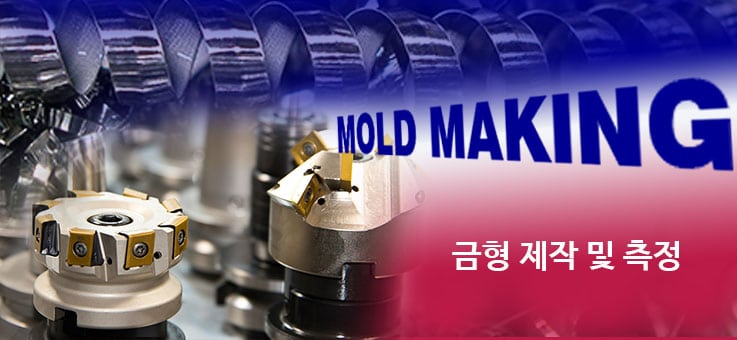
금형 제작 8
제8장 연삭의 특성
연삭의 특징 연삭작용, 자생작용, 숫돌면의 변화가 발생하는데 재생작용은 마멸된 숫돌입자가 탈락하여 새 날이 생기는 현상으로 숫돌입자의 마멸→파괴→탈락→생성이 주기적으로 반복되며 눈탈락→ 눈무딤→ 눈메움과 같은 숫돌면의 변화가 일어나게 됩니다.
1. 연삭 시 발생하는 작용
(1) 연삭작용
WS는 절입 또는 연삭깊이를 의미함.
숫돌바퀴의 절입이 증가하면 연삭저항이 증가하게 됨.
연삭 시 배분력이 주분력의 2배로 작용함.
(2) 자생작용
자생작용이란 마멸된 숫돌입자가 탈락하여 새 날이 생기는 현상으로 숫돌입자의 마멸 → 파괴 → 탈락 → 생성이 주기적으로 반복됨.
장시간 좋은 가공면을 유지할 수 있고 공구 교환이나 재연삭 공정을 생략할 수 있으며 숫돌바퀴의 선택과 적절한 연삭 조건이 필요함.
(3) 숫돌면의 변화
1) 눈탈락
눈탈락은 과도한 자생작용이 발생 시에 숫돌입자의 끝이 충분히 파쇄되지 않고 마모하였을 때 결합제가 파쇄되어 숫돌입자가 입자 그대로 빠져나가는 현상이 일어나는데 숫돌바퀴의 결합도가 작업에 대해 지나치게 낮을 경우 발생되며 숫돌의 손모가 심하고 가공면도 나빠짐.
2) 눈무딤
눈무딤은 자생작용의 부족으로 입자의 표면이 평탄해지는 상태.
(가) 원인
연삭 숫돌의 결합도가 높을 때.
연삭 숫돌의 원주속도가 너무 클 때.
숫돌의 재료가 가공물의 재료에 부적합할 때.
(나) 현상
연삭성이 불량하고 가공물에 열이 발생함.
연삭 손실이 발생함.
3) 눈메움
눈메움은 결합도가 높은 숫돌로 연성 재료를 연삭 시 숫돌 표면의 기공에 칩이 메워지는 현상.
(가) 원인
숫돌입자가 너무 작을 때.
조직이 너무 치밀할 때.
연삭깊이가 깊을 때.
숫돌바퀴의 원주속도가 느릴 때.
(나) 현상
연삭성이 불량하고 다듬질면이 거칠어짐.
다듬질면에 떨림 자리와 같은 상처가 생김.
숫돌입자가 마모되기 쉬움.
2. 특수 연삭 가공 기술
(1) 고속 연삭
1) 정의
연삭 능률 향상을 위해 숫돌 원주속도를 보통의 연삭에서보다 2~3배 크게 한 것으로 가공물 속도나 연삭깊이를 깊게할 수 있어 가공능률이 향상됨.
2) 특징
스파크 아웃 시간을 단축할 수 있음.
연삭저항이 감소하고 가공 정밀도가 향상됨.
숫돌의 손모가 적어 숫돌의 수명이 향상됨.
(2) 크림피드 연삭
1) 정의
종래의 평면 연삭법에 비하여 연삭깊이를 깊게 하고 테이블 이송속도를 매우 느리게 하여 1회 또는 수 회의 이송으로 가공하는 방법으로 숫돌의 원주면을 사용하는 성형 연삭을 고능률화 시킨 것.
2) 특징
숫돌의 마모가 비교적 균일하고 숫돌 윤곽 형상의 변화가 적음.
연삭저항의 변동이 심하고 가공 상태가 불안정할 수 있음.
숫돌 접촉면적이 크고 연삭열의 발생, 연삭균열의 우려가 있음.
(3) 중 연삭
1) 정의
연삭깊이나 가공물의 속도를 크게 하고 단위 시간당 연삭량을 증가시켜 가공능률을 향상시키는 연삭 방법.
2) 종류 및 특징
(가) 슬랩 연삭(SLAB GRINDING)
버 제거, 슬랩의 표피 연삭 등 가공 정도에 비교적 문제가 안 되는 경우 사용됨.
(나) 연마 가공(ABRASIVE MACHING)
높은 연삭능률과 가공 정도를 동시에 얻기 위한 방법으로서 평면 연삭 가공에는 세그먼트형 숫돌을 사용한 고마력의 연삭기가 사용됨.
3. 연삭면의 형성과 스파크 아웃
(1) 개요
연삭 다듬질면은 연삭입자의 절삭날에 의해 절삭된 가공면으로서 연삭 조건에 큰 영향을 받으며 특히 절삭날의 밀도가 중요함.
다듬질면의 거칠기 형상을 위해서는 적절한 날 교정에 의해서 숫돌 표면의 절삭날 높이를 균일하게 하고 밀도를 높이는 것이 무엇보다 중요시됨.
연삭 시에는 설정 절삭깊이만큼 실제로 절삭되지 않으며 여러 요인에 의해 연삭 잔량이 생기게 됨.
(2) 다듬질면에 영향을 주는 요인
1) 입도
입도가 고울수록 다듬질면의 거칠기는 향상되는데 그 감소의 정도는 입도가 거친 영역에서 크고 연삭입자는 연삭저항에 의해 마멸되며 그 마멸 정도가 균일한 것이 다듬질면에 큰 영향을 미침.
2) 결합도
같은 입도의 숫돌로 적당한 연삭 조건하에서 연삭 시 결합도가 굳은 숫돌의 다듬질면이 일반적으로 좋아지는 경향이 있음.
3) 절삭깊이
절삭깊이의 증가에 따라 다듬질면의 거칠기도 증가하며 각각의 절삭날에 작용하는 힘이 증가하여 연삭입자의 마멸이 심해지기 때문이고 동시에 연삭기에 걸리는 부하의 증가로 인한 진동의 요인도 수반함.
4) 이송
이송속도의 증가에 따라 다듬질면의 거칠기도 거의 비례적으로 증가함.
5) 진동
연삭숫돌과 가공물 사이에 상대 진동이 있으면 절삭날의 밀도가 거칠어지므로 조도가 커짐.
6) 절삭잔량
절삭잔량이 있으면 거칠어지며 반복 연삭을 통해 절삭잔량이 적어질 때 다듬질면의 거칠기도 향상되고 절삭깊이가 깊거나 이송속도가 빨라지면 절삭잔량도 많아짐.
(3) 스파크 아웃
1) 정의
연삭 시 숫돌의 마모가 거의 없고 가공물과 숫돌축이 강체라면 설정된 절삭깊이만큼 연삭이 되겠지만 실제로는 여러 요인에 의해 연삭 잔량이 남게 되는데 이때 더 이상의 절삭깊이 이송을 중지하고 연삭을 계속하면 탄성변형이 회복되면서 실 연삭량이 증가되는 상태를 말함.
2) 절삭 잔량 요인
숫돌바퀴의 마모(d0).
숫돌축 및 가공물의 휨(d1).
가공물과 숫돌 접촉 부의 탄성변형(d2).
연삭 입자가 절삭하지 않고 가공물을 밀어젖히는 현상(d3).
3) 연삭면의 형성
설정 절삭깊이가 OG와 같이 경과해도 OP는 탄성변형에 의해 PC는 가공물을 밀어젖힐 때 절삭깊이의 양이 소비되어 실제 가공 치수는 OPCB와 같이 경과함.
결국 d0+d1+d2+d3의 치수가 설정 연삭깊이보다 연삭이 되지 않아 연삭 잔량이 남게 됨.
이때 G 점에서 연삭깊이의 이송을 중지하고 연삭을 계속하면 탄성변형이 회복되면서 스파크 아웃 상태에 도달하게 되어 실제 절삭량은 BB´ 만큼 증가하게 됨.
4. 연삭열과 연삭온도 측정법
(1) 개요
연삭 시에는 부(-)의 경사각을 가진 연삭입자의 절삭날이 고속으로 가공물을 절삭하게 되어 거의 가공물에 용융점에 가까운 연삭열이 발생하게 됨.
이러한 열은 절삭유와 칩에 의해 제거되고 가공물 및 숫돌바퀴에 전도되는데 연삭열에 의해 가공물이 가열되면 열팽창에의해 가공 정밀도가 저하되며 다듬질면이 산회되어 내마모성이 떨어지거나 경화강 등은 뜨임이 되어 경도가 약해짐.
열 발생이 심할 경우 가공 중 또는 가공 후에 미세한 연삭균열이 발생하므로 연삭 시에는 연삭열의 발생을 최소화해야 하고 연삭액도 냉각 성능이 뛰어난 것을 사용해야 함.
(2) 연삭온도
1) 연삭입자의 연삭점 온도
입자의 연삭점 온도는 연삭입자가 연삭 시 절삭날 끝의 온도로서 일반적으로 수백 도 이상이며 연삭입자의 손모와 관계가 깊고 개개의 연삭입자의 절삭날을 수십 ~수백 μm에 걸친 면에서 가공물과 접촉하여 절삭작용을 수행하게 됨.
2) 숫돌 연삭점 온도
숫돌과 가공물의 겉보기 접촉면에서의 평균적인 온도이며 가공물의 열 손상과 관계가 있음.
3) 가공물의 평균 상승 온도
연삭열이 유입되어 연삭액이나 공기의 접촉에 의해 제거되고 남은 열로서 연삭시간과 더불어 상승하여 유입 열과 방열이 같아지면 일정한 평균 온도를 나타내고 열팽창에 의한 치수 정밀도의 저하와 관계가 있으며 다량의 연삭액 사용을 통해 10℃ 이내로 억제할 수 있음.
(3) 연삭온도 측정법
1) 연삭입자의 연삭점 온도 측정
(가) 가공물과 숫돌을 열전쌍으로 하는 방법
SiC 연삭 입자는 반도체이므로 이 숫돌과 가공물을 열전쌍으로 하여 열기전력을 측정하는 방법.
