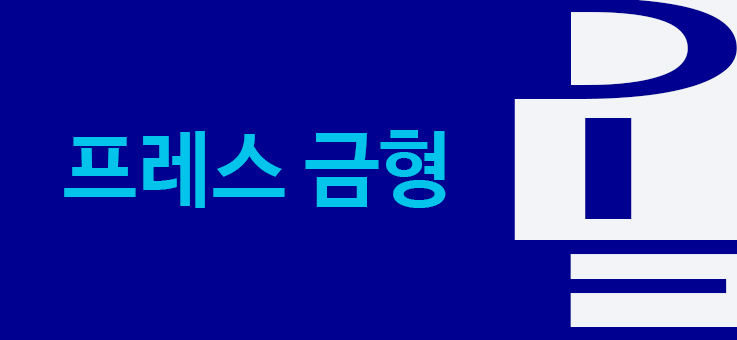
HOME → DIE CATEGORIES →
프레스 금형 3
제3장 전단금형 – 다이 세트 및 다이 설계
1. 다이 세트
(1) 다이 세트의 개요
다이 세트는 프레스 금형을 제작할 때 사용하는 표준 부품으로써 금형의 설치를 신속•정확하게 할 수 있고 펀치와 다이의 상대 위치를 정확하게 유지시켜 가공품의 정밀도와 생산성을 형상시킬 수 있습니다.
다이 세트는 펀치 홀더, 다이 홀더, 생크, 가이드 포스트 및 가이드 부시 등으로 구성됩니다.
NO | PART NAME | MATERIAL |
---|---|---|
1 | 펀치 홀더 | SM34C |
2 | 다이 홀더 | SM45C |
3 | 가이드 포스트 | STC3 |
4 | 가이드 부시 | STC3 |
(2) 다이 세트의 사용상 이점
금형의 탈•부착이 용이함.
펀치와 다이 사이의 클리어런스를 일정하게 유지시킴.
금형의 강도가 향상됨.
금형의 수명이 연장됨.
(3) 다이 세트의 종류 및 특징
1) A형
가이드 포스트가 없는 것으로 정도가 매우 떨어지며 클리어런스는 0.03mm 이상.
2) BB형(BACK POST TYPE)
다이 세트 뒤쪽에 2개의 가이드 포스트가 위치하고 소재를 전후좌우로 이송하여 가공할 수 있으나 전후방향은 편심하중이 발생하기 때문에 정도 유지에 주의를 요하며 클리어런스는 0.02mm ~0.03mm 정도임.
3) CB형(CENTER POST TYPE)
펀치와 다이판을 고정하는 위치와 가이드 포스트의 위치가 다이 세트 중앙에 일직선상으로 위치함.
홀더의 모양이 타원형이고 다이, 펀치, 가이드 포스트가 일직선상에 있으므로 소재를 전후로 이송시 편리하고 편심 하중이 발생하지 않아 BB형보다 상대적으로 높은 정도를 가지며 클리어런스는 0.01mm~0.02mm 정도임.
4) DB형(DIAGONAL POST TYPE)
다이 세트의 대각선상에 2개의 가이드 포스트가 위치하고 BB형과 CB형보다 강성, 정밀도, 작업성이 우수하며 클리어런스는 CB형과 동일한 0.01mm~0.02mm 정도임.
5) FB형(FOUR POST TYPE)
다이 세트 각 모서리에 4개의 가이드 포스트가 위치하고 안내 정밀도가 높고 강성이 커서 주로 정밀가공 금형, 대량생산 금형, 초경합금의 다이 재료를 사용한 금형, 대형 금형 등에 적합하며 클리어런스는 0.005mm~0.01mm 정도임.
6) R형(볼 리테이너 삽입형)
상형의 상하운동 시 볼 부시와 가이드 포스트에 클리어런스가 작고 구름접촉을 하기 때문에 에너지 손실이 적어 안내 정밀도가 높으며 정밀도가 높은 제품을 고속 대량생산할 수 있는 금형에 적합.
NO | PART NAME | MATERIAL |
---|---|---|
1 | 펀치 홀더 | SM45C |
2 | 다이 홀더 | SM45C |
3 | 가이드 포스트 | STC3 |
4 | 가이드 부시 | STC3 |
5 | 볼 리테이너 | – |
6 | 볼 | – |
(4) 다이 세트의 선택 시 고려사항
1) 구조
클리어런스, 시어각(전단각) 등의 날끝 형상.
가공 후 제품에 생기는 변형.
버의 높이 및 방향.
2) 소재
소재의 재질 및 경도.
가공 형상 및 난이도와 이송 방법.
3) 프레스
프레임의 구조.
하중특성 곡선 및 운전방식.
프레스의 정밀도 및 능력과 사양.
4) 작업조건
이송속도, 제품 수량 및 납기.
전단 두께, 전단 하중 및 스트리퍼 하중.
윤활.
