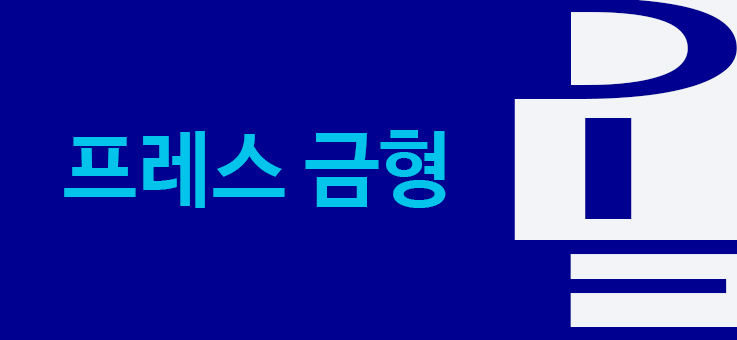
HOME → DIE CATEGORIES →
프레스 금형 10
제9장 전단가공의 특징과 프레스 가공의 부적합 사례
프레스 가공 시 대표적인 가공법인 드로잉, 전단, 굽힘 가공의 부적합 사례의 원인을 파악하고 이에 맞는 대책을 강구하여 가공 공정을 개선함으로써 고품질 고정도의 제품을 생산하는데 무리가 없음을 강조하고자 합니다.
2. 프레스 가공의 부적합 사례
(1) 드로잉가공의 결함 및 대책
1) 용기의 바닥 부분의 파단
(가) 원인
펀치의 코너 반지름이 너무 작음.
블랭크 홀딩력이 너무 큼.
블랭크 치수가 너무 큼.
드로잉률 및 재 드로잉률이 너무 작음.
클리어런스가 너무 작음.
윤활유가 부적당함.
가공속도가 너무 빠름.
블랭크 홀더의 표면 가공 상태가 나쁨.
(나) 대책
펀치의 코너 반지름을 크게 조정하여 용기 모서리부에 응력이 집중되는 것을 방지할 것.
블랭크 홀딩력을 작게 조정하여 블랭크 홀더와 다이면 상에 발생하는 마찰력을 줄일 것.
블랭크 치수를 조정하고 클리어런스 적정치를 구하여 조정할 것.
드로잉률을 조정하고 가공속도를 늦추며 가공방법에 맞는 윤활유를 재 선택.
블랭크 홀더의 표면을 재가공하여 균일한 면이 되도록 할 것.
2) 용기의 다이 코너 반지름 부위 균열
(가) 원인
다이의 코너 반지름이 작고 펀치와 다이 사이의 클리어런스가 충분하지 못함.
다이 코너 반지름의 가공 상태가 나쁨.
(나) 대책
다이 코너 반지름 적정치를 구하여 크기를 키울 것.
펀치와 다이의 클리어런스 적정치를 구하여 적정할 것.
3) 용기의 주름
(가) 원인
블랭크의 크기가 너무 큼.
블랭크 홀딩력이 부족하고 비드 형상 및 위치가 부적절함.
드로잉 공정수가 너무 적음.
다이 코너 반지름이 너무 큼.
(나) 대책
블랭크의 크기를 작게 조정할 것.
최소 블랭크 홀더의 압력을 구하여 블랭크 홀딩력을 조정할 것.
공정수를 늘려서 펀치의 가압력을 감소시킬 것.
다이 코너 반지름 적정치를 구하여 크기를 줄일 것.
대책을 적용한 다음 시험 드로잉 가공을 시행할 것.
4) 용기 선단에 생기는 귀
(가) 원인
소재의 압연 방향에 따른 이방성.
펀치와 다이의 편심.
블랭크 홀더의 압력이 상이함.
(나) 대책
소재를 풀림 처리하여 이방성을 최소화할 것.
펀치와 다이의 맞춤 상태를 조정하여 편심을 제거할 것.
블랭크 홀더의 표면을 재가공하여 균일한 면이 되도록 할 것.
5) 쇼트 마크(SHOCK MARK), STEPRING
(가) 원인
펀치 또는 다이의 코너 반지름이 다름.
다이 코너 반지름의 형상이 매끄럽지 못해 소재 변형에 저항이 있음.
(나) 대책
다이의 코너 반지름 부위를 매끄럽게 가공할 것.
블랭크 홀딩력과 비드의 높이를 조절할 것.
☞ 쇼트 마크란 재드로잉 가공을 하기 전 드로잉 공정에서 소재가 인장 되어 얇아진 펀치 코너 반지름이 재드로잉 가공으로 용기의 벽으로 이동하여 남은 링 모양의 마크를 말함.
(2) 전단가공의 결함 및 대책
1) 금형 트러블
(가) 펀치의 변형 및 파손
ㄱ) 현상
펀치에 가해지는 전단력에 의해 펀치가 소성변형, 마모, 결손의 형태로 손상이 나타남.
ㄴ) 원인
다이와 펀치의 편심.
펀치의 열처리 조건 및 경도 부적당.
펀치의 재질, 가공, 잘못된 설계.
ㄷ) 대책
펀치의 재질과 가공 상태가 나쁠 때 발생하는 현상이므로 펀치의 강도를 높이고 정밀하게 가공할 것.
(나) 펀치의 치우침
ㄱ) 현상
펀치가 펀치 고정판에 수직으로 위치하지 못하고 한 쪽으로 기울어져서 다이와의 클리어런스가 일정하지 않게 되어 제품의 전단면의 상태가 균일하지 못함.
ㄴ) 원인
프레스의 정밀도 낮음.
펀치의 고정 불량.
금형의 안내 불량.
금형의 취급 부주의.
