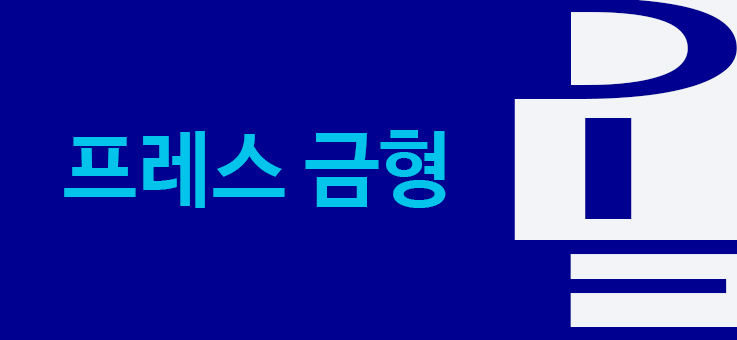
HOME → DIE CATEGORIES →
프레스 금형 9
제9장 전단가공 특징과 프레스 가공의 부적합 사례
1. 전단가공의 특징
(1) 전단현상
1) 개요
전단가공(SHEARING)은 목적에 알맞은 형상의 공구로 금속 소재에 전단변형을 주어 최종적으로 파단을 일으켜 필요한 부분을 분리시키는 가공법으로 소재는 펀치와 다이 사이에서 소성변형과 전단 단계를 거쳐 파단됨.
2) 전단 과정
(가) 탄성변형 단계
펀치가 하강함에 따라 소재는 펀치와 접촉하여 소재 내부에 저항이 발생함.
펀치가 더욱 하강하면 소재의 표면에서는 인장응력이, 다이 및 펀치의 접촉면에서는 압축응력이 발생함.
(나) 소성변형 단계
다이 및 펀치의 접촉면에서 발생하는 압축응력은 가공이 진행됨에 따라 소재의 탄성한도를 넘어 소성변형을 일으킴.
이때 소재는 펀치의 날끝에 의하여 굽혀지면서 눌리게 되는데 이를 눌린면(ROLL OVER)이라 함.
(다) 전단 단계
소성변형이 진행된 소재에 가공을 좀 더 진행하면 전단 날끝의 압축응력이 전단강도를 넘어 감소된 면적의 재료가 전단이 됨.
소성변형을 거쳐 전단 단계로 가공이 진행될 때 펀치가 소재 속으로 들어가면 수직•수평하중을 받게 되고 이때의 수평하중이 소재의 측벽을 매끄럽게 하는데 이를 버니싱(BURNISHING)이라 함.
(라) 파단 단계
전단 단계에서 가공이 더 진행되면 소재의 전단강도 이상의 전단응력이 발생하여 소재는 상•하 균열이 커지면서 파단됨.
소재는 완전 분리되어 펀치는 소재의 절단부를 통과해서 다이 속으로 유입되고 절단된 소재는 낙하됨.
3) 전단가공의 단면 형상
(가) 개요
전단가공(SHEARING)은 소재의 표면에 압력을 가해 전단응력을 발생시켜 파단 현상을 일으키게 하여 소재와 분리하는 가공인데 전단 과정을 거쳐 전단된 블랭크의 형상은 처짐, 전단면, 파단면, 버로 구성됨.
(나) 단면 형상
펀치가 소재에 닿아 압력을 가하면 소재는 압축응력을 받아서 변형되어 항복되는데 이와 같이 소재가 소성변형하면서 소재의 표면에 눌린 자국으로 인하여 처짐이 발생함.
처짐량은 클리어런스를 작게 하여 그 양을 감소시킬 수 있으나 일반적으로 판 두께의 10~20% 정도를 차지함.
펀치가 소재에 침입하면 펀치의 가압력과 측방력의 작용으로 소재는 압축응력과 인장응력에 의해 쐐기작용을 받게 됨.
이로 인해 크랙이 일어나기까지 펀치에 의하여 전단된 면은 광택이 생기게 되고 전단면은 표면에 대해 90º로 형성되며 판 두께의 25~50% 정도를 차지함.
펀치가 하강하면 점점 저항력이 증가하여 최고 하중점에 도달하면 날끝부분의 집중력 때문에 소재 내부의 날끝부분에서 균열이 발생함.
균열이 발생한 면은 인장파단으로 인하여 표면이 거칠지는데 전단면이 증가하면 파단면이 감소하고 전단면이 감소하면 파단면이 증가됨.
처짐과 인장파단의 최후 부분으로 버가 발생함.
버는 제품의 정도를 향상시키려면 발생되지 말아야 하나 전단 형상에서 버를 없애는 것은 불가능하고 일반적으로 판 두께의 10% 이내로 규제하는 것이 적절함.
날끝의 무딘 정도와 소재의 연성에 비례하여 버의 높이가 높아지고 이 값에 의해 금형 수정 시기의 판단 척도가 될 수 있음.
프로그레시브 금형의 경우에는 피어싱된 구멍과 블랭킹된 외곽선에 발생하는 버의 방향은 서로 반대이고 콤파운드 금형의 경우에는 피어싱된 구멍과 블랭킹된 외곽선에 발생하는 버의 방향이 같음.
(다) 전단면 형성의 영향을 미치는 인자
소재가 경질이면 처짐과 전단면이 차지하는 비중이 작아지고 파단면은 커짐.
반면에 연질이면 광택이 있는 전단면이 차지하는 비중 뿐만 아니라 처짐과 버도 커짐.
클리어런스가 커지면 파단면의 각도와 처짐은 약간 커지지만 버는 그다지 커지지 않음.
더욱 클리어런스가 커져 임계점을 넘어가면 버와 처짐이 갑자기 커져서 제품에 휨이 발생함.
블랭크 홀더를 설치하여 소재를 고정 지지하면 동일한 클리어런스일 때 자유 지지에 비해 전단면은 커지고 처짐도 약간 커짐.
녹아웃을 설치하면 전단면은 커지고 처짐은 작아져서 전단면의 형상이 상대적으로 양호함.
