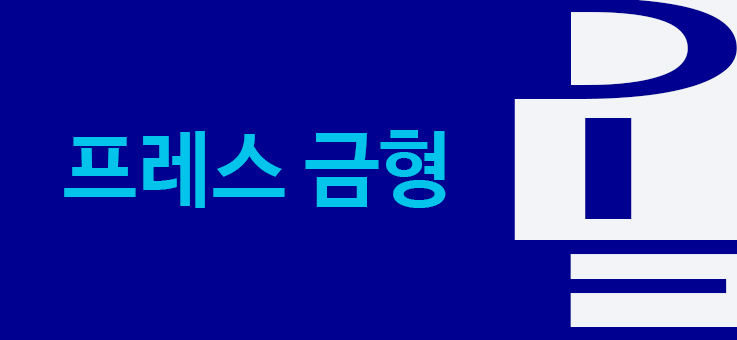
HOME → DIE CATEGORIES →
프레스 금형 1
본격적으로 프레스 금형을 기술하기 전에 프레스 가공(DIE Working)에 따른 분류와 특징 그리고 가공 방법에 대해서 언급을 먼저 하겠습니다.
제1장 프레스 가공
1. 개요
프레스 가공은 프레스를 이용하여 소재를 소성변형시켜 여러 가지 형상으로 만드는 가공법이며 금형, 프레스 기계, 피가공재를 프레스 가공의 3요소라고 합니다.
2. 특징
(1) 복잡한 형상을 간단하게 가공할 수 있음.
(2) 절삭가공에 비해 인성 및 강도가 우수함.
(3) 정밀도가 높고 대량생산이 가능함.
(4) 재료 이용률이 높음.
(5) 가공속도가 빠르고 능률적임.
(6) 절삭가공만큼 숙련된 기술을 요하지 않음.
3. 종류
(1) 전단 가공
전단 가공을 시행할 때에는 클리어런스가 필요하므로 펀치의 외경보다 다이의 내경이 커야 하며 클리어런스는 소재의 두께에 4~12% 정도가 적당합니다.
1) 시어링(SHEARING)
시어링 머신으로 소재의 일부를 잘라내는 작업으로 이 작업 중 스크랩이 거의 없이 규칙적인 배열로 전단하는 공정을 컷 오프라고 함.
2) 블랭킹(BLANKING)
미리 결정되어 있는 윤곽을 전단하는 작업으로 외부에 남는 것은 스크랩이 됨.
소재(왼쪽)와 제품(오른쪽)
3) 파인 블랭킹(FINE BLANKING)
스트리퍼 밑면에 삼각선의 비드를 설치하여 소재를 강하게 눌러 정수압 상태를 만들고 다이와 펀치 사이의 클리어런스를 최대한 없앤 후 상하 양쪽에서 가압하여 고운 전단면과 정밀한 치수를 얻을 수 있는 가공.
나중에 또 언급하겠지만 일반 블랭킹과 파인 블랭킹의 차이점이 무엇인지 궁금할 수 있을 것입니다.
다음과 같이 표로 두 가공법의 차이점을 간략히 설명해보도록 하겠습니다.
일반 블랭킹 | 파인 블랭킹 | |
---|---|---|
전단 면 상태 | 버가 발생함 | 버가 발생하지 않음 |
치수 정밀도 | 미크론 가공 불가능 | 미크론 가공 가능 |
공 정 | 단일 공정만 가능 | 복잡한 여러 공정 가능 |
후 가 공 | 필요 | 불필요 |
원 가 | 높다 | 낮다 |
클리어런스 | 크다 | 0에 가깝다 |
4) 분단(PARTING)
소재의 중심선을 따라 혹은 소재의 사이를 절단하여 동일 형상이 두 개 이상으로 나뉘는 가공.
5) 피어싱
블랭킹과 사용목적이 반대이며 소재에 형을 이용하여 구멍을 뚫는 가공으로 다른 말로 펀칭이라고 하며 떼어낸 부분이 스크랩이 됨.
소재(왼쪽)와 제품(오른쪽)
6) 트리밍(TRIMMING)
중간 또는 최종 프레스 공정에서 제품을 소요 형상으로 만들기 위해 전체 둘레 또는 부분적으로 스크랩 부위를 절단하는 가공.
소재(왼쪽)와 제품(오른쪽)
7) 노칭(NOTCHING)
소재의 가장자리를 여러 가지 모양으로 절단하는 가공.
소재(왼쪽)와 제품(오른쪽)
8) 셰이빙(SHAVING)
1차 가공된 절단면을 다시 전단 금형으로 파단면을 깎아내어 평활하고 깨끗한 전단면을 얻을 수 있는 가공.
소재(왼쪽)와 제품(오른쪽)
9) 루버링(LOUVERING)
펀치와 다이의 한쪽은 전단이 되고 다른쪽은 바늘 창 형상으로 굽히는 가공.