ㄷ) 대책
프레스 슬라이드(램)의 상하 운동이 부적절하고 펀치의 고정 불량, 금형의 안내 불량에 의해 발생되며 프레스의 정밀도를 보완하고 펀치의 고정과 안내를 재조정할 것.
(다) 다이의 손상
ㄱ) 현상
가공조건, 다이 날끝의 경도 등이 부적합하여 다이 날끝의 치핑, 늘어붙음, 마모 등의 손상이 발생함.
ㄴ) 원인
다이의 날끝 경도가 높거나 다이의 재료의 선택이 잘못되었을 경우 다이와 소재의 마찰에 의해 발생함.
다이의 전단 날의 직선부에 발생되는 눌어붙음은 마찰력이 원인임.
다이 날끝의 경도가 너무 높거나 다이의 재료 불량 때문이므로 가공 시 윤활유를 사용하고 다이 날끝에 뜨임 처리를 하여 인성을 부여하고 가공속도를 늦출 필요가 있음.
마모된 다이의 날끝은 재연삭을 할 것.
(라) 제품의 트러블
ㄱ) 블랭크 업(스크랩 상승)
전단가공 시 스크랩이 다이 상면 위로 올라오는 현상.
펀치의 상승 시 발생한 흡입 작용과 하강 사이에 생기는 압상력이 원인임.
단순한 블랭크 형상일 경우에는 펀치에 묻은 윤활유나 정전기로 인하여 스크랩이 펀치의 바닥에 부착되어 발생함.
펀치와 다이 사이의 클리어런스가 한쪽으로 치우칠 경우에도 발생함.
펀치에 셰더 핀을 설치할 것.
다이 랜드(어깨)부에 라운드나 테이퍼를 설치하여 작업 중 펀치로 인한 흡입 작용과 압상력이 발생하지 않도록 할 것.
펀치에 전단각을 설치하여 스크랩이 부착되지 않도록 할 것.
펀치에 공기 구멍을 뚫고 공기를 불어넣어 스크랩이 부착되지 않도록 할 것.
윤활유를 점도가 낮은 것으로 교체할 것.
펀치와 다이 사이의 클리어런스가 한쪽으로 치우치면 스크랩 상승은 물론 펀치도 잘 부러지므로 이를 개선해야 함.
ㄴ) 블랭크 스톱(스크랩 막힘)
전단가공 시 스크랩에 발생한 측방력에 의해 스크랩이 다이에 밀착되어 취출이 이루어지지 않는 현상.
피어싱 가공 시 자주 발생함.
다이 날 끝의 직선부가 너무 긺.
다이 여유각의 형상이 역테이퍼일 경우.
다이 내면의 표면 거칠기가 나쁨.
다이, 백킹 플레이트, 다이 홀더의 중심이 어긋나서 단차가 발생.
배출된 스크랩이 쌓여 봉 모양으로 이어져 떨어질 때 다이 구멍에 막힘.
스크랩이 자기를 뜀.
박판재나 스크랩의 크기가 작으면 무게가 가볍기 때문에 사소한 원인에도 자주 스크랩이 막힘.
다이 날끝의 직선부를 짧게 할 것.
다이 어깨부에 홈을 파거나 라운드 혹은 테이퍼를 설치할 것.
펀치에 전단각을 설치할 것.
다이에 여유각을 충분히 주어 역테이퍼 형상이 되지 않도록 할 것.
다이 내면을 재연삭 하여 표면 조도를 향상시킬 것.
금형의 하형을 재조립하여 어긋난 중심을 맞추거나 재가공을 하여 단차를 제거.
펀치에 공기 구멍을 뚫고 공기를 불어넣어 스크랩이 부착되지 않도록 할 것.
ㄷ) 버
전단 가공은 절삭 가공과 달리 펀치나 다이의 날 끝으로 소재에 전단응력을 발생시켜 파단(균열)을 일으키는 가공.
전단 과정은 소성변형 단계, 전단 단계, 파단 단계로 이루어지며 버는 파단 단계에서 발생함.
버를 완전히 없애는 것은 불가능 하며 다만, 제품의 정밀도, 제조원가, 작업 난이도 등을 고려하여 규제하는 것이 바람직함.
펀치와 다이 사이의 클리어런스가 클 경우.
소재의 재질이 연질일 경우.
펀치와 다이의 날 끝 부근에서 소재가 인장 되지 않으려는 수평방향 저항이 약하여 정상적인 파단이 일어나지 않을 경우.
펀치와 다이의 날끝이 무딘 경우.
클리어런스 적정치를 소재 두께의 5~10%로 조정하고 날끝의 형상과 표면 거칠기 등을 개선할 것.
또는 역누르개를 설치하거나 가공속도를 빠르게 할 것.
정밀전단법을 시행할 것.
소재가 이동하지 못하도록 눌러서 펀치와 다이의 날끝 부근에서 소재에 인장응력이 작용하도록 할 것.
ㄹ) 재료의 변형(휨)
블랭크 아웃이 원활하게 진행되지 않거나 클리어런스가 과대할 때 발생함.
녹아웃 장치의 스프링력이 커서 취출 과정에서 발생함.
다이의 전단각이 너무 클 때도 발생함.
클리어런스 적정치를 선정하여 클리어런스를 줄이고 녹아웃 장치의 스프링 하중이 낮은 스프링으로 교체할 것.
다이 전단각의 크기를 적절하게 줄일 것.
(3) 굽힘가공의 결함 및 대책
1) 굽힘부분의 균열
(가) 원인
굽힘 반지름의 과소.
클리어런스의 과소.
윤활 불량.
다이의 코너 반지름의 형상과 다듬질 불량.
버의 방향이 인장측에 위치함.
(나) 대책
다이의 코너 반지름을 키우고 정밀도를 향상시킬 것.
펀치와 다이 사이에 클리어런스를 소재의 판 두께 이상으로 크게 할 것.