(나) 가공물과 미세 도선을 이용한 방법
도체인 가공물을 2개로 분할하여 운모와 같은 절연막을 사이에 두고 백금 선 등의 미세도선을 끼워넣고 결합하여 연삭 시 미세도선과 가공물과의 열 접점을 이용하여 오실로스코프 등으로 절삭날 끝 온도를 검출함.
2) 숫돌 연삭점 온도
(가) 열전쌍을 이용하는 방법
수평형 평면 연삭기 등에서 이용되는 방법으로 가공물의 뒷면에 가는 구멍을 뚫고 콘스탄탄선 등을 구멍 끝에 접촉시켜 오실로스코프로 열기전력을 측정하는 방법.
열 접점이 숫돌 외주에서 막 절단될 때의 검출온도가 숫돌 연삭점 온도이며 연삭깊이에 따른 온도 분포를 알 수 있음.
(나) 방사 온도계에 의한 방법
숫돌을 관통하는 작은 구멍을 뚫고 방사 온도계를 고정하여 가공면에서부터의 적외선 방사 온도를 측정하는 방법.
(다) 연삭에 의한 변색이나 시온도료의 변색에 의한 방법.
3) 가공물의 평균 온도
칼로 미터에 의한 방법.
시오 도료의 변색에 의한 방법.
(4) 연삭 시의 온도 상승을 억제하는 방법
냉각 능력이 우수한 연삭액을 다량 사용할 것.
입도가 크고 결합도가 작으며 조직이 거친 숫돌을 사용할 것.
숫돌바퀴의 속도 및 절입깊이, 접촉면적을 작게 할 것.
이송을 크게 할 것.
눈무딤, 눈메움이 된 숫돌은 바로 수정할 것.
5. 연삭 가공면의 손상 형태
(1) 개요
연삭 가공면은 고온•고속의 절삭 및 마찰 현상에 의해 가공면이 심한 변질을 받으며 연삭열에 의해 열팽창이 발생되고 가공물의 내부에는 잔류응력이 발생함.
연삭 가공면의 손상 형태는 가공 변질층, 잔류응력, 연삭버닝과 연삭균열로 구분할 수 있음.
(2) 가공 변질층
1) 가공 변질층의 생성 원인
절삭성이 나쁜 숫돌로 다듬질 연삭하는 경우 마찰에 의한 역학적 작용.
절삭깊이가 과도하게 큰 경우 절삭저항에 의한 응력.
과대한 연삭열로 인한 조직의 변화.
2) 변질 현상
(가) 표면 경도 변화
기계적 응력에 의한 가공경화.
연삭열에 의한 담금질 경화 및 뜨임으로 인한 연화.
(나) 열응력, 변태응력에 의한 잔류응력층의 형성
(다) 연삭균열
(3) 잔류응력
1) 발생 원인과 영향
연삭 가공 시에는 연삭열과 마찰 및 절삭에 따른 소성변형이 가공물의 표면층에 가해지며 이로 인해 잔류응력이 발생됨.
잔류응력은 가공 후에 서서히 소멸하여 제품의 치수적인 경년 변화를 초래하는데 잔류응력이 매우 큰 경우에는 시효균열이 발생함.
2) 대책
잔류응력이 작은 연삭 조건 선택.
연삭 후 처리.(서브제로, 풀림, 인공시효)
(4) 연삭버닝과 연삭균열
1) 정의
(가) 연삭버닝
연삭 시 가공면에 연삭열로 인해 다듬질면이 산화되어 그 산화막이 빛의 간섭에 의해 막 두께에 따른 착색이 발생되는 것.
(나) 연삭균열
연삭열에 의한 열팽창 또는 재질의 변화 등이 원인으로서 공석강에 가까운 탄소강이나 담금질한 재료의 연삭면에 발생하는 미세균열.
2) 발생 원인
숫돌바퀴의 원주속도가 크고 절삭깊이가 깊음.
숫돌의 입도가 작고 결합도가 높음.
피삭재의 발열성이 큼.
건식 연삭인 경우 발생.
3) 방지 대책
(가) 연삭온도가 낮은 연삭 조건 선택
연삭액을 충분히 사용하여 발열을 억제할 것.
연한 숫돌을 사용하고 이송을 크게 할 것.
절삭깊이를 작게 하여 절삭압력을 감소시킬 것.
(나) 가공물 열처리 시 최적의 조건 선택
6. 연삭 조건의 선정 방법
(1) 개요
가공물과 숫돌의 크기, 모양, 재질이나 연삭 방법에 따라 숫돌바퀴의 원주속도, 이송속도, 절삭깊이 등이 다르며 이와 같은 조건은 서로 관계를 가지고 연삭작용에 영향을 미침.
(2) 숫돌의 원주속도
숫돌이 원주속도는 연삭능률과 관계가 깊고 원주속도가 너무 느리면 숫돌의 손모가 심하고 원주속도가 지나치게 빠르면 숫돌의 절삭성이 저하하며 원심력에 의해 파괴될 위험이 있음.
일반적인 비트리파이드 숫돌인 경우 원통 외면 연삭은 1700 ~ 2000m/min, 내면 연삭은 600 ~ 1800m/min, 평면 연삭은 1200 ~ 1800m/min, 공구 연삭은 1400 ~ 1800m/min의 원주속도를 가짐.
단, 원통 연삭기의 경우 숫돌과 가공물의 회전 방향이 다를 경우에는
V = V₁+ V₂(m/min)
여기서 V₁ = 연삭숫돌의 원주 속도, V₂ = 가공물의 원주 속도
(3) 가공물의 원주속도
가공물의 원주속도는 숫돌의 원주속도와 깊은 관계를 갖고 있으며 이 속도비(숫돌바퀴의 속도/가공물 속도)는 다듬질면의 표면 거칠기, 연삭능률에 큰 영향을 미침.
속도비는 보통 1/100 정도로 하며 가공물의 재질, 숫돌의 성질, 숫돌의 폭, 다듬질면의 표면 거칠기 등을 함께 고려하여 결정해야 함.
고속 연삭에서는 속도비를 크게 하여 가공능률과 가공 변질층 면에서 유리한 결과를 얻기도 하며 가공물의 원주속도가 빠르면 숫돌 절삭저항이 커짐.
(4) 이송속도
원통 트래버스 연삭에서의 이송속도는 가공물의 원주속도와 서로 관계하며 일반적으로 가공물의 이송이 작으면 다듬질면이 양호해짐.
가공물의 축 방향 이송은 가공물 1회전에 대하여 숫돌폭(B) 이하로 선정해야 하며 다음의 표준값을 선택해야 함.
(5) 연삭깊이
연삭깊이는 연삭능률에 영향을 미치며 가공물의 재질, 연삭 방법, 연삭 정밀도 등에 따라서 연삭깊이를 결정함.
가공물의 원주속도가 빠르거나 숫돌바퀴의 원주속도가 느릴수록 연삭깊이를 깊게 줄 수 있으며 거친 연삭에서는 가능한 한 연삭깊이를 깊게 주고 다듬질 연삭 시에는 얕게 주어야 함.
연삭깊이는 다음과 같이 선정함.
(6) 연삭여유
연삭여유는 가공물의 재질, 모양, 치수, 전 가공의 다듬질면의 표면 거칠기 등에 따라 다르나 되도록이면 작을수록 좋으며 선반 가공 시에는 0.3 ~ 0.8mm의 여유를 두고 가공하면 됨.
연삭여유가 너무 적으면 전 가공 시 시간이 많이 걸리므로 가공물의 지름, 길이, 연삭 방법에 따라 적절한 연삭여유를 선정해야 함.
(7) 연삭비
연삭비 = 가공물의 연삭된 부피/ 숫돌바퀴의 소모된 부피
7. 연삭 숫돌의 드레싱 및 트루잉
(1) 개요
연삭 숫돌이 눈탈락, 눈무딤, 눈메움을 일으키게 되면 연삭성이 떨어지고 떨림, 발열 등이 발생하므로 연삭성을 회복시키기 위해 새로운 예리한 연삭입자를 표면에 나타나도록 하는 것을 드레싱이라 함.
숫돌바퀴의 질이 균일하지 못하거나 가공물의 영향을 받아 숫돌바퀴의 모양이 점차 변하게 되며 특히 나사나 기어의 연삭, 윤곽 연삭 등에 있어서는 정확한 숫돌 형상이 필요하므로 숫돌의 형상을 정확하게 깎아내는 작업을 트루잉이라 하고 트루잉을 하면 동시에 드레싱도 됨.
(2) 드레싱의 필요성
눈탈락, 눈무딤, 눈메움 등이 발생하면 연삭성이 떨어지기 때문에 드레싱이 통해 연삭성을 회복시켜야 함.
(3) 숫돌바퀴의 수정 공구
1) 핸팅톤 드레서
(가) 형상 및 작업 방법
담금질된 강판재의 파형 원판을 다수 겹쳐서 홀더축에 끼운 것으로서 가장 간단한 공구로서 회전하는 숫돌 표면에 드레서를 접촉시키면 회전하여 파형 모서리에 충격에 의해 숫돌 표면이 드레싱됨.
(나) 용도
정밀도를 그리 필요로 하지 않는 연삭숫돌의 드레싱에 사용하며 성형 연삭 숫돌, 정밀 연삭 숫돌에는 사용하지 않음.
2) 연삭숫돌을 사용한 드레싱
탄화규소제 비트리파이드 숫돌에서 결합도가 굳은 드레싱용 숫돌을 이용하여 수정하고자 하는 숫돌과 접촉 회전시킨 후 브레이크를 걸어 상대 미끄럼을 통해 드레싱하는 것으로 비교적 매끈하고 정밀도가 높은 숫돌면을 얻을 수 있음.
3) 다이아몬드 드레서
가장 널리 사용하는 것을 모든 숫돌의 드레싱 및 트루잉에 사용할 수 있음.
형상이나 다이아몬드 개수에 따라 여러 종류가 있으며3 드레싱할 때는 숫돌의 수평 중심방향에서 3˚ ~ 15˚ 위로 기울여 드레서를 접촉시키고 절삭깊이가 너무 깊으면 다이아몬드의 마모가 커지므로 0.02mm 이하로 절삭깊이를 주고 시행해야 함.
4) 크러시 롤러
총형 연삭을 할 때 숫돌을 가공물의 반대 모양으로 성형하여 드레싱하기 위해 롤러로서 숫돌을 저속 회전시켜서 이것에 담금질된 크러시 롤러를 접촉시키면 숫돌면이 부서지면서 총형으로 드레싱과 트루잉이 됨.
크러시 롤러는 나사 연삭, 윤곽 연삭 숫돌과 같은 숫돌바퀴를 복잡한 형상으로 수정하는데 효과적임.
5) 로터리 드레서
큰 입자의 다이아몬드 연삭입자를 숫돌 외주면에 배열하여 소결 시킨 것으로 드레서를 회전시켜 숫돌과 접촉하면 절삭작용에 의해 드레싱과 트루잉을 동시에 할 수 있음.