2. 전단금형의 구조 및 가동 방법
(1) 구조 및 각부 명칭
전단 금형은 판재에서 필요한 형상을 전단하여 분리하는 블랭킹 금형과 판재에서 필요한 구멍을 뚫는 피어싱 금형으로 구분되는데 전단 금형을 설계할 때에는 제품의 형상 및 크기, 두께, 정밀도, 생산수량 등을 고려해야 함.
전단 금형의 종류로는 블랭킹, 피어싱, 컴파운드, 트랜스퍼, 프로그레시브 금형 등이 있고 스트리퍼판의 방식에 따라 고정형과 가동형으로 나뉠 수 있는데 이 분야는 추후 언급하기로 하고 전단 금형의 기본적인 구조를 살펴보면 다음과 같음.
NO | PART NAME | MATERIAL |
---|---|---|
1 | 생크 | SM45C |
2 | 펀치 홀더 | SM45C |
3 | 배킹 플레이트 | STD11 |
4 | 펀치 고정판 | STC3 |
5 | 스트리퍼판 | STD11 |
6 | 다이 | STD11 |
7 | 펀치 | STD11 |
8 | 다이 홀더 | SM45C |
9 | 가이드 부시 | STC3 |
10 | 가이드 포스트 | STC3 |
(2) 가동 방법
① 소재가 다이의 윗면으로 이동.
② 프레스의 슬라이더(램)에 장착되어 있는 상형 (펀치 홀더, 펀치 등)이 하강.
③ 펀치에 의해 소재가 전단되면서 블랭킹 제품이 다이 속으로 들어감.
④ 전단이 완료되면 펀치가 슬라이더(램)와 함께 상승하고 이때 펀치에 붙어 있는 스크랩은 스트리퍼판에 의해 분리되며 다이 속에 있던 블랭킹 제품은 다이 밑으로 낙하함.
⑤ ①에서 ④의 과정을 계속해서 반복.
3. 전단금형의 설계
(1) 설계순서
① 재료의 레이아웃 설계 – 전개 방법 및 브리지 여유값을 결정.
② 다이 설계 – 판취 전개 고려.
③ 펀치 설계 – 좌굴이 발생하지 않도록 펀치 길이 선정.
④ 펀치 고정판 설계 – 펀치를 안전하게 지지할 수 있도록 두께 결정.
⑤ 파일럿 핀 설계 – 스트립 형태를 결정하고 이를 고려하여 파일럿 핀 선택.
⑥ 가이드 및 스토퍼 설계 – 스트립 띠강이 금형을 통과할 때 진행 방향의 위치를 결정.
⑦ 스트리퍼판 설계 – 스트리핑력을 고려.
⑧ 체결구 및 다이 세트 선택 – 제품의 정밀도, 다이 재료, 클리어런스 등을 고려하여 선택.
(2) 다이의 설계
1) 다이의 개요
다이는 금속의 소성가공에 사용하는 형틀로 펀치와 상대운동을 하는 부품으로써 펀치가 가하는 하중이나 열처리에 의한 변형이 일어나기 쉬워서 충분한 두께 및 강도를 가지고 있어야 파손되지 않음.
2) 다이의 두께
다이의 두께를 결정하는 방법에는 전단력에 의한 방법, 전단 길이와 소재의 두께에 의한 방법. 제품 수량에 의한 방법 등이 있음.
(가) 전단력에 의한 방법
여기서, H = 다이 두께(mm), P = 전단력(kgf), K = 보정계수
전단 길이에 따른 보정계수(K)
전단길이(mm) | 50~75 | 75~150 | 150~300 | 300~500 | 500 이상 |
---|---|---|---|---|---|
보정계수(K) | 1.12 | 1.25 | 1.37 | 1.50 | 1.60 |
ㄱ) 전단력 계산
P = τ•A
여기서, τ = 전단강도(kg/㎟), A = 단면적(㎟)
원형의 단면적 = π x D x t (D = 직경, t = 두께)
사각형의 단면적 = 4변의 합 x t
평철의 단면적 = 전단 길이(ι) x t
프레스 선정 시 전단력의 2~3배의 큰 것을 선정할 것.
(나) 전단 길이와 소재의 두께에 의한 방법
ㄱ) 경질일 경우 기준표 값에 +3
ㄴ) 연질일 경우 기준표 값에 -3
(다) 제품 수량에 의한 방법
ㄱ) 경질일 경우 기준표 값에 +3
ㄴ) 연질일 경우 기준표 값에 -3
3) 다이의 크기
다이의 외곽 치수 결정은 판취 전개에 기반하여 설계되어야 하고 블록의 강도와 수명을 고려해야 하며 소재 안내판과 가이드 포스트, 가이드 부시의 설치 여유를 확보해야 함.
(가) 다이 구멍과 외곽선까지의 거리(L)
매끄러운 곡선일 경우 – L ≥ 1.2H
형상이 직선일 경우 – L ≥ 1.5H
형상에 모서리가 있을 경우 – L ≥ 2.0H
(나) 다이의 조립용 구멍의 위치(c)
c = (1.7 ~ 2.0)d
(다) 다이의 각 구멍 간의 거리(a)
일반적으로는 a < 2d로 하고 최소 허용 거리는 열처리 된 재료일 경우 a = 1.3d, 열처리를 하지 않은 재료일 경우 a = d로 함.
