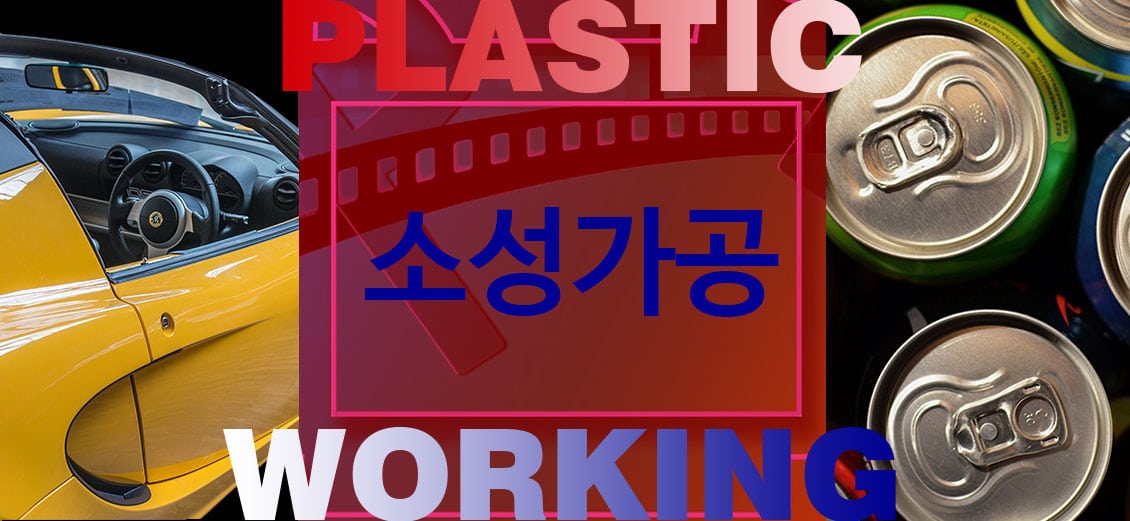
소성가공 4
제4장 특수 가공 및 금형
소성 가공 중에서 특수 가공 및 금형(PLASTIC WORKING)에 대표적인 것으로는 다이나 롤러를 이용하여 소재를 공구의 표면 형상으로 각인하는 전조와 금속 분말을 금형에서 압축한 후 가열•소결 하여 제품을 가공하는 분말야금이 있습니다.
1. 전조
(1) 개요
특수 가공 및 금형 중 전조는 다이나 롤러와 같은 성형 공구를 회전 또는 직선운동시키면서 그 사이에 소재를 넣어 공구의 표면 형상으로 각인하는 일종의 특수 압연을 말함.
전조로 가공되는 제품으로는 기어, 나사, 볼, 링, 스플라인 축 등이며 전조기에는 제품에 따라 특수한 장치를 갖춘 전용기가 있음.
(2) 특징
소재의 섬유조직이 전단되지 않으므로 제품의 강도가 큼.
소재와 공구의 국부적인 접촉으로 인한 작은 가공력만 가지고도 가공이 가능함.
칩이 생성되지 않으므로 소재의 이용률이 높음.
소성변형으로 인한 가공경화 및 치밀한 조직이 형성됨.
가공속도가 빠르고 자동화가 쉬움.
(3) 전조 가공의 종류
1) 나사 전조
(가) 평 다이 전조
평 다이 전조는 한 쌍의 평 다이 중 하나는 고정, 다른 하나는 직선운동을 시켜 1회의 행정으로 나사를 성형하는 방법.
평 다이 전조의 소재는 대부분 연성재료가 사용되며 다이에는 성형부와 다듬질부가 있음.
둥근형 다이 전조에 비해 제품의 정밀도가 떨어짐.
(나) 둥근형 다이 전조
둥근형 다이 전조는 고정축 다이와 가동축 다이로 되어 있으며 두 축은 평행하고 재료는 지지대에 의해 지지됨.
둥근형 다이 전조는 가동축은 축이 이동되며 롤러 다이를 3개 사용하는 경우가 있음.
평 다이 전조에 비해 생산속도가 매우 빠르고 정밀한 나사를 제작할 수 있음.
(다) 프래너터리 전조(PLANETARY 전조)
프래너터리 전조는 고정 원호 다이를 고정시키고 원형 다이를 회전시켜 자동으로 장입 소재가 타단에서 완성된 나사로 나오며 물림률이 크고 대량생산에 적합함.
프래너터리 전조는 크랭크 운동에 의한 평 다이 전조에서는 가공을 하지 않는 귀환행정이 있으나 플래너터리 전조에서는 공전이 없으므로 가공 능률이 높음.
2) 기어 전조
(가) 래크 다이 전조
래크 다이 전조는 한 쌍의 래크 다이 사이에 소재를 넣고 압력을 가하면서 래크를 이동시켜 소재의 치형을 성형함.
이 방법은 지름이 큰 기어에 대해서는 래크가 커야 하고 설치 공간도 넓어야 되기 때문에 지름이 작은 기어 제작에 적합함.
기어 전조법은 보통 냉간가공을 하고 있으나 모듈이 약 3 이상인 경우나 굵은 재료의 경우에는 열간가공으로 함.
(나) 피니언 다이 전조
피니언 다이 전조는 피니언 다이와 소재의 맞물림을 동일하게 하여 압력을 가하면서 회전시켜 치형을 성형하며 공구의 작동이 용이함.
피니언 다이 전조는 지름이 큰 기어, 웜, 스플라인 성형가공에 많이 적용됨.
(다) 호브 다이 전조
호브 다이 전조는 전조 공구를 상하에 두고 소재를 회전시키면서 축 방향으로 보내어 성형함.
소재는 인덱스 헤드에 의하여 소정의 각도만큼 회전시켜 다이 사이에 삽입됨.
소재의 유동이 좋고 롤러에 무리한 힘이 작용되지 않음.
3) 볼 전조
볼 전조는 2개의 다이가 롤러 축과 교차되어 있어 소재의 성형과 이송을 동시에 행함.
다이의 홈은 볼을 성형하는 가공면이고 산은 소재를 오목 패이게 가공하면서 최후에는 절단하는 역할을 함.
볼 전조는 500 ~ 1,000℃의 열간가공에서 행해짐.
4) 드릴 전조
드릴 전조는 소재가 길이 방향으로 연신 되면서 홈이 성형됨.
공구는 홈 가공용과 릴리프면 가공용이 따로 있음.
2. 반용융 금속을 이용한 성형법(SEMI-SOLIDE FORMING PROCESS)
(1) 반용융 압연
1) 성형 방법 및 특징
특수 가공 및 금형 중 반용융 압연이란 반용융 금속으로부터 열연강판 및 냉연강판을 제조하는 것으로 롤러 사이에 주입하는 금속의 주입온도를 낮춤으로써 롤러에 발생하는 열응력과 열피로 현상을 감소시켜 롤러의 수명을 연장시킬 수 있음.
롤러 내에서 응고하기 시작한 재료의 응고 완료점의 위치에 따라 판재 성형성이 결정되기 때문에 롤러의 온도 및 속도 변화에 따른 응고 제어가 매우 중요함.
2) 기술적인 요점
(가) 공정변수의 확립을 통한 자동화
고상률, 롤러 회전수, 롤러 간격, 탕면 높이, 재료의 주입방법, 롤러 냉각방법 등과 같은 공정변수들 사이의 관계가 정량적으로 규명되어야 하며 공정변수를 변화시켜 응고속도를 일정하게 유지되도록 제어해야 함.
(나) 롤러 냉각 방식에 따른 냉각 특성 파악
냉각 특성에 따른 롤러 재질 선정, 롤러 형상 설계, 냉각수 주입량을 결정하여 롤러에 작용하는 열응력 및 열피로를 줄임.
(다) 분산장치 및 노즐 형상의 결정
반용융 금속을 롤러 폭 방향으로 균일하게 분산시키기 위한 분산장치 및 노즐의 형상이 결정되어야 함.
(2) 반용융 단조
1) 성형 방법 및 특징
반용융 단조는 금속의 온도를 제어하면서 교반을 행하는 교반부, 밀폐형 다이 내로 주입하기 위한 주입부, 그리고 밀폐형 다이와 다이 내에 충전된 반용융 금속을 가압하는 가압부로 구성됨.
반용융 단조는 단조 하중이 작고 가공속도가 빠르며 편석, 기공 등과 같은 결함이 없는 주조와 단조 공정이 결합된 복합 공정임.
2) 기술적인 요점
(가) 성형 가능한 고상률 범위와 금형온도
반용융상과 고상의 경계를 시간에 따라 추정하여 완전히 응고가 되는 시간을 예측하고 시간의 변화에 따라 응고 측정과 다이의 온도 분포를 파악하여 금형의 예열온도를 예측해야 함.
(나) 최적 단조 조건 확인
단조압력, 단조속도, 단조시간 등이 정량적으로 확립되어야 하며 이들 인자의 변화에 따른 재료의 흐름 특성과 재료의 이방성이 파악되어야 함.
또한 공구의 최적 윤활제 선정, 금형온도가 품질에 미치는 영향 등이 검토되어야 함.
(3) 반용융 압출
1) 성형 방법 및 특징
반용융 압출은 기존의 빌렛 대신 반용융 금속을 호퍼를 통해 컨테이너 내에 공급하고 스템의 가압과 동시에 다이를 통하여 원하는 부품을 성형함.
2) 기술적인 요점
(가) 컨테이너 및 금형의 온도 제어
반용융 금속의 고상률의 제어 때문에 컨테이너에서의 온도 제어가 중요하며 결정립의 균일한 분포를 위해 다이의 온도 제어가 특히 중요함.
(나) 금속 복합재료의 압축 기술
강화제의 파단을 방지하기 위한 다이의 설계, 기지 내의 소성유동과 강화제의 배향 사이의 관계가 정립되어야 함.
(4) 반용융 다이캐스팅
1) 성형 방법 및 특징
(가) 성형 방법
용융 금속을 전자 교반하면서 연속 주조를 통해 수지상 결정을 분단하여 균일한 조직의 빌렛을 만든 후 다이캐스팅 1 SHOT에 해당하는 양만큼 자름.
로터리식 유도가열 장치에 의해 약 590℃까지 가열하여 고상률 50 ~ 60%의 반용융 상태로 만들고 반용융 빌렛을 로봇을 이용하여 사출 슬리브에 삽입한 후 플런저로 금형의 캐비티 내로 사출 충전함.
반용융 다이캐스팅 제품은 수축이 적고 편석이 적어 기계적 강도가 안정되며 내기밀성이 우수함.
(나) 특징
① 제조상의 특징
– 점성 충전이므로 탕 끝에서 공기 권입이 없음.
– 이미 반은 응고된 상태이므로 수축 캐비티가 적음.
– 저온 주입으로 형 수명이 길고 에너지가 절감됨.
– 유지로가 필요 없음.
– 주조 핀이 거의 발생하지 않음.
– 응고 수축이 작으므로 이형하기도 쉽고 치수 정밀도가 좋아 정형가공이 용이함.
– 복합재료의 제조가 용이함.
– 작업환경이 양호함.
② 제품의 특징
– 블로 홀이 매우 적음.
– 편석이 적음.
– 파단질층이 적음.
– 표면에서 내부까지 균일한 입상조직을 취함.
– 기밀성이 양호함.
– 연성, 인성이 현저하게 큼.
2) 기술적인 요점
(가) 반용융 다이캐스팅 빌렛
수지상의 결정이 파괴•분단된 조직의 빌렛을 저렴하게 제조할 수 있어야 하는데 빌렛의 가격이 높아 반용융 다이캐스팅의 보급이 광범위하게 이루어지지 못하고 있음.
(나) 주조 조건
초기에 플런저의 전진속도는 고속이지만 금형의 캐비티에 용융 금속을 충전 할 경우에는 저속이므로 사출속도를 임의로 설정할 수 있는 고출력의 사출기구를 가진 다이캐스트 머신이 필요함.
(다) 금형 설계
반용융 금속은 고점성 충전이므로 유동저항의 경감 및 충류 충전을 위해 탕구를 두껍게 하고 인발 코어 등을 추가하며 가스 빼기를 충분하게 설치하고 가공여유를 많이 주는 것이 좋음.
금형은 예열 장치 및 온도조절 장치가 있어야 함.
3. 신기술 단조 방법
(1) 개요
단조의 가공속도 향상을 통해 생산성을 향상시키거나 작은 하중으로 고품질의 제품을 생산할 뿐만 아니라 다이의 수명을 연장시키기 위한 새로운 단조법이 연구 개발되고 있고 이를 신기술 단조법이라 함.
(2) 신기술 단조 방법의 종류
1) 고에너지 단조
고에너지 단조는 내연기관을 이용하여 수천 분의 일 초만에 순간적으로 단조 가공을 완료하는 기술임.
주로 판재 성형에 응용되며 얇은 단면을 가지는 복잡한 형상의 제품 생산에 적합함.
상용화된 고에너지 단조 기계로는 영국에서 개발한 PETRO FORGE, 미국에서 개발한 DYNAPAK 등이 있음.
2) 반용융 단조
3) 분말 단조
분말 단조는 분말 소재를 소력하여 만든 예비 성형체를 열간 단조하여 제품을 만드는 단조법.
분말 단조는 가공 단계가 단순하고 후처리가 필요 없어 복잡한 형상을 만들 수 있음.
주로 커넥팅 로드, 기어 등과 같이 높은 강도를 요하는 기계부품 생산에 적합함.
4) 등온 단조
등온 단조는 가열 금형 단조라고도 하며 가열된 소재의 온도와 동일하도록 다이를 가열하여 단조하는 방법.
등온 단조는 단조가 진행되는 동안 소재가 냉각되지 않으므로 소재의 유동이 원활하여 작은 힘으로도 제품을 성형할 수 있음.
등온 단조용 다이는 니켈이나 몰리브덴 합금으로 제작됨.
4. 반용융 가공의 특징과 문제점
(1) 개요
특수 가공 및 금형 중 반용융 가공은 용융 상태에서의 금속을 냉각 도중 기계적으로 교반하여 수지 상정을 파괴시킨 다음 압연, 압출, 단조, 용탕 단조 및 다이캐스팅에 의하여 제품을 제조하는 공정으로 주조와 단조 공정이 결합된 복합 공정을 말함.
반용융 가공은 에너지 절약, 응용범위 확대, 공정 단축 등의 측면에서 많은 연구와 관심을 불러일으키고 있음.
(2) 반용융 가공의 특징과 문제점
1) 특징
변형저항이 현저하게 적어 적은 하중으로도 가공률을 증대시킬 수 있고 가공 기계 설비의 소형화가 가능함.
유동성과 성형성이 양호하기 때문에 공정 단축이 가능하고 에너지 절약과 재료의 절감을 이룰 수 있음.
결정립이 미세한 주조 조직을 얻을 수 있고 기계적 성질이 우수한 제품을 만들 수 있음.
이종 재료와의 접합이 용이하여 분산 강화 및 적층 강화형 복합 재료의 제조가 가능하고 성형성이 우수함.
다이캐스팅 및 용탕 단조법에서의 용융 재료보다 온도가 훨씬 낮기 때문에 금형과 공구에 가해지는 열적 부하가 적어 수명을 연장시킬 수 있음.
단조 시 편석이 없는 균질한 제품의 제조, 압력 및 냉각속도의 제어에 의하여 결함과 기공이 없는 성형이 가능함.
2) 문제점
(가) 반용융 금속의 연속적인 제조 기술 개발
기계적 교반법, 전자기적 교반법, 초음파 진동법 등과 결합된 제어 냉각 기술 및 교반 장치 개발이 필요함.
(나) 반용융 금속을 금형에 일정한 양을 주입할 수 있는 이송 기술 개발
제품을 대량으로 제조하기 위하여 반용융 재료를 금형에 일정하게 주입하는 이송 기술 개발이 필요함.
(다) 반용융 금속의 성형 공정 확립
압연, 단조, 압출, 용탕 단조, 다이캐스팅 등에 있어 주입하는 반용융 금속의 고상률, 가압력, 가압속도, 가압시간, 다이 온도 등 최적의 공정 변수를 설정할 수 있어야 함.
5. 분말야금
(1) 개요
특수 가공 및 금형 중 금속 분말을 소요 형상의 금형에서 압축한 후 이것을 금속의 용융점 이하로 가열•소결하여 각종 제품을 가공하는 방법을 분말야금이라 함.
2종의 금속 또는 비금속 재료를 혼합하여 입자 간의 결합 강도를 향상시키고 필요한 성질을 부여하며 용융점이 높은 텅스텐, 몰리브덴 및 초경합금 등 치수 정밀도가 높은 기계부품의 대량생산에 적합함.
(2) 특징
용융점이 높은 금속에 적합함.
잘 융합되지 않는 금속 또는 비금속을 균일하게 섞어서 결합시킬 수 있음.
다공질의 금속 제품을 얻을 수 있음.
자동화로 대량생산이 가능함.
치수 정밀도가 높고 가공면이 평활하여 기계 가공이 불필요함.
(3) 제조 공정
① 분말 제조
– 기계 가공에 의한 방법.(절삭, 분쇄 등)
– 용금의 적하에 의한 방법.
– 분사에 의한 방법.
– 산화 분말을 이용하는 방법.
② 충전 및 성형
– 가압 성형.
– 원심 가압.
– 압출법
– 압연법.
③ 소결
– 1차 소결 및 재 압축.
– 2차 소결.
④ 교정(사이징, 코이닝)
⑤ 후처리
⑥ 제품 완성
(4) 분말의 가압 성형법
1) 1방향 압축방식
가장 간단한 방식으로 6mm 이하의 얇은 제품의 성형에 사용되는데 압축 시 다이와 하부 펀치는 고정되어 있고 상부 펀치의 하강에 의해 압축되며 하부 펀치의 상승으로 인해 성형 제품이 취출됨.
압분체의 상•하부 밀도 차가 커서 극히 얇은 제품을 성형할 경우에 사용함.
2) 2방향 압축방식
비교적 균일한 제품을 얻을 수 있으며 제품 각부의 높이가 다른 경우에는 금형을 분할하여 사용함.