(2) 전단가공의 클리어런스
1) 개요
프레스 금형에서의 클리어런스는 펀치와 다이의 한쪽 틈새의 양을 의미하며 전단가공(SHEARING)에서 좋은 전단면을 얻기 위해서는 클리어런스의 선택이 무엇보다 중요함.
클리어런스가 클수록 전단력은 감소하나 굽힘량이 많아져서 2중의 전단면이 발생할 수 있고 또한 클리어런스는 제품의 단면 형상, 전단력, 치수 정밀도와 밀접한 관계가 있음.
2) 클리어런스와 단면형상
전단된 제품의 단면은 처짐, 전단면, 파단면, 버로 구성되어 있는데 경질 소재는 처짐과 전단면이 차지하는 비중이 적어서 단면의 대부분을 파단면이 차지함.
같은 소재에서는 클리어런스의 양에 따라서 단면 형상이 상이함.
클리어런스가 너무 작으면 상하의 균열이 잘 맞지 않아 단면 상태가 나빠지고 반대로 너무 크면 굽힘 모멘트가 켜져서 제품의 정밀도가 나빠지며 파단면이 증가함.
3) 클리어런스와 전단저항
전단가공(SHEARING)에서는 클리어런스가 커지면 전단저항이 작아지는데 이는 펀치와 다이 사이의 클리어런스가 커지는 만큼 측방력도 같이 커지기 때문에 균열이 발생하는 쐐기효과를 유발하여 전단저항이 작아짐.
전단저항은 클러어런스 이외에도 사용하는 공구 형상, 작업조건 등에 따라서 변할 수 있음.
4) 클리어런스의 적정치
(가) 개요
전단가공 시 적정한 클리어런스 설정은 매우 중요하며 소재의 연성에 따라 다르고 두께에 따라 비례하는데 다음은 소재에 따른 클리어런스의 적정치를 소개한 것임.
소재 | 클리어런스(%) | 소재 | 클리어런스(%) |
---|---|---|---|
연강 | 6 ~ 9 | 구리합금 | 6 ~ 10 |
경강 | 8 ~ 12 | 알루미늄(연질) | 5 ~ 8 |
스테인레스강 | 6 ~ 10 | 알루미늄합금 | 6 ~ 10 |
(나) 클리어런스와 균열 형태
적정한 클리어런스란 전단 과정에서 펀치와 다이의 전단날이 있는 곳에서 발생된 상•하 균열이 중간 위치에서 만나는 것과 같은 것을 의미함.
클리어런스가 너무 작을 경우에는 상•하 균열이 엇갈림.
클리어런스가 적정한 경우에는 상•하 균열이 소재의 중심 위치에서 일치.
클리어런스가 너무 클 경우에는 상•하 균열이 불일치.
5) 클리어런스 결정
(가) 블랭킹의 경우
펀치에 클리어런스를 적용하며 블랭킹된 제품의 외곽 치수는 다이의 치수와 같음.
(나) 피어싱의 경우
다이에 클리어런스를 적용하며 제품의 구멍 치수는 펀치의 치수와 같음.
(다) 클리어런스 구하는 공식
6) 클리어런스의 영향
(가) 클리어런스가 작을 경우
제품의 정도가 향상되며 뒤틀림(CABER) 현상이 적어짐.
제품의 전단면이 커지며 깨끗이 가공됨.
전단날에 큰 하중이 작용하므로 마모가 발생함.
제품 또는 소재가 펀치에 부착되어 상승하므로 이를 빼는 힘이 커짐.
2차 전단 현상이 일어나게 되어 펀치가 두 번 전단을 하므로 전단력이 커지고 따라서 프레스에 부담을 주게 되어 프레스가 파손될 우려가 있음.
(나) 클리어런스가 클 경우
전단력이 작아지므로 금형의 파손이 적음.
전단날에 작용하는 하중이 작으므로 마모의 발생이 적음.
제품의 뒤틀림 현상이 커지고 정도가 높은 제품이 요구될 경우는 불량품을 양산할 수 있음.
제품의 뒤틀림 현상이 제자리로 돌아가지 못할 수도 있음.
파단면의 각도는 클리어런스가 클수록 커짐.
(3) 전단에 필요한 힘과 영향요인
1) 측방력(LATERAL FORCE)
블랭킹이나 피어싱의 경우 펀치와 다이 및 소재에는 클리어런스의 영향으로 회전 모멘트가 작용함.
이 회전 모멘트에 저항하여 펀치의 측면과 다이의 측면에 대하여 직각 방향으로 힘이 작용함.
측방력은 펀치를 휘게 하거나 절손, 다이의 파손이나 제품 전단면에 버를 발생시킴.
펀치의 가압력과 측방력이 작용하여 소재는 압축응력과 인장응력을 모두 받게 되므로 전단이 시작되는 입구부는 쐐기작용에 의해 깨끗한 전단면이 형성됨.
펀치측 측방력(F1) = Ptp – u1•Pnp
다이측 측방력(F2) = Ptd – u2•Pnd
2) 전단저항
(가) 개요
전단가공에서 소재가 점점 변형되어 파단이 일어나기 직전에 소재의 저항력이 최대가 되는데 그 최대의 저항력을 전단저항 또는 전단강도라고 함.
전단저항(kgf/㎟) = 최대압력(kg) / 절단된 면적(㎟) = 0.6σ
여기서, σ = 인장강도
(나) 전단저항에 영향을 주는 요인
클리어런스.
날끝 형상.(다이에 여유각을, 펀치나 다이에 시어각을 설치하면 전단저항이 감소함)
전단속도.(전단속도가 어느 한도 이내일 때 속도에 비례하여 전단저항이 증가함)
윤활제 사용 유무.
3) 스크랩 제거력(Ps)
스트리퍼로 펀치에 박혀 있는 스크랩을 제거하는데 필요한 힘.
재료의 종류나 작업조건에 따라 다르며 최대 편치 압력의 3 ~ 20% 범위에서 변화함.