6) 전해 드레싱
최근 정보통신기기 및 O/A에 사용되는 부품은 높은 정밀도와 고품질의 저렴한 가격을 요구하고 있는데 이러한 요구를 만족하기 위한 연삭법으로 전해 드레싱이 개발되어 생산 현장에서 이용되고 있음.
전해 드레싱은 미세립의 지석을 사용하여 드레싱을 하면서 연삭하는 방법으로 지석의 로딩을 방지하고 고능률로 가공할 수 있는 센터리스 연삭기에 채용하여 좋은 결과를 얻고 있음.
전해 드레싱의 원리는 전기분해로 메탈 본드를 녹여서 제거하면 지립이 돌출되는 동시에 산화 피막이 만들어지고 산화 피막이 지립을 탄력적으로 유지하기 때문에 고품질의 연삭이 가능하게끔 함.
전해 드레싱은 다음과 같은 특징을 가지고 있음.
– 지석의 절삭성이 양호하여 1공정으로 가공이 가능.
– 트루잉과 드레싱을 자동화할 수 있음.
– 경면 가공이 가능.
– 연속적인 라인 생산을 통하여 생산능률을 높일 수 있음.
8. 연삭액의 사용 목적과 주가법
(1) 개요
연삭에서는 절삭과 달리 연삭열에 의해 가공물이 가열되어 가공 정밀도의 저하, 내마모성의 저하, 조직의 변화, 연삭균열 등의 문제점이 나타나므로 일반적으로 연삭액을 사용하며 연삭액은 가공물의 면 상태나 숫돌의 마멸에 직접 영향을 미치게 됨.
(2) 연삭액의 기능과 구비 조건
1) 기능
가공물 및 연삭 숫돌을 냉각함.
연삭입자 절삭날과 칩과의 윤활작용을 좋게 하여 연삭입자의 마모 및 용착을 억제함.
칩이나 탈락된 연삭입자를 씻어내어 숫돌의 눈메움을 억제함.
2) 구비 조건
냉각성, 윤활성, 유동성이 좋아야 함.
부식과 변질이 되지 말아야 하고 화학 반응이 없어야 함.
연삭열에 의해 증발되지 않아야 함.
(3) 연삭액의 종류
1) 불수용성 연삭액
광유, 지방유 등에 각종 첨가제를 가하여 냉각 성능보다는 윤활 성능을 중시한 것으로서 숫돌의 마찰을 작게 해주고 눈메움 현상억제에 효과가 있으며 나사 연삭, 총형 연삭 등에 쓰임.
2) 수용성 연삭액
일반적으로 많이 사용되는 것으로서 방청제, 계면활성제를 다량의 물에 첨가하여 냉각 등을 중시한 것이며 보통 원통 연삭, 평면 연삭 등에 쓰임.
(4) 연삭액 주가법
1) 노즐 주가
일반적인 방법으로 연삭액 받이, 펌프, 회수 장치가 있어 노즐을 사용하여 가공물과 연삭숫돌 사이에 연삭 전에 연삭액을 주가함.
2) 통액 주가
숫돌바퀴의 다공성을 이용한 것으로 숫돌 내부에서 연삭입자의 날끝으로 원심력에 의해 분무되어 주가하는 방법이며 경합금 연삭 시와 같이 눈메움이 있는 경우에 효과적임.
연삭액의 주가량이 적으므로 노즐 주가와 병행함.
3) 제트 주가
숫돌바퀴 작업면에 직각으로 제트 분사하여 칩을 불어 날려서 눈메움을 방지하며 연삭액에 초음파를 걸어서 억제하는 방법도 있음.
9. 연삭 시의 결함 및 대책
(1) 개요
연삭 시에 가공물에 나타나는 가공 결함으로서 떨림, 다듬질면 불량, 정밀도 불량 등이 있음.
(2) 연삭 시의 결함 및 대책
1) 떨림
(가) 다듬질면에 떨림 자국이 발생
① 연삭숫돌 자체의 불균형
– 숫돌의 균형을 다시 잡을 것.
– 트루잉 후 균형을 다시 교정할 것.
– 연삭액을 가하지 않고 숫돌을 운전하여 함유된 연삭액을 제거할 것.
② 숫돌의 진원 불량
– 균형을 잡기 전후에 트루잉을 할 것.
– 숫돌의 양측면의 형상을 교정할 것.
③ 숫돌의 결합도 과대
– 결합도가 약한 숫돌 선택할 것.
– 입도와 조직이 거친 것을 선택할 것.
④ 센터 및 센터레스트의 사용법 불량
– 센터와 센터레스트의 맞춤을 확인할 것.
– 윤활을 충분히 할 것.
⑤ 연삭기 자체의 진동
– 설치 시의 문제 요인을 검사할 것.
2) 다듬질면의 불량
(가) 폭이 좁고 깊은 규칙적인 줄 자국 발생
① 숫돌입자가 큼
– 입도가 미세한 숫돌을 사용할 것.
(나) 폭이 좁고 깊은 불규칙한 줄 자국 발생
① 숫돌 결합도가 작음
– 결합도가 큰 숫돌을 사용할 것.
(다) 가는 나사 모양 흠집 발생
① 드레싱 불량
– 드레서의 이송을 작고 균일하게 할 것.
– 다이아몬드 또는 홀더의 장착을 확실하게 할 것.
– 다이아몬드의 절삭깊이를 얕게 할 것.
– 드레싱은 숫돌의 끝에서부터 시작할 것.
– 숫돌의 양끝 가장자리는 둥글게 할 것.
② 연삭 작업 불량
– 숫돌면과 가공물이 평행하도록 하여 연삭할 것.
– 숫돌압력을 감소시킬 것.
– 센터레스트를 추가 설치할 것.
– 가공물 1회전에 대한 숫돌 이송을 작게 할 것.
– 이송속도를 조금씩 변경할 것.
(라) 길이나 폭이 불규칙한 홈 발생
① 불결한 연삭액 사용
– 연삭액 탱크를 깨끗하게 할 것.
– 안전 커버를 깨끗하게 할 것.
(마) 이송 마크 발생
① 중심맞춤 불량
– 가공물 센터의 중심맞춤을 확인할 것.
– 숫돌축과 가공물의 중심맞춤을 확인할 것.
② 트루잉 불량
– 다이아몬드를 수평보다 5˚ 하향으로 장착할 것.
– 숫돌의 양끝 가장자리를 둥글게 할 것.
3) 가공물의 정밀도 불량
(가) 가공물의 진원도, 테이퍼, 평행도 불량
① 센터 또는 센터레스트의 중심맞춤 불량
– 센터 또는 센터레스트의 장착 상태를 확인할 것.
– 급유를 충분하게 할 것.
– 적당한 방진구를 사용할 것.
② 드레싱 불량
– 숫돌을 연삭 시와 같은 상태에서 드레싱할 것.
③ 연삭 작업 불량
– 이송 양끝에서 숫돌이 가공물을 벗어나지 않도록 할 것.
– 숫돌압력을 감소시킬 것.
– 결합도가 굳은 숫돌을 사용할 것.
④ 가공물의 팽창
– 연삭액을 다량 사용할 것.
– 연삭깊이를 얕게 하여 연삭저항을 줄일 것.
– 결합도가 약한 숫돌을 사용하고 약하게 작용시킬 것.
이상으로 연삭의 특성에 대한 연재를 마치고 다음에는 래핑에 대한 연재를 시작할 예정입니다.
2020년 10월 16일
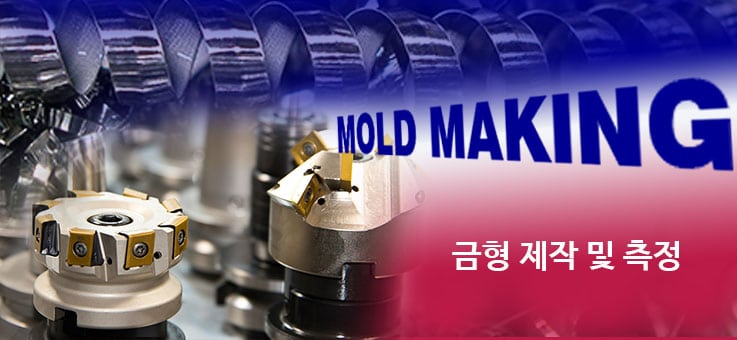
금형 제작 8
제8장 연삭의 특성
연삭의 특징 연삭작용, 자생작용, 숫돌면의 변화가 발생하는데 재생작용은 마멸된 숫돌입자가 탈락하여 새 날이 생기는 현상으로 숫돌입자의 마멸→파괴→탈락→생성이 주기적으로 반복되며 눈탈락→ 눈무딤→ 눈메움과 같은 숫돌면의 변화가 일어나게 됩니다.
1. 연삭 시 발생하는 작용
(1) 연삭작용
WS는 절입 또는 연삭깊이를 의미함.
숫돌바퀴의 절입이 증가하면 연삭저항이 증가하게 됨.
연삭 시 배분력이 주분력의 2배로 작용함.
(2) 자생작용
자생작용이란 마멸된 숫돌입자가 탈락하여 새 날이 생기는 현상으로 숫돌입자의 마멸 → 파괴 → 탈락 → 생성이 주기적으로 반복됨.
장시간 좋은 가공면을 유지할 수 있고 공구 교환이나 재연삭 공정을 생략할 수 있으며 숫돌바퀴의 선택과 적절한 연삭 조건이 필요함.
(3) 숫돌면의 변화
1) 눈탈락
눈탈락은 과도한 자생작용이 발생 시에 숫돌입자의 끝이 충분히 파쇄되지 않고 마모하였을 때 결합제가 파쇄되어 숫돌입자가 입자 그대로 빠져나가는 현상이 일어나는데 숫돌바퀴의 결합도가 작업에 대해 지나치게 낮을 경우 발생되며 숫돌의 손모가 심하고 가공면도 나빠짐.
2) 눈무딤
눈무딤은 자생작용의 부족으로 입자의 표면이 평탄해지는 상태.
(가) 원인
연삭 숫돌의 결합도가 높을 때.
연삭 숫돌의 원주속도가 너무 클 때.
숫돌의 재료가 가공물의 재료에 부적합할 때.
(나) 현상
연삭성이 불량하고 가공물에 열이 발생함.
연삭 손실이 발생함.
3) 눈메움
눈메움은 결합도가 높은 숫돌로 연성 재료를 연삭 시 숫돌 표면의 기공에 칩이 메워지는 현상.
(가) 원인
숫돌입자가 너무 작을 때.
조직이 너무 치밀할 때.
연삭깊이가 깊을 때.
숫돌바퀴의 원주속도가 느릴 때.
(나) 현상
연삭성이 불량하고 다듬질면이 거칠어짐.
다듬질면에 떨림 자리와 같은 상처가 생김.
숫돌입자가 마모되기 쉬움.
2. 특수 연삭 가공 기술
(1) 고속 연삭
1) 정의
연삭 능률 향상을 위해 숫돌 원주속도를 보통의 연삭에서보다 2~3배 크게 한 것으로 가공물 속도나 연삭깊이를 깊게할 수 있어 가공능률이 향상됨.