상부 펀치의 하강과 하부 펀치의 상승에 의해 가압함.
3) 부동형 방식
다이를 스프링으로 받치고 상부 펀치로 압축함.
다이의 주동력으로는 유압이나 공기압을 이용하고 조정이 용이하며 균일한 제품을 얻을 수 있어 복잡한 형상의 압분체를 성형하는데 유리함.
4) 강제 인하 방식
다이가 프레스의 하부 슬라이드(램)에 연결되어 가압 중에 하부 펀치는 고정되어 있어도 다이가 하강하면 하부 펀치의 상승효과를 얻을 수 있도록 하여 2방향 압축 성형하는 방식임.
부동형 방식의 개량 다이라고 할 수 있으며 복잡한 형상, 특히 압축 방향의 단면 변화가 많은 압분체 성형에 사용됨.
(5) 분말야금의 응용
가공용 전극의 성형.
소결 베어링 제조.(오일리스 베어링)
내열 부품 제조.
공구 제조.(초경합금, 서멧)
요업 제품 제조.
6. 금속 박판의 특수 성형법
(1) 개요
판재의 특수 성형은 고무나 액체 대신 펀치나 다이를 사용한 성형법이 일반적으로 이용되고 있으나 새로운 형태의 성형법이 연구되어 상용화되고 있으며 이러한 가공법은 특수 용도의 제품을 소량생산하는 데 적합함.
(2) 워터 피닝
1) 개요
워터 피닝은 강구나 그릿을 사용하는 숏 피닝 가공법에서 숏 대신 물을 고속으로 분사하여 판재의 표면을 가공함.
위터 피닝은 다른 가공법에 비해 소재의 표면을 경화시켜 피로 수명을 증대시킬 수 있고 응력 부식을 방지함.
위터 피닝은 주로 연질 금속의 판재나 임의의 형상을 가진 구조재, 원자력 발전소 등에 이용됨.
2) 워터 피닝의 특징과 효과
(가) 특징
가공에 의한 열 영향부가 발생하지 않음.
가공면이 매끄러워 별도의 기계적인 연마 작업이 불필요함.
숏 피닝 가공에 비해 훨씬 큰 공작물을 가공할 수 있으며 완벽한 커버리지를 달성할 수 있음.
물을 이용하므로 유지비가 적게 들고 환경친화적임.
숏 피닝에서와 같은 쇼트 볼의 처리, 분진 회수 문제가 없음.
(나) 효과
압축 잔류응력의 생성.
표면부의 경도가 증가,
3) 워터 피닝의 적용
쇼트 볼 회수, 분진, 노치부 가공의 어려움, 예리한 모서리부 가공 시 균열 발생 등과 같은 숏 피닝의 문제점을 해결하고자 워터 피닝을 적용하는 데 항공기 엔진 가공이 대표적인 사례임.
(3) 인장 성형법
인장 성형법은 프레스 굽힘 가공에서 스프링 백을 제거하거나 줄이기 위해 굽힘 가공 중에 소재를 항복응력 이상까지 인장하고 압축을 하면서 성형하는 방법임.
소재의 양단을 조에 물리고 펀치로 가압하거나 고정된 펀치로 소재의 양단을 인장하여 가공함.
조에 물리는 부위는 재료 손실이 있으나 항공기 몸체, 지붕 판넬 등의 성형에 사용됨.
일반적으로 펀치와 소재의 마찰에 의해 일부분에 변형률이 집중되어 파단되는 경우가 있으며 이를 방지하기 위해 소재와 펀치 사이에 윤활을 좋게 하고 펀치의 코너 반지름을 크게 해야 함.
(4) 플라스마 용사 성형법
플라스마 용사 성형법은 이온화된 플라스마를 금속 분말과 함께 소재가 제품의 원형에서 필요한 크기와 두께가 될 때까지 반복 분사하여 성형한 후 제품을 원형으로부터 분리시켜 제품을 완성하는 방법임.
일반 금속재의 경우에는 경제적이지 못하지만 텅스텐과 같은 고용융점 재료의 성형에는 적합함.
(5) 레이저 빔 용접에 의한 성형법
모양과 크기, 두께가 다른 판재 조각을 블랭킹 등으로 가공한 후 레이저 빔 용접을 통해 일정 형상으로 붙이고 용접된 판재를 성형하여 제품을 완성하는 방법임.
양복을 재단하는 것과 유사하다고 하여 테일러드 블랭킹이라고 하며 판재 조각의 용접 강도가 매우 높음.
판재 조각을 이용하기 때문에 제품 설계의 유연성이 높고 부분적인 강도 조절이 가능하여 자동차 부품 제작에 많이 사용됨.
(6) 숏 피닝
1) 개요
숏 피닝은 경화된 작은 쇠구슬인 쇼트 볼을 피가공물에 고압으로 분사시켜 표면의 강도를 증가시킴으로써 기계적 성능을 향상시키는 가공법.
숏 피닝의 효과를 최대로 올리기 위해서는 압축 잔류응력을 극 표면으로 끌어내야 하는데 이것을 좌우하는 인자가 쇼트 볼임.
숏 피닝의 강도 조절 변수로는 쇼트 볼의 투사 속도, 크기, 경도, 형상, 단위 시간당 투사량 그리고 투사각도 등이 있음.
2) 숏 피닝 효과의 영향 인자
(가) 쇼트 볼의 크기
쇼트 볼의 다른 인자들이 일정하면 쇼트 볼의 크기가 커짐에 따라 아크 하이트는 커지고 적용 범위는 감소함.
작은 쇼트 볼은 적용 범위에 빨리 도달할 수 있는 이점이 있기 때문에 최소 쇼트 볼의 크기를 선택하여 요구되는 아크 하이트를 얻을 수 있어야 함.
(나) 공작물의 경도
공작물보다 쇼트 볼의 경도가 높으면 아크 하이트에는 영향이 없고 공작물보다 쇼트 볼의 경도가 낮으면 아크 하이트가 낮아짐.
(다) 쇼트 볼의 투사속도
쇼트 볼에 의해 행해지는 최대 일량은 운동 에너지를 초과할 수 없음.
높은 운동 에너지를 얻기 위해 쇼트 볼의 질량을 증가시키면 공작물의 표면 조도가 커지며 기계 작동 상의 문제가 발생할 수도 있음.
따라서 쇼트 볼의 투사속도를 증가시켜 높은 운동 에너지를 얻는 것이 현명한 방법임.
지나치게 쇼트 볼의 투사속도를 증가시키면 아크 하이트는 커지는 반면에 쇼트 볼의 파손율은 높아지고 표면 조도도 커지게 되므로 적절한 쇼트 볼 크기와 투사속도의 선정이 중요함.
(라) 쇼트 볼의 투사각도
쇼트 볼은 투사체가 날아와서 피가공물의 표면에 충격 에너지를 전달하여 압축 잔류응력이 소재의 수직방향으로 발생하게 되므로 입사각도가 0˚에 가까울수록 숏 피닝의 강도가 증가함.
충돌각이 증가하면 충격 에너지가 충돌각만큼 감소하기 때문에 되도록이면 충돌각을 작게 해야 재료 표면에 많은 충격 에너지를 공급할 수 있음.
(7) 핀 포밍
1) 개요
핀 포밍은 항공기 날개 판재의 곡면 부분을 가공하는 데 이용된 이후로 적용 범위가 확대되고 있고 형상을 만드는데 비용을 절약할 수 있으며 손쉽게 테이퍼나 만곡면을 만들어 낼 수 있고 무게에 비해 최대 강도를 증가시킬 수 있으며 재료의 불필요한 손실을 줄일 수 있음.
핀 포밍으로 숏 피닝을 하면 만곡이 일어나는데 이러한 성질을 이용하여 프레스 금형을 사용하지 않고 굽힘 가공이 가능하도록 한 가공법을 말함.
2) 핀 포밍의 원리
쇼트 볼의 충격에 의해 재료 내부에는 소성변형 영역이 발생되는데 투사 에너지의 양에 따라 재료에 전이되는 양이 결정됨.
쇼트 볼의 투사 에너지는 정확한 위치에 정확하게 피닝 강도를 부여해야 하며 가공 재료는 에너지를 흡수하여 소성변형이 될 수 있는 판재여야 함.
쇼트 볼의 투사 에너지는 쇼트 볼의 투사속도와 직경, 판재의 강성에 의존하며 판재는 투사 에너지가 낮을 경우 위로 볼록하게 변형이 이루어지지만 그 반대일 경우에는 아래로 볼록하게 변형함.
이러한 원리를 이용하여 숏 피닝 투사 에너지의 강약에 의한 변형량을 적절히 조절하면 원하는 곡면 형상을 만들 수 있음.
숏 피닝으로 가공한 면의 표층에 똑같이 반복해서숏 피닝을 시행하면 원래의 형상에 가깝게 환원되기 때문에 부분적인 적용을 통해 더욱 복잡한 면의 성형도 가능함.
3) 쇼트 볼의 투사 방식
(가) 중력 낙하식
중력 낙하식은 항공기의 큰 동체 날개를 제작할 때 사용되며 직경이 큰 쇼트 볼을 사용하여 두께 20mm 이상의 날개 표면을 가공함.
쇼트 볼의 투사속도는 저속으로 하여 가공면의 표면 거칠기를 좋게 하고 쇼트 볼의 투사각을 적절히 유지하며 중력 가속도에 의한 낙하 높이를 조절하여 원하는 가공 표면을 얻어야 함.
(나) 공기 노즐식
공기 노즐식은 크기가 작은 노즐 가공이나 매우 소량을 생산하는 경우에 적용되며 쇼트 볼이 커지면 속도의 조절이 어렵고 투사 에너지의 효율이 떨어지며 노즐의 직경도 커지게 되므로 적절한 크기의 쇼트 볼을 선정해야 함.
(다) 원심력 휠식
원심력 휠식은 쇼트 볼의 크기가 큰 것을 투사하는데 가장 적합한 방식이지만 쇼트 볼의 재질이나 크기에 관계없이 투사할 수 있음.
쇼트 볼의 투사속도를 매우 정확하고 재현성 있게 조절할 수 있으므로 CNC 숏 피닝기를 적용하는데 유용한 방식임.
CNC 숏피닝기는 쇼트 볼의 공급량을 조정하고 파쇄 및 마모된 쇼트 볼을 자동으로 분리할 수 있으며 임펠러 제어를 통해 공작물의 재질에 따라 투사속도를 제어할 수 있음.
(8) 워터 제트 가공
1) 개요
워터 제트 가공법은 물줄기를 고속으로 분출시켜 물체와 충돌시키면 물줄기의 운동량의 변화로 물체에 힘을 가하게 되는데 작은 노즐 구멍을 통해 초고압으로 분출시킨 물의 침식으로 소재를 가공함.
각종 기판, 복합 재료, 플라스틱, 작물, 나무, 종이, 가죽 등 비금속 재료의 절단에 우수한 성능을 발휘함.
2) 워터제트의 구성
(가) 고압증강 장치 및 펌핑 유닛
증압기는 물을 고압으로 만들어 주는 장치로써 왕복동형 플런저 펌프가 주로 사용되며 증압된 물은 축압기로 보내지는데 축압기는 물이 노즐에서 분출되기 전에 저장되는 곳으로 압력이 일정하게 유지되어야 함.
(나) 노즐
제트를 형성하는 곳으로 노즐의 직경은 0.05 ~ 0.5mm 정도이고 분출되는 물의 속도는 600 ~ 900m/sec이며 공작물과의 간격은 약 3 ~ 25mm임.
노즐의 구멍부는 사파이어를 주로 사용하나 최근에는 다이아몬드를 사용하기도 함.
3) 특징
예비 구멍이 불필요하고 버의 열적 손상이 거의 없음.
공작물 상에서 절삭력이 작아 취성 재료도 가공이 가능함.
공작물의 변형이 적어 유연한 재료의 절단에 용이함.
환경친화적이고 NC 회로 자유 곡선도 쉽게 가공할 수 있음.
소음이 크고 절단할 수 있는 두께에 제한이 있음.
(9) 입자 제트 가공
1) 가공 원리 및 특징
입자 제트 가공은 워터 제트 또는 비활성 가스의 흐름에 10 ~ 50μm의 연삭입자를 노즐부에서 같이 분출하여 공작물과의 기계적 충격력을 이용하는 가공법임.
금속도 충분히 절단할 수 있으며 열 발생이 없어서 열에 민감한 재료의 절단에 적합함.
2) 적용 분야
취성 재료의 가공.
미소 입자 블라스팅에 사용.
7. 컬링 금형
(1) 개요
특수 가공 및 금형 중 컬링은 판재 또는 용기의 윗부분에 원형 단면의 테두리를 말아 넣는 가공이며 플랜징과 같은 목적으로 사용됨.
플랜지 부분을 둥글게 가공하는 것으로서 컬링 속에 철사나 봉재를 넣고 겉면을 둥글게 하는 것을 와이어링이라 함.
컬링은 경첩과 같은 판형 제품의 컬링 가공과 드로잉 된 원통형 용기의 가장자리에 테두리를 만드는 컬링 가공 2가지로 나뉨.
컬링을 하는 목적은 강도를 높이고 끝부분의 예리함을 없애주기 위함임.
(2) 가공 종류
1) 판형 제품의 컬링 가공
컬링 가공은 일반적으로 컬링 할 부분을 일정한 곡률로 약간 굽혀주는 제1공정과 원형의 형상으로 완전히 마는 제2공정으로 구분.
제1공정은 펀치의 한쪽 날을 제1공정의 형상으로 하여 재료가 눌려 굽혀지면서 블랭킹 작업과 동시에 진행됨.
미리 전단된 제품을 굽힘 가공별로 하여 제2공정을 마무리함.
2) 원통 용기의 컬링 가공
원통 용기의 컬링 가공은 판형 제품과 같이 2단계의 공정을 가지지 않고 1공정에 가공을 완료함.
원통 용기의 컬링 부위는 가공면이 균일해야 하며 불균일할 때는 트리밍 가공을 해야 함.
(3) 컬링 금형의 종류
1) 판형 컬링 금형
판형 컬링 금형은 컬링한 부분이 위로 가도록 재료를 다이에 세워서 가공하는 방식과 다이에 컬링 홈을 만들어 재료를 밀어 넣고 위에서 펀치로 가압하는 방식으로 구분됨.
펀치에서 컬링 부분이 굽혀질 경우 둥글게 말리는 부분은 펀치의 상승 시 펀치에 끼어 위로 올라가 다이에서 빠져나오게 됨.
이후 제품은 손이나 녹아웃 장치에 의해 펀치에서 취출됨.
다이에 부시를 설치한 컬링 금형인 경우 제1공정에서 굽혀지는 부분이 다이 속으로 들어가면 펀치의 압력에 의해 부시 구멍의 원추를 따라 둥글게 말림.
다이 속에서 컬링 가공된 제품은 다이에 꽉 차기 때문에 펀치의 상승 시 작동되는 기계적 도그래그 캠과 슬라이드 장치를 이용함.
2) 원통 용기의 컬링 금형
원통 용기의 컬링 금형은 내 컬링과 외 컬링으로 구분됨.
컬링 홈은 펀치에 설치되어 있고 다이는 제품의 외형에 똑같은 형상으로 가공함.
다이의 길이는 제품의 컬링 깊이를 뺀 값보다 약간 작아야 하며 제품의 밑바닥 라운드 부분이 꼭 맞게 다이가 제작되어야 함.
펀치의 컬링 홈은 말리는 내측 부분을 더 길게 하고 약 30˚ 정도 경사지게 하여 소재의 안내를 원활하게 함.
가공할 소재의 용기가 깊은 경우에는 녹아웃 장치를 설치하여 제품을 취출함.
8. 버링
(1) 개요
특수 가공 및 금형 중 버링은 평판에 기초 구멍을 뚫고 그것으로부터 직경이 큰 펀치로 훑어 내려서 원통 벽을 세우는 공정으로서 홈 플랜징이라고도 함.
버링 된 플랜지의 내면에 성형용 탭을 이용하여 암나사를 가공하거나 두께 이상의 판을 리벳 없이 결합할 때 이용함.
보통의 버링 가공에서는 수직벽의 판 두께가 15 ~ 20%이고 1회 가공으로 달성할 수 있는 플랜지 높이의 한계는 대체로 구멍 지름의 10% 정도임.
(2) 버링의 가공 변수
1) 펀치 선단의 형상
펀치 선단의 형상이 원추형으로 예리할수록 성형성은 증가하나 성형 스트로크가 길어지게 됨에 따라 생상성이 저하됨.
2) 구멍의 전단면 상태
구멍의 전단면 상태가 불량하면 균열이 생겨 성형을 저하시킴.
피어싱한 구멍의 전단면을 드릴링 등을 통해 다듬질하게 되면 상대적으로 플랜징의 높이가 높은 버링 가공이 가능함.
3) 재료의 성질
연성이 높은 재질은 변형 저항이 작게 되어 버링의 가공성을 향상시킴.
알루미늄은 보통 강판에 비해 버링 가공의 한계(펀치의 직경 / 초기 구멍의 직경)가 약 40% 향상됨.
4) 다이의 코너 반지름
가능한 한 다이의 코너 반지름을 크게 해야 버링 된 수직벽의 높이를 높일 수 있음.
(3) 버링 가공의 종류
1) 일반 버링
태핑용 버링 가공을 할 때에는 탭의 치수를 먼저 결정한 다음 버링 치수를 결정하고 마지막으로 피어싱 치수를 결정함.
드로잉 가공과 같이 블랭크 홀더를 부착하여 피어싱된 소재를 누르면서 가공하는 것이 일반적임.
드로잉 제품의 밑바닥을 펀칭하고 버링으로 제품의 높이를 증가시키는 방법도 있는데 이를 드로 버링이라함.
2) 돌파 버링
구멍 뚫기와 버링을 동시에 가공하는 것으로서 구멍을 가공한 후 확대·성형한 것임.
작은 구멍의 버링에 많이 사용하고 펀치의 선단 각도는 소재 두께에 영향을 받으나 대략 55 ~ 60˚ 정도로 함.