Ps = c•l•t
여기서,
c = 계수(1.6mm 이하면 1.6, 1.6mm 이상이면 2.3)
l = 전단육곽의 길이
t = 소재의 두께
(4) 정밀전단가공법
1) 개요
일반적인 전단가공(SHEARING)으로는 소재의 측면에 버가 생기거나 흠집, 휨, 찌그러짐 등의 불량 요인이 발생하는 경우가 많은데 이러한 현상을 방지하거나 최소화하여 깨끗한 전단면을 얻고자 할 때 시행하는 가공법을 말함.
2) 미세블랭킹
(가) 개요
절단선의 윤곽이 폐곡선으로 구성된 제품의 외형을 전단하는 전단가공(SHEARING)법으로 다이 세트 제작에서 펀치까지 동일 기계에서 가공하여 미세 펀칭을 용이하게 할 수 있고 자동 가공을 가능하게 한 가공법.
(나) 특징
펀치, 다이 구멍 등의 위치가 공통이기 때문에 중심을 맞출 필요가 없음.
다이 세트 제작 기간이 짧음.
응력집중이 발생하기 쉬운 어려운 형상의 펀치도 성형할 수 있음.
펀치와 다이 사이의 클리어런스를 임의로 설정할 수 있음.
정밀도가 놓음.(20㎛)
3) 고속 프레스가공
고속 프레스가공은 1,400 ~ 1,500slot/m의 속도로 가공되며 생산 시 프레스 상태를 안정적으로 관리하고 제품을 일정 범위로 유지하기 위해 제어장치를 이용하는 가공법.
제어장치는 치수 측정, 압입력, 이탈력, 스프링의 힘, 부하 상태 확인, 데이터 해석 처리, 카운터 등의 기능을 제어함.
4) 파인 블랭킹
(가) 개요
(나) 특징
3동 특수 프레스가 필요함.
금형 정밀도가 높을 것. (볼붙이 부시형 다이 세트 사용)
돌기 높이는 소재 두께의 1/6 ~ 1/3 정도를 적용할 것.
압축판과 녹아웃 장치가 필요함.
이송 브리지와 에지 브리지는 금형에서 전단일 때와 동일함.
클리어런스는 0에 가까움. (0.5%t)
전단력이 일반 블랭킹에 비해 약 2배가 큼.
(다) 다이의 종류
역누르개에 의한 반력에 의해 펀치의 유지가 확실함.
펀치 홀더에 집중응력이 작용하지 않아 경사가 생기지 않음.
압축판에 의해 펀치를 안내할 수 있음.
굴곡부가 있는 부품의 정밀 블랭킹이 가능함.
다열 펀치 작업이 비교적 수월함.
펀치 홀더의 강도가 충분해야 함.
펀치로 압축판을 안내하기 때문에 펀치에 측방력이 작용함.
판누르개용 가압 핀의 개수가 제한적임.
굴곡부가 있는 제품에 적용하기 힘듦.
다열 펀치 작업이 난해함.
소재에 전단력이 가해지기 전에 압축판의 V자 돌기가 소재를 언더 컷하여 클램핑을 하고,
전단 단계로 들어서면서 펀치 아래쪽의 역누르개가 전단되는 소재의 바닥면을 받치면서 순수 유동으로 소재가 전단됨.
소재가 전단이 되면 펀치의 하강은 소재의 두께만큼 내려가게 되고 이후에 역누르개에 의해 블랭킹 된 제품이 다이의 표면으로 올라오면 압축공기나 녹아웃 장치를 작동시켜 프레스 밖으로 제품을 취출함.
5) 압축전단
(가) 개요
소재를 축 방향으로 압축하면서 전단을 하는 것으로 봉재의 전단가공에 적합한 가공법.
가공 시 전용기가 필요하며 전단면의 정밀도는 공구 클리어런스와 축의 압축력에 의해 좌우됨.
(나) 특징
처짐(눌린면)이 없는 평활한 면을 얻을 수 있음.
공구 날끝부터의 균열 발생을 억제하여 파단면이 발생하지 않음.
이상으로 전단가공의 특징에 대한 연재를 마치고 다음에는 프레스 가공의 부적합 사례에 대하여 다룰 예정입니다.
2020년 06월 26일
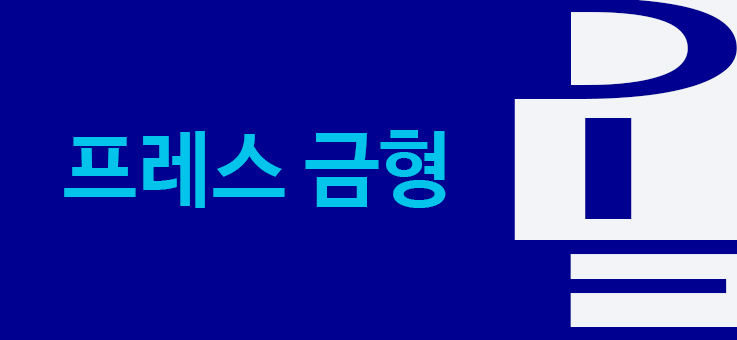
HOME → DIE CATEGORIES →
프레스 금형 9
제9장 전단가공 특징과 프레스 가공의 부적합 사례
1. 전단가공의 특징
(1) 전단현상
1) 개요
전단가공(SHEARING)은 목적에 알맞은 형상의 공구로 금속 소재에 전단변형을 주어 최종적으로 파단을 일으켜 필요한 부분을 분리시키는 가공법으로 소재는 펀치와 다이 사이에서 소성변형과 전단 단계를 거쳐 파단됨.
2) 전단 과정
(가) 탄성변형 단계
펀치가 하강함에 따라 소재는 펀치와 접촉하여 소재 내부에 저항이 발생함.
펀치가 더욱 하강하면 소재의 표면에서는 인장응력이, 다이 및 펀치의 접촉면에서는 압축응력이 발생함.
(나) 소성변형 단계
다이 및 펀치의 접촉면에서 발생하는 압축응력은 가공이 진행됨에 따라 소재의 탄성한도를 넘어 소성변형을 일으킴.
이때 소재는 펀치의 날끝에 의하여 굽혀지면서 눌리게 되는데 이를 눌린면(ROLL OVER)이라 함.