제품
(2) 굽힘 가공
소재에 외력을 가해 재료에 영구 변형을 주어 외력을 제거하여도 본래의 형태로 돌아가지 않도록 하는 가공법이며 신장이 크고 점성이 약한 연질 재료가 적합합니다.
경질 재료일수록 스프링 백이 크고 취성이 있어 굽힘 반지름 부분에 균열이 생기기 쉽고 가공이 어렵습니다.
1) 벤딩(BENDING)
제품의 장식 또는 보강을 목적으로 소재에 변형을 주어 여러 가지 형상으로 굽히는 가공으로 V자, U자, L자, Z자, 채널 굽힘 등이 있음.
2) 포밍(FORMING)
판 두께의 감소를 의식적으로 행하지 않고 소재를 상•하형 사이에 놓고 눌러서 여러 가지 형상을 만드는 가공.
제품
3) 버링(BURRING)
뚫려 있는 구멍의 내경보다 큰 직경의 펀치로 눌러 구멍의 가장자리를 판재의 면과 직각으로 구멍 둘레에 플랜지를 만드는 가공.
4) 시이밍(SEAMING)
두 장에 판재의 단부를 굽히면서 눌러 접합하는 가공법으로 음료수나 통조림 캔 등을 제조할 때 사용.
5) 컬링(CURLING)
판재 또는 용기의 윗부분에 원형 단면의 테두리를 말아 넣는 가공법으로 플랜징과 같은 목적으로 사용.
6) 플랜징(FLANGING)
소재의 가장자리를 구부려 세우는 가공.
소재(왼쪽)와 제품(오른쪽)
7) 비딩(BEADING)
용기 또는 판재의 일부에 장식 또는 보강의 목적으로 줄 모양의 돌기를 넣은 가공.
제품
8) 엠보싱(EMBOSSING)
소재에 두께의 변화를 일으키지 않고 여러 가지 형상의 작은 요철을 만드는 가공.
제품
9) 네킹(NECKING)
원통이나 원형 용기 끝부분의 지름을 감소시키는 가공.
소재(왼쪽)와 제품(오른쪽)
10) 폴딩(FOLDING)
판재의 끝이나 중앙을 90° 이상 구부려 접는 가공.
소재(왼쪽)와 제품(오른쪽)
(3) 성형 가공
성형 가공 또는 드로잉 가공은 블랭킹한 판재를 원통형, 각통형, 반구형 등의 밑면이 있고 이음새가 없는 용기를 만드는 가공법입니다.
드로잉 가공에 적합한 소재는 연성이 좋고 인장강도가 크고 균열이 발생하지 않아야 합니다.
드로잉 가공 시 제품의 원주방향으로 수축이 되면서 길이 방향으로는 늘어나는 현상이 발생하므로 펀치나 다이 날부에 R을 주어 제품에 주름 및 전단 현상이 발생하지 않도록 주의해야 합니다.
1) 드로잉(DRAWING)
평판의 소재에 이음매가 없는 중공 용기를 주름이나 균열이 생기지 않고 다이 안에 펀치를 넣어 성형시키는 가공.

2) 재드로잉(REDRAWING)
드로잉 된 제품의 지름을 감소시키면서 깊이를 증가시키는 가공법으로 가공 방식에 따라 직접 재드로잉과 역(식) 재드로잉으로 구분.
3) 아이어닝(IRONING)
드로잉 가공 후 제품의 두께가 일정하지 않기 때문에 제품의 측벽 두께를 얇고 균일하며 높이를 높게 훑어주는 가공.
4) 리스트라이킹(RESTRIKING)
앞 공정에서 만든 형상을 보다 정확하게 하기 위해 최종 제품 치수로 만드는 가공.
5) 스피닝(SPINNING)
제품의 원형을 선반의 스핀들에 고정하고 원형과 심압대와의 사이에 소재를 끼워서 스핀들과 함께 롤러를 회전시켜 가공.

(4) 압축 가공
펀치와 다이를 이용하여 여러 가지 단면 형상을 가진 솔리드 제품이나 중공 제품을 만드는 가공을 말합니다.
상온에서 소재에 펀치의 압력을 가하여 다이의 구멍이나 펀치와 다이의 틈으로 유동 현상을 일으켜 긴 슬리브 형태의 제품을 한 공정으로 완성합니다.
1)전방 압출(FORWARD EXTRUSION)
다이의 개구부로부터 펀치의 진행 방향으로 소재를 유출시켜 형상을 만드는 압출 가공.
2) 후방 압출(BACKWARD EXTRUSION)
다이와 펀치 사이의 틈으로부터 펀치의 진행과 반대 방향으로 소재를 유출시키는 압출 가공.
3) 복합 압출(FORWARD & BACKWARD EXTRUSION)
전방 압출과 후방 압출을 한 공정에 동시에 시행하는 가공.