(3) 다이의 날끝 형상
1) 여유각
(가) 설치 이유
블랭킹 작업 시 펀칭한 블랭크는 다이 구멍에 눌러 넣어져 다이 안쪽 벽을 강하게 압박하게 되는데 이때 과열 부착을 일으켜서 다이를 마모시키고 제품의 취출을 어렵게 하므로 이를 방지하기 위해 여유각을 설치함.
(나) 형상
ㄱ) 일반형
제품이 자유낙하하는 금형에 사용하며 다이의 절단 입구부터 여유각을 설치함.
소재 두께(mm) | 여유각(α) |
---|---|
0.8 이하 | 1/6 ~ 1/4° |
0.8 ~ 4.0 | 1/2° |
4.0 이상 | 3/4° |
ㄴ) 직선형
날끝 형상이 여유각이 없는 직선형이고 정밀도가 높은 제품을 가공할 경우에 사용되며 녹아웃 장치가 없으면 대량생산이 곤란함.
ㄷ) 정밀형
유효 날끝길이(h)를 3~5mm 주고 여유각(α)을 1/2~2°로 한 것으로 날끝 마모로 인하여 재연삭을 하여도 정도가 보존되고 다이의 수명을 연장시킬 수 있음.
ㄹ) 대량생산형
유효 날끝길이(h)를 5~7mm 주고 s의 값을 길게 하면 다이의 재연삭 시 날끝의 길이가 짧아지면서 강도가 약해지기 때문에 자유낙하가 아닌 경우에 s의 값은 0.2~0.5mm 정도를 줄 것.
2) 전단각(SHEAR ANGLE)
전단각은 전단력을 감소시키기 위해 설치하는데 펀치에 전단각을 설치하면 블랭크가 휘어지므로 블랭킹 가공에는 사용할 수 없고 피어싱 가공에 사용함.
(가) 전단각 설치 방법
전단력이 프레스의 가압 능력에 50%를 초과할 경우 전단 저항을 감소시키기 위해 전단각을 설치함.
블랭킹의 경우 다이측에, 피어싱의 경우 펀치측에 전단각을 설치할 것.
연속 블랭킹이나 두꺼운 판을 블랭킹할 경우에는 블랭크의 변형을 방지하기 위해 판 두께의 1/2~1/3 범위 내에서 전단각을 설치할 것.
전단각의 높이는 0.6~0.9t로 할 것.
(나) 형상
ㄱ) 피어싱용
펀치측에 전단각을 설치하며 각도가 대칭인 것과 한쪽만 경사지게 한 것이 있고 대칭이 아닌 것은 소재에 외력이 작용하는 것을 방지해야 함.
ㄴ) 블랭킹용
다이측에 전단각을 설치하며 피어싱용과 마찬가지로 각도가 대칭인 것과 한쪽만 경사지게 한 것이 있는데 대칭이 아닌 경우에는 소재에 미끄럼을 방지해야 함.
이상으로 다이 설계를 마치고 다음에는 펀치 및 스트리퍼판 설계에 대해서 연재할 예정입니다.
2020년 04월 24일
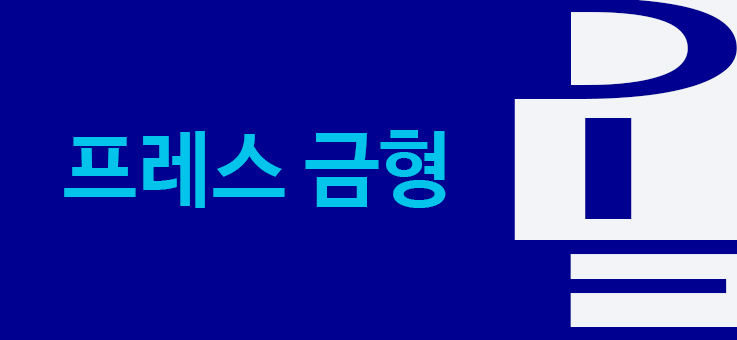
HOME → DIE CATEGORIES →
프레스 금형 3
제3장 전단금형 – 다이 세트 및 다이 설계
1. 다이 세트
(1) 다이 세트의 개요
다이 세트는 프레스 금형을 제작할 때 사용하는 표준 부품으로써 금형의 설치를 신속•정확하게 할 수 있고 펀치와 다이의 상대 위치를 정확하게 유지시켜 가공품의 정밀도와 생산성을 형상시킬 수 있습니다.
다이 세트는 펀치 홀더, 다이 홀더, 생크, 가이드 포스트 및 가이드 부시 등으로 구성됩니다.