(다) 전단 단계
소성변형이 진행된 소재에 가공을 좀 더 진행하면 전단 날끝의 압축응력이 전단강도를 넘어 감소된 면적의 재료가 전단이 됨.
소성변형을 거쳐 전단 단계로 가공이 진행될 때 펀치가 소재 속으로 들어가면 수직•수평하중을 받게 되고 이때의 수평하중이 소재의 측벽을 매끄럽게 하는데 이를 버니싱(BURNISHING)이라 함.
(라) 파단 단계
전단 단계에서 가공이 더 진행되면 소재의 전단강도 이상의 전단응력이 발생하여 소재는 상•하 균열이 커지면서 파단됨.
소재는 완전 분리되어 펀치는 소재의 절단부를 통과해서 다이 속으로 유입되고 절단된 소재는 낙하됨.
3) 전단가공의 단면 형상
(가) 개요
전단가공(SHEARING)은 소재의 표면에 압력을 가해 전단응력을 발생시켜 파단 현상을 일으키게 하여 소재와 분리하는 가공인데 전단 과정을 거쳐 전단된 블랭크의 형상은 처짐, 전단면, 파단면, 버로 구성됨.
(나) 단면 형상
펀치가 소재에 닿아 압력을 가하면 소재는 압축응력을 받아서 변형되어 항복되는데 이와 같이 소재가 소성변형하면서 소재의 표면에 눌린 자국으로 인하여 처짐이 발생함.
처짐량은 클리어런스를 작게 하여 그 양을 감소시킬 수 있으나 일반적으로 판 두께의 10~20% 정도를 차지함.
펀치가 소재에 침입하면 펀치의 가압력과 측방력의 작용으로 소재는 압축응력과 인장응력에 의해 쐐기작용을 받게 됨.
이로 인해 크랙이 일어나기까지 펀치에 의하여 전단된 면은 광택이 생기게 되고 전단면은 표면에 대해 90º로 형성되며 판 두께의 25~50% 정도를 차지함.
펀치가 하강하면 점점 저항력이 증가하여 최고 하중점에 도달하면 날끝부분의 집중력 때문에 소재 내부의 날끝부분에서 균열이 발생함.
균열이 발생한 면은 인장파단으로 인하여 표면이 거칠지는데 전단면이 증가하면 파단면이 감소하고 전단면이 감소하면 파단면이 증가됨.
처짐과 인장파단의 최후 부분으로 버가 발생함.
버는 제품의 정도를 향상시키려면 발생되지 말아야 하나 전단 형상에서 버를 없애는 것은 불가능하고 일반적으로 판 두께의 10% 이내로 규제하는 것이 적절함.
날끝의 무딘 정도와 소재의 연성에 비례하여 버의 높이가 높아지고 이 값에 의해 금형 수정 시기의 판단 척도가 될 수 있음.
프로그레시브 금형의 경우에는 피어싱된 구멍과 블랭킹된 외곽선에 발생하는 버의 방향은 서로 반대이고 콤파운드 금형의 경우에는 피어싱된 구멍과 블랭킹된 외곽선에 발생하는 버의 방향이 같음.
(다) 전단면 형성의 영향을 미치는 인자
소재가 경질이면 처짐과 전단면이 차지하는 비중이 작아지고 파단면은 커짐.
반면에 연질이면 광택이 있는 전단면이 차지하는 비중 뿐만 아니라 처짐과 버도 커짐.
클리어런스가 커지면 파단면의 각도와 처짐은 약간 커지지만 버는 그다지 커지지 않음.
더욱 클리어런스가 커져 임계점을 넘어가면 버와 처짐이 갑자기 커져서 제품에 휨이 발생함.
블랭크 홀더를 설치하여 소재를 고정 지지하면 동일한 클리어런스일 때 자유 지지에 비해 전단면은 커지고 처짐도 약간 커짐.
녹아웃을 설치하면 전단면은 커지고 처짐은 작아져서 전단면의 형상이 상대적으로 양호함.
(2) 전단가공의 클리어런스
1) 개요
프레스 금형에서의 클리어런스는 펀치와 다이의 한쪽 틈새의 양을 의미하며 전단가공(SHEARING)에서 좋은 전단면을 얻기 위해서는 클리어런스의 선택이 무엇보다 중요함.
클리어런스가 클수록 전단력은 감소하나 굽힘량이 많아져서 2중의 전단면이 발생할 수 있고 또한 클리어런스는 제품의 단면 형상, 전단력, 치수 정밀도와 밀접한 관계가 있음.
2) 클리어런스와 단면형상
전단된 제품의 단면은 처짐, 전단면, 파단면, 버로 구성되어 있는데 경질 소재는 처짐과 전단면이 차지하는 비중이 적어서 단면의 대부분을 파단면이 차지함.
같은 소재에서는 클리어런스의 양에 따라서 단면 형상이 상이함.
클리어런스가 너무 작으면 상하의 균열이 잘 맞지 않아 단면 상태가 나빠지고 반대로 너무 크면 굽힘 모멘트가 켜져서 제품의 정밀도가 나빠지며 파단면이 증가함.
3) 클리어런스와 전단저항
전단가공(SHEARING)에서는 클리어런스가 커지면 전단저항이 작아지는데 이는 펀치와 다이 사이의 클리어런스가 커지는 만큼 측방력도 같이 커지기 때문에 균열이 발생하는 쐐기효과를 유발하여 전단저항이 작아짐.
전단저항은 클러어런스 이외에도 사용하는 공구 형상, 작업조건 등에 따라서 변할 수 있음.
4) 클리어런스의 적정치
(가) 개요
전단가공 시 적정한 클리어런스 설정은 매우 중요하며 소재의 연성에 따라 다르고 두께에 따라 비례하는데 다음은 소재에 따른 클리어런스의 적정치를 소개한 것임.