펀치의 선단 형상을 3각, 4각, 5각으로 하여 초기의 구멍을 내지 않은 상태로 1회 가공으로 돌파하면서 버링 가공을 하는 경우도 있으나 이 경우 플랜지의 윗부분에 균열이 생김.
3) 스트레치 버링
Φ12mm 이하의 비교적 작은 구멍은 피어싱과 버링을 동시에 할 수 있는 스트레치 버링 공정을 취함.
펀치에 단을 주어 1공정에서 1개의 펀치로 피어싱과 버링 가공을 시행함.
4) 아이오닝 버링
일반적으로 버링 가공에서 버링 된 측벽의 판 두께 감소가 15 ~ 30%이나 판 두께의 감소를 일반 버링의 2배 정도로 크게 하여 수직벽의 높이를 증가시키는 버링 가공법.
9. 스웨이징
(1) 개요
특수 가공 및 금형 중 스웨이징은 중공축, 중실축 및 강선 등의 소재를 2개 또는 그 이상의 분리형 금형에 삽입한 후 소재의 반지름 방향으로 점진적인 반복하중을 가하여 소재의 단면을 변화시키는 점진 성형 공정으로 기계 가공을 필요로 하지 않음.
로터리 스웨이징은 봉이나 원통형 관 모양의 재료를 축 주위로 회전시키면서 공구를 이용하여 재료를 한 부분씩 축과 직각방향으로 짓눌러 경사지게 하거나 지름을 줄여서 길이를 늘이는 점진 성형 공정으로 자동차 중공축 등의 생산에 활용됨.
(2) 스웨이징 공정
1) 로터리 스웨이징
로터리 스웨이징은 스웨이징 또는 경방향 단조라고도 하며 왕복운동하는 금형으로 봉재나 관재의 반지름 방향으로 타격하여 작업을 진행함.
금형의 움직임은 롤러 베어링처럼 틀 속에 들어 있는 롤러에 의해 이루어지며 소재는 움직이지 않고 금형 세트가 회전하면서 초당 20회 정도의 고속으로 소재에 타격을 가하여 주로 축 대칭 원형 제품을 생산하지만 외륜 회전형인 경우에는 육각형, 팔각형, 타원형, 십자형 같은 비원형 제품도 생산할 수 있음.
2) 금형 밀폐형 스웨이징
금형 밀폐형 스웨이징은 금형의 운동이 왕복하는 쐐기의 운동으로부터 얻어지는데 로터리 스웨이징에 비해 금형이 넓게 벌어지므로 지름이 크거나 고르지 않은 제품도 생산할 수 있음.
또 다른 유형으로는 금형이 회전하지 않고 반지름 방향으로 왕복운동만 하는 것도 있음.
금형 밀폐형 스웨이징은 2개의 롤러가 트러스트 피스 양단에 위치할 때 다이는 최대한 개폐가 되며 이러한 방법은 트러스트 피스나 다이스의 관리나 교체 시 유리한 구조를 가짐.
해머의 스트로크만큼 서로 마주 보고 있는 금형은 축 중심을 향하여 반지름 방향으로 타격을 유발하게 되며 반복적인 충격에 의해 금형 속의 소재는 점진적으로 금형 형상으로 성형이 이루어짐.
맨드렐을 사용하면 내부에 형상이 있는 튜브 제품도 성형할 수 있음.
(3) 특징
치수 정밀도가 우수한 고정도의 제품의 대량생산에 유용함.
설비비가 저렴하고 구조가 간단하며 비숙련자도 작업이 용이함.
강과 비철금속 등 여러 가지 재질을 이용하여 열간, 냉간 성형이 가능함.
금속 섬유 조직이 연속적으로 형성되어 기계적 성질을 향상시킴.
절삭가공에 비해 경면에 가까운 표면 정밀도를 얻을 수 있음.
칩 발생이 없고 재료비가 40% 이상 절감됨.
다른 점진 성형 공정보다 높은 소음과 진동이 발생함.
(4) 성형 가공 형상
축 대칭 성형 소재의 중앙부 단면을 감소시키는 성형.
봉재 성형, 튜브 성형, 내•외부 성형.
테이퍼 성형, 튜브의 끝단 오므리기 성형.
10. 하이드로 포밍
(1) 개요
특수 가공 및 금형 중 하이드로 포밍은 금형 속에 들어가 있는 강관 속에 물 등의 액체를 주입하여 내부에부터 강한 액압을 가하여 복잡한 형상으로 일체 성형하는 공법.
하이드로 포밍은 관의 중간 부분을 확관 가공하는 가공법과 굽혀진 강관의 일부를 확관하는 가공법으로 나뉨.
하이드로 포밍의 가장 큰 특징은 한 개의 파이프로 요철이 있거나 휘어진 복잡한 형태의 제품을 단 한번에 만들어 낼 수 있음.
(2) 종류와 특징
1) 관재 하이드로 포밍
관재 하이드로 포밍 제품은 전 세계 자동차 회사에서 가장 많이 사용하고 있는 추세이며 그 적용 부품 역시 점차 확대되고 있음.
관재 하이드로 포밍 제품은 경량화 뿐만 아니라 부품수를 감소시켜 조립 공정을 단순화할 수 있으며 조립 정도를 향상시킬 수 있는 효과가 있음.
하지만 생산 설계 기술이 요구되고 초기 투자비가 많이 든다는 것이 단점임.
2) 판재 하이드로 포밍
관재 하이드로 포밍에 비해 판재를 이용한 하이드로 포밍은 생산성 및 투자비 때문에 적용 범위가 크게 늘어나지 않고 있음.
판재 하이드로 포밍은 펀치만으로 제품을 성형하는 기술로 고무를 이용한 마폼법에서 고무 대신에 액체를 이용한 것이 유사함.
기존 프레스 금형을 이용한 성형에서 다이측을 액압 탱크로 구성하여 액압을 이용하여 펀치 형상대로 제품을 가공하는 방법임.
따라서 금형비가 프레스 금형보다 적게 소요되어 다품종 소량생산에 유리하고 제작 기간을 단축시킬 수 있음.
관재 하이드로 포밍과 마찬가지로 판재 하이드로 포밍도 경량화의 효과를 높일 수 있는 장점을 가짐.
(3) 생산설비
하이드로 포밍은 금형에 의존하기보다는 재료 특성에 따른 압력을 제어하는 기술에 더 의존하는 가공법임.
따라서 하이드로 포밍의 성공 여부는 외부로부터 압력 부하나 힘을 가하는 타이밍, 크기, 속도 등을 어떻게 제어하는가에 달려있음.
하이드로 포밍 프레스는 단독 고압 프레스 장비에 자동화 장비를 설치하여 라인 개념으로 구성하는 게 일반적임.
기존 하이드로 포밍 장비와 달리 프레스가 모듈화되어 있으며 성형 시 고압으로 금형을 지지하는 것이 아니라 프레스 구조물을 기계적으로 고정시킴으로서 고압에 대한 반발력을 유지할 수 있기 때문에 라인 개념으로 구성할 수 있음.
11. 고무 성형
(1) 개요
고무 성형은 압축 성형법이 일반적으로 널리 이용되고 있음.
고무 생지로 고무 제품을 성형할 때에는 일반적으로 혼합, 성형, 가황, 다듬질 등의 공정을 거쳐 성형함.
성형가공을 용이하게 하기 위해 가역화한 고무에 가황제, 촉진제, 노화 방지제 등의 배합제를 혼합함.
하지만 플래시 발생, 스프루-러너의 가류화에 따른 손실, 제품 취출 후 폐기되는 스크랩으로 인한 환경 문제 발생, 후공정에 따른 품질 저하 및 원가 상승, 자동화를 수행할 수 없는 금형 구조로 인해 대량생산에서 나타는 취약점 등이 대두되고 있음.
(2) 고무 성형 금형의 고려 사항
1) 형체 기구
고무 성형은 금형의 작은 틈새가 있으면 플래시가 발생함.
이것을 방지하기 위해 금형 설계, 제작상에서의 열적 요인을 충분히 고려해야 하며 형체 장치로 휨을 억제할 수 있는 고강성의 플레이트와 가공정도, 열변형 대책이 중요함.
성형품의 투영면적보다 형체결력이 작으면 사출압력에 의해 고정측 형판과 가동측 형판 사이가 벌어져 플래시가 발생함.
2) 가스제거(범핑)
사출 성형에서는 고압 형체로 닫힌 금형 내에 고무 생지를 충전하는데 캐비티 내의 공기나 가류반응에 의한 가스를 빼내는 동작이 필요하게 되어 충전 완료 후에 타이밍을 가늠하여 형체압력을 내리거나 금형을 조금 열어 공기나 가스를 배출하고 다시 형체 하는 동작으로 성형 불량을 피해야 함.
3) 진공장치
금형 캐비티 내의 공기나 가류반응에 의한 가스를 진공펌프로 흡인하는 방법으로서 금형에 설치된 가스 빼기 홈을 이용하여 흡인하거나 파팅 라인에 오링실 등을 설치하여 형체 일시정지 시 흡인 후 사출하는 과정을 수행함.
4) 플래시 제거
일반적으로 고무 금형에서 완벽한 플래시 처리가 불가능한 것으로 보이지만 플래시를 깨끗이 처리하기 위해서는 고무 재료의 흐름성이나 사상성과 기계의 정확한 정도가 중요함.
금형의 각 형판들의 정밀 평판 연삭을 통한 두께 평행도를 정확하게 가공하고 여러 판을 조립한 후에도 정확한 평행도를 유지해야 함.
형체결력과 캐비티 개수 등의 선정이 균일한 압력을 유지하기 위하여 금형에 가하는 압력 지점을 다르게 하고 압력을 집중시켜 접합부를 정밀 밀착시키는 금형 제작 기술을 확보함으로서 플래시 발생을 방지할 수 있음.
(3) 고무 성형의 종류
1) 압축성형
압축성형은 고무 성형의 기본적인 방법으로서 열경화성 플라스틱의 대표적인 성형법임.
계량한 원료를 가열한 금형의 캐비티에 넣어 가압하여 경화시켜 성형하는 방법으로서 원료는 캐비티 내에서 가열되어 경화하므로 적당한 경화시간 후 금형을 열고 성형품을 취출함.
캐비티 내의 공기를 빼고 원류를 흘려 충전을 좋게 하기 위해 진공 흡인을 하거나 가열•화학반응으로 발생한 가스를 빼는 조작을 등을 수행해야 함.
압축성형은 설비비가 저렴하고 어떠한 성형 재료도 성형 가능하며 성형품 배향이 적고 재료 손실이 적은 장점이 있음.
고무 제품의 다품종 소량생산에 넓게 사용되고 있음.
2) 사출성형
플라스틱 사출성형과 매우 유사한 방법으로서 고무 생지는 스크루로 연속 공급하고 소정량을 연화•용융시켜가며 계량하는 스크루로 금형에 고압•충전하고 가류하는 성형법임.
다른 성형법보다 성형 사이클이 빠르고 균일한 가류 제품을 얻을 수 있어 대량생산에 적합함.
3) 이송성형
사출성형의 간이 방법으로서 고무 생지를 가열부에서 가열하여 가압부로 이송한 후 플랜저로 가열된 금형에 주입하여 가류를 하는 성형법임.
이송성형에서 성형압력이 가장 중요한 요인이며 성형압력이 낮으면 충전을 완료하기가 어렵고 반대로 너무 높으면 플래시가 발생할 뿐만 아니라 캐비티 내의 각종 핀 이나 코어류 및 삽입물 등에 과대한 힘이 작용하여 변형되거나 그 위치를 어긋나게 하여 이송성형의 본래의 이점을 잃게 됨.
이송성형에서는 포트부의 구조상 재료의 흐름에 대한 저항이 크기 때문에 보조 램식 이송성형의 경우에 비해서 10 ~ 20% 높은 성형압력이 필요함.
특수 가공 및 금형 연재를 끝으로 소성가공에 대한 연재을 마치고 다음에는 금형 제작 및 측정에 대한 연재를 시작할 예정입니다.
2020년 09월 06일
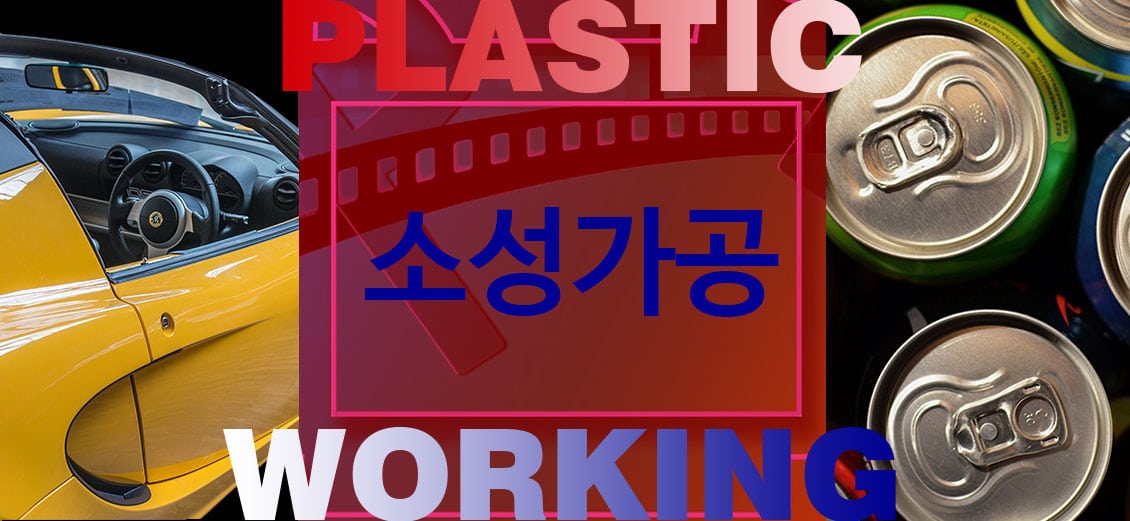
소성가공 4
제4장 특수 가공 및 금형
소성 가공 중에서 특수 가공 및 금형(PLASTIC WORKING)에 대표적인 것으로는 다이나 롤러를 이용하여 소재를 공구의 표면 형상으로 각인하는 전조와 금속 분말을 금형에서 압축한 후 가열•소결 하여 제품을 가공하는 분말야금이 있습니다.
1. 전조
(1) 개요
특수 가공 및 금형 중 전조는 다이나 롤러와 같은 성형 공구를 회전 또는 직선운동시키면서 그 사이에 소재를 넣어 공구의 표면 형상으로 각인하는 일종의 특수 압연을 말함.
전조로 가공되는 제품으로는 기어, 나사, 볼, 링, 스플라인 축 등이며 전조기에는 제품에 따라 특수한 장치를 갖춘 전용기가 있음.
(2) 특징
소재의 섬유조직이 전단되지 않으므로 제품의 강도가 큼.
소재와 공구의 국부적인 접촉으로 인한 작은 가공력만 가지고도 가공이 가능함.
칩이 생성되지 않으므로 소재의 이용률이 높음.
소성변형으로 인한 가공경화 및 치밀한 조직이 형성됨.
가공속도가 빠르고 자동화가 쉬움.
(3) 전조 가공의 종류
1) 나사 전조
(가) 평 다이 전조
평 다이 전조는 한 쌍의 평 다이 중 하나는 고정, 다른 하나는 직선운동을 시켜 1회의 행정으로 나사를 성형하는 방법.
평 다이 전조의 소재는 대부분 연성재료가 사용되며 다이에는 성형부와 다듬질부가 있음.
둥근형 다이 전조에 비해 제품의 정밀도가 떨어짐.
(나) 둥근형 다이 전조
둥근형 다이 전조는 고정축 다이와 가동축 다이로 되어 있으며 두 축은 평행하고 재료는 지지대에 의해 지지됨.
둥근형 다이 전조는 가동축은 축이 이동되며 롤러 다이를 3개 사용하는 경우가 있음.
평 다이 전조에 비해 생산속도가 매우 빠르고 정밀한 나사를 제작할 수 있음.
(다) 프래너터리 전조(PLANETARY 전조)
프래너터리 전조는 고정 원호 다이를 고정시키고 원형 다이를 회전시켜 자동으로 장입 소재가 타단에서 완성된 나사로 나오며 물림률이 크고 대량생산에 적합함.
프래너터리 전조는 크랭크 운동에 의한 평 다이 전조에서는 가공을 하지 않는 귀환행정이 있으나 플래너터리 전조에서는 공전이 없으므로 가공 능률이 높음.
2) 기어 전조
(가) 래크 다이 전조
래크 다이 전조는 한 쌍의 래크 다이 사이에 소재를 넣고 압력을 가하면서 래크를 이동시켜 소재의 치형을 성형함.
이 방법은 지름이 큰 기어에 대해서는 래크가 커야 하고 설치 공간도 넓어야 되기 때문에 지름이 작은 기어 제작에 적합함.
기어 전조법은 보통 냉간가공을 하고 있으나 모듈이 약 3 이상인 경우나 굵은 재료의 경우에는 열간가공으로 함.
(나) 피니언 다이 전조
피니언 다이 전조는 피니언 다이와 소재의 맞물림을 동일하게 하여 압력을 가하면서 회전시켜 치형을 성형하며 공구의 작동이 용이함.
피니언 다이 전조는 지름이 큰 기어, 웜, 스플라인 성형가공에 많이 적용됨.
(다) 호브 다이 전조
호브 다이 전조는 전조 공구를 상하에 두고 소재를 회전시키면서 축 방향으로 보내어 성형함.
소재는 인덱스 헤드에 의하여 소정의 각도만큼 회전시켜 다이 사이에 삽입됨.
소재의 유동이 좋고 롤러에 무리한 힘이 작용되지 않음.
3) 볼 전조
볼 전조는 2개의 다이가 롤러 축과 교차되어 있어 소재의 성형과 이송을 동시에 행함.
다이의 홈은 볼을 성형하는 가공면이고 산은 소재를 오목 패이게 가공하면서 최후에는 절단하는 역할을 함.