2) 특징
스파크 아웃 시간을 단축할 수 있음.
연삭저항이 감소하고 가공 정밀도가 향상됨.
숫돌의 손모가 적어 숫돌의 수명이 향상됨.
(2) 크림피드 연삭
1) 정의
종래의 평면 연삭법에 비하여 연삭깊이를 깊게 하고 테이블 이송속도를 매우 느리게 하여 1회 또는 수 회의 이송으로 가공하는 방법으로 숫돌의 원주면을 사용하는 성형 연삭을 고능률화 시킨 것.
2) 특징
숫돌의 마모가 비교적 균일하고 숫돌 윤곽 형상의 변화가 적음.
연삭저항의 변동이 심하고 가공 상태가 불안정할 수 있음.
숫돌 접촉면적이 크고 연삭열의 발생, 연삭균열의 우려가 있음.
(3) 중 연삭
1) 정의
연삭깊이나 가공물의 속도를 크게 하고 단위 시간당 연삭량을 증가시켜 가공능률을 향상시키는 연삭 방법.
2) 종류 및 특징
(가) 슬랩 연삭(SLAB GRINDING)
버 제거, 슬랩의 표피 연삭 등 가공 정도에 비교적 문제가 안 되는 경우 사용됨.
(나) 연마 가공(ABRASIVE MACHING)
높은 연삭능률과 가공 정도를 동시에 얻기 위한 방법으로서 평면 연삭 가공에는 세그먼트형 숫돌을 사용한 고마력의 연삭기가 사용됨.
3. 연삭면의 형성과 스파크 아웃
(1) 개요
연삭 다듬질면은 연삭입자의 절삭날에 의해 절삭된 가공면으로서 연삭 조건에 큰 영향을 받으며 특히 절삭날의 밀도가 중요함.
다듬질면의 거칠기 형상을 위해서는 적절한 날 교정에 의해서 숫돌 표면의 절삭날 높이를 균일하게 하고 밀도를 높이는 것이 무엇보다 중요시됨.
연삭 시에는 설정 절삭깊이만큼 실제로 절삭되지 않으며 여러 요인에 의해 연삭 잔량이 생기게 됨.
(2) 다듬질면에 영향을 주는 요인
1) 입도
입도가 고울수록 다듬질면의 거칠기는 향상되는데 그 감소의 정도는 입도가 거친 영역에서 크고 연삭입자는 연삭저항에 의해 마멸되며 그 마멸 정도가 균일한 것이 다듬질면에 큰 영향을 미침.
2) 결합도
같은 입도의 숫돌로 적당한 연삭 조건하에서 연삭 시 결합도가 굳은 숫돌의 다듬질면이 일반적으로 좋아지는 경향이 있음.
3) 절삭깊이
절삭깊이의 증가에 따라 다듬질면의 거칠기도 증가하며 각각의 절삭날에 작용하는 힘이 증가하여 연삭입자의 마멸이 심해지기 때문이고 동시에 연삭기에 걸리는 부하의 증가로 인한 진동의 요인도 수반함.
4) 이송
이송속도의 증가에 따라 다듬질면의 거칠기도 거의 비례적으로 증가함.
5) 진동
연삭숫돌과 가공물 사이에 상대 진동이 있으면 절삭날의 밀도가 거칠어지므로 조도가 커짐.
6) 절삭잔량
절삭잔량이 있으면 거칠어지며 반복 연삭을 통해 절삭잔량이 적어질 때 다듬질면의 거칠기도 향상되고 절삭깊이가 깊거나 이송속도가 빨라지면 절삭잔량도 많아짐.
(3) 스파크 아웃
1) 정의
연삭 시 숫돌의 마모가 거의 없고 가공물과 숫돌축이 강체라면 설정된 절삭깊이만큼 연삭이 되겠지만 실제로는 여러 요인에 의해 연삭 잔량이 남게 되는데 이때 더 이상의 절삭깊이 이송을 중지하고 연삭을 계속하면 탄성변형이 회복되면서 실 연삭량이 증가되는 상태를 말함.
2) 절삭 잔량 요인
숫돌바퀴의 마모(d0).
숫돌축 및 가공물의 휨(d1).
가공물과 숫돌 접촉 부의 탄성변형(d2).
연삭 입자가 절삭하지 않고 가공물을 밀어젖히는 현상(d3).
3) 연삭면의 형성
설정 절삭깊이가 OG와 같이 경과해도 OP는 탄성변형에 의해 PC는 가공물을 밀어젖힐 때 절삭깊이의 양이 소비되어 실제 가공 치수는 OPCB와 같이 경과함.
결국 d0+d1+d2+d3의 치수가 설정 연삭깊이보다 연삭이 되지 않아 연삭 잔량이 남게 됨.
이때 G 점에서 연삭깊이의 이송을 중지하고 연삭을 계속하면 탄성변형이 회복되면서 스파크 아웃 상태에 도달하게 되어 실제 절삭량은 BB´ 만큼 증가하게 됨.
4. 연삭열과 연삭온도 측정법
(1) 개요
연삭 시에는 부(-)의 경사각을 가진 연삭입자의 절삭날이 고속으로 가공물을 절삭하게 되어 거의 가공물에 용융점에 가까운 연삭열이 발생하게 됨.
이러한 열은 절삭유와 칩에 의해 제거되고 가공물 및 숫돌바퀴에 전도되는데 연삭열에 의해 가공물이 가열되면 열팽창에의해 가공 정밀도가 저하되며 다듬질면이 산회되어 내마모성이 떨어지거나 경화강 등은 뜨임이 되어 경도가 약해짐.
열 발생이 심할 경우 가공 중 또는 가공 후에 미세한 연삭균열이 발생하므로 연삭 시에는 연삭열의 발생을 최소화해야 하고 연삭액도 냉각 성능이 뛰어난 것을 사용해야 함.
(2) 연삭온도
1) 연삭입자의 연삭점 온도
입자의 연삭점 온도는 연삭입자가 연삭 시 절삭날 끝의 온도로서 일반적으로 수백 도 이상이며 연삭입자의 손모와 관계가 깊고 개개의 연삭입자의 절삭날을 수십 ~수백 μm에 걸친 면에서 가공물과 접촉하여 절삭작용을 수행하게 됨.
2) 숫돌 연삭점 온도
숫돌과 가공물의 겉보기 접촉면에서의 평균적인 온도이며 가공물의 열 손상과 관계가 있음.
3) 가공물의 평균 상승 온도
연삭열이 유입되어 연삭액이나 공기의 접촉에 의해 제거되고 남은 열로서 연삭시간과 더불어 상승하여 유입 열과 방열이 같아지면 일정한 평균 온도를 나타내고 열팽창에 의한 치수 정밀도의 저하와 관계가 있으며 다량의 연삭액 사용을 통해 10℃ 이내로 억제할 수 있음.
(3) 연삭온도 측정법
1) 연삭입자의 연삭점 온도 측정
(가) 가공물과 숫돌을 열전쌍으로 하는 방법
SiC 연삭 입자는 반도체이므로 이 숫돌과 가공물을 열전쌍으로 하여 열기전력을 측정하는 방법.
(나) 가공물과 미세 도선을 이용한 방법
도체인 가공물을 2개로 분할하여 운모와 같은 절연막을 사이에 두고 백금 선 등의 미세도선을 끼워넣고 결합하여 연삭 시 미세도선과 가공물과의 열 접점을 이용하여 오실로스코프 등으로 절삭날 끝 온도를 검출함.
2) 숫돌 연삭점 온도
(가) 열전쌍을 이용하는 방법
수평형 평면 연삭기 등에서 이용되는 방법으로 가공물의 뒷면에 가는 구멍을 뚫고 콘스탄탄선 등을 구멍 끝에 접촉시켜 오실로스코프로 열기전력을 측정하는 방법.
열 접점이 숫돌 외주에서 막 절단될 때의 검출온도가 숫돌 연삭점 온도이며 연삭깊이에 따른 온도 분포를 알 수 있음.
(나) 방사 온도계에 의한 방법
숫돌을 관통하는 작은 구멍을 뚫고 방사 온도계를 고정하여 가공면에서부터의 적외선 방사 온도를 측정하는 방법.
(다) 연삭에 의한 변색이나 시온도료의 변색에 의한 방법.
3) 가공물의 평균 온도
칼로 미터에 의한 방법.
시오 도료의 변색에 의한 방법.
(4) 연삭 시의 온도 상승을 억제하는 방법
냉각 능력이 우수한 연삭액을 다량 사용할 것.
입도가 크고 결합도가 작으며 조직이 거친 숫돌을 사용할 것.
숫돌바퀴의 속도 및 절입깊이, 접촉면적을 작게 할 것.
이송을 크게 할 것.
눈무딤, 눈메움이 된 숫돌은 바로 수정할 것.
5. 연삭 가공면의 손상 형태
(1) 개요
연삭 가공면은 고온•고속의 절삭 및 마찰 현상에 의해 가공면이 심한 변질을 받으며 연삭열에 의해 열팽창이 발생되고 가공물의 내부에는 잔류응력이 발생함.
연삭 가공면의 손상 형태는 가공 변질층, 잔류응력, 연삭버닝과 연삭균열로 구분할 수 있음.
(2) 가공 변질층
1) 가공 변질층의 생성 원인
절삭성이 나쁜 숫돌로 다듬질 연삭하는 경우 마찰에 의한 역학적 작용.
절삭깊이가 과도하게 큰 경우 절삭저항에 의한 응력.
과대한 연삭열로 인한 조직의 변화.
2) 변질 현상
(가) 표면 경도 변화
기계적 응력에 의한 가공경화.
연삭열에 의한 담금질 경화 및 뜨임으로 인한 연화.
(나) 열응력, 변태응력에 의한 잔류응력층의 형성
(다) 연삭균열
(3) 잔류응력
1) 발생 원인과 영향
연삭 가공 시에는 연삭열과 마찰 및 절삭에 따른 소성변형이 가공물의 표면층에 가해지며 이로 인해 잔류응력이 발생됨.
잔류응력은 가공 후에 서서히 소멸하여 제품의 치수적인 경년 변화를 초래하는데 잔류응력이 매우 큰 경우에는 시효균열이 발생함.
2) 대책
잔류응력이 작은 연삭 조건 선택.
연삭 후 처리.(서브제로, 풀림, 인공시효)
(4) 연삭버닝과 연삭균열
1) 정의
(가) 연삭버닝
연삭 시 가공면에 연삭열로 인해 다듬질면이 산화되어 그 산화막이 빛의 간섭에 의해 막 두께에 따른 착색이 발생되는 것.
(나) 연삭균열
연삭열에 의한 열팽창 또는 재질의 변화 등이 원인으로서 공석강에 가까운 탄소강이나 담금질한 재료의 연삭면에 발생하는 미세균열.
2) 발생 원인
숫돌바퀴의 원주속도가 크고 절삭깊이가 깊음.