NO | PART NAME | MATERIAL |
---|---|---|
1 | 펀치 홀더 | SM34C |
2 | 다이 홀더 | SM45C |
3 | 가이드 포스트 | STC3 |
4 | 가이드 부시 | STC3 |
(2) 다이 세트의 사용상 이점
금형의 탈•부착이 용이함.
펀치와 다이 사이의 클리어런스를 일정하게 유지시킴.
금형의 강도가 향상됨.
금형의 수명이 연장됨.
(3) 다이 세트의 종류 및 특징
1) A형
가이드 포스트가 없는 것으로 정도가 매우 떨어지며 클리어런스는 0.03mm 이상.
2) BB형(BACK POST TYPE)
다이 세트 뒤쪽에 2개의 가이드 포스트가 위치하고 소재를 전후좌우로 이송하여 가공할 수 있으나 전후방향은 편심하중이 발생하기 때문에 정도 유지에 주의를 요하며 클리어런스는 0.02mm ~0.03mm 정도임.
3) CB형(CENTER POST TYPE)
펀치와 다이판을 고정하는 위치와 가이드 포스트의 위치가 다이 세트 중앙에 일직선상으로 위치함.
홀더의 모양이 타원형이고 다이, 펀치, 가이드 포스트가 일직선상에 있으므로 소재를 전후로 이송시 편리하고 편심 하중이 발생하지 않아 BB형보다 상대적으로 높은 정도를 가지며 클리어런스는 0.01mm~0.02mm 정도임.
4) DB형(DIAGONAL POST TYPE)
다이 세트의 대각선상에 2개의 가이드 포스트가 위치하고 BB형과 CB형보다 강성, 정밀도, 작업성이 우수하며 클리어런스는 CB형과 동일한 0.01mm~0.02mm 정도임.
5) FB형(FOUR POST TYPE)
다이 세트 각 모서리에 4개의 가이드 포스트가 위치하고 안내 정밀도가 높고 강성이 커서 주로 정밀가공 금형, 대량생산 금형, 초경합금의 다이 재료를 사용한 금형, 대형 금형 등에 적합하며 클리어런스는 0.005mm~0.01mm 정도임.
6) R형(볼 리테이너 삽입형)
상형의 상하운동 시 볼 부시와 가이드 포스트에 클리어런스가 작고 구름접촉을 하기 때문에 에너지 손실이 적어 안내 정밀도가 높으며 정밀도가 높은 제품을 고속 대량생산할 수 있는 금형에 적합.
NO | PART NAME | MATERIAL |
---|---|---|
1 | 펀치 홀더 | SM45C |
2 | 다이 홀더 | SM45C |
3 | 가이드 포스트 | STC3 |
4 | 가이드 부시 | STC3 |
5 | 볼 리테이너 | – |
6 | 볼 | – |
(4) 다이 세트의 선택 시 고려사항
1) 구조
클리어런스, 시어각(전단각) 등의 날끝 형상.
가공 후 제품에 생기는 변형.
버의 높이 및 방향.
2) 소재
소재의 재질 및 경도.
가공 형상 및 난이도와 이송 방법.
3) 프레스
프레임의 구조.
하중특성 곡선 및 운전방식.
프레스의 정밀도 및 능력과 사양.
4) 작업조건
이송속도, 제품 수량 및 납기.
전단 두께, 전단 하중 및 스트리퍼 하중.
윤활.
2. 전단금형의 구조 및 가동 방법
(1) 구조 및 각부 명칭
전단 금형은 판재에서 필요한 형상을 전단하여 분리하는 블랭킹 금형과 판재에서 필요한 구멍을 뚫는 피어싱 금형으로 구분되는데 전단 금형을 설계할 때에는 제품의 형상 및 크기, 두께, 정밀도, 생산수량 등을 고려해야 함.
전단 금형의 종류로는 블랭킹, 피어싱, 컴파운드, 트랜스퍼, 프로그레시브 금형 등이 있고 스트리퍼판의 방식에 따라 고정형과 가동형으로 나뉠 수 있는데 이 분야는 추후 언급하기로 하고 전단 금형의 기본적인 구조를 살펴보면 다음과 같음.
NO | PART NAME | MATERIAL |
---|---|---|
1 | 생크 | SM45C |
2 | 펀치 홀더 | SM45C |
3 | 배킹 플레이트 | STD11 |
4 | 펀치 고정판 | STC3 |
5 | 스트리퍼판 | STD11 |
6 | 다이 | STD11 |
7 | 펀치 | STD11 |
8 | 다이 홀더 | SM45C |
9 | 가이드 부시 | STC3 |
10 | 가이드 포스트 | STC3 |
(2) 가동 방법
① 소재가 다이의 윗면으로 이동.
② 프레스의 슬라이더(램)에 장착되어 있는 상형 (펀치 홀더, 펀치 등)이 하강.
③ 펀치에 의해 소재가 전단되면서 블랭킹 제품이 다이 속으로 들어감.
④ 전단이 완료되면 펀치가 슬라이더(램)와 함께 상승하고 이때 펀치에 붙어 있는 스크랩은 스트리퍼판에 의해 분리되며 다이 속에 있던 블랭킹 제품은 다이 밑으로 낙하함.