윤활유를 충분히 주입할 것.
버를 제거하거나 버를 압축 방향으로 굽힐 것.
2) 굽힘부분의 변형
(가) 원인
클리어런스의 부적절. (클리어런스가 크면 주름이 발생하고 작으면 두께가 감소함.)
굽힘 반지름이 과대하여 굽힘부 바깥쪽으로 부풀어 오름.
소재 두께의 불균일.
(나) 대책
클리어런스를 적절하게 조정할 것.
굽힘 반지름을 줄일 것.
균일한 판 두께를 가지는 소재를 선택할 것.
구멍이 있는 제품의 구멍 위치 변형은 구멍 중심의 처짐과 구멍의 상대 위치가 변경되어서 발생하는데 이는 굽힘부의 위치와 구멍 간의 거리가 너무 가깝기 때문임.
3) 굽힘부위 치수 불량
(가) 원인
전개 길이의 계산 오류.
V 굽힘일 경우 다이 어깨폭의 과대.
L 굽힘일 경우 측방력의 과대.
U 굽힘일 경우 좌우 다이의 코너 반지름 및 클리어런스의 상이.
(나) 대책
소재의 길이를 재계산 후 금형의 위치결정 장치를 수정할 것.
V 굽힘의 경우 다이의 어깨폭을 적정하게 수정할 것.
L 굽힘의 경우 힐 블록을 설치할 것.
U 굽힘의 경우 좌우 다이의 코너 반지름 크기를 동일하게 재가공하여 일치시키고 클리어런스를 재조정할 것.
☞ 힐 블록(HEEL BLOCK)이란 펀치나 캠이 축 압력을 받을 때 펀치 또는 캠의 휨을 최소화하거나 방지하기 위하여 운동의 축 방향으로 지지하기 위한 블록을 다이에 설치.
(4) 프레스 가공에서의 버 방지 대책
1) 대책 원칙
(가) 파단 발생 위치가 날끝 각에 가까울 것.
내마모성이 높고 열처리를 정확하게 시행한 재료로 펀치와 다이를 제작해야 하고,
날끝의 표면 거칠기 정도를 높여야 하고,
마모가 너무 진행되기 전에 날끝을 재연삭하고,
날끝에 0.5t 정도의 미소 R을 설치하고,
날 표면에 피막을 코팅하여 내마모성을 높이고,
동적 정밀도가 높은 프레스를 사용할 것.
(나) 파단은 펀치, 다이의 쌍방에서 발생하고 도중에 처지지 않을 것.
피가공재의 재질, 판 두께, 윤곽 형상에 맞게 클리어런스를 부여하고,
정밀도와 강성이 높은 형 구조를 선택하고,
컷 오프의 경우에는 측압 대책을 수립하고,
이송 불량, 가공 실수 등을 방지하고,
수평방향의 동적 정밀도가 높은 프레스를 사용할 것.
(다) 날 측면과 재료의 미끄러짐을 좋게 하고 시저의 발생이 없을 것.
다이의 스트레이트 랜드를 짧게 하여 확실하게 릴리빙 하고,
날 측면의 표면 거칠기 정도를 높여야 하고,
피가공재와 친화성이 낮은 형 재료를 사용하고,
클리어런스를 적정하게 수정하고,
피어싱용 공작유를 사용하고,
수직방향의 동적 정밀도가 높은 프레스를 사용할 것.
(라) 날끝 부근의 재료에 인장력이 작용하도록 할 것.
고정 스트리퍼를 가동 스트리퍼로 변경하고,
클리어런스를 작게 설정하고,
브리지를 넓게 하고,
예각으로 교차하는 절단, 분단, 피어싱은 피할 것.
이상으로 프레스 금형의 연재 마치고 다음에는 사출 금형에 대한 연재를 시작할 예정입니다.
2020년 06월 29일
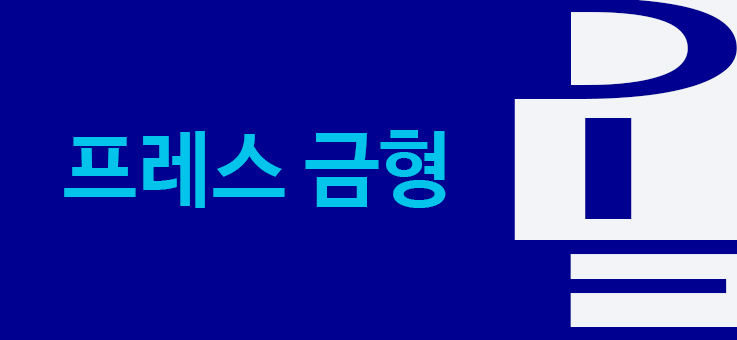
HOME → DIE CATEGORIES →
프레스 금형 10
제9장 전단가공의 특징과 프레스 가공의 부적합 사례
프레스 가공 시 대표적인 가공법인 드로잉, 전단, 굽힘 가공의 부적합 사례의 원인을 파악하고 이에 맞는 대책을 강구하여 가공 공정을 개선함으로써 고품질 고정도의 제품을 생산하는데 무리가 없음을 강조하고자 합니다.
2. 프레스 가공의 부적합 사례
(1) 드로잉가공의 결함 및 대책
1) 용기의 바닥 부분의 파단
(가) 원인
펀치의 코너 반지름이 너무 작음.
블랭크 홀딩력이 너무 큼.
블랭크 치수가 너무 큼.
드로잉률 및 재 드로잉률이 너무 작음.
클리어런스가 너무 작음.
윤활유가 부적당함.
가공속도가 너무 빠름.
블랭크 홀더의 표면 가공 상태가 나쁨.