숫돌의 입도가 작고 결합도가 높음.
피삭재의 발열성이 큼.
건식 연삭인 경우 발생.
3) 방지 대책
(가) 연삭온도가 낮은 연삭 조건 선택
연삭액을 충분히 사용하여 발열을 억제할 것.
연한 숫돌을 사용하고 이송을 크게 할 것.
절삭깊이를 작게 하여 절삭압력을 감소시킬 것.
(나) 가공물 열처리 시 최적의 조건 선택
6. 연삭 조건의 선정 방법
(1) 개요
가공물과 숫돌의 크기, 모양, 재질이나 연삭 방법에 따라 숫돌바퀴의 원주속도, 이송속도, 절삭깊이 등이 다르며 이와 같은 조건은 서로 관계를 가지고 연삭작용에 영향을 미침.
(2) 숫돌의 원주속도
숫돌이 원주속도는 연삭능률과 관계가 깊고 원주속도가 너무 느리면 숫돌의 손모가 심하고 원주속도가 지나치게 빠르면 숫돌의 절삭성이 저하하며 원심력에 의해 파괴될 위험이 있음.
일반적인 비트리파이드 숫돌인 경우 원통 외면 연삭은 1700 ~ 2000m/min, 내면 연삭은 600 ~ 1800m/min, 평면 연삭은 1200 ~ 1800m/min, 공구 연삭은 1400 ~ 1800m/min의 원주속도를 가짐.
단, 원통 연삭기의 경우 숫돌과 가공물의 회전 방향이 다를 경우에는
V = V₁+ V₂(m/min)
여기서 V₁ = 연삭숫돌의 원주 속도, V₂ = 가공물의 원주 속도
(3) 가공물의 원주속도
가공물의 원주속도는 숫돌의 원주속도와 깊은 관계를 갖고 있으며 이 속도비(숫돌바퀴의 속도/가공물 속도)는 다듬질면의 표면 거칠기, 연삭능률에 큰 영향을 미침.
속도비는 보통 1/100 정도로 하며 가공물의 재질, 숫돌의 성질, 숫돌의 폭, 다듬질면의 표면 거칠기 등을 함께 고려하여 결정해야 함.
고속 연삭에서는 속도비를 크게 하여 가공능률과 가공 변질층 면에서 유리한 결과를 얻기도 하며 가공물의 원주속도가 빠르면 숫돌 절삭저항이 커짐.
(4) 이송속도
원통 트래버스 연삭에서의 이송속도는 가공물의 원주속도와 서로 관계하며 일반적으로 가공물의 이송이 작으면 다듬질면이 양호해짐.
가공물의 축 방향 이송은 가공물 1회전에 대하여 숫돌폭(B) 이하로 선정해야 하며 다음의 표준값을 선택해야 함.
(5) 연삭깊이
연삭깊이는 연삭능률에 영향을 미치며 가공물의 재질, 연삭 방법, 연삭 정밀도 등에 따라서 연삭깊이를 결정함.
가공물의 원주속도가 빠르거나 숫돌바퀴의 원주속도가 느릴수록 연삭깊이를 깊게 줄 수 있으며 거친 연삭에서는 가능한 한 연삭깊이를 깊게 주고 다듬질 연삭 시에는 얕게 주어야 함.
연삭깊이는 다음과 같이 선정함.
(6) 연삭여유
연삭여유는 가공물의 재질, 모양, 치수, 전 가공의 다듬질면의 표면 거칠기 등에 따라 다르나 되도록이면 작을수록 좋으며 선반 가공 시에는 0.3 ~ 0.8mm의 여유를 두고 가공하면 됨.
연삭여유가 너무 적으면 전 가공 시 시간이 많이 걸리므로 가공물의 지름, 길이, 연삭 방법에 따라 적절한 연삭여유를 선정해야 함.
(7) 연삭비
연삭비 = 가공물의 연삭된 부피/ 숫돌바퀴의 소모된 부피
7. 연삭 숫돌의 드레싱 및 트루잉
(1) 개요
연삭 숫돌이 눈탈락, 눈무딤, 눈메움을 일으키게 되면 연삭성이 떨어지고 떨림, 발열 등이 발생하므로 연삭성을 회복시키기 위해 새로운 예리한 연삭입자를 표면에 나타나도록 하는 것을 드레싱이라 함.
숫돌바퀴의 질이 균일하지 못하거나 가공물의 영향을 받아 숫돌바퀴의 모양이 점차 변하게 되며 특히 나사나 기어의 연삭, 윤곽 연삭 등에 있어서는 정확한 숫돌 형상이 필요하므로 숫돌의 형상을 정확하게 깎아내는 작업을 트루잉이라 하고 트루잉을 하면 동시에 드레싱도 됨.
(2) 드레싱의 필요성
눈탈락, 눈무딤, 눈메움 등이 발생하면 연삭성이 떨어지기 때문에 드레싱이 통해 연삭성을 회복시켜야 함.
(3) 숫돌바퀴의 수정 공구
1) 핸팅톤 드레서
(가) 형상 및 작업 방법
담금질된 강판재의 파형 원판을 다수 겹쳐서 홀더축에 끼운 것으로서 가장 간단한 공구로서 회전하는 숫돌 표면에 드레서를 접촉시키면 회전하여 파형 모서리에 충격에 의해 숫돌 표면이 드레싱됨.
(나) 용도
정밀도를 그리 필요로 하지 않는 연삭숫돌의 드레싱에 사용하며 성형 연삭 숫돌, 정밀 연삭 숫돌에는 사용하지 않음.
2) 연삭숫돌을 사용한 드레싱
탄화규소제 비트리파이드 숫돌에서 결합도가 굳은 드레싱용 숫돌을 이용하여 수정하고자 하는 숫돌과 접촉 회전시킨 후 브레이크를 걸어 상대 미끄럼을 통해 드레싱하는 것으로 비교적 매끈하고 정밀도가 높은 숫돌면을 얻을 수 있음.
3) 다이아몬드 드레서
가장 널리 사용하는 것을 모든 숫돌의 드레싱 및 트루잉에 사용할 수 있음.
형상이나 다이아몬드 개수에 따라 여러 종류가 있으며3 드레싱할 때는 숫돌의 수평 중심방향에서 3˚ ~ 15˚ 위로 기울여 드레서를 접촉시키고 절삭깊이가 너무 깊으면 다이아몬드의 마모가 커지므로 0.02mm 이하로 절삭깊이를 주고 시행해야 함.
4) 크러시 롤러
총형 연삭을 할 때 숫돌을 가공물의 반대 모양으로 성형하여 드레싱하기 위해 롤러로서 숫돌을 저속 회전시켜서 이것에 담금질된 크러시 롤러를 접촉시키면 숫돌면이 부서지면서 총형으로 드레싱과 트루잉이 됨.
크러시 롤러는 나사 연삭, 윤곽 연삭 숫돌과 같은 숫돌바퀴를 복잡한 형상으로 수정하는데 효과적임.
5) 로터리 드레서
큰 입자의 다이아몬드 연삭입자를 숫돌 외주면에 배열하여 소결 시킨 것으로 드레서를 회전시켜 숫돌과 접촉하면 절삭작용에 의해 드레싱과 트루잉을 동시에 할 수 있음.
6) 전해 드레싱
최근 정보통신기기 및 O/A에 사용되는 부품은 높은 정밀도와 고품질의 저렴한 가격을 요구하고 있는데 이러한 요구를 만족하기 위한 연삭법으로 전해 드레싱이 개발되어 생산 현장에서 이용되고 있음.
전해 드레싱은 미세립의 지석을 사용하여 드레싱을 하면서 연삭하는 방법으로 지석의 로딩을 방지하고 고능률로 가공할 수 있는 센터리스 연삭기에 채용하여 좋은 결과를 얻고 있음.
전해 드레싱의 원리는 전기분해로 메탈 본드를 녹여서 제거하면 지립이 돌출되는 동시에 산화 피막이 만들어지고 산화 피막이 지립을 탄력적으로 유지하기 때문에 고품질의 연삭이 가능하게끔 함.
전해 드레싱은 다음과 같은 특징을 가지고 있음.
– 지석의 절삭성이 양호하여 1공정으로 가공이 가능.
– 트루잉과 드레싱을 자동화할 수 있음.
– 경면 가공이 가능.
– 연속적인 라인 생산을 통하여 생산능률을 높일 수 있음.
8. 연삭액의 사용 목적과 주가법
(1) 개요
연삭에서는 절삭과 달리 연삭열에 의해 가공물이 가열되어 가공 정밀도의 저하, 내마모성의 저하, 조직의 변화, 연삭균열 등의 문제점이 나타나므로 일반적으로 연삭액을 사용하며 연삭액은 가공물의 면 상태나 숫돌의 마멸에 직접 영향을 미치게 됨.
(2) 연삭액의 기능과 구비 조건
1) 기능
가공물 및 연삭 숫돌을 냉각함.
연삭입자 절삭날과 칩과의 윤활작용을 좋게 하여 연삭입자의 마모 및 용착을 억제함.
칩이나 탈락된 연삭입자를 씻어내어 숫돌의 눈메움을 억제함.
2) 구비 조건
냉각성, 윤활성, 유동성이 좋아야 함.
부식과 변질이 되지 말아야 하고 화학 반응이 없어야 함.
연삭열에 의해 증발되지 않아야 함.
(3) 연삭액의 종류
1) 불수용성 연삭액
광유, 지방유 등에 각종 첨가제를 가하여 냉각 성능보다는 윤활 성능을 중시한 것으로서 숫돌의 마찰을 작게 해주고 눈메움 현상억제에 효과가 있으며 나사 연삭, 총형 연삭 등에 쓰임.
2) 수용성 연삭액
일반적으로 많이 사용되는 것으로서 방청제, 계면활성제를 다량의 물에 첨가하여 냉각 등을 중시한 것이며 보통 원통 연삭, 평면 연삭 등에 쓰임.
(4) 연삭액 주가법
1) 노즐 주가
일반적인 방법으로 연삭액 받이, 펌프, 회수 장치가 있어 노즐을 사용하여 가공물과 연삭숫돌 사이에 연삭 전에 연삭액을 주가함.
2) 통액 주가
숫돌바퀴의 다공성을 이용한 것으로 숫돌 내부에서 연삭입자의 날끝으로 원심력에 의해 분무되어 주가하는 방법이며 경합금 연삭 시와 같이 눈메움이 있는 경우에 효과적임.
연삭액의 주가량이 적으므로 노즐 주가와 병행함.
3) 제트 주가
숫돌바퀴 작업면에 직각으로 제트 분사하여 칩을 불어 날려서 눈메움을 방지하며 연삭액에 초음파를 걸어서 억제하는 방법도 있음.
9. 연삭 시의 결함 및 대책
(1) 개요
연삭 시에 가공물에 나타나는 가공 결함으로서 떨림, 다듬질면 불량, 정밀도 불량 등이 있음.