볼 전조는 500 ~ 1,000℃의 열간가공에서 행해짐.
4) 드릴 전조
드릴 전조는 소재가 길이 방향으로 연신 되면서 홈이 성형됨.
공구는 홈 가공용과 릴리프면 가공용이 따로 있음.
2. 반용융 금속을 이용한 성형법(SEMI-SOLIDE FORMING PROCESS)
(1) 반용융 압연
1) 성형 방법 및 특징
특수 가공 및 금형 중 반용융 압연이란 반용융 금속으로부터 열연강판 및 냉연강판을 제조하는 것으로 롤러 사이에 주입하는 금속의 주입온도를 낮춤으로써 롤러에 발생하는 열응력과 열피로 현상을 감소시켜 롤러의 수명을 연장시킬 수 있음.
롤러 내에서 응고하기 시작한 재료의 응고 완료점의 위치에 따라 판재 성형성이 결정되기 때문에 롤러의 온도 및 속도 변화에 따른 응고 제어가 매우 중요함.
2) 기술적인 요점
(가) 공정변수의 확립을 통한 자동화
고상률, 롤러 회전수, 롤러 간격, 탕면 높이, 재료의 주입방법, 롤러 냉각방법 등과 같은 공정변수들 사이의 관계가 정량적으로 규명되어야 하며 공정변수를 변화시켜 응고속도를 일정하게 유지되도록 제어해야 함.
(나) 롤러 냉각 방식에 따른 냉각 특성 파악
냉각 특성에 따른 롤러 재질 선정, 롤러 형상 설계, 냉각수 주입량을 결정하여 롤러에 작용하는 열응력 및 열피로를 줄임.
(다) 분산장치 및 노즐 형상의 결정
반용융 금속을 롤러 폭 방향으로 균일하게 분산시키기 위한 분산장치 및 노즐의 형상이 결정되어야 함.
(2) 반용융 단조
1) 성형 방법 및 특징
반용융 단조는 금속의 온도를 제어하면서 교반을 행하는 교반부, 밀폐형 다이 내로 주입하기 위한 주입부, 그리고 밀폐형 다이와 다이 내에 충전된 반용융 금속을 가압하는 가압부로 구성됨.
반용융 단조는 단조 하중이 작고 가공속도가 빠르며 편석, 기공 등과 같은 결함이 없는 주조와 단조 공정이 결합된 복합 공정임.
2) 기술적인 요점
(가) 성형 가능한 고상률 범위와 금형온도
반용융상과 고상의 경계를 시간에 따라 추정하여 완전히 응고가 되는 시간을 예측하고 시간의 변화에 따라 응고 측정과 다이의 온도 분포를 파악하여 금형의 예열온도를 예측해야 함.
(나) 최적 단조 조건 확인
단조압력, 단조속도, 단조시간 등이 정량적으로 확립되어야 하며 이들 인자의 변화에 따른 재료의 흐름 특성과 재료의 이방성이 파악되어야 함.
또한 공구의 최적 윤활제 선정, 금형온도가 품질에 미치는 영향 등이 검토되어야 함.
(3) 반용융 압출
1) 성형 방법 및 특징
반용융 압출은 기존의 빌렛 대신 반용융 금속을 호퍼를 통해 컨테이너 내에 공급하고 스템의 가압과 동시에 다이를 통하여 원하는 부품을 성형함.
2) 기술적인 요점
(가) 컨테이너 및 금형의 온도 제어
반용융 금속의 고상률의 제어 때문에 컨테이너에서의 온도 제어가 중요하며 결정립의 균일한 분포를 위해 다이의 온도 제어가 특히 중요함.
(나) 금속 복합재료의 압축 기술
강화제의 파단을 방지하기 위한 다이의 설계, 기지 내의 소성유동과 강화제의 배향 사이의 관계가 정립되어야 함.
(4) 반용융 다이캐스팅
1) 성형 방법 및 특징
(가) 성형 방법
용융 금속을 전자 교반하면서 연속 주조를 통해 수지상 결정을 분단하여 균일한 조직의 빌렛을 만든 후 다이캐스팅 1 SHOT에 해당하는 양만큼 자름.
로터리식 유도가열 장치에 의해 약 590℃까지 가열하여 고상률 50 ~ 60%의 반용융 상태로 만들고 반용융 빌렛을 로봇을 이용하여 사출 슬리브에 삽입한 후 플런저로 금형의 캐비티 내로 사출 충전함.
반용융 다이캐스팅 제품은 수축이 적고 편석이 적어 기계적 강도가 안정되며 내기밀성이 우수함.
(나) 특징
① 제조상의 특징
– 점성 충전이므로 탕 끝에서 공기 권입이 없음.
– 이미 반은 응고된 상태이므로 수축 캐비티가 적음.
– 저온 주입으로 형 수명이 길고 에너지가 절감됨.
– 유지로가 필요 없음.
– 주조 핀이 거의 발생하지 않음.
– 응고 수축이 작으므로 이형하기도 쉽고 치수 정밀도가 좋아 정형가공이 용이함.
– 복합재료의 제조가 용이함.
– 작업환경이 양호함.
② 제품의 특징
– 블로 홀이 매우 적음.
– 편석이 적음.
– 파단질층이 적음.
– 표면에서 내부까지 균일한 입상조직을 취함.
– 기밀성이 양호함.
– 연성, 인성이 현저하게 큼.
2) 기술적인 요점
(가) 반용융 다이캐스팅 빌렛
수지상의 결정이 파괴•분단된 조직의 빌렛을 저렴하게 제조할 수 있어야 하는데 빌렛의 가격이 높아 반용융 다이캐스팅의 보급이 광범위하게 이루어지지 못하고 있음.
(나) 주조 조건
초기에 플런저의 전진속도는 고속이지만 금형의 캐비티에 용융 금속을 충전 할 경우에는 저속이므로 사출속도를 임의로 설정할 수 있는 고출력의 사출기구를 가진 다이캐스트 머신이 필요함.
(다) 금형 설계
반용융 금속은 고점성 충전이므로 유동저항의 경감 및 충류 충전을 위해 탕구를 두껍게 하고 인발 코어 등을 추가하며 가스 빼기를 충분하게 설치하고 가공여유를 많이 주는 것이 좋음.
금형은 예열 장치 및 온도조절 장치가 있어야 함.
3. 신기술 단조 방법
(1) 개요
단조의 가공속도 향상을 통해 생산성을 향상시키거나 작은 하중으로 고품질의 제품을 생산할 뿐만 아니라 다이의 수명을 연장시키기 위한 새로운 단조법이 연구 개발되고 있고 이를 신기술 단조법이라 함.
(2) 신기술 단조 방법의 종류
1) 고에너지 단조
고에너지 단조는 내연기관을 이용하여 수천 분의 일 초만에 순간적으로 단조 가공을 완료하는 기술임.
주로 판재 성형에 응용되며 얇은 단면을 가지는 복잡한 형상의 제품 생산에 적합함.
상용화된 고에너지 단조 기계로는 영국에서 개발한 PETRO FORGE, 미국에서 개발한 DYNAPAK 등이 있음.
2) 반용융 단조
3) 분말 단조
분말 단조는 분말 소재를 소력하여 만든 예비 성형체를 열간 단조하여 제품을 만드는 단조법.
분말 단조는 가공 단계가 단순하고 후처리가 필요 없어 복잡한 형상을 만들 수 있음.
주로 커넥팅 로드, 기어 등과 같이 높은 강도를 요하는 기계부품 생산에 적합함.
4) 등온 단조
등온 단조는 가열 금형 단조라고도 하며 가열된 소재의 온도와 동일하도록 다이를 가열하여 단조하는 방법.
등온 단조는 단조가 진행되는 동안 소재가 냉각되지 않으므로 소재의 유동이 원활하여 작은 힘으로도 제품을 성형할 수 있음.
등온 단조용 다이는 니켈이나 몰리브덴 합금으로 제작됨.
4. 반용융 가공의 특징과 문제점
(1) 개요
특수 가공 및 금형 중 반용융 가공은 용융 상태에서의 금속을 냉각 도중 기계적으로 교반하여 수지 상정을 파괴시킨 다음 압연, 압출, 단조, 용탕 단조 및 다이캐스팅에 의하여 제품을 제조하는 공정으로 주조와 단조 공정이 결합된 복합 공정을 말함.
반용융 가공은 에너지 절약, 응용범위 확대, 공정 단축 등의 측면에서 많은 연구와 관심을 불러일으키고 있음.
(2) 반용융 가공의 특징과 문제점
1) 특징
변형저항이 현저하게 적어 적은 하중으로도 가공률을 증대시킬 수 있고 가공 기계 설비의 소형화가 가능함.
유동성과 성형성이 양호하기 때문에 공정 단축이 가능하고 에너지 절약과 재료의 절감을 이룰 수 있음.
결정립이 미세한 주조 조직을 얻을 수 있고 기계적 성질이 우수한 제품을 만들 수 있음.
이종 재료와의 접합이 용이하여 분산 강화 및 적층 강화형 복합 재료의 제조가 가능하고 성형성이 우수함.
다이캐스팅 및 용탕 단조법에서의 용융 재료보다 온도가 훨씬 낮기 때문에 금형과 공구에 가해지는 열적 부하가 적어 수명을 연장시킬 수 있음.
단조 시 편석이 없는 균질한 제품의 제조, 압력 및 냉각속도의 제어에 의하여 결함과 기공이 없는 성형이 가능함.
2) 문제점
(가) 반용융 금속의 연속적인 제조 기술 개발
기계적 교반법, 전자기적 교반법, 초음파 진동법 등과 결합된 제어 냉각 기술 및 교반 장치 개발이 필요함.
(나) 반용융 금속을 금형에 일정한 양을 주입할 수 있는 이송 기술 개발
제품을 대량으로 제조하기 위하여 반용융 재료를 금형에 일정하게 주입하는 이송 기술 개발이 필요함.
(다) 반용융 금속의 성형 공정 확립
압연, 단조, 압출, 용탕 단조, 다이캐스팅 등에 있어 주입하는 반용융 금속의 고상률, 가압력, 가압속도, 가압시간, 다이 온도 등 최적의 공정 변수를 설정할 수 있어야 함.
5. 분말야금
(1) 개요
특수 가공 및 금형 중 금속 분말을 소요 형상의 금형에서 압축한 후 이것을 금속의 용융점 이하로 가열•소결하여 각종 제품을 가공하는 방법을 분말야금이라 함.
2종의 금속 또는 비금속 재료를 혼합하여 입자 간의 결합 강도를 향상시키고 필요한 성질을 부여하며 용융점이 높은 텅스텐, 몰리브덴 및 초경합금 등 치수 정밀도가 높은 기계부품의 대량생산에 적합함.
(2) 특징
용융점이 높은 금속에 적합함.
잘 융합되지 않는 금속 또는 비금속을 균일하게 섞어서 결합시킬 수 있음.
다공질의 금속 제품을 얻을 수 있음.
자동화로 대량생산이 가능함.
치수 정밀도가 높고 가공면이 평활하여 기계 가공이 불필요함.
(3) 제조 공정
① 분말 제조
– 기계 가공에 의한 방법.(절삭, 분쇄 등)
– 용금의 적하에 의한 방법.
– 분사에 의한 방법.
– 산화 분말을 이용하는 방법.
② 충전 및 성형
– 가압 성형.
– 원심 가압.
– 압출법
– 압연법.
③ 소결
– 1차 소결 및 재 압축.
– 2차 소결.
④ 교정(사이징, 코이닝)
⑤ 후처리
⑥ 제품 완성
(4) 분말의 가압 성형법
1) 1방향 압축방식
가장 간단한 방식으로 6mm 이하의 얇은 제품의 성형에 사용되는데 압축 시 다이와 하부 펀치는 고정되어 있고 상부 펀치의 하강에 의해 압축되며 하부 펀치의 상승으로 인해 성형 제품이 취출됨.
압분체의 상•하부 밀도 차가 커서 극히 얇은 제품을 성형할 경우에 사용함.
2) 2방향 압축방식
비교적 균일한 제품을 얻을 수 있으며 제품 각부의 높이가 다른 경우에는 금형을 분할하여 사용함.
상부 펀치의 하강과 하부 펀치의 상승에 의해 가압함.
3) 부동형 방식
다이를 스프링으로 받치고 상부 펀치로 압축함.
다이의 주동력으로는 유압이나 공기압을 이용하고 조정이 용이하며 균일한 제품을 얻을 수 있어 복잡한 형상의 압분체를 성형하는데 유리함.
4) 강제 인하 방식
다이가 프레스의 하부 슬라이드(램)에 연결되어 가압 중에 하부 펀치는 고정되어 있어도 다이가 하강하면 하부 펀치의 상승효과를 얻을 수 있도록 하여 2방향 압축 성형하는 방식임.
부동형 방식의 개량 다이라고 할 수 있으며 복잡한 형상, 특히 압축 방향의 단면 변화가 많은 압분체 성형에 사용됨.
(5) 분말야금의 응용
가공용 전극의 성형.
소결 베어링 제조.(오일리스 베어링)
내열 부품 제조.
공구 제조.(초경합금, 서멧)
요업 제품 제조.
6. 금속 박판의 특수 성형법
(1) 개요
판재의 특수 성형은 고무나 액체 대신 펀치나 다이를 사용한 성형법이 일반적으로 이용되고 있으나 새로운 형태의 성형법이 연구되어 상용화되고 있으며 이러한 가공법은 특수 용도의 제품을 소량생산하는 데 적합함.
(2) 워터 피닝
1) 개요
워터 피닝은 강구나 그릿을 사용하는 숏 피닝 가공법에서 숏 대신 물을 고속으로 분사하여 판재의 표면을 가공함.
위터 피닝은 다른 가공법에 비해 소재의 표면을 경화시켜 피로 수명을 증대시킬 수 있고 응력 부식을 방지함.
위터 피닝은 주로 연질 금속의 판재나 임의의 형상을 가진 구조재, 원자력 발전소 등에 이용됨.
2) 워터 피닝의 특징과 효과
(가) 특징
가공에 의한 열 영향부가 발생하지 않음.
가공면이 매끄러워 별도의 기계적인 연마 작업이 불필요함.
숏 피닝 가공에 비해 훨씬 큰 공작물을 가공할 수 있으며 완벽한 커버리지를 달성할 수 있음.
물을 이용하므로 유지비가 적게 들고 환경친화적임.
숏 피닝에서와 같은 쇼트 볼의 처리, 분진 회수 문제가 없음.
(나) 효과
압축 잔류응력의 생성.
표면부의 경도가 증가,
3) 워터 피닝의 적용
쇼트 볼 회수, 분진, 노치부 가공의 어려움, 예리한 모서리부 가공 시 균열 발생 등과 같은 숏 피닝의 문제점을 해결하고자 워터 피닝을 적용하는 데 항공기 엔진 가공이 대표적인 사례임.
(3) 인장 성형법
인장 성형법은 프레스 굽힘 가공에서 스프링 백을 제거하거나 줄이기 위해 굽힘 가공 중에 소재를 항복응력 이상까지 인장하고 압축을 하면서 성형하는 방법임.
소재의 양단을 조에 물리고 펀치로 가압하거나 고정된 펀치로 소재의 양단을 인장하여 가공함.
조에 물리는 부위는 재료 손실이 있으나 항공기 몸체, 지붕 판넬 등의 성형에 사용됨.
일반적으로 펀치와 소재의 마찰에 의해 일부분에 변형률이 집중되어 파단되는 경우가 있으며 이를 방지하기 위해 소재와 펀치 사이에 윤활을 좋게 하고 펀치의 코너 반지름을 크게 해야 함.
(4) 플라스마 용사 성형법
플라스마 용사 성형법은 이온화된 플라스마를 금속 분말과 함께 소재가 제품의 원형에서 필요한 크기와 두께가 될 때까지 반복 분사하여 성형한 후 제품을 원형으로부터 분리시켜 제품을 완성하는 방법임.
일반 금속재의 경우에는 경제적이지 못하지만 텅스텐과 같은 고용융점 재료의 성형에는 적합함.
(5) 레이저 빔 용접에 의한 성형법
모양과 크기, 두께가 다른 판재 조각을 블랭킹 등으로 가공한 후 레이저 빔 용접을 통해 일정 형상으로 붙이고 용접된 판재를 성형하여 제품을 완성하는 방법임.
양복을 재단하는 것과 유사하다고 하여 테일러드 블랭킹이라고 하며 판재 조각의 용접 강도가 매우 높음.
판재 조각을 이용하기 때문에 제품 설계의 유연성이 높고 부분적인 강도 조절이 가능하여 자동차 부품 제작에 많이 사용됨.
(6) 숏 피닝
1) 개요
숏 피닝은 경화된 작은 쇠구슬인 쇼트 볼을 피가공물에 고압으로 분사시켜 표면의 강도를 증가시킴으로써 기계적 성능을 향상시키는 가공법.
숏 피닝의 효과를 최대로 올리기 위해서는 압축 잔류응력을 극 표면으로 끌어내야 하는데 이것을 좌우하는 인자가 쇼트 볼임.
숏 피닝의 강도 조절 변수로는 쇼트 볼의 투사 속도, 크기, 경도, 형상, 단위 시간당 투사량 그리고 투사각도 등이 있음.
2) 숏 피닝 효과의 영향 인자
(가) 쇼트 볼의 크기
쇼트 볼의 다른 인자들이 일정하면 쇼트 볼의 크기가 커짐에 따라 아크 하이트는 커지고 적용 범위는 감소함.
작은 쇼트 볼은 적용 범위에 빨리 도달할 수 있는 이점이 있기 때문에 최소 쇼트 볼의 크기를 선택하여 요구되는 아크 하이트를 얻을 수 있어야 함.
(나) 공작물의 경도
공작물보다 쇼트 볼의 경도가 높으면 아크 하이트에는 영향이 없고 공작물보다 쇼트 볼의 경도가 낮으면 아크 하이트가 낮아짐.
(다) 쇼트 볼의 투사속도
쇼트 볼에 의해 행해지는 최대 일량은 운동 에너지를 초과할 수 없음.