소재 | 클리어런스(%) | 소재 | 클리어런스(%) |
---|---|---|---|
연강 | 6 ~ 9 | 구리합금 | 6 ~ 10 |
경강 | 8 ~ 12 | 알루미늄(연질) | 5 ~ 8 |
스테인레스강 | 6 ~ 10 | 알루미늄합금 | 6 ~ 10 |
(나) 클리어런스와 균열 형태
적정한 클리어런스란 전단 과정에서 펀치와 다이의 전단날이 있는 곳에서 발생된 상•하 균열이 중간 위치에서 만나는 것과 같은 것을 의미함.
클리어런스가 너무 작을 경우에는 상•하 균열이 엇갈림.
클리어런스가 적정한 경우에는 상•하 균열이 소재의 중심 위치에서 일치.
클리어런스가 너무 클 경우에는 상•하 균열이 불일치.
5) 클리어런스 결정
(가) 블랭킹의 경우
펀치에 클리어런스를 적용하며 블랭킹된 제품의 외곽 치수는 다이의 치수와 같음.
(나) 피어싱의 경우
다이에 클리어런스를 적용하며 제품의 구멍 치수는 펀치의 치수와 같음.
(다) 클리어런스 구하는 공식
6) 클리어런스의 영향
(가) 클리어런스가 작을 경우
제품의 정도가 향상되며 뒤틀림(CABER) 현상이 적어짐.
제품의 전단면이 커지며 깨끗이 가공됨.
전단날에 큰 하중이 작용하므로 마모가 발생함.
제품 또는 소재가 펀치에 부착되어 상승하므로 이를 빼는 힘이 커짐.
2차 전단 현상이 일어나게 되어 펀치가 두 번 전단을 하므로 전단력이 커지고 따라서 프레스에 부담을 주게 되어 프레스가 파손될 우려가 있음.
(나) 클리어런스가 클 경우
전단력이 작아지므로 금형의 파손이 적음.
전단날에 작용하는 하중이 작으므로 마모의 발생이 적음.
제품의 뒤틀림 현상이 커지고 정도가 높은 제품이 요구될 경우는 불량품을 양산할 수 있음.
제품의 뒤틀림 현상이 제자리로 돌아가지 못할 수도 있음.
파단면의 각도는 클리어런스가 클수록 커짐.
(3) 전단에 필요한 힘과 영향요인
1) 측방력(LATERAL FORCE)
블랭킹이나 피어싱의 경우 펀치와 다이 및 소재에는 클리어런스의 영향으로 회전 모멘트가 작용함.
이 회전 모멘트에 저항하여 펀치의 측면과 다이의 측면에 대하여 직각 방향으로 힘이 작용함.
측방력은 펀치를 휘게 하거나 절손, 다이의 파손이나 제품 전단면에 버를 발생시킴.
펀치의 가압력과 측방력이 작용하여 소재는 압축응력과 인장응력을 모두 받게 되므로 전단이 시작되는 입구부는 쐐기작용에 의해 깨끗한 전단면이 형성됨.
펀치측 측방력(F1) = Ptp – u1•Pnp
다이측 측방력(F2) = Ptd – u2•Pnd
2) 전단저항
(가) 개요
전단가공에서 소재가 점점 변형되어 파단이 일어나기 직전에 소재의 저항력이 최대가 되는데 그 최대의 저항력을 전단저항 또는 전단강도라고 함.
전단저항(kgf/㎟) = 최대압력(kg) / 절단된 면적(㎟) = 0.6σ
여기서, σ = 인장강도
(나) 전단저항에 영향을 주는 요인
클리어런스.
날끝 형상.(다이에 여유각을, 펀치나 다이에 시어각을 설치하면 전단저항이 감소함)
전단속도.(전단속도가 어느 한도 이내일 때 속도에 비례하여 전단저항이 증가함)
윤활제 사용 유무.
3) 스크랩 제거력(Ps)
스트리퍼로 펀치에 박혀 있는 스크랩을 제거하는데 필요한 힘.
재료의 종류나 작업조건에 따라 다르며 최대 편치 압력의 3 ~ 20% 범위에서 변화함.
Ps = c•l•t
여기서,
c = 계수(1.6mm 이하면 1.6, 1.6mm 이상이면 2.3)
l = 전단육곽의 길이
t = 소재의 두께
(4) 정밀전단가공법
1) 개요
일반적인 전단가공(SHEARING)으로는 소재의 측면에 버가 생기거나 흠집, 휨, 찌그러짐 등의 불량 요인이 발생하는 경우가 많은데 이러한 현상을 방지하거나 최소화하여 깨끗한 전단면을 얻고자 할 때 시행하는 가공법을 말함.
2) 미세블랭킹
(가) 개요
절단선의 윤곽이 폐곡선으로 구성된 제품의 외형을 전단하는 전단가공(SHEARING)법으로 다이 세트 제작에서 펀치까지 동일 기계에서 가공하여 미세 펀칭을 용이하게 할 수 있고 자동 가공을 가능하게 한 가공법.
(나) 특징
펀치, 다이 구멍 등의 위치가 공통이기 때문에 중심을 맞출 필요가 없음.
다이 세트 제작 기간이 짧음.
응력집중이 발생하기 쉬운 어려운 형상의 펀치도 성형할 수 있음.
펀치와 다이 사이의 클리어런스를 임의로 설정할 수 있음.
정밀도가 놓음.(20㎛)
3) 고속 프레스가공
고속 프레스가공은 1,400 ~ 1,500slot/m의 속도로 가공되며 생산 시 프레스 상태를 안정적으로 관리하고 제품을 일정 범위로 유지하기 위해 제어장치를 이용하는 가공법.
제어장치는 치수 측정, 압입력, 이탈력, 스프링의 힘, 부하 상태 확인, 데이터 해석 처리, 카운터 등의 기능을 제어함.
4) 파인 블랭킹
(가) 개요
(나) 특징
3동 특수 프레스가 필요함.
금형 정밀도가 높을 것. (볼붙이 부시형 다이 세트 사용)
돌기 높이는 소재 두께의 1/6 ~ 1/3 정도를 적용할 것.
압축판과 녹아웃 장치가 필요함.
이송 브리지와 에지 브리지는 금형에서 전단일 때와 동일함.