(2) 연삭 시의 결함 및 대책
1) 떨림
(가) 다듬질면에 떨림 자국이 발생
① 연삭숫돌 자체의 불균형
– 숫돌의 균형을 다시 잡을 것.
– 트루잉 후 균형을 다시 교정할 것.
– 연삭액을 가하지 않고 숫돌을 운전하여 함유된 연삭액을 제거할 것.
② 숫돌의 진원 불량
– 균형을 잡기 전후에 트루잉을 할 것.
– 숫돌의 양측면의 형상을 교정할 것.
③ 숫돌의 결합도 과대
– 결합도가 약한 숫돌 선택할 것.
– 입도와 조직이 거친 것을 선택할 것.
④ 센터 및 센터레스트의 사용법 불량
– 센터와 센터레스트의 맞춤을 확인할 것.
– 윤활을 충분히 할 것.
⑤ 연삭기 자체의 진동
– 설치 시의 문제 요인을 검사할 것.
2) 다듬질면의 불량
(가) 폭이 좁고 깊은 규칙적인 줄 자국 발생
① 숫돌입자가 큼
– 입도가 미세한 숫돌을 사용할 것.
(나) 폭이 좁고 깊은 불규칙한 줄 자국 발생
① 숫돌 결합도가 작음
– 결합도가 큰 숫돌을 사용할 것.
(다) 가는 나사 모양 흠집 발생
① 드레싱 불량
– 드레서의 이송을 작고 균일하게 할 것.
– 다이아몬드 또는 홀더의 장착을 확실하게 할 것.
– 다이아몬드의 절삭깊이를 얕게 할 것.
– 드레싱은 숫돌의 끝에서부터 시작할 것.
– 숫돌의 양끝 가장자리는 둥글게 할 것.
② 연삭 작업 불량
– 숫돌면과 가공물이 평행하도록 하여 연삭할 것.
– 숫돌압력을 감소시킬 것.
– 센터레스트를 추가 설치할 것.
– 가공물 1회전에 대한 숫돌 이송을 작게 할 것.
– 이송속도를 조금씩 변경할 것.
(라) 길이나 폭이 불규칙한 홈 발생
① 불결한 연삭액 사용
– 연삭액 탱크를 깨끗하게 할 것.
– 안전 커버를 깨끗하게 할 것.
(마) 이송 마크 발생
① 중심맞춤 불량
– 가공물 센터의 중심맞춤을 확인할 것.
– 숫돌축과 가공물의 중심맞춤을 확인할 것.
② 트루잉 불량
– 다이아몬드를 수평보다 5˚ 하향으로 장착할 것.
– 숫돌의 양끝 가장자리를 둥글게 할 것.
3) 가공물의 정밀도 불량
(가) 가공물의 진원도, 테이퍼, 평행도 불량
① 센터 또는 센터레스트의 중심맞춤 불량
– 센터 또는 센터레스트의 장착 상태를 확인할 것.
– 급유를 충분하게 할 것.
– 적당한 방진구를 사용할 것.
② 드레싱 불량
– 숫돌을 연삭 시와 같은 상태에서 드레싱할 것.
③ 연삭 작업 불량
– 이송 양끝에서 숫돌이 가공물을 벗어나지 않도록 할 것.
– 숫돌압력을 감소시킬 것.
– 결합도가 굳은 숫돌을 사용할 것.
④ 가공물의 팽창
– 연삭액을 다량 사용할 것.
– 연삭깊이를 얕게 하여 연삭저항을 줄일 것.
– 결합도가 약한 숫돌을 사용하고 약하게 작용시킬 것.
이상으로 연삭의 특성에 대한 연재를 마치고 다음에는 래핑에 대한 연재를 시작할 예정입니다.
2020년 10월 16일
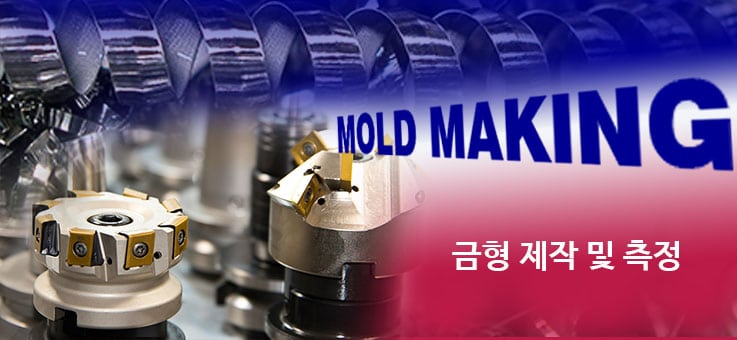
금형 제작 8
제8장 연삭의 특성
연삭의 특징 연삭작용, 자생작용, 숫돌면의 변화가 발생하는데 재생작용은 마멸된 숫돌입자가 탈락하여 새 날이 생기는 현상으로 숫돌입자의 마멸→파괴→탈락→생성이 주기적으로 반복되며 눈탈락→ 눈무딤→ 눈메움과 같은 숫돌면의 변화가 일어나게 됩니다.
1. 연삭 시 발생하는 작용
(1) 연삭작용
WS는 절입 또는 연삭깊이를 의미함.
숫돌바퀴의 절입이 증가하면 연삭저항이 증가하게 됨.
연삭 시 배분력이 주분력의 2배로 작용함.
(2) 자생작용
자생작용이란 마멸된 숫돌입자가 탈락하여 새 날이 생기는 현상으로 숫돌입자의 마멸 → 파괴 → 탈락 → 생성이 주기적으로 반복됨.
장시간 좋은 가공면을 유지할 수 있고 공구 교환이나 재연삭 공정을 생략할 수 있으며 숫돌바퀴의 선택과 적절한 연삭 조건이 필요함.
(3) 숫돌면의 변화
1) 눈탈락
눈탈락은 과도한 자생작용이 발생 시에 숫돌입자의 끝이 충분히 파쇄되지 않고 마모하였을 때 결합제가 파쇄되어 숫돌입자가 입자 그대로 빠져나가는 현상이 일어나는데 숫돌바퀴의 결합도가 작업에 대해 지나치게 낮을 경우 발생되며 숫돌의 손모가 심하고 가공면도 나빠짐.
2) 눈무딤
눈무딤은 자생작용의 부족으로 입자의 표면이 평탄해지는 상태.
(가) 원인
연삭 숫돌의 결합도가 높을 때.
연삭 숫돌의 원주속도가 너무 클 때.
숫돌의 재료가 가공물의 재료에 부적합할 때.
(나) 현상
연삭성이 불량하고 가공물에 열이 발생함.
연삭 손실이 발생함.
3) 눈메움
눈메움은 결합도가 높은 숫돌로 연성 재료를 연삭 시 숫돌 표면의 기공에 칩이 메워지는 현상.
(가) 원인
숫돌입자가 너무 작을 때.
조직이 너무 치밀할 때.
연삭깊이가 깊을 때.
숫돌바퀴의 원주속도가 느릴 때.
(나) 현상
연삭성이 불량하고 다듬질면이 거칠어짐.
다듬질면에 떨림 자리와 같은 상처가 생김.
숫돌입자가 마모되기 쉬움.
2. 특수 연삭 가공 기술
(1) 고속 연삭
1) 정의
연삭 능률 향상을 위해 숫돌 원주속도를 보통의 연삭에서보다 2~3배 크게 한 것으로 가공물 속도나 연삭깊이를 깊게할 수 있어 가공능률이 향상됨.
2) 특징
스파크 아웃 시간을 단축할 수 있음.
연삭저항이 감소하고 가공 정밀도가 향상됨.
숫돌의 손모가 적어 숫돌의 수명이 향상됨.
(2) 크림피드 연삭
1) 정의
종래의 평면 연삭법에 비하여 연삭깊이를 깊게 하고 테이블 이송속도를 매우 느리게 하여 1회 또는 수 회의 이송으로 가공하는 방법으로 숫돌의 원주면을 사용하는 성형 연삭을 고능률화 시킨 것.
2) 특징
숫돌의 마모가 비교적 균일하고 숫돌 윤곽 형상의 변화가 적음.
연삭저항의 변동이 심하고 가공 상태가 불안정할 수 있음.
숫돌 접촉면적이 크고 연삭열의 발생, 연삭균열의 우려가 있음.
(3) 중 연삭
1) 정의
연삭깊이나 가공물의 속도를 크게 하고 단위 시간당 연삭량을 증가시켜 가공능률을 향상시키는 연삭 방법.
2) 종류 및 특징
(가) 슬랩 연삭(SLAB GRINDING)
버 제거, 슬랩의 표피 연삭 등 가공 정도에 비교적 문제가 안 되는 경우 사용됨.
(나) 연마 가공(ABRASIVE MACHING)
높은 연삭능률과 가공 정도를 동시에 얻기 위한 방법으로서 평면 연삭 가공에는 세그먼트형 숫돌을 사용한 고마력의 연삭기가 사용됨.
3. 연삭면의 형성과 스파크 아웃
(1) 개요
연삭 다듬질면은 연삭입자의 절삭날에 의해 절삭된 가공면으로서 연삭 조건에 큰 영향을 받으며 특히 절삭날의 밀도가 중요함.
다듬질면의 거칠기 형상을 위해서는 적절한 날 교정에 의해서 숫돌 표면의 절삭날 높이를 균일하게 하고 밀도를 높이는 것이 무엇보다 중요시됨.
연삭 시에는 설정 절삭깊이만큼 실제로 절삭되지 않으며 여러 요인에 의해 연삭 잔량이 생기게 됨.
(2) 다듬질면에 영향을 주는 요인
1) 입도
입도가 고울수록 다듬질면의 거칠기는 향상되는데 그 감소의 정도는 입도가 거친 영역에서 크고 연삭입자는 연삭저항에 의해 마멸되며 그 마멸 정도가 균일한 것이 다듬질면에 큰 영향을 미침.
2) 결합도
같은 입도의 숫돌로 적당한 연삭 조건하에서 연삭 시 결합도가 굳은 숫돌의 다듬질면이 일반적으로 좋아지는 경향이 있음.
3) 절삭깊이
절삭깊이의 증가에 따라 다듬질면의 거칠기도 증가하며 각각의 절삭날에 작용하는 힘이 증가하여 연삭입자의 마멸이 심해지기 때문이고 동시에 연삭기에 걸리는 부하의 증가로 인한 진동의 요인도 수반함.
4) 이송
이송속도의 증가에 따라 다듬질면의 거칠기도 거의 비례적으로 증가함.
5) 진동
연삭숫돌과 가공물 사이에 상대 진동이 있으면 절삭날의 밀도가 거칠어지므로 조도가 커짐.
6) 절삭잔량
절삭잔량이 있으면 거칠어지며 반복 연삭을 통해 절삭잔량이 적어질 때 다듬질면의 거칠기도 향상되고 절삭깊이가 깊거나 이송속도가 빨라지면 절삭잔량도 많아짐.