4) 충격 압출(IMPACT EXTRUSION)
매우 얇은 살두께의 제품을 만드는 후방 압출 가공으로 연질 금속에 한해서 가공이 가능.
5) 업셋팅(UPSETTING)
소재를 길이 방향으로 압축하여 길이를 감소시킴으로써 길이 방향과 직각 방향으로 소재를 이동•유동시켜 큰 길이 방향과 직각인 단면을 만드는 가공으로 대표적으로 볼트와 리벳이 있음.
6) 압인(COINING)
금속판이나 반제품의 전 표면을 규제하는 밀폐형에 의해 그 표면을 압축하여 형과 똑같은 모양의 요철을 만드는 가공으로 대표적으로 화폐와 메달이 있음.
7) 사이징(SIZING)
형에 의해 소재의 전체 또는 일부에 강한 압력을 가하여 소재에 유동을 일으켜서 제품의 치수와 정도를 향상시키는 가공.
8) 헤딩(HEADING)
봉재의 끝을 업셋팅하여 볼트나 리벳을 만드는 일종의 업셋팅 가공.
9) 스웨이징(SWAGING)
중공축, 중실축 및 강재 등의 소재를 2개 또는 그 이상의 분리형 금형에 삽입한 후 소재의 반경 방향으로 점진적인 반복하중을 가하여 소재의 단면을 변화시키는 가공.
(5) 기타
클램프 장치를 이용하거나 순간적인 충격을 가하거나, 고무나 액체를 이용하여 소재에 변형을 주는 가공법으로 여러 가지 형태의 제품을 만드는데 이점이 있습니다.
특수 장치와 기술이 뒷받침되어야 하기 때문에 가공방법이 어려울 수 있으나 차츰 기술이 발달됨에 따라 복잡한 형상이나 가공시간을 단축과 소재를 절약하기 위해서 시행되고 있습니다.
1) 벌징(BULGING)
통 모양의 용기, 관 등의 측벽을 내부로부터 압력을 가하여 배를 부르게 하는 가공으로 내부에 압력을 가하는 수단으로는 방사상으로 분할된 펀치나 유체, 고무 등을 사용함.
2) 스트레치 드로우 포밍(STRETCH DRAW FORMING)
프레스 금형의 양쪽에 설치된 스트레치 장치에 의해 강판을 항복점 이상으로 늘리고 그 상태에서 드로잉을 시행하는 가공.
3) 하이드로 포밍(HYDRO-FORMING)
펀치만 금형을 사용하고 다이에는 유압으로 지지된 고무판을 사용하는 가공으로 성형이 어려운 모양을 만들 때 사용함.
4) 허프 포밍(HERF FORMING)
여러 가지 허프 장치를 사용하여 초고속으로 시행하는 가공으로 소재의 성형성이 좋아져서 종래의 방법으로 할 수 없던 것을 무리 없이 시행할 수 있음.
이상으로 프레스 금형의 개요를 마치고 다음 연재는 아마도 프레스에 대한 것이 될 것 같습니다.
프레스는 프레스 가공을 하는 데 있어 매우 중요한 기계이며 대량생산을 위해 폭넓게 사용되고 있기 때문에 꼭 집고 넘어가야 할 분야인 것 같습니다.
2020년 04월 21일
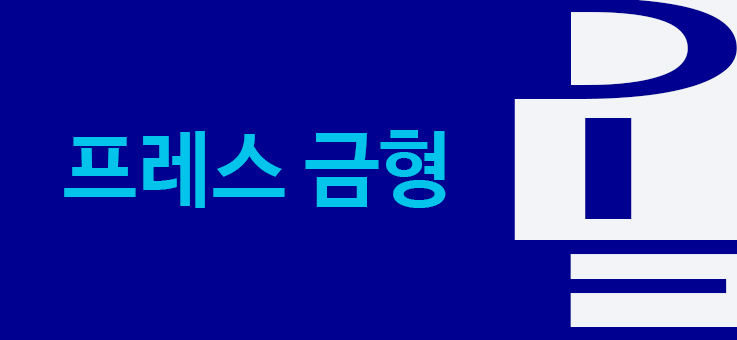
HOME → DIE CATEGORIES →
프레스 금형 1
본격적으로 프레스 금형을 기술하기 전에 프레스 가공(DIE Working)에 따른 분류와 특징 그리고 가공 방법에 대해서 언급을 먼저 하겠습니다.
제1장 프레스 가공
1. 개요
프레스 가공은 프레스를 이용하여 소재를 소성변형시켜 여러 가지 형상으로 만드는 가공법이며 금형, 프레스 기계, 피가공재를 프레스 가공의 3요소라고 합니다.
2. 특징
(1) 복잡한 형상을 간단하게 가공할 수 있음.
(2) 절삭가공에 비해 인성 및 강도가 우수함.
(3) 정밀도가 높고 대량생산이 가능함.