⑤ ①에서 ④의 과정을 계속해서 반복.
3. 전단금형의 설계
(1) 설계순서
① 재료의 레이아웃 설계 – 전개 방법 및 브리지 여유값을 결정.
② 다이 설계 – 판취 전개 고려.
③ 펀치 설계 – 좌굴이 발생하지 않도록 펀치 길이 선정.
④ 펀치 고정판 설계 – 펀치를 안전하게 지지할 수 있도록 두께 결정.
⑤ 파일럿 핀 설계 – 스트립 형태를 결정하고 이를 고려하여 파일럿 핀 선택.
⑥ 가이드 및 스토퍼 설계 – 스트립 띠강이 금형을 통과할 때 진행 방향의 위치를 결정.
⑦ 스트리퍼판 설계 – 스트리핑력을 고려.
⑧ 체결구 및 다이 세트 선택 – 제품의 정밀도, 다이 재료, 클리어런스 등을 고려하여 선택.
(2) 다이의 설계
1) 다이의 개요
다이는 금속의 소성가공에 사용하는 형틀로 펀치와 상대운동을 하는 부품으로써 펀치가 가하는 하중이나 열처리에 의한 변형이 일어나기 쉬워서 충분한 두께 및 강도를 가지고 있어야 파손되지 않음.
2) 다이의 두께
다이의 두께를 결정하는 방법에는 전단력에 의한 방법, 전단 길이와 소재의 두께에 의한 방법. 제품 수량에 의한 방법 등이 있음.
(가) 전단력에 의한 방법
여기서, H = 다이 두께(mm), P = 전단력(kgf), K = 보정계수
전단 길이에 따른 보정계수(K)
전단길이(mm) | 50~75 | 75~150 | 150~300 | 300~500 | 500 이상 |
---|---|---|---|---|---|
보정계수(K) | 1.12 | 1.25 | 1.37 | 1.50 | 1.60 |
ㄱ) 전단력 계산
P = τ•A
여기서, τ = 전단강도(kg/㎟), A = 단면적(㎟)
원형의 단면적 = π x D x t (D = 직경, t = 두께)
사각형의 단면적 = 4변의 합 x t
평철의 단면적 = 전단 길이(ι) x t
프레스 선정 시 전단력의 2~3배의 큰 것을 선정할 것.
(나) 전단 길이와 소재의 두께에 의한 방법
ㄱ) 경질일 경우 기준표 값에 +3
ㄴ) 연질일 경우 기준표 값에 -3
(다) 제품 수량에 의한 방법
ㄱ) 경질일 경우 기준표 값에 +3
ㄴ) 연질일 경우 기준표 값에 -3
3) 다이의 크기
다이의 외곽 치수 결정은 판취 전개에 기반하여 설계되어야 하고 블록의 강도와 수명을 고려해야 하며 소재 안내판과 가이드 포스트, 가이드 부시의 설치 여유를 확보해야 함.
(가) 다이 구멍과 외곽선까지의 거리(L)
매끄러운 곡선일 경우 – L ≥ 1.2H
형상이 직선일 경우 – L ≥ 1.5H
형상에 모서리가 있을 경우 – L ≥ 2.0H
(나) 다이의 조립용 구멍의 위치(c)
c = (1.7 ~ 2.0)d
(다) 다이의 각 구멍 간의 거리(a)
일반적으로는 a < 2d로 하고 최소 허용 거리는 열처리 된 재료일 경우 a = 1.3d, 열처리를 하지 않은 재료일 경우 a = d로 함.
(3) 다이의 날끝 형상
1) 여유각
(가) 설치 이유
블랭킹 작업 시 펀칭한 블랭크는 다이 구멍에 눌러 넣어져 다이 안쪽 벽을 강하게 압박하게 되는데 이때 과열 부착을 일으켜서 다이를 마모시키고 제품의 취출을 어렵게 하므로 이를 방지하기 위해 여유각을 설치함.
(나) 형상
ㄱ) 일반형
제품이 자유낙하하는 금형에 사용하며 다이의 절단 입구부터 여유각을 설치함.
소재 두께(mm) | 여유각(α) |
---|---|
0.8 이하 | 1/6 ~ 1/4° |
0.8 ~ 4.0 | 1/2° |
4.0 이상 | 3/4° |
ㄴ) 직선형
날끝 형상이 여유각이 없는 직선형이고 정밀도가 높은 제품을 가공할 경우에 사용되며 녹아웃 장치가 없으면 대량생산이 곤란함.
ㄷ) 정밀형
유효 날끝길이(h)를 3~5mm 주고 여유각(α)을 1/2~2°로 한 것으로 날끝 마모로 인하여 재연삭을 하여도 정도가 보존되고 다이의 수명을 연장시킬 수 있음.
ㄹ) 대량생산형
유효 날끝길이(h)를 5~7mm 주고 s의 값을 길게 하면 다이의 재연삭 시 날끝의 길이가 짧아지면서 강도가 약해지기 때문에 자유낙하가 아닌 경우에 s의 값은 0.2~0.5mm 정도를 줄 것.