(3) 스파크 아웃
1) 정의
연삭 시 숫돌의 마모가 거의 없고 가공물과 숫돌축이 강체라면 설정된 절삭깊이만큼 연삭이 되겠지만 실제로는 여러 요인에 의해 연삭 잔량이 남게 되는데 이때 더 이상의 절삭깊이 이송을 중지하고 연삭을 계속하면 탄성변형이 회복되면서 실 연삭량이 증가되는 상태를 말함.
2) 절삭 잔량 요인
숫돌바퀴의 마모(d0).
숫돌축 및 가공물의 휨(d1).
가공물과 숫돌 접촉 부의 탄성변형(d2).
연삭 입자가 절삭하지 않고 가공물을 밀어젖히는 현상(d3).
3) 연삭면의 형성
설정 절삭깊이가 OG와 같이 경과해도 OP는 탄성변형에 의해 PC는 가공물을 밀어젖힐 때 절삭깊이의 양이 소비되어 실제 가공 치수는 OPCB와 같이 경과함.
결국 d0+d1+d2+d3의 치수가 설정 연삭깊이보다 연삭이 되지 않아 연삭 잔량이 남게 됨.
이때 G 점에서 연삭깊이의 이송을 중지하고 연삭을 계속하면 탄성변형이 회복되면서 스파크 아웃 상태에 도달하게 되어 실제 절삭량은 BB´ 만큼 증가하게 됨.
4. 연삭열과 연삭온도 측정법
(1) 개요
연삭 시에는 부(-)의 경사각을 가진 연삭입자의 절삭날이 고속으로 가공물을 절삭하게 되어 거의 가공물에 용융점에 가까운 연삭열이 발생하게 됨.
이러한 열은 절삭유와 칩에 의해 제거되고 가공물 및 숫돌바퀴에 전도되는데 연삭열에 의해 가공물이 가열되면 열팽창에의해 가공 정밀도가 저하되며 다듬질면이 산회되어 내마모성이 떨어지거나 경화강 등은 뜨임이 되어 경도가 약해짐.
열 발생이 심할 경우 가공 중 또는 가공 후에 미세한 연삭균열이 발생하므로 연삭 시에는 연삭열의 발생을 최소화해야 하고 연삭액도 냉각 성능이 뛰어난 것을 사용해야 함.
(2) 연삭온도
1) 연삭입자의 연삭점 온도
입자의 연삭점 온도는 연삭입자가 연삭 시 절삭날 끝의 온도로서 일반적으로 수백 도 이상이며 연삭입자의 손모와 관계가 깊고 개개의 연삭입자의 절삭날을 수십 ~수백 μm에 걸친 면에서 가공물과 접촉하여 절삭작용을 수행하게 됨.
2) 숫돌 연삭점 온도
숫돌과 가공물의 겉보기 접촉면에서의 평균적인 온도이며 가공물의 열 손상과 관계가 있음.
3) 가공물의 평균 상승 온도
연삭열이 유입되어 연삭액이나 공기의 접촉에 의해 제거되고 남은 열로서 연삭시간과 더불어 상승하여 유입 열과 방열이 같아지면 일정한 평균 온도를 나타내고 열팽창에 의한 치수 정밀도의 저하와 관계가 있으며 다량의 연삭액 사용을 통해 10℃ 이내로 억제할 수 있음.
(3) 연삭온도 측정법
1) 연삭입자의 연삭점 온도 측정
(가) 가공물과 숫돌을 열전쌍으로 하는 방법
SiC 연삭 입자는 반도체이므로 이 숫돌과 가공물을 열전쌍으로 하여 열기전력을 측정하는 방법.
(나) 가공물과 미세 도선을 이용한 방법
도체인 가공물을 2개로 분할하여 운모와 같은 절연막을 사이에 두고 백금 선 등의 미세도선을 끼워넣고 결합하여 연삭 시 미세도선과 가공물과의 열 접점을 이용하여 오실로스코프 등으로 절삭날 끝 온도를 검출함.
2) 숫돌 연삭점 온도
(가) 열전쌍을 이용하는 방법
수평형 평면 연삭기 등에서 이용되는 방법으로 가공물의 뒷면에 가는 구멍을 뚫고 콘스탄탄선 등을 구멍 끝에 접촉시켜 오실로스코프로 열기전력을 측정하는 방법.
열 접점이 숫돌 외주에서 막 절단될 때의 검출온도가 숫돌 연삭점 온도이며 연삭깊이에 따른 온도 분포를 알 수 있음.
(나) 방사 온도계에 의한 방법
숫돌을 관통하는 작은 구멍을 뚫고 방사 온도계를 고정하여 가공면에서부터의 적외선 방사 온도를 측정하는 방법.
(다) 연삭에 의한 변색이나 시온도료의 변색에 의한 방법.
3) 가공물의 평균 온도
칼로 미터에 의한 방법.
시오 도료의 변색에 의한 방법.
(4) 연삭 시의 온도 상승을 억제하는 방법
냉각 능력이 우수한 연삭액을 다량 사용할 것.
입도가 크고 결합도가 작으며 조직이 거친 숫돌을 사용할 것.
숫돌바퀴의 속도 및 절입깊이, 접촉면적을 작게 할 것.
이송을 크게 할 것.
눈무딤, 눈메움이 된 숫돌은 바로 수정할 것.
5. 연삭 가공면의 손상 형태
(1) 개요
연삭 가공면은 고온•고속의 절삭 및 마찰 현상에 의해 가공면이 심한 변질을 받으며 연삭열에 의해 열팽창이 발생되고 가공물의 내부에는 잔류응력이 발생함.
연삭 가공면의 손상 형태는 가공 변질층, 잔류응력, 연삭버닝과 연삭균열로 구분할 수 있음.
(2) 가공 변질층
1) 가공 변질층의 생성 원인
절삭성이 나쁜 숫돌로 다듬질 연삭하는 경우 마찰에 의한 역학적 작용.
절삭깊이가 과도하게 큰 경우 절삭저항에 의한 응력.
과대한 연삭열로 인한 조직의 변화.
2) 변질 현상
(가) 표면 경도 변화
기계적 응력에 의한 가공경화.
연삭열에 의한 담금질 경화 및 뜨임으로 인한 연화.
(나) 열응력, 변태응력에 의한 잔류응력층의 형성
(다) 연삭균열
(3) 잔류응력
1) 발생 원인과 영향
연삭 가공 시에는 연삭열과 마찰 및 절삭에 따른 소성변형이 가공물의 표면층에 가해지며 이로 인해 잔류응력이 발생됨.
잔류응력은 가공 후에 서서히 소멸하여 제품의 치수적인 경년 변화를 초래하는데 잔류응력이 매우 큰 경우에는 시효균열이 발생함.
2) 대책
잔류응력이 작은 연삭 조건 선택.
연삭 후 처리.(서브제로, 풀림, 인공시효)
(4) 연삭버닝과 연삭균열
1) 정의
(가) 연삭버닝
연삭 시 가공면에 연삭열로 인해 다듬질면이 산화되어 그 산화막이 빛의 간섭에 의해 막 두께에 따른 착색이 발생되는 것.
(나) 연삭균열
연삭열에 의한 열팽창 또는 재질의 변화 등이 원인으로서 공석강에 가까운 탄소강이나 담금질한 재료의 연삭면에 발생하는 미세균열.
2) 발생 원인
숫돌바퀴의 원주속도가 크고 절삭깊이가 깊음.
숫돌의 입도가 작고 결합도가 높음.
피삭재의 발열성이 큼.
건식 연삭인 경우 발생.
3) 방지 대책
(가) 연삭온도가 낮은 연삭 조건 선택
연삭액을 충분히 사용하여 발열을 억제할 것.
연한 숫돌을 사용하고 이송을 크게 할 것.
절삭깊이를 작게 하여 절삭압력을 감소시킬 것.
(나) 가공물 열처리 시 최적의 조건 선택
6. 연삭 조건의 선정 방법
(1) 개요
가공물과 숫돌의 크기, 모양, 재질이나 연삭 방법에 따라 숫돌바퀴의 원주속도, 이송속도, 절삭깊이 등이 다르며 이와 같은 조건은 서로 관계를 가지고 연삭작용에 영향을 미침.
(2) 숫돌의 원주속도
숫돌이 원주속도는 연삭능률과 관계가 깊고 원주속도가 너무 느리면 숫돌의 손모가 심하고 원주속도가 지나치게 빠르면 숫돌의 절삭성이 저하하며 원심력에 의해 파괴될 위험이 있음.
일반적인 비트리파이드 숫돌인 경우 원통 외면 연삭은 1700 ~ 2000m/min, 내면 연삭은 600 ~ 1800m/min, 평면 연삭은 1200 ~ 1800m/min, 공구 연삭은 1400 ~ 1800m/min의 원주속도를 가짐.
단, 원통 연삭기의 경우 숫돌과 가공물의 회전 방향이 다를 경우에는
V = V₁+ V₂(m/min)
여기서 V₁ = 연삭숫돌의 원주 속도, V₂ = 가공물의 원주 속도
(3) 가공물의 원주속도
가공물의 원주속도는 숫돌의 원주속도와 깊은 관계를 갖고 있으며 이 속도비(숫돌바퀴의 속도/가공물 속도)는 다듬질면의 표면 거칠기, 연삭능률에 큰 영향을 미침.
속도비는 보통 1/100 정도로 하며 가공물의 재질, 숫돌의 성질, 숫돌의 폭, 다듬질면의 표면 거칠기 등을 함께 고려하여 결정해야 함.
고속 연삭에서는 속도비를 크게 하여 가공능률과 가공 변질층 면에서 유리한 결과를 얻기도 하며 가공물의 원주속도가 빠르면 숫돌 절삭저항이 커짐.
(4) 이송속도
원통 트래버스 연삭에서의 이송속도는 가공물의 원주속도와 서로 관계하며 일반적으로 가공물의 이송이 작으면 다듬질면이 양호해짐.
가공물의 축 방향 이송은 가공물 1회전에 대하여 숫돌폭(B) 이하로 선정해야 하며 다음의 표준값을 선택해야 함.
(5) 연삭깊이
연삭깊이는 연삭능률에 영향을 미치며 가공물의 재질, 연삭 방법, 연삭 정밀도 등에 따라서 연삭깊이를 결정함.
가공물의 원주속도가 빠르거나 숫돌바퀴의 원주속도가 느릴수록 연삭깊이를 깊게 줄 수 있으며 거친 연삭에서는 가능한 한 연삭깊이를 깊게 주고 다듬질 연삭 시에는 얕게 주어야 함.
연삭깊이는 다음과 같이 선정함.
(6) 연삭여유
연삭여유는 가공물의 재질, 모양, 치수, 전 가공의 다듬질면의 표면 거칠기 등에 따라 다르나 되도록이면 작을수록 좋으며 선반 가공 시에는 0.3 ~ 0.8mm의 여유를 두고 가공하면 됨.