(4) 재료 이용률이 높음.
(5) 가공속도가 빠르고 능률적임.
(6) 절삭가공만큼 숙련된 기술을 요하지 않음.
3. 종류
(1) 전단 가공
전단 가공을 시행할 때에는 클리어런스가 필요하므로 펀치의 외경보다 다이의 내경이 커야 하며 클리어런스는 소재의 두께에 4~12% 정도가 적당합니다.
1) 시어링(SHEARING)
시어링 머신으로 소재의 일부를 잘라내는 작업으로 이 작업 중 스크랩이 거의 없이 규칙적인 배열로 전단하는 공정을 컷 오프라고 함.
2) 블랭킹(BLANKING)
미리 결정되어 있는 윤곽을 전단하는 작업으로 외부에 남는 것은 스크랩이 됨.
소재(왼쪽)와 제품(오른쪽)
3) 파인 블랭킹(FINE BLANKING)
스트리퍼 밑면에 삼각선의 비드를 설치하여 소재를 강하게 눌러 정수압 상태를 만들고 다이와 펀치 사이의 클리어런스를 최대한 없앤 후 상하 양쪽에서 가압하여 고운 전단면과 정밀한 치수를 얻을 수 있는 가공.
나중에 또 언급하겠지만 일반 블랭킹과 파인 블랭킹의 차이점이 무엇인지 궁금할 수 있을 것입니다.
다음과 같이 표로 두 가공법의 차이점을 간략히 설명해보도록 하겠습니다.
일반 블랭킹 | 파인 블랭킹 | |
---|---|---|
전단 면 상태 | 버가 발생함 | 버가 발생하지 않음 |
치수 정밀도 | 미크론 가공 불가능 | 미크론 가공 가능 |
공 정 | 단일 공정만 가능 | 복잡한 여러 공정 가능 |
후 가 공 | 필요 | 불필요 |
원 가 | 높다 | 낮다 |
클리어런스 | 크다 | 0에 가깝다 |
4) 분단(PARTING)
소재의 중심선을 따라 혹은 소재의 사이를 절단하여 동일 형상이 두 개 이상으로 나뉘는 가공.
5) 피어싱
블랭킹과 사용목적이 반대이며 소재에 형을 이용하여 구멍을 뚫는 가공으로 다른 말로 펀칭이라고 하며 떼어낸 부분이 스크랩이 됨.
소재(왼쪽)와 제품(오른쪽)
6) 트리밍(TRIMMING)
중간 또는 최종 프레스 공정에서 제품을 소요 형상으로 만들기 위해 전체 둘레 또는 부분적으로 스크랩 부위를 절단하는 가공.
소재(왼쪽)와 제품(오른쪽)
7) 노칭(NOTCHING)
소재의 가장자리를 여러 가지 모양으로 절단하는 가공.
소재(왼쪽)와 제품(오른쪽)
8) 셰이빙(SHAVING)
1차 가공된 절단면을 다시 전단 금형으로 파단면을 깎아내어 평활하고 깨끗한 전단면을 얻을 수 있는 가공.
소재(왼쪽)와 제품(오른쪽)
9) 루버링(LOUVERING)
펀치와 다이의 한쪽은 전단이 되고 다른쪽은 바늘 창 형상으로 굽히는 가공.
제품
(2) 굽힘 가공
소재에 외력을 가해 재료에 영구 변형을 주어 외력을 제거하여도 본래의 형태로 돌아가지 않도록 하는 가공법이며 신장이 크고 점성이 약한 연질 재료가 적합합니다.
경질 재료일수록 스프링 백이 크고 취성이 있어 굽힘 반지름 부분에 균열이 생기기 쉽고 가공이 어렵습니다.
1) 벤딩(BENDING)
제품의 장식 또는 보강을 목적으로 소재에 변형을 주어 여러 가지 형상으로 굽히는 가공으로 V자, U자, L자, Z자, 채널 굽힘 등이 있음.
2) 포밍(FORMING)
판 두께의 감소를 의식적으로 행하지 않고 소재를 상•하형 사이에 놓고 눌러서 여러 가지 형상을 만드는 가공.
제품
3) 버링(BURRING)
뚫려 있는 구멍의 내경보다 큰 직경의 펀치로 눌러 구멍의 가장자리를 판재의 면과 직각으로 구멍 둘레에 플랜지를 만드는 가공.
4) 시이밍(SEAMING)
두 장에 판재의 단부를 굽히면서 눌러 접합하는 가공법으로 음료수나 통조림 캔 등을 제조할 때 사용.
5) 컬링(CURLING)
판재 또는 용기의 윗부분에 원형 단면의 테두리를 말아 넣는 가공법으로 플랜징과 같은 목적으로 사용.
6) 플랜징(FLANGING)
소재의 가장자리를 구부려 세우는 가공.