2) 전단각(SHEAR ANGLE)
전단각은 전단력을 감소시키기 위해 설치하는데 펀치에 전단각을 설치하면 블랭크가 휘어지므로 블랭킹 가공에는 사용할 수 없고 피어싱 가공에 사용함.
(가) 전단각 설치 방법
전단력이 프레스의 가압 능력에 50%를 초과할 경우 전단 저항을 감소시키기 위해 전단각을 설치함.
블랭킹의 경우 다이측에, 피어싱의 경우 펀치측에 전단각을 설치할 것.
연속 블랭킹이나 두꺼운 판을 블랭킹할 경우에는 블랭크의 변형을 방지하기 위해 판 두께의 1/2~1/3 범위 내에서 전단각을 설치할 것.
전단각의 높이는 0.6~0.9t로 할 것.
(나) 형상
ㄱ) 피어싱용
펀치측에 전단각을 설치하며 각도가 대칭인 것과 한쪽만 경사지게 한 것이 있고 대칭이 아닌 것은 소재에 외력이 작용하는 것을 방지해야 함.
ㄴ) 블랭킹용
다이측에 전단각을 설치하며 피어싱용과 마찬가지로 각도가 대칭인 것과 한쪽만 경사지게 한 것이 있는데 대칭이 아닌 경우에는 소재에 미끄럼을 방지해야 함.
이상으로 다이 설계를 마치고 다음에는 펀치 및 스트리퍼판 설계에 대해서 연재할 예정입니다.
2020년 04월 24일
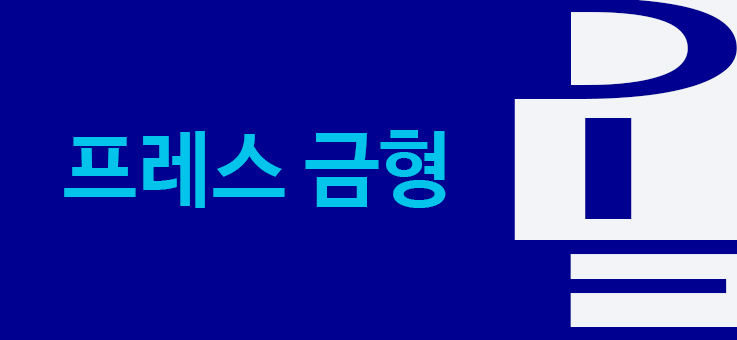
HOME → DIE CATEGORIES →
프레스 금형 3
제3장 전단금형 – 다이 세트 및 다이 설계
1. 다이 세트
(1) 다이 세트의 개요
다이 세트는 프레스 금형을 제작할 때 사용하는 표준 부품으로써 금형의 설치를 신속•정확하게 할 수 있고 펀치와 다이의 상대 위치를 정확하게 유지시켜 가공품의 정밀도와 생산성을 형상시킬 수 있습니다.
다이 세트는 펀치 홀더, 다이 홀더, 생크, 가이드 포스트 및 가이드 부시 등으로 구성됩니다.
NO | PART NAME | MATERIAL |
---|---|---|
1 | 펀치 홀더 | SM34C |
2 | 다이 홀더 | SM45C |
3 | 가이드 포스트 | STC3 |
4 | 가이드 부시 | STC3 |
(2) 다이 세트의 사용상 이점
금형의 탈•부착이 용이함.
펀치와 다이 사이의 클리어런스를 일정하게 유지시킴.
금형의 강도가 향상됨.
금형의 수명이 연장됨.
(3) 다이 세트의 종류 및 특징
1) A형
가이드 포스트가 없는 것으로 정도가 매우 떨어지며 클리어런스는 0.03mm 이상.
2) BB형(BACK POST TYPE)
다이 세트 뒤쪽에 2개의 가이드 포스트가 위치하고 소재를 전후좌우로 이송하여 가공할 수 있으나 전후방향은 편심하중이 발생하기 때문에 정도 유지에 주의를 요하며 클리어런스는 0.02mm ~0.03mm 정도임.
3) CB형(CENTER POST TYPE)
펀치와 다이판을 고정하는 위치와 가이드 포스트의 위치가 다이 세트 중앙에 일직선상으로 위치함.
홀더의 모양이 타원형이고 다이, 펀치, 가이드 포스트가 일직선상에 있으므로 소재를 전후로 이송시 편리하고 편심 하중이 발생하지 않아 BB형보다 상대적으로 높은 정도를 가지며 클리어런스는 0.01mm~0.02mm 정도임.
4) DB형(DIAGONAL POST TYPE)
다이 세트의 대각선상에 2개의 가이드 포스트가 위치하고 BB형과 CB형보다 강성, 정밀도, 작업성이 우수하며 클리어런스는 CB형과 동일한 0.01mm~0.02mm 정도임.