높은 운동 에너지를 얻기 위해 쇼트 볼의 질량을 증가시키면 공작물의 표면 조도가 커지며 기계 작동 상의 문제가 발생할 수도 있음.
따라서 쇼트 볼의 투사속도를 증가시켜 높은 운동 에너지를 얻는 것이 현명한 방법임.
지나치게 쇼트 볼의 투사속도를 증가시키면 아크 하이트는 커지는 반면에 쇼트 볼의 파손율은 높아지고 표면 조도도 커지게 되므로 적절한 쇼트 볼 크기와 투사속도의 선정이 중요함.
(라) 쇼트 볼의 투사각도
쇼트 볼은 투사체가 날아와서 피가공물의 표면에 충격 에너지를 전달하여 압축 잔류응력이 소재의 수직방향으로 발생하게 되므로 입사각도가 0˚에 가까울수록 숏 피닝의 강도가 증가함.
충돌각이 증가하면 충격 에너지가 충돌각만큼 감소하기 때문에 되도록이면 충돌각을 작게 해야 재료 표면에 많은 충격 에너지를 공급할 수 있음.
(7) 핀 포밍
1) 개요
핀 포밍은 항공기 날개 판재의 곡면 부분을 가공하는 데 이용된 이후로 적용 범위가 확대되고 있고 형상을 만드는데 비용을 절약할 수 있으며 손쉽게 테이퍼나 만곡면을 만들어 낼 수 있고 무게에 비해 최대 강도를 증가시킬 수 있으며 재료의 불필요한 손실을 줄일 수 있음.
핀 포밍으로 숏 피닝을 하면 만곡이 일어나는데 이러한 성질을 이용하여 프레스 금형을 사용하지 않고 굽힘 가공이 가능하도록 한 가공법을 말함.
2) 핀 포밍의 원리
쇼트 볼의 충격에 의해 재료 내부에는 소성변형 영역이 발생되는데 투사 에너지의 양에 따라 재료에 전이되는 양이 결정됨.
쇼트 볼의 투사 에너지는 정확한 위치에 정확하게 피닝 강도를 부여해야 하며 가공 재료는 에너지를 흡수하여 소성변형이 될 수 있는 판재여야 함.
쇼트 볼의 투사 에너지는 쇼트 볼의 투사속도와 직경, 판재의 강성에 의존하며 판재는 투사 에너지가 낮을 경우 위로 볼록하게 변형이 이루어지지만 그 반대일 경우에는 아래로 볼록하게 변형함.
이러한 원리를 이용하여 숏 피닝 투사 에너지의 강약에 의한 변형량을 적절히 조절하면 원하는 곡면 형상을 만들 수 있음.
숏 피닝으로 가공한 면의 표층에 똑같이 반복해서숏 피닝을 시행하면 원래의 형상에 가깝게 환원되기 때문에 부분적인 적용을 통해 더욱 복잡한 면의 성형도 가능함.
3) 쇼트 볼의 투사 방식
(가) 중력 낙하식
중력 낙하식은 항공기의 큰 동체 날개를 제작할 때 사용되며 직경이 큰 쇼트 볼을 사용하여 두께 20mm 이상의 날개 표면을 가공함.
쇼트 볼의 투사속도는 저속으로 하여 가공면의 표면 거칠기를 좋게 하고 쇼트 볼의 투사각을 적절히 유지하며 중력 가속도에 의한 낙하 높이를 조절하여 원하는 가공 표면을 얻어야 함.
(나) 공기 노즐식
공기 노즐식은 크기가 작은 노즐 가공이나 매우 소량을 생산하는 경우에 적용되며 쇼트 볼이 커지면 속도의 조절이 어렵고 투사 에너지의 효율이 떨어지며 노즐의 직경도 커지게 되므로 적절한 크기의 쇼트 볼을 선정해야 함.
(다) 원심력 휠식
원심력 휠식은 쇼트 볼의 크기가 큰 것을 투사하는데 가장 적합한 방식이지만 쇼트 볼의 재질이나 크기에 관계없이 투사할 수 있음.
쇼트 볼의 투사속도를 매우 정확하고 재현성 있게 조절할 수 있으므로 CNC 숏 피닝기를 적용하는데 유용한 방식임.
CNC 숏피닝기는 쇼트 볼의 공급량을 조정하고 파쇄 및 마모된 쇼트 볼을 자동으로 분리할 수 있으며 임펠러 제어를 통해 공작물의 재질에 따라 투사속도를 제어할 수 있음.
(8) 워터 제트 가공
1) 개요
워터 제트 가공법은 물줄기를 고속으로 분출시켜 물체와 충돌시키면 물줄기의 운동량의 변화로 물체에 힘을 가하게 되는데 작은 노즐 구멍을 통해 초고압으로 분출시킨 물의 침식으로 소재를 가공함.
각종 기판, 복합 재료, 플라스틱, 작물, 나무, 종이, 가죽 등 비금속 재료의 절단에 우수한 성능을 발휘함.
2) 워터제트의 구성
(가) 고압증강 장치 및 펌핑 유닛
증압기는 물을 고압으로 만들어 주는 장치로써 왕복동형 플런저 펌프가 주로 사용되며 증압된 물은 축압기로 보내지는데 축압기는 물이 노즐에서 분출되기 전에 저장되는 곳으로 압력이 일정하게 유지되어야 함.
(나) 노즐
제트를 형성하는 곳으로 노즐의 직경은 0.05 ~ 0.5mm 정도이고 분출되는 물의 속도는 600 ~ 900m/sec이며 공작물과의 간격은 약 3 ~ 25mm임.
노즐의 구멍부는 사파이어를 주로 사용하나 최근에는 다이아몬드를 사용하기도 함.
3) 특징
예비 구멍이 불필요하고 버의 열적 손상이 거의 없음.
공작물 상에서 절삭력이 작아 취성 재료도 가공이 가능함.
공작물의 변형이 적어 유연한 재료의 절단에 용이함.
환경친화적이고 NC 회로 자유 곡선도 쉽게 가공할 수 있음.
소음이 크고 절단할 수 있는 두께에 제한이 있음.
(9) 입자 제트 가공
1) 가공 원리 및 특징
입자 제트 가공은 워터 제트 또는 비활성 가스의 흐름에 10 ~ 50μm의 연삭입자를 노즐부에서 같이 분출하여 공작물과의 기계적 충격력을 이용하는 가공법임.
금속도 충분히 절단할 수 있으며 열 발생이 없어서 열에 민감한 재료의 절단에 적합함.
2) 적용 분야
취성 재료의 가공.
미소 입자 블라스팅에 사용.
7. 컬링 금형
(1) 개요
특수 가공 및 금형 중 컬링은 판재 또는 용기의 윗부분에 원형 단면의 테두리를 말아 넣는 가공이며 플랜징과 같은 목적으로 사용됨.
플랜지 부분을 둥글게 가공하는 것으로서 컬링 속에 철사나 봉재를 넣고 겉면을 둥글게 하는 것을 와이어링이라 함.
컬링은 경첩과 같은 판형 제품의 컬링 가공과 드로잉 된 원통형 용기의 가장자리에 테두리를 만드는 컬링 가공 2가지로 나뉨.
컬링을 하는 목적은 강도를 높이고 끝부분의 예리함을 없애주기 위함임.
(2) 가공 종류
1) 판형 제품의 컬링 가공
컬링 가공은 일반적으로 컬링 할 부분을 일정한 곡률로 약간 굽혀주는 제1공정과 원형의 형상으로 완전히 마는 제2공정으로 구분.
제1공정은 펀치의 한쪽 날을 제1공정의 형상으로 하여 재료가 눌려 굽혀지면서 블랭킹 작업과 동시에 진행됨.
미리 전단된 제품을 굽힘 가공별로 하여 제2공정을 마무리함.
2) 원통 용기의 컬링 가공
원통 용기의 컬링 가공은 판형 제품과 같이 2단계의 공정을 가지지 않고 1공정에 가공을 완료함.
원통 용기의 컬링 부위는 가공면이 균일해야 하며 불균일할 때는 트리밍 가공을 해야 함.
(3) 컬링 금형의 종류
1) 판형 컬링 금형
판형 컬링 금형은 컬링한 부분이 위로 가도록 재료를 다이에 세워서 가공하는 방식과 다이에 컬링 홈을 만들어 재료를 밀어 넣고 위에서 펀치로 가압하는 방식으로 구분됨.
펀치에서 컬링 부분이 굽혀질 경우 둥글게 말리는 부분은 펀치의 상승 시 펀치에 끼어 위로 올라가 다이에서 빠져나오게 됨.
이후 제품은 손이나 녹아웃 장치에 의해 펀치에서 취출됨.
다이에 부시를 설치한 컬링 금형인 경우 제1공정에서 굽혀지는 부분이 다이 속으로 들어가면 펀치의 압력에 의해 부시 구멍의 원추를 따라 둥글게 말림.
다이 속에서 컬링 가공된 제품은 다이에 꽉 차기 때문에 펀치의 상승 시 작동되는 기계적 도그래그 캠과 슬라이드 장치를 이용함.
2) 원통 용기의 컬링 금형
원통 용기의 컬링 금형은 내 컬링과 외 컬링으로 구분됨.
컬링 홈은 펀치에 설치되어 있고 다이는 제품의 외형에 똑같은 형상으로 가공함.
다이의 길이는 제품의 컬링 깊이를 뺀 값보다 약간 작아야 하며 제품의 밑바닥 라운드 부분이 꼭 맞게 다이가 제작되어야 함.
펀치의 컬링 홈은 말리는 내측 부분을 더 길게 하고 약 30˚ 정도 경사지게 하여 소재의 안내를 원활하게 함.
가공할 소재의 용기가 깊은 경우에는 녹아웃 장치를 설치하여 제품을 취출함.
8. 버링
(1) 개요
특수 가공 및 금형 중 버링은 평판에 기초 구멍을 뚫고 그것으로부터 직경이 큰 펀치로 훑어 내려서 원통 벽을 세우는 공정으로서 홈 플랜징이라고도 함.
버링 된 플랜지의 내면에 성형용 탭을 이용하여 암나사를 가공하거나 두께 이상의 판을 리벳 없이 결합할 때 이용함.
보통의 버링 가공에서는 수직벽의 판 두께가 15 ~ 20%이고 1회 가공으로 달성할 수 있는 플랜지 높이의 한계는 대체로 구멍 지름의 10% 정도임.
(2) 버링의 가공 변수
1) 펀치 선단의 형상
펀치 선단의 형상이 원추형으로 예리할수록 성형성은 증가하나 성형 스트로크가 길어지게 됨에 따라 생상성이 저하됨.
2) 구멍의 전단면 상태
구멍의 전단면 상태가 불량하면 균열이 생겨 성형을 저하시킴.
피어싱한 구멍의 전단면을 드릴링 등을 통해 다듬질하게 되면 상대적으로 플랜징의 높이가 높은 버링 가공이 가능함.
3) 재료의 성질
연성이 높은 재질은 변형 저항이 작게 되어 버링의 가공성을 향상시킴.
알루미늄은 보통 강판에 비해 버링 가공의 한계(펀치의 직경 / 초기 구멍의 직경)가 약 40% 향상됨.
4) 다이의 코너 반지름
가능한 한 다이의 코너 반지름을 크게 해야 버링 된 수직벽의 높이를 높일 수 있음.
(3) 버링 가공의 종류
1) 일반 버링
태핑용 버링 가공을 할 때에는 탭의 치수를 먼저 결정한 다음 버링 치수를 결정하고 마지막으로 피어싱 치수를 결정함.
드로잉 가공과 같이 블랭크 홀더를 부착하여 피어싱된 소재를 누르면서 가공하는 것이 일반적임.
드로잉 제품의 밑바닥을 펀칭하고 버링으로 제품의 높이를 증가시키는 방법도 있는데 이를 드로 버링이라함.
2) 돌파 버링
구멍 뚫기와 버링을 동시에 가공하는 것으로서 구멍을 가공한 후 확대·성형한 것임.
작은 구멍의 버링에 많이 사용하고 펀치의 선단 각도는 소재 두께에 영향을 받으나 대략 55 ~ 60˚ 정도로 함.
펀치의 선단 형상을 3각, 4각, 5각으로 하여 초기의 구멍을 내지 않은 상태로 1회 가공으로 돌파하면서 버링 가공을 하는 경우도 있으나 이 경우 플랜지의 윗부분에 균열이 생김.
3) 스트레치 버링
Φ12mm 이하의 비교적 작은 구멍은 피어싱과 버링을 동시에 할 수 있는 스트레치 버링 공정을 취함.
펀치에 단을 주어 1공정에서 1개의 펀치로 피어싱과 버링 가공을 시행함.
4) 아이오닝 버링
일반적으로 버링 가공에서 버링 된 측벽의 판 두께 감소가 15 ~ 30%이나 판 두께의 감소를 일반 버링의 2배 정도로 크게 하여 수직벽의 높이를 증가시키는 버링 가공법.
9. 스웨이징
(1) 개요
특수 가공 및 금형 중 스웨이징은 중공축, 중실축 및 강선 등의 소재를 2개 또는 그 이상의 분리형 금형에 삽입한 후 소재의 반지름 방향으로 점진적인 반복하중을 가하여 소재의 단면을 변화시키는 점진 성형 공정으로 기계 가공을 필요로 하지 않음.
로터리 스웨이징은 봉이나 원통형 관 모양의 재료를 축 주위로 회전시키면서 공구를 이용하여 재료를 한 부분씩 축과 직각방향으로 짓눌러 경사지게 하거나 지름을 줄여서 길이를 늘이는 점진 성형 공정으로 자동차 중공축 등의 생산에 활용됨.
(2) 스웨이징 공정
1) 로터리 스웨이징
로터리 스웨이징은 스웨이징 또는 경방향 단조라고도 하며 왕복운동하는 금형으로 봉재나 관재의 반지름 방향으로 타격하여 작업을 진행함.
금형의 움직임은 롤러 베어링처럼 틀 속에 들어 있는 롤러에 의해 이루어지며 소재는 움직이지 않고 금형 세트가 회전하면서 초당 20회 정도의 고속으로 소재에 타격을 가하여 주로 축 대칭 원형 제품을 생산하지만 외륜 회전형인 경우에는 육각형, 팔각형, 타원형, 십자형 같은 비원형 제품도 생산할 수 있음.
2) 금형 밀폐형 스웨이징
금형 밀폐형 스웨이징은 금형의 운동이 왕복하는 쐐기의 운동으로부터 얻어지는데 로터리 스웨이징에 비해 금형이 넓게 벌어지므로 지름이 크거나 고르지 않은 제품도 생산할 수 있음.
또 다른 유형으로는 금형이 회전하지 않고 반지름 방향으로 왕복운동만 하는 것도 있음.
금형 밀폐형 스웨이징은 2개의 롤러가 트러스트 피스 양단에 위치할 때 다이는 최대한 개폐가 되며 이러한 방법은 트러스트 피스나 다이스의 관리나 교체 시 유리한 구조를 가짐.
해머의 스트로크만큼 서로 마주 보고 있는 금형은 축 중심을 향하여 반지름 방향으로 타격을 유발하게 되며 반복적인 충격에 의해 금형 속의 소재는 점진적으로 금형 형상으로 성형이 이루어짐.
맨드렐을 사용하면 내부에 형상이 있는 튜브 제품도 성형할 수 있음.
(3) 특징
치수 정밀도가 우수한 고정도의 제품의 대량생산에 유용함.
설비비가 저렴하고 구조가 간단하며 비숙련자도 작업이 용이함.
강과 비철금속 등 여러 가지 재질을 이용하여 열간, 냉간 성형이 가능함.
금속 섬유 조직이 연속적으로 형성되어 기계적 성질을 향상시킴.
절삭가공에 비해 경면에 가까운 표면 정밀도를 얻을 수 있음.
칩 발생이 없고 재료비가 40% 이상 절감됨.
다른 점진 성형 공정보다 높은 소음과 진동이 발생함.
(4) 성형 가공 형상
축 대칭 성형 소재의 중앙부 단면을 감소시키는 성형.
봉재 성형, 튜브 성형, 내•외부 성형.
테이퍼 성형, 튜브의 끝단 오므리기 성형.
10. 하이드로 포밍
(1) 개요
특수 가공 및 금형 중 하이드로 포밍은 금형 속에 들어가 있는 강관 속에 물 등의 액체를 주입하여 내부에부터 강한 액압을 가하여 복잡한 형상으로 일체 성형하는 공법.
하이드로 포밍은 관의 중간 부분을 확관 가공하는 가공법과 굽혀진 강관의 일부를 확관하는 가공법으로 나뉨.
하이드로 포밍의 가장 큰 특징은 한 개의 파이프로 요철이 있거나 휘어진 복잡한 형태의 제품을 단 한번에 만들어 낼 수 있음.
(2) 종류와 특징
1) 관재 하이드로 포밍
관재 하이드로 포밍 제품은 전 세계 자동차 회사에서 가장 많이 사용하고 있는 추세이며 그 적용 부품 역시 점차 확대되고 있음.
관재 하이드로 포밍 제품은 경량화 뿐만 아니라 부품수를 감소시켜 조립 공정을 단순화할 수 있으며 조립 정도를 향상시킬 수 있는 효과가 있음.
하지만 생산 설계 기술이 요구되고 초기 투자비가 많이 든다는 것이 단점임.
2) 판재 하이드로 포밍
관재 하이드로 포밍에 비해 판재를 이용한 하이드로 포밍은 생산성 및 투자비 때문에 적용 범위가 크게 늘어나지 않고 있음.
판재 하이드로 포밍은 펀치만으로 제품을 성형하는 기술로 고무를 이용한 마폼법에서 고무 대신에 액체를 이용한 것이 유사함.
기존 프레스 금형을 이용한 성형에서 다이측을 액압 탱크로 구성하여 액압을 이용하여 펀치 형상대로 제품을 가공하는 방법임.
따라서 금형비가 프레스 금형보다 적게 소요되어 다품종 소량생산에 유리하고 제작 기간을 단축시킬 수 있음.