소재(왼쪽)와 제품(오른쪽)
7) 비딩(BEADING)
용기 또는 판재의 일부에 장식 또는 보강의 목적으로 줄 모양의 돌기를 넣은 가공.
제품
8) 엠보싱(EMBOSSING)
소재에 두께의 변화를 일으키지 않고 여러 가지 형상의 작은 요철을 만드는 가공.
제품
9) 네킹(NECKING)
원통이나 원형 용기 끝부분의 지름을 감소시키는 가공.
소재(왼쪽)와 제품(오른쪽)
10) 폴딩(FOLDING)
판재의 끝이나 중앙을 90° 이상 구부려 접는 가공.
소재(왼쪽)와 제품(오른쪽)
(3) 성형 가공
성형 가공 또는 드로잉 가공은 블랭킹한 판재를 원통형, 각통형, 반구형 등의 밑면이 있고 이음새가 없는 용기를 만드는 가공법입니다.
드로잉 가공에 적합한 소재는 연성이 좋고 인장강도가 크고 균열이 발생하지 않아야 합니다.
드로잉 가공 시 제품의 원주방향으로 수축이 되면서 길이 방향으로는 늘어나는 현상이 발생하므로 펀치나 다이 날부에 R을 주어 제품에 주름 및 전단 현상이 발생하지 않도록 주의해야 합니다.
1) 드로잉(DRAWING)
평판의 소재에 이음매가 없는 중공 용기를 주름이나 균열이 생기지 않고 다이 안에 펀치를 넣어 성형시키는 가공.

2) 재드로잉(REDRAWING)
드로잉 된 제품의 지름을 감소시키면서 깊이를 증가시키는 가공법으로 가공 방식에 따라 직접 재드로잉과 역(식) 재드로잉으로 구분.
3) 아이어닝(IRONING)
드로잉 가공 후 제품의 두께가 일정하지 않기 때문에 제품의 측벽 두께를 얇고 균일하며 높이를 높게 훑어주는 가공.
4) 리스트라이킹(RESTRIKING)
앞 공정에서 만든 형상을 보다 정확하게 하기 위해 최종 제품 치수로 만드는 가공.
5) 스피닝(SPINNING)
제품의 원형을 선반의 스핀들에 고정하고 원형과 심압대와의 사이에 소재를 끼워서 스핀들과 함께 롤러를 회전시켜 가공.

(4) 압축 가공
펀치와 다이를 이용하여 여러 가지 단면 형상을 가진 솔리드 제품이나 중공 제품을 만드는 가공을 말합니다.
상온에서 소재에 펀치의 압력을 가하여 다이의 구멍이나 펀치와 다이의 틈으로 유동 현상을 일으켜 긴 슬리브 형태의 제품을 한 공정으로 완성합니다.
1)전방 압출(FORWARD EXTRUSION)
다이의 개구부로부터 펀치의 진행 방향으로 소재를 유출시켜 형상을 만드는 압출 가공.
2) 후방 압출(BACKWARD EXTRUSION)
다이와 펀치 사이의 틈으로부터 펀치의 진행과 반대 방향으로 소재를 유출시키는 압출 가공.
3) 복합 압출(FORWARD & BACKWARD EXTRUSION)
전방 압출과 후방 압출을 한 공정에 동시에 시행하는 가공.
4) 충격 압출(IMPACT EXTRUSION)
매우 얇은 살두께의 제품을 만드는 후방 압출 가공으로 연질 금속에 한해서 가공이 가능.
5) 업셋팅(UPSETTING)
소재를 길이 방향으로 압축하여 길이를 감소시킴으로써 길이 방향과 직각 방향으로 소재를 이동•유동시켜 큰 길이 방향과 직각인 단면을 만드는 가공으로 대표적으로 볼트와 리벳이 있음.
6) 압인(COINING)
금속판이나 반제품의 전 표면을 규제하는 밀폐형에 의해 그 표면을 압축하여 형과 똑같은 모양의 요철을 만드는 가공으로 대표적으로 화폐와 메달이 있음.
7) 사이징(SIZING)
형에 의해 소재의 전체 또는 일부에 강한 압력을 가하여 소재에 유동을 일으켜서 제품의 치수와 정도를 향상시키는 가공.
8) 헤딩(HEADING)
봉재의 끝을 업셋팅하여 볼트나 리벳을 만드는 일종의 업셋팅 가공.
9) 스웨이징(SWAGING)
중공축, 중실축 및 강재 등의 소재를 2개 또는 그 이상의 분리형 금형에 삽입한 후 소재의 반경 방향으로 점진적인 반복하중을 가하여 소재의 단면을 변화시키는 가공.
(5) 기타
클램프 장치를 이용하거나 순간적인 충격을 가하거나, 고무나 액체를 이용하여 소재에 변형을 주는 가공법으로 여러 가지 형태의 제품을 만드는데 이점이 있습니다.