클리어런스는 0에 가까움. (0.5%t)
전단력이 일반 블랭킹에 비해 약 2배가 큼.
(다) 다이의 종류
역누르개에 의한 반력에 의해 펀치의 유지가 확실함.
펀치 홀더에 집중응력이 작용하지 않아 경사가 생기지 않음.
압축판에 의해 펀치를 안내할 수 있음.
굴곡부가 있는 부품의 정밀 블랭킹이 가능함.
다열 펀치 작업이 비교적 수월함.
펀치 홀더의 강도가 충분해야 함.
펀치로 압축판을 안내하기 때문에 펀치에 측방력이 작용함.
판누르개용 가압 핀의 개수가 제한적임.
굴곡부가 있는 제품에 적용하기 힘듦.
다열 펀치 작업이 난해함.
소재에 전단력이 가해지기 전에 압축판의 V자 돌기가 소재를 언더 컷하여 클램핑을 하고,
전단 단계로 들어서면서 펀치 아래쪽의 역누르개가 전단되는 소재의 바닥면을 받치면서 순수 유동으로 소재가 전단됨.
소재가 전단이 되면 펀치의 하강은 소재의 두께만큼 내려가게 되고 이후에 역누르개에 의해 블랭킹 된 제품이 다이의 표면으로 올라오면 압축공기나 녹아웃 장치를 작동시켜 프레스 밖으로 제품을 취출함.
5) 압축전단
(가) 개요
소재를 축 방향으로 압축하면서 전단을 하는 것으로 봉재의 전단가공에 적합한 가공법.
가공 시 전용기가 필요하며 전단면의 정밀도는 공구 클리어런스와 축의 압축력에 의해 좌우됨.
(나) 특징
처짐(눌린면)이 없는 평활한 면을 얻을 수 있음.
공구 날끝부터의 균열 발생을 억제하여 파단면이 발생하지 않음.
이상으로 전단가공의 특징에 대한 연재를 마치고 다음에는 프레스 가공의 부적합 사례에 대하여 다룰 예정입니다.
2020년 06월 26일
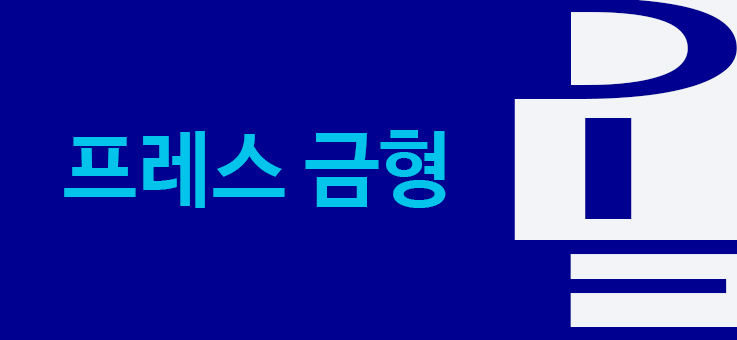
HOME → DIE CATEGORIES →
프레스 금형 9
제9장 전단가공 특징과 프레스 가공의 부적합 사례
1. 전단가공의 특징
(1) 전단현상
1) 개요
전단가공(SHEARING)은 목적에 알맞은 형상의 공구로 금속 소재에 전단변형을 주어 최종적으로 파단을 일으켜 필요한 부분을 분리시키는 가공법으로 소재는 펀치와 다이 사이에서 소성변형과 전단 단계를 거쳐 파단됨.
2) 전단 과정
(가) 탄성변형 단계
펀치가 하강함에 따라 소재는 펀치와 접촉하여 소재 내부에 저항이 발생함.
펀치가 더욱 하강하면 소재의 표면에서는 인장응력이, 다이 및 펀치의 접촉면에서는 압축응력이 발생함.
(나) 소성변형 단계
다이 및 펀치의 접촉면에서 발생하는 압축응력은 가공이 진행됨에 따라 소재의 탄성한도를 넘어 소성변형을 일으킴.
이때 소재는 펀치의 날끝에 의하여 굽혀지면서 눌리게 되는데 이를 눌린면(ROLL OVER)이라 함.
(다) 전단 단계
소성변형이 진행된 소재에 가공을 좀 더 진행하면 전단 날끝의 압축응력이 전단강도를 넘어 감소된 면적의 재료가 전단이 됨.
소성변형을 거쳐 전단 단계로 가공이 진행될 때 펀치가 소재 속으로 들어가면 수직•수평하중을 받게 되고 이때의 수평하중이 소재의 측벽을 매끄럽게 하는데 이를 버니싱(BURNISHING)이라 함.
(라) 파단 단계
전단 단계에서 가공이 더 진행되면 소재의 전단강도 이상의 전단응력이 발생하여 소재는 상•하 균열이 커지면서 파단됨.
소재는 완전 분리되어 펀치는 소재의 절단부를 통과해서 다이 속으로 유입되고 절단된 소재는 낙하됨.
3) 전단가공의 단면 형상
(가) 개요
전단가공(SHEARING)은 소재의 표면에 압력을 가해 전단응력을 발생시켜 파단 현상을 일으키게 하여 소재와 분리하는 가공인데 전단 과정을 거쳐 전단된 블랭크의 형상은 처짐, 전단면, 파단면, 버로 구성됨.
(나) 단면 형상
펀치가 소재에 닿아 압력을 가하면 소재는 압축응력을 받아서 변형되어 항복되는데 이와 같이 소재가 소성변형하면서 소재의 표면에 눌린 자국으로 인하여 처짐이 발생함.
처짐량은 클리어런스를 작게 하여 그 양을 감소시킬 수 있으나 일반적으로 판 두께의 10~20% 정도를 차지함.
펀치가 소재에 침입하면 펀치의 가압력과 측방력의 작용으로 소재는 압축응력과 인장응력에 의해 쐐기작용을 받게 됨.
이로 인해 크랙이 일어나기까지 펀치에 의하여 전단된 면은 광택이 생기게 되고 전단면은 표면에 대해 90º로 형성되며 판 두께의 25~50% 정도를 차지함.