관재 하이드로 포밍과 마찬가지로 판재 하이드로 포밍도 경량화의 효과를 높일 수 있는 장점을 가짐.
(3) 생산설비
하이드로 포밍은 금형에 의존하기보다는 재료 특성에 따른 압력을 제어하는 기술에 더 의존하는 가공법임.
따라서 하이드로 포밍의 성공 여부는 외부로부터 압력 부하나 힘을 가하는 타이밍, 크기, 속도 등을 어떻게 제어하는가에 달려있음.
하이드로 포밍 프레스는 단독 고압 프레스 장비에 자동화 장비를 설치하여 라인 개념으로 구성하는 게 일반적임.
기존 하이드로 포밍 장비와 달리 프레스가 모듈화되어 있으며 성형 시 고압으로 금형을 지지하는 것이 아니라 프레스 구조물을 기계적으로 고정시킴으로서 고압에 대한 반발력을 유지할 수 있기 때문에 라인 개념으로 구성할 수 있음.
11. 고무 성형
(1) 개요
고무 성형은 압축 성형법이 일반적으로 널리 이용되고 있음.
고무 생지로 고무 제품을 성형할 때에는 일반적으로 혼합, 성형, 가황, 다듬질 등의 공정을 거쳐 성형함.
성형가공을 용이하게 하기 위해 가역화한 고무에 가황제, 촉진제, 노화 방지제 등의 배합제를 혼합함.
하지만 플래시 발생, 스프루-러너의 가류화에 따른 손실, 제품 취출 후 폐기되는 스크랩으로 인한 환경 문제 발생, 후공정에 따른 품질 저하 및 원가 상승, 자동화를 수행할 수 없는 금형 구조로 인해 대량생산에서 나타는 취약점 등이 대두되고 있음.
(2) 고무 성형 금형의 고려 사항
1) 형체 기구
고무 성형은 금형의 작은 틈새가 있으면 플래시가 발생함.
이것을 방지하기 위해 금형 설계, 제작상에서의 열적 요인을 충분히 고려해야 하며 형체 장치로 휨을 억제할 수 있는 고강성의 플레이트와 가공정도, 열변형 대책이 중요함.
성형품의 투영면적보다 형체결력이 작으면 사출압력에 의해 고정측 형판과 가동측 형판 사이가 벌어져 플래시가 발생함.
2) 가스제거(범핑)
사출 성형에서는 고압 형체로 닫힌 금형 내에 고무 생지를 충전하는데 캐비티 내의 공기나 가류반응에 의한 가스를 빼내는 동작이 필요하게 되어 충전 완료 후에 타이밍을 가늠하여 형체압력을 내리거나 금형을 조금 열어 공기나 가스를 배출하고 다시 형체 하는 동작으로 성형 불량을 피해야 함.
3) 진공장치
금형 캐비티 내의 공기나 가류반응에 의한 가스를 진공펌프로 흡인하는 방법으로서 금형에 설치된 가스 빼기 홈을 이용하여 흡인하거나 파팅 라인에 오링실 등을 설치하여 형체 일시정지 시 흡인 후 사출하는 과정을 수행함.
4) 플래시 제거
일반적으로 고무 금형에서 완벽한 플래시 처리가 불가능한 것으로 보이지만 플래시를 깨끗이 처리하기 위해서는 고무 재료의 흐름성이나 사상성과 기계의 정확한 정도가 중요함.
금형의 각 형판들의 정밀 평판 연삭을 통한 두께 평행도를 정확하게 가공하고 여러 판을 조립한 후에도 정확한 평행도를 유지해야 함.
형체결력과 캐비티 개수 등의 선정이 균일한 압력을 유지하기 위하여 금형에 가하는 압력 지점을 다르게 하고 압력을 집중시켜 접합부를 정밀 밀착시키는 금형 제작 기술을 확보함으로서 플래시 발생을 방지할 수 있음.
(3) 고무 성형의 종류
1) 압축성형
압축성형은 고무 성형의 기본적인 방법으로서 열경화성 플라스틱의 대표적인 성형법임.
계량한 원료를 가열한 금형의 캐비티에 넣어 가압하여 경화시켜 성형하는 방법으로서 원료는 캐비티 내에서 가열되어 경화하므로 적당한 경화시간 후 금형을 열고 성형품을 취출함.
캐비티 내의 공기를 빼고 원류를 흘려 충전을 좋게 하기 위해 진공 흡인을 하거나 가열•화학반응으로 발생한 가스를 빼는 조작을 등을 수행해야 함.
압축성형은 설비비가 저렴하고 어떠한 성형 재료도 성형 가능하며 성형품 배향이 적고 재료 손실이 적은 장점이 있음.
고무 제품의 다품종 소량생산에 넓게 사용되고 있음.
2) 사출성형
플라스틱 사출성형과 매우 유사한 방법으로서 고무 생지는 스크루로 연속 공급하고 소정량을 연화•용융시켜가며 계량하는 스크루로 금형에 고압•충전하고 가류하는 성형법임.
다른 성형법보다 성형 사이클이 빠르고 균일한 가류 제품을 얻을 수 있어 대량생산에 적합함.
3) 이송성형
사출성형의 간이 방법으로서 고무 생지를 가열부에서 가열하여 가압부로 이송한 후 플랜저로 가열된 금형에 주입하여 가류를 하는 성형법임.
이송성형에서 성형압력이 가장 중요한 요인이며 성형압력이 낮으면 충전을 완료하기가 어렵고 반대로 너무 높으면 플래시가 발생할 뿐만 아니라 캐비티 내의 각종 핀 이나 코어류 및 삽입물 등에 과대한 힘이 작용하여 변형되거나 그 위치를 어긋나게 하여 이송성형의 본래의 이점을 잃게 됨.
이송성형에서는 포트부의 구조상 재료의 흐름에 대한 저항이 크기 때문에 보조 램식 이송성형의 경우에 비해서 10 ~ 20% 높은 성형압력이 필요함.
특수 가공 및 금형 연재를 끝으로 소성가공에 대한 연재을 마치고 다음에는 금형 제작 및 측정에 대한 연재를 시작할 예정입니다.
2020년 09월 06일
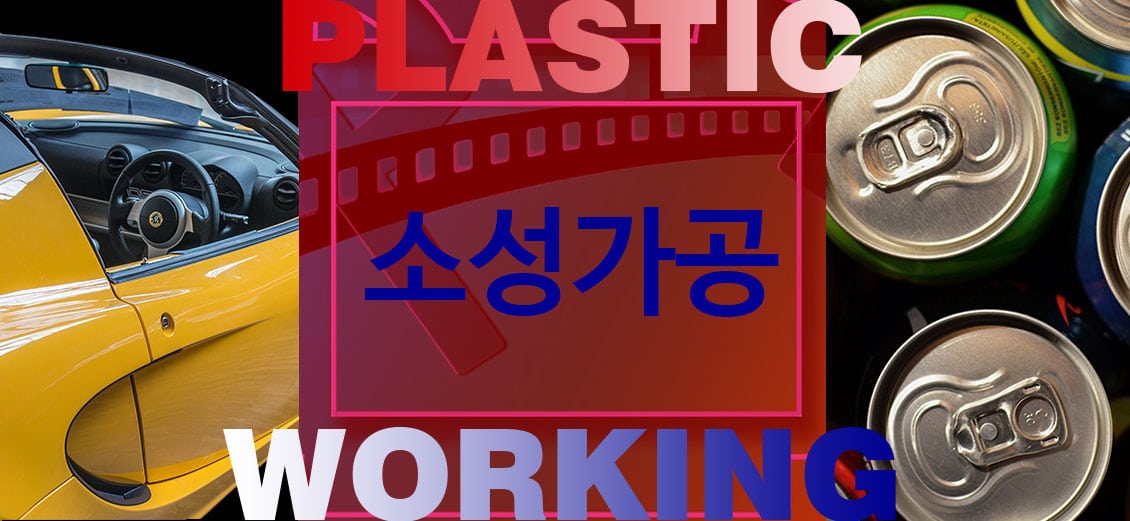
소성가공 4
제4장 특수 가공 및 금형
소성 가공 중에서 특수 가공 및 금형(PLASTIC WORKING)에 대표적인 것으로는 다이나 롤러를 이용하여 소재를 공구의 표면 형상으로 각인하는 전조와 금속 분말을 금형에서 압축한 후 가열•소결 하여 제품을 가공하는 분말야금이 있습니다.
1. 전조
(1) 개요
특수 가공 및 금형 중 전조는 다이나 롤러와 같은 성형 공구를 회전 또는 직선운동시키면서 그 사이에 소재를 넣어 공구의 표면 형상으로 각인하는 일종의 특수 압연을 말함.
전조로 가공되는 제품으로는 기어, 나사, 볼, 링, 스플라인 축 등이며 전조기에는 제품에 따라 특수한 장치를 갖춘 전용기가 있음.
(2) 특징
소재의 섬유조직이 전단되지 않으므로 제품의 강도가 큼.
소재와 공구의 국부적인 접촉으로 인한 작은 가공력만 가지고도 가공이 가능함.
칩이 생성되지 않으므로 소재의 이용률이 높음.
소성변형으로 인한 가공경화 및 치밀한 조직이 형성됨.
가공속도가 빠르고 자동화가 쉬움.
(3) 전조 가공의 종류
1) 나사 전조
(가) 평 다이 전조
평 다이 전조는 한 쌍의 평 다이 중 하나는 고정, 다른 하나는 직선운동을 시켜 1회의 행정으로 나사를 성형하는 방법.
평 다이 전조의 소재는 대부분 연성재료가 사용되며 다이에는 성형부와 다듬질부가 있음.
둥근형 다이 전조에 비해 제품의 정밀도가 떨어짐.
(나) 둥근형 다이 전조
둥근형 다이 전조는 고정축 다이와 가동축 다이로 되어 있으며 두 축은 평행하고 재료는 지지대에 의해 지지됨.
둥근형 다이 전조는 가동축은 축이 이동되며 롤러 다이를 3개 사용하는 경우가 있음.
평 다이 전조에 비해 생산속도가 매우 빠르고 정밀한 나사를 제작할 수 있음.
(다) 프래너터리 전조(PLANETARY 전조)
프래너터리 전조는 고정 원호 다이를 고정시키고 원형 다이를 회전시켜 자동으로 장입 소재가 타단에서 완성된 나사로 나오며 물림률이 크고 대량생산에 적합함.
프래너터리 전조는 크랭크 운동에 의한 평 다이 전조에서는 가공을 하지 않는 귀환행정이 있으나 플래너터리 전조에서는 공전이 없으므로 가공 능률이 높음.
2) 기어 전조
(가) 래크 다이 전조
래크 다이 전조는 한 쌍의 래크 다이 사이에 소재를 넣고 압력을 가하면서 래크를 이동시켜 소재의 치형을 성형함.
이 방법은 지름이 큰 기어에 대해서는 래크가 커야 하고 설치 공간도 넓어야 되기 때문에 지름이 작은 기어 제작에 적합함.
기어 전조법은 보통 냉간가공을 하고 있으나 모듈이 약 3 이상인 경우나 굵은 재료의 경우에는 열간가공으로 함.
(나) 피니언 다이 전조
피니언 다이 전조는 피니언 다이와 소재의 맞물림을 동일하게 하여 압력을 가하면서 회전시켜 치형을 성형하며 공구의 작동이 용이함.
피니언 다이 전조는 지름이 큰 기어, 웜, 스플라인 성형가공에 많이 적용됨.
(다) 호브 다이 전조
호브 다이 전조는 전조 공구를 상하에 두고 소재를 회전시키면서 축 방향으로 보내어 성형함.
소재는 인덱스 헤드에 의하여 소정의 각도만큼 회전시켜 다이 사이에 삽입됨.
소재의 유동이 좋고 롤러에 무리한 힘이 작용되지 않음.
3) 볼 전조
볼 전조는 2개의 다이가 롤러 축과 교차되어 있어 소재의 성형과 이송을 동시에 행함.
다이의 홈은 볼을 성형하는 가공면이고 산은 소재를 오목 패이게 가공하면서 최후에는 절단하는 역할을 함.
볼 전조는 500 ~ 1,000℃의 열간가공에서 행해짐.
4) 드릴 전조
드릴 전조는 소재가 길이 방향으로 연신 되면서 홈이 성형됨.
공구는 홈 가공용과 릴리프면 가공용이 따로 있음.
2. 반용융 금속을 이용한 성형법(SEMI-SOLIDE FORMING PROCESS)
(1) 반용융 압연
1) 성형 방법 및 특징
특수 가공 및 금형 중 반용융 압연이란 반용융 금속으로부터 열연강판 및 냉연강판을 제조하는 것으로 롤러 사이에 주입하는 금속의 주입온도를 낮춤으로써 롤러에 발생하는 열응력과 열피로 현상을 감소시켜 롤러의 수명을 연장시킬 수 있음.
롤러 내에서 응고하기 시작한 재료의 응고 완료점의 위치에 따라 판재 성형성이 결정되기 때문에 롤러의 온도 및 속도 변화에 따른 응고 제어가 매우 중요함.
2) 기술적인 요점
(가) 공정변수의 확립을 통한 자동화
고상률, 롤러 회전수, 롤러 간격, 탕면 높이, 재료의 주입방법, 롤러 냉각방법 등과 같은 공정변수들 사이의 관계가 정량적으로 규명되어야 하며 공정변수를 변화시켜 응고속도를 일정하게 유지되도록 제어해야 함.
(나) 롤러 냉각 방식에 따른 냉각 특성 파악
냉각 특성에 따른 롤러 재질 선정, 롤러 형상 설계, 냉각수 주입량을 결정하여 롤러에 작용하는 열응력 및 열피로를 줄임.
(다) 분산장치 및 노즐 형상의 결정
반용융 금속을 롤러 폭 방향으로 균일하게 분산시키기 위한 분산장치 및 노즐의 형상이 결정되어야 함.
(2) 반용융 단조
1) 성형 방법 및 특징
반용융 단조는 금속의 온도를 제어하면서 교반을 행하는 교반부, 밀폐형 다이 내로 주입하기 위한 주입부, 그리고 밀폐형 다이와 다이 내에 충전된 반용융 금속을 가압하는 가압부로 구성됨.
반용융 단조는 단조 하중이 작고 가공속도가 빠르며 편석, 기공 등과 같은 결함이 없는 주조와 단조 공정이 결합된 복합 공정임.
2) 기술적인 요점
(가) 성형 가능한 고상률 범위와 금형온도
반용융상과 고상의 경계를 시간에 따라 추정하여 완전히 응고가 되는 시간을 예측하고 시간의 변화에 따라 응고 측정과 다이의 온도 분포를 파악하여 금형의 예열온도를 예측해야 함.
(나) 최적 단조 조건 확인
단조압력, 단조속도, 단조시간 등이 정량적으로 확립되어야 하며 이들 인자의 변화에 따른 재료의 흐름 특성과 재료의 이방성이 파악되어야 함.
또한 공구의 최적 윤활제 선정, 금형온도가 품질에 미치는 영향 등이 검토되어야 함.
(3) 반용융 압출
1) 성형 방법 및 특징
반용융 압출은 기존의 빌렛 대신 반용융 금속을 호퍼를 통해 컨테이너 내에 공급하고 스템의 가압과 동시에 다이를 통하여 원하는 부품을 성형함.
2) 기술적인 요점
(가) 컨테이너 및 금형의 온도 제어
반용융 금속의 고상률의 제어 때문에 컨테이너에서의 온도 제어가 중요하며 결정립의 균일한 분포를 위해 다이의 온도 제어가 특히 중요함.
(나) 금속 복합재료의 압축 기술
강화제의 파단을 방지하기 위한 다이의 설계, 기지 내의 소성유동과 강화제의 배향 사이의 관계가 정립되어야 함.
(4) 반용융 다이캐스팅
1) 성형 방법 및 특징
(가) 성형 방법
용융 금속을 전자 교반하면서 연속 주조를 통해 수지상 결정을 분단하여 균일한 조직의 빌렛을 만든 후 다이캐스팅 1 SHOT에 해당하는 양만큼 자름.
로터리식 유도가열 장치에 의해 약 590℃까지 가열하여 고상률 50 ~ 60%의 반용융 상태로 만들고 반용융 빌렛을 로봇을 이용하여 사출 슬리브에 삽입한 후 플런저로 금형의 캐비티 내로 사출 충전함.
반용융 다이캐스팅 제품은 수축이 적고 편석이 적어 기계적 강도가 안정되며 내기밀성이 우수함.
(나) 특징
① 제조상의 특징
– 점성 충전이므로 탕 끝에서 공기 권입이 없음.
– 이미 반은 응고된 상태이므로 수축 캐비티가 적음.
– 저온 주입으로 형 수명이 길고 에너지가 절감됨.
– 유지로가 필요 없음.
– 주조 핀이 거의 발생하지 않음.
– 응고 수축이 작으므로 이형하기도 쉽고 치수 정밀도가 좋아 정형가공이 용이함.
– 복합재료의 제조가 용이함.
– 작업환경이 양호함.
② 제품의 특징
– 블로 홀이 매우 적음.
– 편석이 적음.
– 파단질층이 적음.
– 표면에서 내부까지 균일한 입상조직을 취함.
– 기밀성이 양호함.
– 연성, 인성이 현저하게 큼.
2) 기술적인 요점
(가) 반용융 다이캐스팅 빌렛
수지상의 결정이 파괴•분단된 조직의 빌렛을 저렴하게 제조할 수 있어야 하는데 빌렛의 가격이 높아 반용융 다이캐스팅의 보급이 광범위하게 이루어지지 못하고 있음.
(나) 주조 조건
초기에 플런저의 전진속도는 고속이지만 금형의 캐비티에 용융 금속을 충전 할 경우에는 저속이므로 사출속도를 임의로 설정할 수 있는 고출력의 사출기구를 가진 다이캐스트 머신이 필요함.
(다) 금형 설계
반용융 금속은 고점성 충전이므로 유동저항의 경감 및 충류 충전을 위해 탕구를 두껍게 하고 인발 코어 등을 추가하며 가스 빼기를 충분하게 설치하고 가공여유를 많이 주는 것이 좋음.