특수 장치와 기술이 뒷받침되어야 하기 때문에 가공방법이 어려울 수 있으나 차츰 기술이 발달됨에 따라 복잡한 형상이나 가공시간을 단축과 소재를 절약하기 위해서 시행되고 있습니다.
1) 벌징(BULGING)
통 모양의 용기, 관 등의 측벽을 내부로부터 압력을 가하여 배를 부르게 하는 가공으로 내부에 압력을 가하는 수단으로는 방사상으로 분할된 펀치나 유체, 고무 등을 사용함.
2) 스트레치 드로우 포밍(STRETCH DRAW FORMING)
프레스 금형의 양쪽에 설치된 스트레치 장치에 의해 강판을 항복점 이상으로 늘리고 그 상태에서 드로잉을 시행하는 가공.
3) 하이드로 포밍(HYDRO-FORMING)
펀치만 금형을 사용하고 다이에는 유압으로 지지된 고무판을 사용하는 가공으로 성형이 어려운 모양을 만들 때 사용함.
4) 허프 포밍(HERF FORMING)
여러 가지 허프 장치를 사용하여 초고속으로 시행하는 가공으로 소재의 성형성이 좋아져서 종래의 방법으로 할 수 없던 것을 무리 없이 시행할 수 있음.
이상으로 프레스 금형의 개요를 마치고 다음 연재는 아마도 프레스에 대한 것이 될 것 같습니다.
프레스는 프레스 가공을 하는 데 있어 매우 중요한 기계이며 대량생산을 위해 폭넓게 사용되고 있기 때문에 꼭 집고 넘어가야 할 분야인 것 같습니다.
2020년 04월 21일
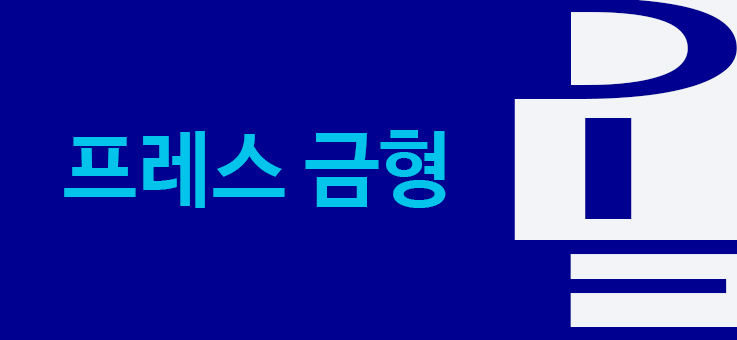
HOME → DIE CATEGORIES →
프레스 금형 1
본격적으로 프레스 금형을 기술하기 전에 프레스 가공(DIE Working)에 따른 분류와 특징 그리고 가공 방법에 대해서 언급을 먼저 하겠습니다.
제1장 프레스 가공
1. 개요
프레스 가공은 프레스를 이용하여 소재를 소성변형시켜 여러 가지 형상으로 만드는 가공법이며 금형, 프레스 기계, 피가공재를 프레스 가공의 3요소라고 합니다.
2. 특징
(1) 복잡한 형상을 간단하게 가공할 수 있음.
(2) 절삭가공에 비해 인성 및 강도가 우수함.
(3) 정밀도가 높고 대량생산이 가능함.
(4) 재료 이용률이 높음.
(5) 가공속도가 빠르고 능률적임.
(6) 절삭가공만큼 숙련된 기술을 요하지 않음.
3. 종류
(1) 전단 가공
전단 가공을 시행할 때에는 클리어런스가 필요하므로 펀치의 외경보다 다이의 내경이 커야 하며 클리어런스는 소재의 두께에 4~12% 정도가 적당합니다.
1) 시어링(SHEARING)
시어링 머신으로 소재의 일부를 잘라내는 작업으로 이 작업 중 스크랩이 거의 없이 규칙적인 배열로 전단하는 공정을 컷 오프라고 함.
2) 블랭킹(BLANKING)
미리 결정되어 있는 윤곽을 전단하는 작업으로 외부에 남는 것은 스크랩이 됨.
소재(왼쪽)와 제품(오른쪽)
3) 파인 블랭킹(FINE BLANKING)
스트리퍼 밑면에 삼각선의 비드를 설치하여 소재를 강하게 눌러 정수압 상태를 만들고 다이와 펀치 사이의 클리어런스를 최대한 없앤 후 상하 양쪽에서 가압하여 고운 전단면과 정밀한 치수를 얻을 수 있는 가공.
나중에 또 언급하겠지만 일반 블랭킹과 파인 블랭킹의 차이점이 무엇인지 궁금할 수 있을 것입니다.
다음과 같이 표로 두 가공법의 차이점을 간략히 설명해보도록 하겠습니다.