(나) 대책
펀치의 코너 반지름을 크게 조정하여 용기 모서리부에 응력이 집중되는 것을 방지할 것.
블랭크 홀딩력을 작게 조정하여 블랭크 홀더와 다이면 상에 발생하는 마찰력을 줄일 것.
블랭크 치수를 조정하고 클리어런스 적정치를 구하여 조정할 것.
드로잉률을 조정하고 가공속도를 늦추며 가공방법에 맞는 윤활유를 재 선택.
블랭크 홀더의 표면을 재가공하여 균일한 면이 되도록 할 것.
2) 용기의 다이 코너 반지름 부위 균열
(가) 원인
다이의 코너 반지름이 작고 펀치와 다이 사이의 클리어런스가 충분하지 못함.
다이 코너 반지름의 가공 상태가 나쁨.
(나) 대책
다이 코너 반지름 적정치를 구하여 크기를 키울 것.
펀치와 다이의 클리어런스 적정치를 구하여 적정할 것.
3) 용기의 주름
(가) 원인
블랭크의 크기가 너무 큼.
블랭크 홀딩력이 부족하고 비드 형상 및 위치가 부적절함.
드로잉 공정수가 너무 적음.
다이 코너 반지름이 너무 큼.
(나) 대책
블랭크의 크기를 작게 조정할 것.
최소 블랭크 홀더의 압력을 구하여 블랭크 홀딩력을 조정할 것.
공정수를 늘려서 펀치의 가압력을 감소시킬 것.
다이 코너 반지름 적정치를 구하여 크기를 줄일 것.
대책을 적용한 다음 시험 드로잉 가공을 시행할 것.
4) 용기 선단에 생기는 귀
(가) 원인
소재의 압연 방향에 따른 이방성.
펀치와 다이의 편심.
블랭크 홀더의 압력이 상이함.
(나) 대책
소재를 풀림 처리하여 이방성을 최소화할 것.
펀치와 다이의 맞춤 상태를 조정하여 편심을 제거할 것.
블랭크 홀더의 표면을 재가공하여 균일한 면이 되도록 할 것.
5) 쇼트 마크(SHOCK MARK), STEPRING
(가) 원인
펀치 또는 다이의 코너 반지름이 다름.
다이 코너 반지름의 형상이 매끄럽지 못해 소재 변형에 저항이 있음.
(나) 대책
다이의 코너 반지름 부위를 매끄럽게 가공할 것.
블랭크 홀딩력과 비드의 높이를 조절할 것.
☞ 쇼트 마크란 재드로잉 가공을 하기 전 드로잉 공정에서 소재가 인장 되어 얇아진 펀치 코너 반지름이 재드로잉 가공으로 용기의 벽으로 이동하여 남은 링 모양의 마크를 말함.
(2) 전단가공의 결함 및 대책
1) 금형 트러블
(가) 펀치의 변형 및 파손
ㄱ) 현상
펀치에 가해지는 전단력에 의해 펀치가 소성변형, 마모, 결손의 형태로 손상이 나타남.
ㄴ) 원인
다이와 펀치의 편심.
펀치의 열처리 조건 및 경도 부적당.
펀치의 재질, 가공, 잘못된 설계.
ㄷ) 대책
펀치의 재질과 가공 상태가 나쁠 때 발생하는 현상이므로 펀치의 강도를 높이고 정밀하게 가공할 것.
(나) 펀치의 치우침
ㄱ) 현상
펀치가 펀치 고정판에 수직으로 위치하지 못하고 한 쪽으로 기울어져서 다이와의 클리어런스가 일정하지 않게 되어 제품의 전단면의 상태가 균일하지 못함.
ㄴ) 원인
프레스의 정밀도 낮음.
펀치의 고정 불량.
금형의 안내 불량.
금형의 취급 부주의.
ㄷ) 대책
프레스 슬라이드(램)의 상하 운동이 부적절하고 펀치의 고정 불량, 금형의 안내 불량에 의해 발생되며 프레스의 정밀도를 보완하고 펀치의 고정과 안내를 재조정할 것.
(다) 다이의 손상
ㄱ) 현상
가공조건, 다이 날끝의 경도 등이 부적합하여 다이 날끝의 치핑, 늘어붙음, 마모 등의 손상이 발생함.
ㄴ) 원인
다이의 날끝 경도가 높거나 다이의 재료의 선택이 잘못되었을 경우 다이와 소재의 마찰에 의해 발생함.
다이의 전단 날의 직선부에 발생되는 눌어붙음은 마찰력이 원인임.
다이 날끝의 경도가 너무 높거나 다이의 재료 불량 때문이므로 가공 시 윤활유를 사용하고 다이 날끝에 뜨임 처리를 하여 인성을 부여하고 가공속도를 늦출 필요가 있음.
마모된 다이의 날끝은 재연삭을 할 것.
(라) 제품의 트러블
ㄱ) 블랭크 업(스크랩 상승)
전단가공 시 스크랩이 다이 상면 위로 올라오는 현상.
펀치의 상승 시 발생한 흡입 작용과 하강 사이에 생기는 압상력이 원인임.
단순한 블랭크 형상일 경우에는 펀치에 묻은 윤활유나 정전기로 인하여 스크랩이 펀치의 바닥에 부착되어 발생함.
펀치와 다이 사이의 클리어런스가 한쪽으로 치우칠 경우에도 발생함.
펀치에 셰더 핀을 설치할 것.
다이 랜드(어깨)부에 라운드나 테이퍼를 설치하여 작업 중 펀치로 인한 흡입 작용과 압상력이 발생하지 않도록 할 것.
펀치에 전단각을 설치하여 스크랩이 부착되지 않도록 할 것.
펀치에 공기 구멍을 뚫고 공기를 불어넣어 스크랩이 부착되지 않도록 할 것.