연삭여유가 너무 적으면 전 가공 시 시간이 많이 걸리므로 가공물의 지름, 길이, 연삭 방법에 따라 적절한 연삭여유를 선정해야 함.
(7) 연삭비
연삭비 = 가공물의 연삭된 부피/ 숫돌바퀴의 소모된 부피
7. 연삭 숫돌의 드레싱 및 트루잉
(1) 개요
연삭 숫돌이 눈탈락, 눈무딤, 눈메움을 일으키게 되면 연삭성이 떨어지고 떨림, 발열 등이 발생하므로 연삭성을 회복시키기 위해 새로운 예리한 연삭입자를 표면에 나타나도록 하는 것을 드레싱이라 함.
숫돌바퀴의 질이 균일하지 못하거나 가공물의 영향을 받아 숫돌바퀴의 모양이 점차 변하게 되며 특히 나사나 기어의 연삭, 윤곽 연삭 등에 있어서는 정확한 숫돌 형상이 필요하므로 숫돌의 형상을 정확하게 깎아내는 작업을 트루잉이라 하고 트루잉을 하면 동시에 드레싱도 됨.
(2) 드레싱의 필요성
눈탈락, 눈무딤, 눈메움 등이 발생하면 연삭성이 떨어지기 때문에 드레싱이 통해 연삭성을 회복시켜야 함.
(3) 숫돌바퀴의 수정 공구
1) 핸팅톤 드레서
(가) 형상 및 작업 방법
담금질된 강판재의 파형 원판을 다수 겹쳐서 홀더축에 끼운 것으로서 가장 간단한 공구로서 회전하는 숫돌 표면에 드레서를 접촉시키면 회전하여 파형 모서리에 충격에 의해 숫돌 표면이 드레싱됨.
(나) 용도
정밀도를 그리 필요로 하지 않는 연삭숫돌의 드레싱에 사용하며 성형 연삭 숫돌, 정밀 연삭 숫돌에는 사용하지 않음.
2) 연삭숫돌을 사용한 드레싱
탄화규소제 비트리파이드 숫돌에서 결합도가 굳은 드레싱용 숫돌을 이용하여 수정하고자 하는 숫돌과 접촉 회전시킨 후 브레이크를 걸어 상대 미끄럼을 통해 드레싱하는 것으로 비교적 매끈하고 정밀도가 높은 숫돌면을 얻을 수 있음.
3) 다이아몬드 드레서
가장 널리 사용하는 것을 모든 숫돌의 드레싱 및 트루잉에 사용할 수 있음.
형상이나 다이아몬드 개수에 따라 여러 종류가 있으며3 드레싱할 때는 숫돌의 수평 중심방향에서 3˚ ~ 15˚ 위로 기울여 드레서를 접촉시키고 절삭깊이가 너무 깊으면 다이아몬드의 마모가 커지므로 0.02mm 이하로 절삭깊이를 주고 시행해야 함.
4) 크러시 롤러
총형 연삭을 할 때 숫돌을 가공물의 반대 모양으로 성형하여 드레싱하기 위해 롤러로서 숫돌을 저속 회전시켜서 이것에 담금질된 크러시 롤러를 접촉시키면 숫돌면이 부서지면서 총형으로 드레싱과 트루잉이 됨.
크러시 롤러는 나사 연삭, 윤곽 연삭 숫돌과 같은 숫돌바퀴를 복잡한 형상으로 수정하는데 효과적임.
5) 로터리 드레서
큰 입자의 다이아몬드 연삭입자를 숫돌 외주면에 배열하여 소결 시킨 것으로 드레서를 회전시켜 숫돌과 접촉하면 절삭작용에 의해 드레싱과 트루잉을 동시에 할 수 있음.
6) 전해 드레싱
최근 정보통신기기 및 O/A에 사용되는 부품은 높은 정밀도와 고품질의 저렴한 가격을 요구하고 있는데 이러한 요구를 만족하기 위한 연삭법으로 전해 드레싱이 개발되어 생산 현장에서 이용되고 있음.
전해 드레싱은 미세립의 지석을 사용하여 드레싱을 하면서 연삭하는 방법으로 지석의 로딩을 방지하고 고능률로 가공할 수 있는 센터리스 연삭기에 채용하여 좋은 결과를 얻고 있음.
전해 드레싱의 원리는 전기분해로 메탈 본드를 녹여서 제거하면 지립이 돌출되는 동시에 산화 피막이 만들어지고 산화 피막이 지립을 탄력적으로 유지하기 때문에 고품질의 연삭이 가능하게끔 함.
전해 드레싱은 다음과 같은 특징을 가지고 있음.
– 지석의 절삭성이 양호하여 1공정으로 가공이 가능.
– 트루잉과 드레싱을 자동화할 수 있음.
– 경면 가공이 가능.
– 연속적인 라인 생산을 통하여 생산능률을 높일 수 있음.
8. 연삭액의 사용 목적과 주가법
(1) 개요
연삭에서는 절삭과 달리 연삭열에 의해 가공물이 가열되어 가공 정밀도의 저하, 내마모성의 저하, 조직의 변화, 연삭균열 등의 문제점이 나타나므로 일반적으로 연삭액을 사용하며 연삭액은 가공물의 면 상태나 숫돌의 마멸에 직접 영향을 미치게 됨.
(2) 연삭액의 기능과 구비 조건
1) 기능
가공물 및 연삭 숫돌을 냉각함.
연삭입자 절삭날과 칩과의 윤활작용을 좋게 하여 연삭입자의 마모 및 용착을 억제함.
칩이나 탈락된 연삭입자를 씻어내어 숫돌의 눈메움을 억제함.
2) 구비 조건
냉각성, 윤활성, 유동성이 좋아야 함.
부식과 변질이 되지 말아야 하고 화학 반응이 없어야 함.
연삭열에 의해 증발되지 않아야 함.
(3) 연삭액의 종류
1) 불수용성 연삭액
광유, 지방유 등에 각종 첨가제를 가하여 냉각 성능보다는 윤활 성능을 중시한 것으로서 숫돌의 마찰을 작게 해주고 눈메움 현상억제에 효과가 있으며 나사 연삭, 총형 연삭 등에 쓰임.
2) 수용성 연삭액
일반적으로 많이 사용되는 것으로서 방청제, 계면활성제를 다량의 물에 첨가하여 냉각 등을 중시한 것이며 보통 원통 연삭, 평면 연삭 등에 쓰임.
(4) 연삭액 주가법
1) 노즐 주가
일반적인 방법으로 연삭액 받이, 펌프, 회수 장치가 있어 노즐을 사용하여 가공물과 연삭숫돌 사이에 연삭 전에 연삭액을 주가함.
2) 통액 주가
숫돌바퀴의 다공성을 이용한 것으로 숫돌 내부에서 연삭입자의 날끝으로 원심력에 의해 분무되어 주가하는 방법이며 경합금 연삭 시와 같이 눈메움이 있는 경우에 효과적임.
연삭액의 주가량이 적으므로 노즐 주가와 병행함.
3) 제트 주가
숫돌바퀴 작업면에 직각으로 제트 분사하여 칩을 불어 날려서 눈메움을 방지하며 연삭액에 초음파를 걸어서 억제하는 방법도 있음.
9. 연삭 시의 결함 및 대책
(1) 개요
연삭 시에 가공물에 나타나는 가공 결함으로서 떨림, 다듬질면 불량, 정밀도 불량 등이 있음.
(2) 연삭 시의 결함 및 대책
1) 떨림
(가) 다듬질면에 떨림 자국이 발생
① 연삭숫돌 자체의 불균형
– 숫돌의 균형을 다시 잡을 것.
– 트루잉 후 균형을 다시 교정할 것.
– 연삭액을 가하지 않고 숫돌을 운전하여 함유된 연삭액을 제거할 것.
② 숫돌의 진원 불량
– 균형을 잡기 전후에 트루잉을 할 것.
– 숫돌의 양측면의 형상을 교정할 것.
③ 숫돌의 결합도 과대
– 결합도가 약한 숫돌 선택할 것.
– 입도와 조직이 거친 것을 선택할 것.
④ 센터 및 센터레스트의 사용법 불량
– 센터와 센터레스트의 맞춤을 확인할 것.
– 윤활을 충분히 할 것.
⑤ 연삭기 자체의 진동
– 설치 시의 문제 요인을 검사할 것.
2) 다듬질면의 불량
(가) 폭이 좁고 깊은 규칙적인 줄 자국 발생
① 숫돌입자가 큼
– 입도가 미세한 숫돌을 사용할 것.
(나) 폭이 좁고 깊은 불규칙한 줄 자국 발생
① 숫돌 결합도가 작음
– 결합도가 큰 숫돌을 사용할 것.
(다) 가는 나사 모양 흠집 발생
① 드레싱 불량
– 드레서의 이송을 작고 균일하게 할 것.
– 다이아몬드 또는 홀더의 장착을 확실하게 할 것.
– 다이아몬드의 절삭깊이를 얕게 할 것.
– 드레싱은 숫돌의 끝에서부터 시작할 것.
– 숫돌의 양끝 가장자리는 둥글게 할 것.
② 연삭 작업 불량
– 숫돌면과 가공물이 평행하도록 하여 연삭할 것.
– 숫돌압력을 감소시킬 것.
– 센터레스트를 추가 설치할 것.
– 가공물 1회전에 대한 숫돌 이송을 작게 할 것.
– 이송속도를 조금씩 변경할 것.
(라) 길이나 폭이 불규칙한 홈 발생
① 불결한 연삭액 사용
– 연삭액 탱크를 깨끗하게 할 것.
– 안전 커버를 깨끗하게 할 것.
(마) 이송 마크 발생
① 중심맞춤 불량
– 가공물 센터의 중심맞춤을 확인할 것.
– 숫돌축과 가공물의 중심맞춤을 확인할 것.
② 트루잉 불량
– 다이아몬드를 수평보다 5˚ 하향으로 장착할 것.
– 숫돌의 양끝 가장자리를 둥글게 할 것.
3) 가공물의 정밀도 불량
(가) 가공물의 진원도, 테이퍼, 평행도 불량
① 센터 또는 센터레스트의 중심맞춤 불량
– 센터 또는 센터레스트의 장착 상태를 확인할 것.
– 급유를 충분하게 할 것.
– 적당한 방진구를 사용할 것.
② 드레싱 불량
– 숫돌을 연삭 시와 같은 상태에서 드레싱할 것.
③ 연삭 작업 불량
– 이송 양끝에서 숫돌이 가공물을 벗어나지 않도록 할 것.
– 숫돌압력을 감소시킬 것.
– 결합도가 굳은 숫돌을 사용할 것.
④ 가공물의 팽창
– 연삭액을 다량 사용할 것.
– 연삭깊이를 얕게 하여 연삭저항을 줄일 것.
– 결합도가 약한 숫돌을 사용하고 약하게 작용시킬 것.
이상으로 연삭의 특성에 대한 연재를 마치고 다음에는 래핑에 대한 연재를 시작할 예정입니다.
2020년 10월 16일