일반 블랭킹 | 파인 블랭킹 | |
---|---|---|
전단 면 상태 | 버가 발생함 | 버가 발생하지 않음 |
치수 정밀도 | 미크론 가공 불가능 | 미크론 가공 가능 |
공 정 | 단일 공정만 가능 | 복잡한 여러 공정 가능 |
후 가 공 | 필요 | 불필요 |
원 가 | 높다 | 낮다 |
클리어런스 | 크다 | 0에 가깝다 |
4) 분단(PARTING)
소재의 중심선을 따라 혹은 소재의 사이를 절단하여 동일 형상이 두 개 이상으로 나뉘는 가공.
5) 피어싱
블랭킹과 사용목적이 반대이며 소재에 형을 이용하여 구멍을 뚫는 가공으로 다른 말로 펀칭이라고 하며 떼어낸 부분이 스크랩이 됨.
소재(왼쪽)와 제품(오른쪽)
6) 트리밍(TRIMMING)
중간 또는 최종 프레스 공정에서 제품을 소요 형상으로 만들기 위해 전체 둘레 또는 부분적으로 스크랩 부위를 절단하는 가공.
소재(왼쪽)와 제품(오른쪽)
7) 노칭(NOTCHING)
소재의 가장자리를 여러 가지 모양으로 절단하는 가공.
소재(왼쪽)와 제품(오른쪽)
8) 셰이빙(SHAVING)
1차 가공된 절단면을 다시 전단 금형으로 파단면을 깎아내어 평활하고 깨끗한 전단면을 얻을 수 있는 가공.
소재(왼쪽)와 제품(오른쪽)
9) 루버링(LOUVERING)
펀치와 다이의 한쪽은 전단이 되고 다른쪽은 바늘 창 형상으로 굽히는 가공.
제품
(2) 굽힘 가공
소재에 외력을 가해 재료에 영구 변형을 주어 외력을 제거하여도 본래의 형태로 돌아가지 않도록 하는 가공법이며 신장이 크고 점성이 약한 연질 재료가 적합합니다.
경질 재료일수록 스프링 백이 크고 취성이 있어 굽힘 반지름 부분에 균열이 생기기 쉽고 가공이 어렵습니다.
1) 벤딩(BENDING)
제품의 장식 또는 보강을 목적으로 소재에 변형을 주어 여러 가지 형상으로 굽히는 가공으로 V자, U자, L자, Z자, 채널 굽힘 등이 있음.
2) 포밍(FORMING)
판 두께의 감소를 의식적으로 행하지 않고 소재를 상•하형 사이에 놓고 눌러서 여러 가지 형상을 만드는 가공.
제품
3) 버링(BURRING)
뚫려 있는 구멍의 내경보다 큰 직경의 펀치로 눌러 구멍의 가장자리를 판재의 면과 직각으로 구멍 둘레에 플랜지를 만드는 가공.
4) 시이밍(SEAMING)
두 장에 판재의 단부를 굽히면서 눌러 접합하는 가공법으로 음료수나 통조림 캔 등을 제조할 때 사용.
5) 컬링(CURLING)
판재 또는 용기의 윗부분에 원형 단면의 테두리를 말아 넣는 가공법으로 플랜징과 같은 목적으로 사용.
6) 플랜징(FLANGING)
소재의 가장자리를 구부려 세우는 가공.
소재(왼쪽)와 제품(오른쪽)
7) 비딩(BEADING)
용기 또는 판재의 일부에 장식 또는 보강의 목적으로 줄 모양의 돌기를 넣은 가공.
제품
8) 엠보싱(EMBOSSING)
소재에 두께의 변화를 일으키지 않고 여러 가지 형상의 작은 요철을 만드는 가공.
제품
9) 네킹(NECKING)
원통이나 원형 용기 끝부분의 지름을 감소시키는 가공.
소재(왼쪽)와 제품(오른쪽)
10) 폴딩(FOLDING)
판재의 끝이나 중앙을 90° 이상 구부려 접는 가공.
소재(왼쪽)와 제품(오른쪽)
(3) 성형 가공
성형 가공 또는 드로잉 가공은 블랭킹한 판재를 원통형, 각통형, 반구형 등의 밑면이 있고 이음새가 없는 용기를 만드는 가공법입니다.
드로잉 가공에 적합한 소재는 연성이 좋고 인장강도가 크고 균열이 발생하지 않아야 합니다.
드로잉 가공 시 제품의 원주방향으로 수축이 되면서 길이 방향으로는 늘어나는 현상이 발생하므로 펀치나 다이 날부에 R을 주어 제품에 주름 및 전단 현상이 발생하지 않도록 주의해야 합니다.
1) 드로잉(DRAWING)
평판의 소재에 이음매가 없는 중공 용기를 주름이나 균열이 생기지 않고 다이 안에 펀치를 넣어 성형시키는 가공.

2) 재드로잉(REDRAWING)
드로잉 된 제품의 지름을 감소시키면서 깊이를 증가시키는 가공법으로 가공 방식에 따라 직접 재드로잉과 역(식) 재드로잉으로 구분.