윤활유를 점도가 낮은 것으로 교체할 것.
펀치와 다이 사이의 클리어런스가 한쪽으로 치우치면 스크랩 상승은 물론 펀치도 잘 부러지므로 이를 개선해야 함.
ㄴ) 블랭크 스톱(스크랩 막힘)
전단가공 시 스크랩에 발생한 측방력에 의해 스크랩이 다이에 밀착되어 취출이 이루어지지 않는 현상.
피어싱 가공 시 자주 발생함.
다이 날 끝의 직선부가 너무 긺.
다이 여유각의 형상이 역테이퍼일 경우.
다이 내면의 표면 거칠기가 나쁨.
다이, 백킹 플레이트, 다이 홀더의 중심이 어긋나서 단차가 발생.
배출된 스크랩이 쌓여 봉 모양으로 이어져 떨어질 때 다이 구멍에 막힘.
스크랩이 자기를 뜀.
박판재나 스크랩의 크기가 작으면 무게가 가볍기 때문에 사소한 원인에도 자주 스크랩이 막힘.
다이 날끝의 직선부를 짧게 할 것.
다이 어깨부에 홈을 파거나 라운드 혹은 테이퍼를 설치할 것.
펀치에 전단각을 설치할 것.
다이에 여유각을 충분히 주어 역테이퍼 형상이 되지 않도록 할 것.
다이 내면을 재연삭 하여 표면 조도를 향상시킬 것.
금형의 하형을 재조립하여 어긋난 중심을 맞추거나 재가공을 하여 단차를 제거.
펀치에 공기 구멍을 뚫고 공기를 불어넣어 스크랩이 부착되지 않도록 할 것.
ㄷ) 버
전단 가공은 절삭 가공과 달리 펀치나 다이의 날 끝으로 소재에 전단응력을 발생시켜 파단(균열)을 일으키는 가공.
전단 과정은 소성변형 단계, 전단 단계, 파단 단계로 이루어지며 버는 파단 단계에서 발생함.
버를 완전히 없애는 것은 불가능 하며 다만, 제품의 정밀도, 제조원가, 작업 난이도 등을 고려하여 규제하는 것이 바람직함.
펀치와 다이 사이의 클리어런스가 클 경우.
소재의 재질이 연질일 경우.
펀치와 다이의 날 끝 부근에서 소재가 인장 되지 않으려는 수평방향 저항이 약하여 정상적인 파단이 일어나지 않을 경우.
펀치와 다이의 날끝이 무딘 경우.
클리어런스 적정치를 소재 두께의 5~10%로 조정하고 날끝의 형상과 표면 거칠기 등을 개선할 것.
또는 역누르개를 설치하거나 가공속도를 빠르게 할 것.
정밀전단법을 시행할 것.
소재가 이동하지 못하도록 눌러서 펀치와 다이의 날끝 부근에서 소재에 인장응력이 작용하도록 할 것.
ㄹ) 재료의 변형(휨)
블랭크 아웃이 원활하게 진행되지 않거나 클리어런스가 과대할 때 발생함.
녹아웃 장치의 스프링력이 커서 취출 과정에서 발생함.
다이의 전단각이 너무 클 때도 발생함.
클리어런스 적정치를 선정하여 클리어런스를 줄이고 녹아웃 장치의 스프링 하중이 낮은 스프링으로 교체할 것.
다이 전단각의 크기를 적절하게 줄일 것.
(3) 굽힘가공의 결함 및 대책
1) 굽힘부분의 균열
(가) 원인
굽힘 반지름의 과소.
클리어런스의 과소.
윤활 불량.
다이의 코너 반지름의 형상과 다듬질 불량.
버의 방향이 인장측에 위치함.
(나) 대책
다이의 코너 반지름을 키우고 정밀도를 향상시킬 것.
펀치와 다이 사이에 클리어런스를 소재의 판 두께 이상으로 크게 할 것.
윤활유를 충분히 주입할 것.
버를 제거하거나 버를 압축 방향으로 굽힐 것.
2) 굽힘부분의 변형
(가) 원인
클리어런스의 부적절. (클리어런스가 크면 주름이 발생하고 작으면 두께가 감소함.)
굽힘 반지름이 과대하여 굽힘부 바깥쪽으로 부풀어 오름.
소재 두께의 불균일.
(나) 대책
클리어런스를 적절하게 조정할 것.
굽힘 반지름을 줄일 것.
균일한 판 두께를 가지는 소재를 선택할 것.
구멍이 있는 제품의 구멍 위치 변형은 구멍 중심의 처짐과 구멍의 상대 위치가 변경되어서 발생하는데 이는 굽힘부의 위치와 구멍 간의 거리가 너무 가깝기 때문임.
3) 굽힘부위 치수 불량
(가) 원인
전개 길이의 계산 오류.
V 굽힘일 경우 다이 어깨폭의 과대.
L 굽힘일 경우 측방력의 과대.
U 굽힘일 경우 좌우 다이의 코너 반지름 및 클리어런스의 상이.
(나) 대책
소재의 길이를 재계산 후 금형의 위치결정 장치를 수정할 것.
V 굽힘의 경우 다이의 어깨폭을 적정하게 수정할 것.
L 굽힘의 경우 힐 블록을 설치할 것.
U 굽힘의 경우 좌우 다이의 코너 반지름 크기를 동일하게 재가공하여 일치시키고 클리어런스를 재조정할 것.
☞ 힐 블록(HEEL BLOCK)이란 펀치나 캠이 축 압력을 받을 때 펀치 또는 캠의 휨을 최소화하거나 방지하기 위하여 운동의 축 방향으로 지지하기 위한 블록을 다이에 설치.
(4) 프레스 가공에서의 버 방지 대책
1) 대책 원칙
(가) 파단 발생 위치가 날끝 각에 가까울 것.