5) FB형(FOUR POST TYPE)
다이 세트 각 모서리에 4개의 가이드 포스트가 위치하고 안내 정밀도가 높고 강성이 커서 주로 정밀가공 금형, 대량생산 금형, 초경합금의 다이 재료를 사용한 금형, 대형 금형 등에 적합하며 클리어런스는 0.005mm~0.01mm 정도임.
6) R형(볼 리테이너 삽입형)
상형의 상하운동 시 볼 부시와 가이드 포스트에 클리어런스가 작고 구름접촉을 하기 때문에 에너지 손실이 적어 안내 정밀도가 높으며 정밀도가 높은 제품을 고속 대량생산할 수 있는 금형에 적합.
NO | PART NAME | MATERIAL |
---|---|---|
1 | 펀치 홀더 | SM45C |
2 | 다이 홀더 | SM45C |
3 | 가이드 포스트 | STC3 |
4 | 가이드 부시 | STC3 |
5 | 볼 리테이너 | – |
6 | 볼 | – |
(4) 다이 세트의 선택 시 고려사항
1) 구조
클리어런스, 시어각(전단각) 등의 날끝 형상.
가공 후 제품에 생기는 변형.
버의 높이 및 방향.
2) 소재
소재의 재질 및 경도.
가공 형상 및 난이도와 이송 방법.
3) 프레스
프레임의 구조.
하중특성 곡선 및 운전방식.
프레스의 정밀도 및 능력과 사양.
4) 작업조건
이송속도, 제품 수량 및 납기.
전단 두께, 전단 하중 및 스트리퍼 하중.
윤활.
2. 전단금형의 구조 및 가동 방법
(1) 구조 및 각부 명칭
전단 금형은 판재에서 필요한 형상을 전단하여 분리하는 블랭킹 금형과 판재에서 필요한 구멍을 뚫는 피어싱 금형으로 구분되는데 전단 금형을 설계할 때에는 제품의 형상 및 크기, 두께, 정밀도, 생산수량 등을 고려해야 함.
전단 금형의 종류로는 블랭킹, 피어싱, 컴파운드, 트랜스퍼, 프로그레시브 금형 등이 있고 스트리퍼판의 방식에 따라 고정형과 가동형으로 나뉠 수 있는데 이 분야는 추후 언급하기로 하고 전단 금형의 기본적인 구조를 살펴보면 다음과 같음.
NO | PART NAME | MATERIAL |
---|---|---|
1 | 생크 | SM45C |
2 | 펀치 홀더 | SM45C |
3 | 배킹 플레이트 | STD11 |
4 | 펀치 고정판 | STC3 |
5 | 스트리퍼판 | STD11 |
6 | 다이 | STD11 |
7 | 펀치 | STD11 |
8 | 다이 홀더 | SM45C |
9 | 가이드 부시 | STC3 |
10 | 가이드 포스트 | STC3 |
(2) 가동 방법
① 소재가 다이의 윗면으로 이동.
② 프레스의 슬라이더(램)에 장착되어 있는 상형 (펀치 홀더, 펀치 등)이 하강.
③ 펀치에 의해 소재가 전단되면서 블랭킹 제품이 다이 속으로 들어감.
④ 전단이 완료되면 펀치가 슬라이더(램)와 함께 상승하고 이때 펀치에 붙어 있는 스크랩은 스트리퍼판에 의해 분리되며 다이 속에 있던 블랭킹 제품은 다이 밑으로 낙하함.
⑤ ①에서 ④의 과정을 계속해서 반복.
3. 전단금형의 설계
(1) 설계순서
① 재료의 레이아웃 설계 – 전개 방법 및 브리지 여유값을 결정.
② 다이 설계 – 판취 전개 고려.
③ 펀치 설계 – 좌굴이 발생하지 않도록 펀치 길이 선정.
④ 펀치 고정판 설계 – 펀치를 안전하게 지지할 수 있도록 두께 결정.
⑤ 파일럿 핀 설계 – 스트립 형태를 결정하고 이를 고려하여 파일럿 핀 선택.
⑥ 가이드 및 스토퍼 설계 – 스트립 띠강이 금형을 통과할 때 진행 방향의 위치를 결정.
⑦ 스트리퍼판 설계 – 스트리핑력을 고려.
⑧ 체결구 및 다이 세트 선택 – 제품의 정밀도, 다이 재료, 클리어런스 등을 고려하여 선택.
(2) 다이의 설계
1) 다이의 개요
다이는 금속의 소성가공에 사용하는 형틀로 펀치와 상대운동을 하는 부품으로써 펀치가 가하는 하중이나 열처리에 의한 변형이 일어나기 쉬워서 충분한 두께 및 강도를 가지고 있어야 파손되지 않음.
2) 다이의 두께
다이의 두께를 결정하는 방법에는 전단력에 의한 방법, 전단 길이와 소재의 두께에 의한 방법. 제품 수량에 의한 방법 등이 있음.