3) 아이어닝(IRONING)
드로잉 가공 후 제품의 두께가 일정하지 않기 때문에 제품의 측벽 두께를 얇고 균일하며 높이를 높게 훑어주는 가공.
4) 리스트라이킹(RESTRIKING)
앞 공정에서 만든 형상을 보다 정확하게 하기 위해 최종 제품 치수로 만드는 가공.
5) 스피닝(SPINNING)
제품의 원형을 선반의 스핀들에 고정하고 원형과 심압대와의 사이에 소재를 끼워서 스핀들과 함께 롤러를 회전시켜 가공.

(4) 압축 가공
펀치와 다이를 이용하여 여러 가지 단면 형상을 가진 솔리드 제품이나 중공 제품을 만드는 가공을 말합니다.
상온에서 소재에 펀치의 압력을 가하여 다이의 구멍이나 펀치와 다이의 틈으로 유동 현상을 일으켜 긴 슬리브 형태의 제품을 한 공정으로 완성합니다.
1)전방 압출(FORWARD EXTRUSION)
다이의 개구부로부터 펀치의 진행 방향으로 소재를 유출시켜 형상을 만드는 압출 가공.
2) 후방 압출(BACKWARD EXTRUSION)
다이와 펀치 사이의 틈으로부터 펀치의 진행과 반대 방향으로 소재를 유출시키는 압출 가공.
3) 복합 압출(FORWARD & BACKWARD EXTRUSION)
전방 압출과 후방 압출을 한 공정에 동시에 시행하는 가공.
4) 충격 압출(IMPACT EXTRUSION)
매우 얇은 살두께의 제품을 만드는 후방 압출 가공으로 연질 금속에 한해서 가공이 가능.
5) 업셋팅(UPSETTING)
소재를 길이 방향으로 압축하여 길이를 감소시킴으로써 길이 방향과 직각 방향으로 소재를 이동•유동시켜 큰 길이 방향과 직각인 단면을 만드는 가공으로 대표적으로 볼트와 리벳이 있음.
6) 압인(COINING)
금속판이나 반제품의 전 표면을 규제하는 밀폐형에 의해 그 표면을 압축하여 형과 똑같은 모양의 요철을 만드는 가공으로 대표적으로 화폐와 메달이 있음.
7) 사이징(SIZING)
형에 의해 소재의 전체 또는 일부에 강한 압력을 가하여 소재에 유동을 일으켜서 제품의 치수와 정도를 향상시키는 가공.
8) 헤딩(HEADING)
봉재의 끝을 업셋팅하여 볼트나 리벳을 만드는 일종의 업셋팅 가공.
9) 스웨이징(SWAGING)
중공축, 중실축 및 강재 등의 소재를 2개 또는 그 이상의 분리형 금형에 삽입한 후 소재의 반경 방향으로 점진적인 반복하중을 가하여 소재의 단면을 변화시키는 가공.
(5) 기타
클램프 장치를 이용하거나 순간적인 충격을 가하거나, 고무나 액체를 이용하여 소재에 변형을 주는 가공법으로 여러 가지 형태의 제품을 만드는데 이점이 있습니다.
특수 장치와 기술이 뒷받침되어야 하기 때문에 가공방법이 어려울 수 있으나 차츰 기술이 발달됨에 따라 복잡한 형상이나 가공시간을 단축과 소재를 절약하기 위해서 시행되고 있습니다.
1) 벌징(BULGING)
통 모양의 용기, 관 등의 측벽을 내부로부터 압력을 가하여 배를 부르게 하는 가공으로 내부에 압력을 가하는 수단으로는 방사상으로 분할된 펀치나 유체, 고무 등을 사용함.
2) 스트레치 드로우 포밍(STRETCH DRAW FORMING)
프레스 금형의 양쪽에 설치된 스트레치 장치에 의해 강판을 항복점 이상으로 늘리고 그 상태에서 드로잉을 시행하는 가공.
3) 하이드로 포밍(HYDRO-FORMING)
펀치만 금형을 사용하고 다이에는 유압으로 지지된 고무판을 사용하는 가공으로 성형이 어려운 모양을 만들 때 사용함.
4) 허프 포밍(HERF FORMING)
여러 가지 허프 장치를 사용하여 초고속으로 시행하는 가공으로 소재의 성형성이 좋아져서 종래의 방법으로 할 수 없던 것을 무리 없이 시행할 수 있음.
이상으로 프레스 금형의 개요를 마치고 다음 연재는 아마도 프레스에 대한 것이 될 것 같습니다.
프레스는 프레스 가공을 하는 데 있어 매우 중요한 기계이며 대량생산을 위해 폭넓게 사용되고 있기 때문에 꼭 집고 넘어가야 할 분야인 것 같습니다.
2020년 04월 21일