내마모성이 높고 열처리를 정확하게 시행한 재료로 펀치와 다이를 제작해야 하고,
날끝의 표면 거칠기 정도를 높여야 하고,
마모가 너무 진행되기 전에 날끝을 재연삭하고,
날끝에 0.5t 정도의 미소 R을 설치하고,
날 표면에 피막을 코팅하여 내마모성을 높이고,
동적 정밀도가 높은 프레스를 사용할 것.
(나) 파단은 펀치, 다이의 쌍방에서 발생하고 도중에 처지지 않을 것.
피가공재의 재질, 판 두께, 윤곽 형상에 맞게 클리어런스를 부여하고,
정밀도와 강성이 높은 형 구조를 선택하고,
컷 오프의 경우에는 측압 대책을 수립하고,
이송 불량, 가공 실수 등을 방지하고,
수평방향의 동적 정밀도가 높은 프레스를 사용할 것.
(다) 날 측면과 재료의 미끄러짐을 좋게 하고 시저의 발생이 없을 것.
다이의 스트레이트 랜드를 짧게 하여 확실하게 릴리빙 하고,
날 측면의 표면 거칠기 정도를 높여야 하고,
피가공재와 친화성이 낮은 형 재료를 사용하고,
클리어런스를 적정하게 수정하고,
피어싱용 공작유를 사용하고,
수직방향의 동적 정밀도가 높은 프레스를 사용할 것.
(라) 날끝 부근의 재료에 인장력이 작용하도록 할 것.
고정 스트리퍼를 가동 스트리퍼로 변경하고,
클리어런스를 작게 설정하고,
브리지를 넓게 하고,
예각으로 교차하는 절단, 분단, 피어싱은 피할 것.
이상으로 프레스 금형의 연재 마치고 다음에는 사출 금형에 대한 연재를 시작할 예정입니다.
2020년 06월 29일
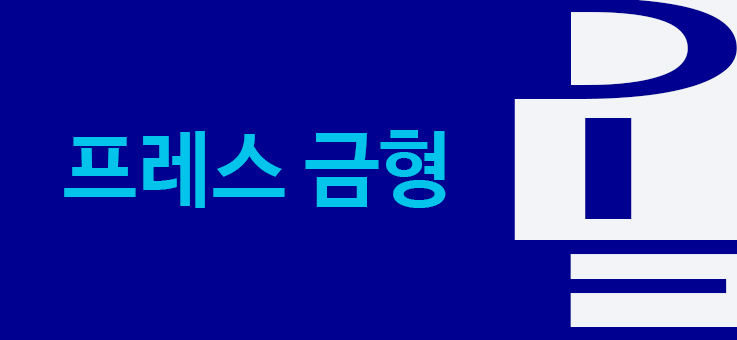
HOME → DIE CATEGORIES →
프레스 금형 10
제9장 전단가공의 특징과 프레스 가공의 부적합 사례
프레스 가공 시 대표적인 가공법인 드로잉, 전단, 굽힘 가공의 부적합 사례의 원인을 파악하고 이에 맞는 대책을 강구하여 가공 공정을 개선함으로써 고품질 고정도의 제품을 생산하는데 무리가 없음을 강조하고자 합니다.
2. 프레스 가공의 부적합 사례
(1) 드로잉가공의 결함 및 대책
1) 용기의 바닥 부분의 파단
(가) 원인
펀치의 코너 반지름이 너무 작음.
블랭크 홀딩력이 너무 큼.
블랭크 치수가 너무 큼.
드로잉률 및 재 드로잉률이 너무 작음.
클리어런스가 너무 작음.
윤활유가 부적당함.
가공속도가 너무 빠름.
블랭크 홀더의 표면 가공 상태가 나쁨.
(나) 대책
펀치의 코너 반지름을 크게 조정하여 용기 모서리부에 응력이 집중되는 것을 방지할 것.
블랭크 홀딩력을 작게 조정하여 블랭크 홀더와 다이면 상에 발생하는 마찰력을 줄일 것.
블랭크 치수를 조정하고 클리어런스 적정치를 구하여 조정할 것.
드로잉률을 조정하고 가공속도를 늦추며 가공방법에 맞는 윤활유를 재 선택.
블랭크 홀더의 표면을 재가공하여 균일한 면이 되도록 할 것.
2) 용기의 다이 코너 반지름 부위 균열
(가) 원인
다이의 코너 반지름이 작고 펀치와 다이 사이의 클리어런스가 충분하지 못함.
다이 코너 반지름의 가공 상태가 나쁨.
(나) 대책
다이 코너 반지름 적정치를 구하여 크기를 키울 것.
펀치와 다이의 클리어런스 적정치를 구하여 적정할 것.
3) 용기의 주름
(가) 원인
블랭크의 크기가 너무 큼.
블랭크 홀딩력이 부족하고 비드 형상 및 위치가 부적절함.
드로잉 공정수가 너무 적음.
다이 코너 반지름이 너무 큼.
(나) 대책
블랭크의 크기를 작게 조정할 것.
최소 블랭크 홀더의 압력을 구하여 블랭크 홀딩력을 조정할 것.
공정수를 늘려서 펀치의 가압력을 감소시킬 것.
다이 코너 반지름 적정치를 구하여 크기를 줄일 것.
대책을 적용한 다음 시험 드로잉 가공을 시행할 것.
4) 용기 선단에 생기는 귀
(가) 원인
소재의 압연 방향에 따른 이방성.
펀치와 다이의 편심.
블랭크 홀더의 압력이 상이함.
(나) 대책
소재를 풀림 처리하여 이방성을 최소화할 것.
펀치와 다이의 맞춤 상태를 조정하여 편심을 제거할 것.