금형은 예열 장치 및 온도조절 장치가 있어야 함.
3. 신기술 단조 방법
(1) 개요
단조의 가공속도 향상을 통해 생산성을 향상시키거나 작은 하중으로 고품질의 제품을 생산할 뿐만 아니라 다이의 수명을 연장시키기 위한 새로운 단조법이 연구 개발되고 있고 이를 신기술 단조법이라 함.
(2) 신기술 단조 방법의 종류
1) 고에너지 단조
고에너지 단조는 내연기관을 이용하여 수천 분의 일 초만에 순간적으로 단조 가공을 완료하는 기술임.
주로 판재 성형에 응용되며 얇은 단면을 가지는 복잡한 형상의 제품 생산에 적합함.
상용화된 고에너지 단조 기계로는 영국에서 개발한 PETRO FORGE, 미국에서 개발한 DYNAPAK 등이 있음.
2) 반용융 단조
3) 분말 단조
분말 단조는 분말 소재를 소력하여 만든 예비 성형체를 열간 단조하여 제품을 만드는 단조법.
분말 단조는 가공 단계가 단순하고 후처리가 필요 없어 복잡한 형상을 만들 수 있음.
주로 커넥팅 로드, 기어 등과 같이 높은 강도를 요하는 기계부품 생산에 적합함.
4) 등온 단조
등온 단조는 가열 금형 단조라고도 하며 가열된 소재의 온도와 동일하도록 다이를 가열하여 단조하는 방법.
등온 단조는 단조가 진행되는 동안 소재가 냉각되지 않으므로 소재의 유동이 원활하여 작은 힘으로도 제품을 성형할 수 있음.
등온 단조용 다이는 니켈이나 몰리브덴 합금으로 제작됨.
4. 반용융 가공의 특징과 문제점
(1) 개요
특수 가공 및 금형 중 반용융 가공은 용융 상태에서의 금속을 냉각 도중 기계적으로 교반하여 수지 상정을 파괴시킨 다음 압연, 압출, 단조, 용탕 단조 및 다이캐스팅에 의하여 제품을 제조하는 공정으로 주조와 단조 공정이 결합된 복합 공정을 말함.
반용융 가공은 에너지 절약, 응용범위 확대, 공정 단축 등의 측면에서 많은 연구와 관심을 불러일으키고 있음.
(2) 반용융 가공의 특징과 문제점
1) 특징
변형저항이 현저하게 적어 적은 하중으로도 가공률을 증대시킬 수 있고 가공 기계 설비의 소형화가 가능함.
유동성과 성형성이 양호하기 때문에 공정 단축이 가능하고 에너지 절약과 재료의 절감을 이룰 수 있음.
결정립이 미세한 주조 조직을 얻을 수 있고 기계적 성질이 우수한 제품을 만들 수 있음.
이종 재료와의 접합이 용이하여 분산 강화 및 적층 강화형 복합 재료의 제조가 가능하고 성형성이 우수함.
다이캐스팅 및 용탕 단조법에서의 용융 재료보다 온도가 훨씬 낮기 때문에 금형과 공구에 가해지는 열적 부하가 적어 수명을 연장시킬 수 있음.
단조 시 편석이 없는 균질한 제품의 제조, 압력 및 냉각속도의 제어에 의하여 결함과 기공이 없는 성형이 가능함.
2) 문제점
(가) 반용융 금속의 연속적인 제조 기술 개발
기계적 교반법, 전자기적 교반법, 초음파 진동법 등과 결합된 제어 냉각 기술 및 교반 장치 개발이 필요함.
(나) 반용융 금속을 금형에 일정한 양을 주입할 수 있는 이송 기술 개발
제품을 대량으로 제조하기 위하여 반용융 재료를 금형에 일정하게 주입하는 이송 기술 개발이 필요함.
(다) 반용융 금속의 성형 공정 확립
압연, 단조, 압출, 용탕 단조, 다이캐스팅 등에 있어 주입하는 반용융 금속의 고상률, 가압력, 가압속도, 가압시간, 다이 온도 등 최적의 공정 변수를 설정할 수 있어야 함.
5. 분말야금
(1) 개요
특수 가공 및 금형 중 금속 분말을 소요 형상의 금형에서 압축한 후 이것을 금속의 용융점 이하로 가열•소결하여 각종 제품을 가공하는 방법을 분말야금이라 함.
2종의 금속 또는 비금속 재료를 혼합하여 입자 간의 결합 강도를 향상시키고 필요한 성질을 부여하며 용융점이 높은 텅스텐, 몰리브덴 및 초경합금 등 치수 정밀도가 높은 기계부품의 대량생산에 적합함.
(2) 특징
용융점이 높은 금속에 적합함.
잘 융합되지 않는 금속 또는 비금속을 균일하게 섞어서 결합시킬 수 있음.
다공질의 금속 제품을 얻을 수 있음.
자동화로 대량생산이 가능함.
치수 정밀도가 높고 가공면이 평활하여 기계 가공이 불필요함.
(3) 제조 공정
① 분말 제조
– 기계 가공에 의한 방법.(절삭, 분쇄 등)
– 용금의 적하에 의한 방법.
– 분사에 의한 방법.
– 산화 분말을 이용하는 방법.
② 충전 및 성형
– 가압 성형.
– 원심 가압.
– 압출법
– 압연법.
③ 소결
– 1차 소결 및 재 압축.
– 2차 소결.
④ 교정(사이징, 코이닝)
⑤ 후처리
⑥ 제품 완성
(4) 분말의 가압 성형법
1) 1방향 압축방식
가장 간단한 방식으로 6mm 이하의 얇은 제품의 성형에 사용되는데 압축 시 다이와 하부 펀치는 고정되어 있고 상부 펀치의 하강에 의해 압축되며 하부 펀치의 상승으로 인해 성형 제품이 취출됨.
압분체의 상•하부 밀도 차가 커서 극히 얇은 제품을 성형할 경우에 사용함.
2) 2방향 압축방식
비교적 균일한 제품을 얻을 수 있으며 제품 각부의 높이가 다른 경우에는 금형을 분할하여 사용함.
상부 펀치의 하강과 하부 펀치의 상승에 의해 가압함.
3) 부동형 방식
다이를 스프링으로 받치고 상부 펀치로 압축함.
다이의 주동력으로는 유압이나 공기압을 이용하고 조정이 용이하며 균일한 제품을 얻을 수 있어 복잡한 형상의 압분체를 성형하는데 유리함.
4) 강제 인하 방식
다이가 프레스의 하부 슬라이드(램)에 연결되어 가압 중에 하부 펀치는 고정되어 있어도 다이가 하강하면 하부 펀치의 상승효과를 얻을 수 있도록 하여 2방향 압축 성형하는 방식임.
부동형 방식의 개량 다이라고 할 수 있으며 복잡한 형상, 특히 압축 방향의 단면 변화가 많은 압분체 성형에 사용됨.
(5) 분말야금의 응용
가공용 전극의 성형.
소결 베어링 제조.(오일리스 베어링)
내열 부품 제조.
공구 제조.(초경합금, 서멧)
요업 제품 제조.
6. 금속 박판의 특수 성형법
(1) 개요
판재의 특수 성형은 고무나 액체 대신 펀치나 다이를 사용한 성형법이 일반적으로 이용되고 있으나 새로운 형태의 성형법이 연구되어 상용화되고 있으며 이러한 가공법은 특수 용도의 제품을 소량생산하는 데 적합함.
(2) 워터 피닝
1) 개요
워터 피닝은 강구나 그릿을 사용하는 숏 피닝 가공법에서 숏 대신 물을 고속으로 분사하여 판재의 표면을 가공함.
위터 피닝은 다른 가공법에 비해 소재의 표면을 경화시켜 피로 수명을 증대시킬 수 있고 응력 부식을 방지함.
위터 피닝은 주로 연질 금속의 판재나 임의의 형상을 가진 구조재, 원자력 발전소 등에 이용됨.
2) 워터 피닝의 특징과 효과
(가) 특징
가공에 의한 열 영향부가 발생하지 않음.
가공면이 매끄러워 별도의 기계적인 연마 작업이 불필요함.
숏 피닝 가공에 비해 훨씬 큰 공작물을 가공할 수 있으며 완벽한 커버리지를 달성할 수 있음.
물을 이용하므로 유지비가 적게 들고 환경친화적임.
숏 피닝에서와 같은 쇼트 볼의 처리, 분진 회수 문제가 없음.
(나) 효과
압축 잔류응력의 생성.
표면부의 경도가 증가,
3) 워터 피닝의 적용
쇼트 볼 회수, 분진, 노치부 가공의 어려움, 예리한 모서리부 가공 시 균열 발생 등과 같은 숏 피닝의 문제점을 해결하고자 워터 피닝을 적용하는 데 항공기 엔진 가공이 대표적인 사례임.
(3) 인장 성형법
인장 성형법은 프레스 굽힘 가공에서 스프링 백을 제거하거나 줄이기 위해 굽힘 가공 중에 소재를 항복응력 이상까지 인장하고 압축을 하면서 성형하는 방법임.
소재의 양단을 조에 물리고 펀치로 가압하거나 고정된 펀치로 소재의 양단을 인장하여 가공함.
조에 물리는 부위는 재료 손실이 있으나 항공기 몸체, 지붕 판넬 등의 성형에 사용됨.
일반적으로 펀치와 소재의 마찰에 의해 일부분에 변형률이 집중되어 파단되는 경우가 있으며 이를 방지하기 위해 소재와 펀치 사이에 윤활을 좋게 하고 펀치의 코너 반지름을 크게 해야 함.
(4) 플라스마 용사 성형법
플라스마 용사 성형법은 이온화된 플라스마를 금속 분말과 함께 소재가 제품의 원형에서 필요한 크기와 두께가 될 때까지 반복 분사하여 성형한 후 제품을 원형으로부터 분리시켜 제품을 완성하는 방법임.
일반 금속재의 경우에는 경제적이지 못하지만 텅스텐과 같은 고용융점 재료의 성형에는 적합함.
(5) 레이저 빔 용접에 의한 성형법
모양과 크기, 두께가 다른 판재 조각을 블랭킹 등으로 가공한 후 레이저 빔 용접을 통해 일정 형상으로 붙이고 용접된 판재를 성형하여 제품을 완성하는 방법임.
양복을 재단하는 것과 유사하다고 하여 테일러드 블랭킹이라고 하며 판재 조각의 용접 강도가 매우 높음.
판재 조각을 이용하기 때문에 제품 설계의 유연성이 높고 부분적인 강도 조절이 가능하여 자동차 부품 제작에 많이 사용됨.
(6) 숏 피닝
1) 개요
숏 피닝은 경화된 작은 쇠구슬인 쇼트 볼을 피가공물에 고압으로 분사시켜 표면의 강도를 증가시킴으로써 기계적 성능을 향상시키는 가공법.
숏 피닝의 효과를 최대로 올리기 위해서는 압축 잔류응력을 극 표면으로 끌어내야 하는데 이것을 좌우하는 인자가 쇼트 볼임.
숏 피닝의 강도 조절 변수로는 쇼트 볼의 투사 속도, 크기, 경도, 형상, 단위 시간당 투사량 그리고 투사각도 등이 있음.
2) 숏 피닝 효과의 영향 인자
(가) 쇼트 볼의 크기
쇼트 볼의 다른 인자들이 일정하면 쇼트 볼의 크기가 커짐에 따라 아크 하이트는 커지고 적용 범위는 감소함.
작은 쇼트 볼은 적용 범위에 빨리 도달할 수 있는 이점이 있기 때문에 최소 쇼트 볼의 크기를 선택하여 요구되는 아크 하이트를 얻을 수 있어야 함.
(나) 공작물의 경도
공작물보다 쇼트 볼의 경도가 높으면 아크 하이트에는 영향이 없고 공작물보다 쇼트 볼의 경도가 낮으면 아크 하이트가 낮아짐.
(다) 쇼트 볼의 투사속도
쇼트 볼에 의해 행해지는 최대 일량은 운동 에너지를 초과할 수 없음.
높은 운동 에너지를 얻기 위해 쇼트 볼의 질량을 증가시키면 공작물의 표면 조도가 커지며 기계 작동 상의 문제가 발생할 수도 있음.
따라서 쇼트 볼의 투사속도를 증가시켜 높은 운동 에너지를 얻는 것이 현명한 방법임.
지나치게 쇼트 볼의 투사속도를 증가시키면 아크 하이트는 커지는 반면에 쇼트 볼의 파손율은 높아지고 표면 조도도 커지게 되므로 적절한 쇼트 볼 크기와 투사속도의 선정이 중요함.
(라) 쇼트 볼의 투사각도
쇼트 볼은 투사체가 날아와서 피가공물의 표면에 충격 에너지를 전달하여 압축 잔류응력이 소재의 수직방향으로 발생하게 되므로 입사각도가 0˚에 가까울수록 숏 피닝의 강도가 증가함.
충돌각이 증가하면 충격 에너지가 충돌각만큼 감소하기 때문에 되도록이면 충돌각을 작게 해야 재료 표면에 많은 충격 에너지를 공급할 수 있음.
(7) 핀 포밍
1) 개요
핀 포밍은 항공기 날개 판재의 곡면 부분을 가공하는 데 이용된 이후로 적용 범위가 확대되고 있고 형상을 만드는데 비용을 절약할 수 있으며 손쉽게 테이퍼나 만곡면을 만들어 낼 수 있고 무게에 비해 최대 강도를 증가시킬 수 있으며 재료의 불필요한 손실을 줄일 수 있음.
핀 포밍으로 숏 피닝을 하면 만곡이 일어나는데 이러한 성질을 이용하여 프레스 금형을 사용하지 않고 굽힘 가공이 가능하도록 한 가공법을 말함.
2) 핀 포밍의 원리
쇼트 볼의 충격에 의해 재료 내부에는 소성변형 영역이 발생되는데 투사 에너지의 양에 따라 재료에 전이되는 양이 결정됨.
쇼트 볼의 투사 에너지는 정확한 위치에 정확하게 피닝 강도를 부여해야 하며 가공 재료는 에너지를 흡수하여 소성변형이 될 수 있는 판재여야 함.
쇼트 볼의 투사 에너지는 쇼트 볼의 투사속도와 직경, 판재의 강성에 의존하며 판재는 투사 에너지가 낮을 경우 위로 볼록하게 변형이 이루어지지만 그 반대일 경우에는 아래로 볼록하게 변형함.
이러한 원리를 이용하여 숏 피닝 투사 에너지의 강약에 의한 변형량을 적절히 조절하면 원하는 곡면 형상을 만들 수 있음.
숏 피닝으로 가공한 면의 표층에 똑같이 반복해서숏 피닝을 시행하면 원래의 형상에 가깝게 환원되기 때문에 부분적인 적용을 통해 더욱 복잡한 면의 성형도 가능함.
3) 쇼트 볼의 투사 방식
(가) 중력 낙하식
중력 낙하식은 항공기의 큰 동체 날개를 제작할 때 사용되며 직경이 큰 쇼트 볼을 사용하여 두께 20mm 이상의 날개 표면을 가공함.
쇼트 볼의 투사속도는 저속으로 하여 가공면의 표면 거칠기를 좋게 하고 쇼트 볼의 투사각을 적절히 유지하며 중력 가속도에 의한 낙하 높이를 조절하여 원하는 가공 표면을 얻어야 함.
(나) 공기 노즐식
공기 노즐식은 크기가 작은 노즐 가공이나 매우 소량을 생산하는 경우에 적용되며 쇼트 볼이 커지면 속도의 조절이 어렵고 투사 에너지의 효율이 떨어지며 노즐의 직경도 커지게 되므로 적절한 크기의 쇼트 볼을 선정해야 함.
(다) 원심력 휠식
원심력 휠식은 쇼트 볼의 크기가 큰 것을 투사하는데 가장 적합한 방식이지만 쇼트 볼의 재질이나 크기에 관계없이 투사할 수 있음.
쇼트 볼의 투사속도를 매우 정확하고 재현성 있게 조절할 수 있으므로 CNC 숏 피닝기를 적용하는데 유용한 방식임.
CNC 숏피닝기는 쇼트 볼의 공급량을 조정하고 파쇄 및 마모된 쇼트 볼을 자동으로 분리할 수 있으며 임펠러 제어를 통해 공작물의 재질에 따라 투사속도를 제어할 수 있음.
(8) 워터 제트 가공
1) 개요
워터 제트 가공법은 물줄기를 고속으로 분출시켜 물체와 충돌시키면 물줄기의 운동량의 변화로 물체에 힘을 가하게 되는데 작은 노즐 구멍을 통해 초고압으로 분출시킨 물의 침식으로 소재를 가공함.
각종 기판, 복합 재료, 플라스틱, 작물, 나무, 종이, 가죽 등 비금속 재료의 절단에 우수한 성능을 발휘함.
2) 워터제트의 구성
(가) 고압증강 장치 및 펌핑 유닛
증압기는 물을 고압으로 만들어 주는 장치로써 왕복동형 플런저 펌프가 주로 사용되며 증압된 물은 축압기로 보내지는데 축압기는 물이 노즐에서 분출되기 전에 저장되는 곳으로 압력이 일정하게 유지되어야 함.
(나) 노즐
제트를 형성하는 곳으로 노즐의 직경은 0.05 ~ 0.5mm 정도이고 분출되는 물의 속도는 600 ~ 900m/sec이며 공작물과의 간격은 약 3 ~ 25mm임.
노즐의 구멍부는 사파이어를 주로 사용하나 최근에는 다이아몬드를 사용하기도 함.
3) 특징
예비 구멍이 불필요하고 버의 열적 손상이 거의 없음.
공작물 상에서 절삭력이 작아 취성 재료도 가공이 가능함.
공작물의 변형이 적어 유연한 재료의 절단에 용이함.
환경친화적이고 NC 회로 자유 곡선도 쉽게 가공할 수 있음.
소음이 크고 절단할 수 있는 두께에 제한이 있음.