펀치가 하강하면 점점 저항력이 증가하여 최고 하중점에 도달하면 날끝부분의 집중력 때문에 소재 내부의 날끝부분에서 균열이 발생함.
균열이 발생한 면은 인장파단으로 인하여 표면이 거칠지는데 전단면이 증가하면 파단면이 감소하고 전단면이 감소하면 파단면이 증가됨.
처짐과 인장파단의 최후 부분으로 버가 발생함.
버는 제품의 정도를 향상시키려면 발생되지 말아야 하나 전단 형상에서 버를 없애는 것은 불가능하고 일반적으로 판 두께의 10% 이내로 규제하는 것이 적절함.
날끝의 무딘 정도와 소재의 연성에 비례하여 버의 높이가 높아지고 이 값에 의해 금형 수정 시기의 판단 척도가 될 수 있음.
프로그레시브 금형의 경우에는 피어싱된 구멍과 블랭킹된 외곽선에 발생하는 버의 방향은 서로 반대이고 콤파운드 금형의 경우에는 피어싱된 구멍과 블랭킹된 외곽선에 발생하는 버의 방향이 같음.
(다) 전단면 형성의 영향을 미치는 인자
소재가 경질이면 처짐과 전단면이 차지하는 비중이 작아지고 파단면은 커짐.
반면에 연질이면 광택이 있는 전단면이 차지하는 비중 뿐만 아니라 처짐과 버도 커짐.
클리어런스가 커지면 파단면의 각도와 처짐은 약간 커지지만 버는 그다지 커지지 않음.
더욱 클리어런스가 커져 임계점을 넘어가면 버와 처짐이 갑자기 커져서 제품에 휨이 발생함.
블랭크 홀더를 설치하여 소재를 고정 지지하면 동일한 클리어런스일 때 자유 지지에 비해 전단면은 커지고 처짐도 약간 커짐.
녹아웃을 설치하면 전단면은 커지고 처짐은 작아져서 전단면의 형상이 상대적으로 양호함.
(2) 전단가공의 클리어런스
1) 개요
프레스 금형에서의 클리어런스는 펀치와 다이의 한쪽 틈새의 양을 의미하며 전단가공(SHEARING)에서 좋은 전단면을 얻기 위해서는 클리어런스의 선택이 무엇보다 중요함.
클리어런스가 클수록 전단력은 감소하나 굽힘량이 많아져서 2중의 전단면이 발생할 수 있고 또한 클리어런스는 제품의 단면 형상, 전단력, 치수 정밀도와 밀접한 관계가 있음.
2) 클리어런스와 단면형상
전단된 제품의 단면은 처짐, 전단면, 파단면, 버로 구성되어 있는데 경질 소재는 처짐과 전단면이 차지하는 비중이 적어서 단면의 대부분을 파단면이 차지함.
같은 소재에서는 클리어런스의 양에 따라서 단면 형상이 상이함.
클리어런스가 너무 작으면 상하의 균열이 잘 맞지 않아 단면 상태가 나빠지고 반대로 너무 크면 굽힘 모멘트가 켜져서 제품의 정밀도가 나빠지며 파단면이 증가함.
3) 클리어런스와 전단저항
전단가공(SHEARING)에서는 클리어런스가 커지면 전단저항이 작아지는데 이는 펀치와 다이 사이의 클리어런스가 커지는 만큼 측방력도 같이 커지기 때문에 균열이 발생하는 쐐기효과를 유발하여 전단저항이 작아짐.
전단저항은 클러어런스 이외에도 사용하는 공구 형상, 작업조건 등에 따라서 변할 수 있음.
4) 클리어런스의 적정치
(가) 개요
전단가공 시 적정한 클리어런스 설정은 매우 중요하며 소재의 연성에 따라 다르고 두께에 따라 비례하는데 다음은 소재에 따른 클리어런스의 적정치를 소개한 것임.
소재 | 클리어런스(%) | 소재 | 클리어런스(%) |
---|---|---|---|
연강 | 6 ~ 9 | 구리합금 | 6 ~ 10 |
경강 | 8 ~ 12 | 알루미늄(연질) | 5 ~ 8 |
스테인레스강 | 6 ~ 10 | 알루미늄합금 | 6 ~ 10 |
(나) 클리어런스와 균열 형태
적정한 클리어런스란 전단 과정에서 펀치와 다이의 전단날이 있는 곳에서 발생된 상•하 균열이 중간 위치에서 만나는 것과 같은 것을 의미함.
클리어런스가 너무 작을 경우에는 상•하 균열이 엇갈림.
클리어런스가 적정한 경우에는 상•하 균열이 소재의 중심 위치에서 일치.
클리어런스가 너무 클 경우에는 상•하 균열이 불일치.
5) 클리어런스 결정
(가) 블랭킹의 경우
펀치에 클리어런스를 적용하며 블랭킹된 제품의 외곽 치수는 다이의 치수와 같음.
(나) 피어싱의 경우
다이에 클리어런스를 적용하며 제품의 구멍 치수는 펀치의 치수와 같음.
(다) 클리어런스 구하는 공식
6) 클리어런스의 영향
(가) 클리어런스가 작을 경우
제품의 정도가 향상되며 뒤틀림(CABER) 현상이 적어짐.
제품의 전단면이 커지며 깨끗이 가공됨.
전단날에 큰 하중이 작용하므로 마모가 발생함.
제품 또는 소재가 펀치에 부착되어 상승하므로 이를 빼는 힘이 커짐.
2차 전단 현상이 일어나게 되어 펀치가 두 번 전단을 하므로 전단력이 커지고 따라서 프레스에 부담을 주게 되어 프레스가 파손될 우려가 있음.
(나) 클리어런스가 클 경우
전단력이 작아지므로 금형의 파손이 적음.
전단날에 작용하는 하중이 작으므로 마모의 발생이 적음.
제품의 뒤틀림 현상이 커지고 정도가 높은 제품이 요구될 경우는 불량품을 양산할 수 있음.
제품의 뒤틀림 현상이 제자리로 돌아가지 못할 수도 있음.