블랭크 홀더의 표면을 재가공하여 균일한 면이 되도록 할 것.
5) 쇼트 마크(SHOCK MARK), STEPRING
(가) 원인
펀치 또는 다이의 코너 반지름이 다름.
다이 코너 반지름의 형상이 매끄럽지 못해 소재 변형에 저항이 있음.
(나) 대책
다이의 코너 반지름 부위를 매끄럽게 가공할 것.
블랭크 홀딩력과 비드의 높이를 조절할 것.
☞ 쇼트 마크란 재드로잉 가공을 하기 전 드로잉 공정에서 소재가 인장 되어 얇아진 펀치 코너 반지름이 재드로잉 가공으로 용기의 벽으로 이동하여 남은 링 모양의 마크를 말함.
(2) 전단가공의 결함 및 대책
1) 금형 트러블
(가) 펀치의 변형 및 파손
ㄱ) 현상
펀치에 가해지는 전단력에 의해 펀치가 소성변형, 마모, 결손의 형태로 손상이 나타남.
ㄴ) 원인
다이와 펀치의 편심.
펀치의 열처리 조건 및 경도 부적당.
펀치의 재질, 가공, 잘못된 설계.
ㄷ) 대책
펀치의 재질과 가공 상태가 나쁠 때 발생하는 현상이므로 펀치의 강도를 높이고 정밀하게 가공할 것.
(나) 펀치의 치우침
ㄱ) 현상
펀치가 펀치 고정판에 수직으로 위치하지 못하고 한 쪽으로 기울어져서 다이와의 클리어런스가 일정하지 않게 되어 제품의 전단면의 상태가 균일하지 못함.
ㄴ) 원인
프레스의 정밀도 낮음.
펀치의 고정 불량.
금형의 안내 불량.
금형의 취급 부주의.
ㄷ) 대책
프레스 슬라이드(램)의 상하 운동이 부적절하고 펀치의 고정 불량, 금형의 안내 불량에 의해 발생되며 프레스의 정밀도를 보완하고 펀치의 고정과 안내를 재조정할 것.
(다) 다이의 손상
ㄱ) 현상
가공조건, 다이 날끝의 경도 등이 부적합하여 다이 날끝의 치핑, 늘어붙음, 마모 등의 손상이 발생함.
ㄴ) 원인
다이의 날끝 경도가 높거나 다이의 재료의 선택이 잘못되었을 경우 다이와 소재의 마찰에 의해 발생함.
다이의 전단 날의 직선부에 발생되는 눌어붙음은 마찰력이 원인임.
다이 날끝의 경도가 너무 높거나 다이의 재료 불량 때문이므로 가공 시 윤활유를 사용하고 다이 날끝에 뜨임 처리를 하여 인성을 부여하고 가공속도를 늦출 필요가 있음.
마모된 다이의 날끝은 재연삭을 할 것.
(라) 제품의 트러블
ㄱ) 블랭크 업(스크랩 상승)
전단가공 시 스크랩이 다이 상면 위로 올라오는 현상.
펀치의 상승 시 발생한 흡입 작용과 하강 사이에 생기는 압상력이 원인임.
단순한 블랭크 형상일 경우에는 펀치에 묻은 윤활유나 정전기로 인하여 스크랩이 펀치의 바닥에 부착되어 발생함.
펀치와 다이 사이의 클리어런스가 한쪽으로 치우칠 경우에도 발생함.
펀치에 셰더 핀을 설치할 것.
다이 랜드(어깨)부에 라운드나 테이퍼를 설치하여 작업 중 펀치로 인한 흡입 작용과 압상력이 발생하지 않도록 할 것.
펀치에 전단각을 설치하여 스크랩이 부착되지 않도록 할 것.
펀치에 공기 구멍을 뚫고 공기를 불어넣어 스크랩이 부착되지 않도록 할 것.
윤활유를 점도가 낮은 것으로 교체할 것.
펀치와 다이 사이의 클리어런스가 한쪽으로 치우치면 스크랩 상승은 물론 펀치도 잘 부러지므로 이를 개선해야 함.
ㄴ) 블랭크 스톱(스크랩 막힘)
전단가공 시 스크랩에 발생한 측방력에 의해 스크랩이 다이에 밀착되어 취출이 이루어지지 않는 현상.
피어싱 가공 시 자주 발생함.
다이 날 끝의 직선부가 너무 긺.
다이 여유각의 형상이 역테이퍼일 경우.
다이 내면의 표면 거칠기가 나쁨.
다이, 백킹 플레이트, 다이 홀더의 중심이 어긋나서 단차가 발생.
배출된 스크랩이 쌓여 봉 모양으로 이어져 떨어질 때 다이 구멍에 막힘.
스크랩이 자기를 뜀.
박판재나 스크랩의 크기가 작으면 무게가 가볍기 때문에 사소한 원인에도 자주 스크랩이 막힘.
다이 날끝의 직선부를 짧게 할 것.
다이 어깨부에 홈을 파거나 라운드 혹은 테이퍼를 설치할 것.
펀치에 전단각을 설치할 것.
다이에 여유각을 충분히 주어 역테이퍼 형상이 되지 않도록 할 것.
다이 내면을 재연삭 하여 표면 조도를 향상시킬 것.
금형의 하형을 재조립하여 어긋난 중심을 맞추거나 재가공을 하여 단차를 제거.
펀치에 공기 구멍을 뚫고 공기를 불어넣어 스크랩이 부착되지 않도록 할 것.
ㄷ) 버
전단 가공은 절삭 가공과 달리 펀치나 다이의 날 끝으로 소재에 전단응력을 발생시켜 파단(균열)을 일으키는 가공.
전단 과정은 소성변형 단계, 전단 단계, 파단 단계로 이루어지며 버는 파단 단계에서 발생함.