(가) 전단력에 의한 방법
여기서, H = 다이 두께(mm), P = 전단력(kgf), K = 보정계수
전단 길이에 따른 보정계수(K)
전단길이(mm) | 50~75 | 75~150 | 150~300 | 300~500 | 500 이상 |
---|---|---|---|---|---|
보정계수(K) | 1.12 | 1.25 | 1.37 | 1.50 | 1.60 |
ㄱ) 전단력 계산
P = τ•A
여기서, τ = 전단강도(kg/㎟), A = 단면적(㎟)
원형의 단면적 = π x D x t (D = 직경, t = 두께)
사각형의 단면적 = 4변의 합 x t
평철의 단면적 = 전단 길이(ι) x t
프레스 선정 시 전단력의 2~3배의 큰 것을 선정할 것.
(나) 전단 길이와 소재의 두께에 의한 방법
ㄱ) 경질일 경우 기준표 값에 +3
ㄴ) 연질일 경우 기준표 값에 -3
(다) 제품 수량에 의한 방법
ㄱ) 경질일 경우 기준표 값에 +3
ㄴ) 연질일 경우 기준표 값에 -3
3) 다이의 크기
다이의 외곽 치수 결정은 판취 전개에 기반하여 설계되어야 하고 블록의 강도와 수명을 고려해야 하며 소재 안내판과 가이드 포스트, 가이드 부시의 설치 여유를 확보해야 함.
(가) 다이 구멍과 외곽선까지의 거리(L)
매끄러운 곡선일 경우 – L ≥ 1.2H
형상이 직선일 경우 – L ≥ 1.5H
형상에 모서리가 있을 경우 – L ≥ 2.0H
(나) 다이의 조립용 구멍의 위치(c)
c = (1.7 ~ 2.0)d
(다) 다이의 각 구멍 간의 거리(a)
일반적으로는 a < 2d로 하고 최소 허용 거리는 열처리 된 재료일 경우 a = 1.3d, 열처리를 하지 않은 재료일 경우 a = d로 함.
(3) 다이의 날끝 형상
1) 여유각
(가) 설치 이유
블랭킹 작업 시 펀칭한 블랭크는 다이 구멍에 눌러 넣어져 다이 안쪽 벽을 강하게 압박하게 되는데 이때 과열 부착을 일으켜서 다이를 마모시키고 제품의 취출을 어렵게 하므로 이를 방지하기 위해 여유각을 설치함.
(나) 형상
ㄱ) 일반형
제품이 자유낙하하는 금형에 사용하며 다이의 절단 입구부터 여유각을 설치함.
소재 두께(mm) | 여유각(α) |
---|---|
0.8 이하 | 1/6 ~ 1/4° |
0.8 ~ 4.0 | 1/2° |
4.0 이상 | 3/4° |
ㄴ) 직선형
날끝 형상이 여유각이 없는 직선형이고 정밀도가 높은 제품을 가공할 경우에 사용되며 녹아웃 장치가 없으면 대량생산이 곤란함.
ㄷ) 정밀형
유효 날끝길이(h)를 3~5mm 주고 여유각(α)을 1/2~2°로 한 것으로 날끝 마모로 인하여 재연삭을 하여도 정도가 보존되고 다이의 수명을 연장시킬 수 있음.
ㄹ) 대량생산형
유효 날끝길이(h)를 5~7mm 주고 s의 값을 길게 하면 다이의 재연삭 시 날끝의 길이가 짧아지면서 강도가 약해지기 때문에 자유낙하가 아닌 경우에 s의 값은 0.2~0.5mm 정도를 줄 것.
2) 전단각(SHEAR ANGLE)
전단각은 전단력을 감소시키기 위해 설치하는데 펀치에 전단각을 설치하면 블랭크가 휘어지므로 블랭킹 가공에는 사용할 수 없고 피어싱 가공에 사용함.
(가) 전단각 설치 방법
전단력이 프레스의 가압 능력에 50%를 초과할 경우 전단 저항을 감소시키기 위해 전단각을 설치함.
블랭킹의 경우 다이측에, 피어싱의 경우 펀치측에 전단각을 설치할 것.
연속 블랭킹이나 두꺼운 판을 블랭킹할 경우에는 블랭크의 변형을 방지하기 위해 판 두께의 1/2~1/3 범위 내에서 전단각을 설치할 것.
전단각의 높이는 0.6~0.9t로 할 것.
(나) 형상
ㄱ) 피어싱용
펀치측에 전단각을 설치하며 각도가 대칭인 것과 한쪽만 경사지게 한 것이 있고 대칭이 아닌 것은 소재에 외력이 작용하는 것을 방지해야 함.
ㄴ) 블랭킹용
다이측에 전단각을 설치하며 피어싱용과 마찬가지로 각도가 대칭인 것과 한쪽만 경사지게 한 것이 있는데 대칭이 아닌 경우에는 소재에 미끄럼을 방지해야 함.
이상으로 다이 설계를 마치고 다음에는 펀치 및 스트리퍼판 설계에 대해서 연재할 예정입니다.
2020년 04월 24일