파단면의 각도는 클리어런스가 클수록 커짐.
(3) 전단에 필요한 힘과 영향요인
1) 측방력(LATERAL FORCE)
블랭킹이나 피어싱의 경우 펀치와 다이 및 소재에는 클리어런스의 영향으로 회전 모멘트가 작용함.
이 회전 모멘트에 저항하여 펀치의 측면과 다이의 측면에 대하여 직각 방향으로 힘이 작용함.
측방력은 펀치를 휘게 하거나 절손, 다이의 파손이나 제품 전단면에 버를 발생시킴.
펀치의 가압력과 측방력이 작용하여 소재는 압축응력과 인장응력을 모두 받게 되므로 전단이 시작되는 입구부는 쐐기작용에 의해 깨끗한 전단면이 형성됨.
펀치측 측방력(F1) = Ptp – u1•Pnp
다이측 측방력(F2) = Ptd – u2•Pnd
2) 전단저항
(가) 개요
전단가공에서 소재가 점점 변형되어 파단이 일어나기 직전에 소재의 저항력이 최대가 되는데 그 최대의 저항력을 전단저항 또는 전단강도라고 함.
전단저항(kgf/㎟) = 최대압력(kg) / 절단된 면적(㎟) = 0.6σ
여기서, σ = 인장강도
(나) 전단저항에 영향을 주는 요인
클리어런스.
날끝 형상.(다이에 여유각을, 펀치나 다이에 시어각을 설치하면 전단저항이 감소함)
전단속도.(전단속도가 어느 한도 이내일 때 속도에 비례하여 전단저항이 증가함)
윤활제 사용 유무.
3) 스크랩 제거력(Ps)
스트리퍼로 펀치에 박혀 있는 스크랩을 제거하는데 필요한 힘.
재료의 종류나 작업조건에 따라 다르며 최대 편치 압력의 3 ~ 20% 범위에서 변화함.
Ps = c•l•t
여기서,
c = 계수(1.6mm 이하면 1.6, 1.6mm 이상이면 2.3)
l = 전단육곽의 길이
t = 소재의 두께
(4) 정밀전단가공법
1) 개요
일반적인 전단가공(SHEARING)으로는 소재의 측면에 버가 생기거나 흠집, 휨, 찌그러짐 등의 불량 요인이 발생하는 경우가 많은데 이러한 현상을 방지하거나 최소화하여 깨끗한 전단면을 얻고자 할 때 시행하는 가공법을 말함.
2) 미세블랭킹
(가) 개요
절단선의 윤곽이 폐곡선으로 구성된 제품의 외형을 전단하는 전단가공(SHEARING)법으로 다이 세트 제작에서 펀치까지 동일 기계에서 가공하여 미세 펀칭을 용이하게 할 수 있고 자동 가공을 가능하게 한 가공법.
(나) 특징
펀치, 다이 구멍 등의 위치가 공통이기 때문에 중심을 맞출 필요가 없음.
다이 세트 제작 기간이 짧음.
응력집중이 발생하기 쉬운 어려운 형상의 펀치도 성형할 수 있음.
펀치와 다이 사이의 클리어런스를 임의로 설정할 수 있음.
정밀도가 놓음.(20㎛)
3) 고속 프레스가공
고속 프레스가공은 1,400 ~ 1,500slot/m의 속도로 가공되며 생산 시 프레스 상태를 안정적으로 관리하고 제품을 일정 범위로 유지하기 위해 제어장치를 이용하는 가공법.
제어장치는 치수 측정, 압입력, 이탈력, 스프링의 힘, 부하 상태 확인, 데이터 해석 처리, 카운터 등의 기능을 제어함.
4) 파인 블랭킹
(가) 개요
(나) 특징
3동 특수 프레스가 필요함.
금형 정밀도가 높을 것. (볼붙이 부시형 다이 세트 사용)
돌기 높이는 소재 두께의 1/6 ~ 1/3 정도를 적용할 것.
압축판과 녹아웃 장치가 필요함.
이송 브리지와 에지 브리지는 금형에서 전단일 때와 동일함.
클리어런스는 0에 가까움. (0.5%t)
전단력이 일반 블랭킹에 비해 약 2배가 큼.
(다) 다이의 종류
역누르개에 의한 반력에 의해 펀치의 유지가 확실함.
펀치 홀더에 집중응력이 작용하지 않아 경사가 생기지 않음.
압축판에 의해 펀치를 안내할 수 있음.
굴곡부가 있는 부품의 정밀 블랭킹이 가능함.
다열 펀치 작업이 비교적 수월함.
펀치 홀더의 강도가 충분해야 함.
펀치로 압축판을 안내하기 때문에 펀치에 측방력이 작용함.
판누르개용 가압 핀의 개수가 제한적임.
굴곡부가 있는 제품에 적용하기 힘듦.
다열 펀치 작업이 난해함.
소재에 전단력이 가해지기 전에 압축판의 V자 돌기가 소재를 언더 컷하여 클램핑을 하고,
전단 단계로 들어서면서 펀치 아래쪽의 역누르개가 전단되는 소재의 바닥면을 받치면서 순수 유동으로 소재가 전단됨.
소재가 전단이 되면 펀치의 하강은 소재의 두께만큼 내려가게 되고 이후에 역누르개에 의해 블랭킹 된 제품이 다이의 표면으로 올라오면 압축공기나 녹아웃 장치를 작동시켜 프레스 밖으로 제품을 취출함.
5) 압축전단
(가) 개요
소재를 축 방향으로 압축하면서 전단을 하는 것으로 봉재의 전단가공에 적합한 가공법.
가공 시 전용기가 필요하며 전단면의 정밀도는 공구 클리어런스와 축의 압축력에 의해 좌우됨.
(나) 특징
처짐(눌린면)이 없는 평활한 면을 얻을 수 있음.
공구 날끝부터의 균열 발생을 억제하여 파단면이 발생하지 않음.
이상으로 전단가공의 특징에 대한 연재를 마치고 다음에는 프레스 가공의 부적합 사례에 대하여 다룰 예정입니다.
2020년 06월 26일