버를 완전히 없애는 것은 불가능 하며 다만, 제품의 정밀도, 제조원가, 작업 난이도 등을 고려하여 규제하는 것이 바람직함.
펀치와 다이 사이의 클리어런스가 클 경우.
소재의 재질이 연질일 경우.
펀치와 다이의 날 끝 부근에서 소재가 인장 되지 않으려는 수평방향 저항이 약하여 정상적인 파단이 일어나지 않을 경우.
펀치와 다이의 날끝이 무딘 경우.
클리어런스 적정치를 소재 두께의 5~10%로 조정하고 날끝의 형상과 표면 거칠기 등을 개선할 것.
또는 역누르개를 설치하거나 가공속도를 빠르게 할 것.
정밀전단법을 시행할 것.
소재가 이동하지 못하도록 눌러서 펀치와 다이의 날끝 부근에서 소재에 인장응력이 작용하도록 할 것.
ㄹ) 재료의 변형(휨)
블랭크 아웃이 원활하게 진행되지 않거나 클리어런스가 과대할 때 발생함.
녹아웃 장치의 스프링력이 커서 취출 과정에서 발생함.
다이의 전단각이 너무 클 때도 발생함.
클리어런스 적정치를 선정하여 클리어런스를 줄이고 녹아웃 장치의 스프링 하중이 낮은 스프링으로 교체할 것.
다이 전단각의 크기를 적절하게 줄일 것.
(3) 굽힘가공의 결함 및 대책
1) 굽힘부분의 균열
(가) 원인
굽힘 반지름의 과소.
클리어런스의 과소.
윤활 불량.
다이의 코너 반지름의 형상과 다듬질 불량.
버의 방향이 인장측에 위치함.
(나) 대책
다이의 코너 반지름을 키우고 정밀도를 향상시킬 것.
펀치와 다이 사이에 클리어런스를 소재의 판 두께 이상으로 크게 할 것.
윤활유를 충분히 주입할 것.
버를 제거하거나 버를 압축 방향으로 굽힐 것.
2) 굽힘부분의 변형
(가) 원인
클리어런스의 부적절. (클리어런스가 크면 주름이 발생하고 작으면 두께가 감소함.)
굽힘 반지름이 과대하여 굽힘부 바깥쪽으로 부풀어 오름.
소재 두께의 불균일.
(나) 대책
클리어런스를 적절하게 조정할 것.
굽힘 반지름을 줄일 것.
균일한 판 두께를 가지는 소재를 선택할 것.
구멍이 있는 제품의 구멍 위치 변형은 구멍 중심의 처짐과 구멍의 상대 위치가 변경되어서 발생하는데 이는 굽힘부의 위치와 구멍 간의 거리가 너무 가깝기 때문임.
3) 굽힘부위 치수 불량
(가) 원인
전개 길이의 계산 오류.
V 굽힘일 경우 다이 어깨폭의 과대.
L 굽힘일 경우 측방력의 과대.
U 굽힘일 경우 좌우 다이의 코너 반지름 및 클리어런스의 상이.
(나) 대책
소재의 길이를 재계산 후 금형의 위치결정 장치를 수정할 것.
V 굽힘의 경우 다이의 어깨폭을 적정하게 수정할 것.
L 굽힘의 경우 힐 블록을 설치할 것.
U 굽힘의 경우 좌우 다이의 코너 반지름 크기를 동일하게 재가공하여 일치시키고 클리어런스를 재조정할 것.
☞ 힐 블록(HEEL BLOCK)이란 펀치나 캠이 축 압력을 받을 때 펀치 또는 캠의 휨을 최소화하거나 방지하기 위하여 운동의 축 방향으로 지지하기 위한 블록을 다이에 설치.
(4) 프레스 가공에서의 버 방지 대책
1) 대책 원칙
(가) 파단 발생 위치가 날끝 각에 가까울 것.
내마모성이 높고 열처리를 정확하게 시행한 재료로 펀치와 다이를 제작해야 하고,
날끝의 표면 거칠기 정도를 높여야 하고,
마모가 너무 진행되기 전에 날끝을 재연삭하고,
날끝에 0.5t 정도의 미소 R을 설치하고,
날 표면에 피막을 코팅하여 내마모성을 높이고,
동적 정밀도가 높은 프레스를 사용할 것.
(나) 파단은 펀치, 다이의 쌍방에서 발생하고 도중에 처지지 않을 것.
피가공재의 재질, 판 두께, 윤곽 형상에 맞게 클리어런스를 부여하고,
정밀도와 강성이 높은 형 구조를 선택하고,
컷 오프의 경우에는 측압 대책을 수립하고,
이송 불량, 가공 실수 등을 방지하고,
수평방향의 동적 정밀도가 높은 프레스를 사용할 것.
(다) 날 측면과 재료의 미끄러짐을 좋게 하고 시저의 발생이 없을 것.
다이의 스트레이트 랜드를 짧게 하여 확실하게 릴리빙 하고,
날 측면의 표면 거칠기 정도를 높여야 하고,
피가공재와 친화성이 낮은 형 재료를 사용하고,
클리어런스를 적정하게 수정하고,
피어싱용 공작유를 사용하고,
수직방향의 동적 정밀도가 높은 프레스를 사용할 것.
(라) 날끝 부근의 재료에 인장력이 작용하도록 할 것.
고정 스트리퍼를 가동 스트리퍼로 변경하고,
클리어런스를 작게 설정하고,
브리지를 넓게 하고,
예각으로 교차하는 절단, 분단, 피어싱은 피할 것.
이상으로 프레스 금형의 연재 마치고 다음에는 사출 금형에 대한 연재를 시작할 예정입니다.
2020년 06월 29일