(9) 입자 제트 가공
1) 가공 원리 및 특징
입자 제트 가공은 워터 제트 또는 비활성 가스의 흐름에 10 ~ 50μm의 연삭입자를 노즐부에서 같이 분출하여 공작물과의 기계적 충격력을 이용하는 가공법임.
금속도 충분히 절단할 수 있으며 열 발생이 없어서 열에 민감한 재료의 절단에 적합함.
2) 적용 분야
취성 재료의 가공.
미소 입자 블라스팅에 사용.
7. 컬링 금형
(1) 개요
특수 가공 및 금형 중 컬링은 판재 또는 용기의 윗부분에 원형 단면의 테두리를 말아 넣는 가공이며 플랜징과 같은 목적으로 사용됨.
플랜지 부분을 둥글게 가공하는 것으로서 컬링 속에 철사나 봉재를 넣고 겉면을 둥글게 하는 것을 와이어링이라 함.
컬링은 경첩과 같은 판형 제품의 컬링 가공과 드로잉 된 원통형 용기의 가장자리에 테두리를 만드는 컬링 가공 2가지로 나뉨.
컬링을 하는 목적은 강도를 높이고 끝부분의 예리함을 없애주기 위함임.
(2) 가공 종류
1) 판형 제품의 컬링 가공
컬링 가공은 일반적으로 컬링 할 부분을 일정한 곡률로 약간 굽혀주는 제1공정과 원형의 형상으로 완전히 마는 제2공정으로 구분.
제1공정은 펀치의 한쪽 날을 제1공정의 형상으로 하여 재료가 눌려 굽혀지면서 블랭킹 작업과 동시에 진행됨.
미리 전단된 제품을 굽힘 가공별로 하여 제2공정을 마무리함.
2) 원통 용기의 컬링 가공
원통 용기의 컬링 가공은 판형 제품과 같이 2단계의 공정을 가지지 않고 1공정에 가공을 완료함.
원통 용기의 컬링 부위는 가공면이 균일해야 하며 불균일할 때는 트리밍 가공을 해야 함.
(3) 컬링 금형의 종류
1) 판형 컬링 금형
판형 컬링 금형은 컬링한 부분이 위로 가도록 재료를 다이에 세워서 가공하는 방식과 다이에 컬링 홈을 만들어 재료를 밀어 넣고 위에서 펀치로 가압하는 방식으로 구분됨.
펀치에서 컬링 부분이 굽혀질 경우 둥글게 말리는 부분은 펀치의 상승 시 펀치에 끼어 위로 올라가 다이에서 빠져나오게 됨.
이후 제품은 손이나 녹아웃 장치에 의해 펀치에서 취출됨.
다이에 부시를 설치한 컬링 금형인 경우 제1공정에서 굽혀지는 부분이 다이 속으로 들어가면 펀치의 압력에 의해 부시 구멍의 원추를 따라 둥글게 말림.
다이 속에서 컬링 가공된 제품은 다이에 꽉 차기 때문에 펀치의 상승 시 작동되는 기계적 도그래그 캠과 슬라이드 장치를 이용함.
2) 원통 용기의 컬링 금형
원통 용기의 컬링 금형은 내 컬링과 외 컬링으로 구분됨.
컬링 홈은 펀치에 설치되어 있고 다이는 제품의 외형에 똑같은 형상으로 가공함.
다이의 길이는 제품의 컬링 깊이를 뺀 값보다 약간 작아야 하며 제품의 밑바닥 라운드 부분이 꼭 맞게 다이가 제작되어야 함.
펀치의 컬링 홈은 말리는 내측 부분을 더 길게 하고 약 30˚ 정도 경사지게 하여 소재의 안내를 원활하게 함.
가공할 소재의 용기가 깊은 경우에는 녹아웃 장치를 설치하여 제품을 취출함.
8. 버링
(1) 개요
특수 가공 및 금형 중 버링은 평판에 기초 구멍을 뚫고 그것으로부터 직경이 큰 펀치로 훑어 내려서 원통 벽을 세우는 공정으로서 홈 플랜징이라고도 함.
버링 된 플랜지의 내면에 성형용 탭을 이용하여 암나사를 가공하거나 두께 이상의 판을 리벳 없이 결합할 때 이용함.
보통의 버링 가공에서는 수직벽의 판 두께가 15 ~ 20%이고 1회 가공으로 달성할 수 있는 플랜지 높이의 한계는 대체로 구멍 지름의 10% 정도임.
(2) 버링의 가공 변수
1) 펀치 선단의 형상
펀치 선단의 형상이 원추형으로 예리할수록 성형성은 증가하나 성형 스트로크가 길어지게 됨에 따라 생상성이 저하됨.
2) 구멍의 전단면 상태
구멍의 전단면 상태가 불량하면 균열이 생겨 성형을 저하시킴.
피어싱한 구멍의 전단면을 드릴링 등을 통해 다듬질하게 되면 상대적으로 플랜징의 높이가 높은 버링 가공이 가능함.
3) 재료의 성질
연성이 높은 재질은 변형 저항이 작게 되어 버링의 가공성을 향상시킴.
알루미늄은 보통 강판에 비해 버링 가공의 한계(펀치의 직경 / 초기 구멍의 직경)가 약 40% 향상됨.
4) 다이의 코너 반지름
가능한 한 다이의 코너 반지름을 크게 해야 버링 된 수직벽의 높이를 높일 수 있음.
(3) 버링 가공의 종류
1) 일반 버링
태핑용 버링 가공을 할 때에는 탭의 치수를 먼저 결정한 다음 버링 치수를 결정하고 마지막으로 피어싱 치수를 결정함.
드로잉 가공과 같이 블랭크 홀더를 부착하여 피어싱된 소재를 누르면서 가공하는 것이 일반적임.
드로잉 제품의 밑바닥을 펀칭하고 버링으로 제품의 높이를 증가시키는 방법도 있는데 이를 드로 버링이라함.
2) 돌파 버링
구멍 뚫기와 버링을 동시에 가공하는 것으로서 구멍을 가공한 후 확대·성형한 것임.
작은 구멍의 버링에 많이 사용하고 펀치의 선단 각도는 소재 두께에 영향을 받으나 대략 55 ~ 60˚ 정도로 함.
펀치의 선단 형상을 3각, 4각, 5각으로 하여 초기의 구멍을 내지 않은 상태로 1회 가공으로 돌파하면서 버링 가공을 하는 경우도 있으나 이 경우 플랜지의 윗부분에 균열이 생김.
3) 스트레치 버링
Φ12mm 이하의 비교적 작은 구멍은 피어싱과 버링을 동시에 할 수 있는 스트레치 버링 공정을 취함.
펀치에 단을 주어 1공정에서 1개의 펀치로 피어싱과 버링 가공을 시행함.
4) 아이오닝 버링
일반적으로 버링 가공에서 버링 된 측벽의 판 두께 감소가 15 ~ 30%이나 판 두께의 감소를 일반 버링의 2배 정도로 크게 하여 수직벽의 높이를 증가시키는 버링 가공법.
9. 스웨이징
(1) 개요
특수 가공 및 금형 중 스웨이징은 중공축, 중실축 및 강선 등의 소재를 2개 또는 그 이상의 분리형 금형에 삽입한 후 소재의 반지름 방향으로 점진적인 반복하중을 가하여 소재의 단면을 변화시키는 점진 성형 공정으로 기계 가공을 필요로 하지 않음.
로터리 스웨이징은 봉이나 원통형 관 모양의 재료를 축 주위로 회전시키면서 공구를 이용하여 재료를 한 부분씩 축과 직각방향으로 짓눌러 경사지게 하거나 지름을 줄여서 길이를 늘이는 점진 성형 공정으로 자동차 중공축 등의 생산에 활용됨.
(2) 스웨이징 공정
1) 로터리 스웨이징
로터리 스웨이징은 스웨이징 또는 경방향 단조라고도 하며 왕복운동하는 금형으로 봉재나 관재의 반지름 방향으로 타격하여 작업을 진행함.
금형의 움직임은 롤러 베어링처럼 틀 속에 들어 있는 롤러에 의해 이루어지며 소재는 움직이지 않고 금형 세트가 회전하면서 초당 20회 정도의 고속으로 소재에 타격을 가하여 주로 축 대칭 원형 제품을 생산하지만 외륜 회전형인 경우에는 육각형, 팔각형, 타원형, 십자형 같은 비원형 제품도 생산할 수 있음.
2) 금형 밀폐형 스웨이징
금형 밀폐형 스웨이징은 금형의 운동이 왕복하는 쐐기의 운동으로부터 얻어지는데 로터리 스웨이징에 비해 금형이 넓게 벌어지므로 지름이 크거나 고르지 않은 제품도 생산할 수 있음.
또 다른 유형으로는 금형이 회전하지 않고 반지름 방향으로 왕복운동만 하는 것도 있음.
금형 밀폐형 스웨이징은 2개의 롤러가 트러스트 피스 양단에 위치할 때 다이는 최대한 개폐가 되며 이러한 방법은 트러스트 피스나 다이스의 관리나 교체 시 유리한 구조를 가짐.
해머의 스트로크만큼 서로 마주 보고 있는 금형은 축 중심을 향하여 반지름 방향으로 타격을 유발하게 되며 반복적인 충격에 의해 금형 속의 소재는 점진적으로 금형 형상으로 성형이 이루어짐.
맨드렐을 사용하면 내부에 형상이 있는 튜브 제품도 성형할 수 있음.
(3) 특징
치수 정밀도가 우수한 고정도의 제품의 대량생산에 유용함.
설비비가 저렴하고 구조가 간단하며 비숙련자도 작업이 용이함.
강과 비철금속 등 여러 가지 재질을 이용하여 열간, 냉간 성형이 가능함.
금속 섬유 조직이 연속적으로 형성되어 기계적 성질을 향상시킴.
절삭가공에 비해 경면에 가까운 표면 정밀도를 얻을 수 있음.
칩 발생이 없고 재료비가 40% 이상 절감됨.
다른 점진 성형 공정보다 높은 소음과 진동이 발생함.
(4) 성형 가공 형상
축 대칭 성형 소재의 중앙부 단면을 감소시키는 성형.
봉재 성형, 튜브 성형, 내•외부 성형.
테이퍼 성형, 튜브의 끝단 오므리기 성형.
10. 하이드로 포밍
(1) 개요
특수 가공 및 금형 중 하이드로 포밍은 금형 속에 들어가 있는 강관 속에 물 등의 액체를 주입하여 내부에부터 강한 액압을 가하여 복잡한 형상으로 일체 성형하는 공법.
하이드로 포밍은 관의 중간 부분을 확관 가공하는 가공법과 굽혀진 강관의 일부를 확관하는 가공법으로 나뉨.
하이드로 포밍의 가장 큰 특징은 한 개의 파이프로 요철이 있거나 휘어진 복잡한 형태의 제품을 단 한번에 만들어 낼 수 있음.
(2) 종류와 특징
1) 관재 하이드로 포밍
관재 하이드로 포밍 제품은 전 세계 자동차 회사에서 가장 많이 사용하고 있는 추세이며 그 적용 부품 역시 점차 확대되고 있음.
관재 하이드로 포밍 제품은 경량화 뿐만 아니라 부품수를 감소시켜 조립 공정을 단순화할 수 있으며 조립 정도를 향상시킬 수 있는 효과가 있음.
하지만 생산 설계 기술이 요구되고 초기 투자비가 많이 든다는 것이 단점임.
2) 판재 하이드로 포밍
관재 하이드로 포밍에 비해 판재를 이용한 하이드로 포밍은 생산성 및 투자비 때문에 적용 범위가 크게 늘어나지 않고 있음.
판재 하이드로 포밍은 펀치만으로 제품을 성형하는 기술로 고무를 이용한 마폼법에서 고무 대신에 액체를 이용한 것이 유사함.
기존 프레스 금형을 이용한 성형에서 다이측을 액압 탱크로 구성하여 액압을 이용하여 펀치 형상대로 제품을 가공하는 방법임.
따라서 금형비가 프레스 금형보다 적게 소요되어 다품종 소량생산에 유리하고 제작 기간을 단축시킬 수 있음.
관재 하이드로 포밍과 마찬가지로 판재 하이드로 포밍도 경량화의 효과를 높일 수 있는 장점을 가짐.
(3) 생산설비
하이드로 포밍은 금형에 의존하기보다는 재료 특성에 따른 압력을 제어하는 기술에 더 의존하는 가공법임.
따라서 하이드로 포밍의 성공 여부는 외부로부터 압력 부하나 힘을 가하는 타이밍, 크기, 속도 등을 어떻게 제어하는가에 달려있음.
하이드로 포밍 프레스는 단독 고압 프레스 장비에 자동화 장비를 설치하여 라인 개념으로 구성하는 게 일반적임.
기존 하이드로 포밍 장비와 달리 프레스가 모듈화되어 있으며 성형 시 고압으로 금형을 지지하는 것이 아니라 프레스 구조물을 기계적으로 고정시킴으로서 고압에 대한 반발력을 유지할 수 있기 때문에 라인 개념으로 구성할 수 있음.
11. 고무 성형
(1) 개요
고무 성형은 압축 성형법이 일반적으로 널리 이용되고 있음.
고무 생지로 고무 제품을 성형할 때에는 일반적으로 혼합, 성형, 가황, 다듬질 등의 공정을 거쳐 성형함.
성형가공을 용이하게 하기 위해 가역화한 고무에 가황제, 촉진제, 노화 방지제 등의 배합제를 혼합함.
하지만 플래시 발생, 스프루-러너의 가류화에 따른 손실, 제품 취출 후 폐기되는 스크랩으로 인한 환경 문제 발생, 후공정에 따른 품질 저하 및 원가 상승, 자동화를 수행할 수 없는 금형 구조로 인해 대량생산에서 나타는 취약점 등이 대두되고 있음.
(2) 고무 성형 금형의 고려 사항
1) 형체 기구
고무 성형은 금형의 작은 틈새가 있으면 플래시가 발생함.
이것을 방지하기 위해 금형 설계, 제작상에서의 열적 요인을 충분히 고려해야 하며 형체 장치로 휨을 억제할 수 있는 고강성의 플레이트와 가공정도, 열변형 대책이 중요함.
성형품의 투영면적보다 형체결력이 작으면 사출압력에 의해 고정측 형판과 가동측 형판 사이가 벌어져 플래시가 발생함.
2) 가스제거(범핑)
사출 성형에서는 고압 형체로 닫힌 금형 내에 고무 생지를 충전하는데 캐비티 내의 공기나 가류반응에 의한 가스를 빼내는 동작이 필요하게 되어 충전 완료 후에 타이밍을 가늠하여 형체압력을 내리거나 금형을 조금 열어 공기나 가스를 배출하고 다시 형체 하는 동작으로 성형 불량을 피해야 함.
3) 진공장치
금형 캐비티 내의 공기나 가류반응에 의한 가스를 진공펌프로 흡인하는 방법으로서 금형에 설치된 가스 빼기 홈을 이용하여 흡인하거나 파팅 라인에 오링실 등을 설치하여 형체 일시정지 시 흡인 후 사출하는 과정을 수행함.
4) 플래시 제거
일반적으로 고무 금형에서 완벽한 플래시 처리가 불가능한 것으로 보이지만 플래시를 깨끗이 처리하기 위해서는 고무 재료의 흐름성이나 사상성과 기계의 정확한 정도가 중요함.
금형의 각 형판들의 정밀 평판 연삭을 통한 두께 평행도를 정확하게 가공하고 여러 판을 조립한 후에도 정확한 평행도를 유지해야 함.
형체결력과 캐비티 개수 등의 선정이 균일한 압력을 유지하기 위하여 금형에 가하는 압력 지점을 다르게 하고 압력을 집중시켜 접합부를 정밀 밀착시키는 금형 제작 기술을 확보함으로서 플래시 발생을 방지할 수 있음.
(3) 고무 성형의 종류
1) 압축성형
압축성형은 고무 성형의 기본적인 방법으로서 열경화성 플라스틱의 대표적인 성형법임.
계량한 원료를 가열한 금형의 캐비티에 넣어 가압하여 경화시켜 성형하는 방법으로서 원료는 캐비티 내에서 가열되어 경화하므로 적당한 경화시간 후 금형을 열고 성형품을 취출함.
캐비티 내의 공기를 빼고 원류를 흘려 충전을 좋게 하기 위해 진공 흡인을 하거나 가열•화학반응으로 발생한 가스를 빼는 조작을 등을 수행해야 함.
압축성형은 설비비가 저렴하고 어떠한 성형 재료도 성형 가능하며 성형품 배향이 적고 재료 손실이 적은 장점이 있음.
고무 제품의 다품종 소량생산에 넓게 사용되고 있음.
2) 사출성형
플라스틱 사출성형과 매우 유사한 방법으로서 고무 생지는 스크루로 연속 공급하고 소정량을 연화•용융시켜가며 계량하는 스크루로 금형에 고압•충전하고 가류하는 성형법임.
다른 성형법보다 성형 사이클이 빠르고 균일한 가류 제품을 얻을 수 있어 대량생산에 적합함.
3) 이송성형
사출성형의 간이 방법으로서 고무 생지를 가열부에서 가열하여 가압부로 이송한 후 플랜저로 가열된 금형에 주입하여 가류를 하는 성형법임.
이송성형에서 성형압력이 가장 중요한 요인이며 성형압력이 낮으면 충전을 완료하기가 어렵고 반대로 너무 높으면 플래시가 발생할 뿐만 아니라 캐비티 내의 각종 핀 이나 코어류 및 삽입물 등에 과대한 힘이 작용하여 변형되거나 그 위치를 어긋나게 하여 이송성형의 본래의 이점을 잃게 됨.
이송성형에서는 포트부의 구조상 재료의 흐름에 대한 저항이 크기 때문에 보조 램식 이송성형의 경우에 비해서 10 ~ 20% 높은 성형압력이 필요함.
특수 가공 및 금형 연재를 끝으로 소성가공에 대한 연재을 마치고 다음에는 금형 제작 및 측정에 대한 연재를 시작할 예정입니다.
2020년 09월 06일