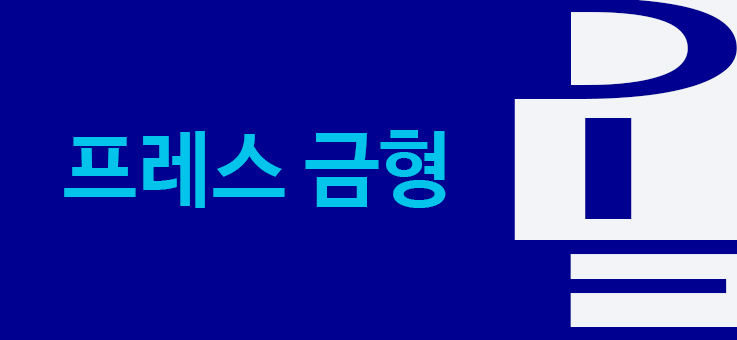
HOME → DIE CATEGORIES →
프레스 금형 2
제2장 프레스 기계
1. 프레스 기계 개요
프레스는 2개 이상의 서로 대응하는 공구를 사용하여 공구 사이에 금속 또는 비금속 판재를 놓고 강한 힘으로 가압하여 전단, 굽힘, 드로잉, 압축 가공을 하는 기계를 말합니다.
프레스는 동력원의 작동 기구에 따라, 구조 및 가공 방법에 따라, 프레임 형식에 따라 분류 기준이 다르지만 일반적으로 동력원의 작동 기구에 따라 분류하고 있습니다.
프레스의 효율은 가압 능력을 톤(ton)으로 표시합니다.
2. 종류
(1) 동력원의 작동 기구에 따른 분류
1) 인력 프레스 기계
수동 프레스로서 스크루 프레스, 수동 편심 프레스가 있으며 레버 조작 구조인 족답 프레스가 있고 얇은 판재 펀칭에 이용됨.
2) 동력 프레스 기계
(가) 기계 프레스
기계의 동력을 이용하여 크랭크 등의 기구로 슬라이드(램)를 작동시키는 프레스.
ㄱ) 크랭크 프레스(CRANK PRESS, POWER PRESS)
크랭크축과 연결봉의 조합으로 축의 회전운동을 직선운동으로 전환시켜 가압하는데 일명 파워 프레스라고도 함.
제작이 쉽고 스트로크 하단 위치가 정확하게 결정되며 슬라이드(램) 운동 곡선이 비교적 무난하고 각종 가공에 유리하여 가장 많이 사용되고 있음.
ㄴ) 편심 프레스(ECCENTRIC PRESS)
클러치의 작동에 따라 편심 주축이 회전하며 그 일단에 상하운동하는 슬라이드(램)가 있고 형틀을 고정하여 가공하는 프레스.
주용도는 뽑기 작업, 블랭킹, 펀칭 가공.
ㄷ) 토글 프레스(TOGGLE PRESS)
크랭크의 회전운동을 다수의 링크장치로 펀치에 전달하도록 한 프레스이며 순간적인 충격을 주지 않고 가공 행정의 끝에서 큰 힘을 발생시킴.
주용도는 블랭킹, 압인, 압출가공.
ㄹ) 너클 프레스(KNUCLE PRESS)
플라이휠의 회전운동을 크랭크 기구에 의해 직선운동으로 바꾸고 이를 너클 기구를 이용하여 슬라이드(램)를 상하로 직선운동시키는 프레스이며 하사점 부근에서 속도가 매우 느려지는 특징이 있음.
주용도는 압인, 냉간단조.
ㅁ) 마찰 프레스(FRICTION PRESS)
플라이휠의 회전력을 마찰차에 전달하며 나사축 바퀴를 마찰차와 접촉시켜 나사축의 회전으로 슬라이드(램)를 상하로 작동시키면서 가공력을 얻는 프레스로 가공정도가 좋지 않고 생산속도도 느림.
주용도는 굽힘, 성형 가공.
이 외에도 랙 프레스, 캠 프레스, 스크루 프레스 등이 있음.
(나) 액압 프레스
유체의 압력에 의해 슬라이드(램)를 작동시키는 프레스로 수압, 유압, 공압 프레스가 있음.
작동 행정을 임의로 조정할 수 있음.
행정에 관계없이 가공력을 가짐.
큰 용량의 가공이 가능함.
과부하가 발생하지 않음.
(다) 기계 프레스와 액압 프레스의 비교
항목 | 기계 프레스 | 액압 프레스 |
---|---|---|
생산속도 | 빠름 | 느림 |
스트로크 | 600~1000(mm) | 기계 프레스보다 제한이 적음 |
스트로크의 변화 | 변화를 주기 힘듦 | 변화를 줄 수 있음 |
스트로크 종단 위치결정 | 정확 | 부정확 |
가압 속도 조절 유무 |
무 | 유 |
가압력 조절 | 어려움 | 쉬움 |
가압력 유지 유무 |
무 | 유 |
과부하 유무 | 유 | 무 |
보수 유지 | 용이함 | 유체 누출 등에 주의가 필요함 |
프레스의 최대 능력 | 4,000t(판금), 9,000t(단조) | 200,000t(단조) |
(2) 프레임 형식에 따른 분류
1) C형 프레임 프레스 기계
프레임의 전면이 C형으로 개방되어 있으며 슬라이드(램)의 위치가 프레스 중심보다 앞쪽에 위치한 프레스.
200t 이하의 소형 프레스에 주로 사용되며 소재의 취급이 용이하나 앞 벌어짐 현상이 발생할 우려가 있음.
2) H형 프레임 프레스 기계
프레임의 형상이 상자형이며 슬라이드(램)의 위치가 프레스의 중심에 있는 프레스.
300t 이상의 중대형 프레스에 주로 사용되며 구조가 안정적이라서 앞 벌어짐이 발생하지 않음.
3) 4주형 프레임 프레스 기계
프레스의 상부구조인 크라운 부위와 하부구조인 베드 부위가 4개의 기둥에 의해 지지되는 프레스.
특수 용도로 사용하는 프레스로 주로 소형 프레스에 적용되며 금형의 취급이 용이하고 유압 성형에 적합함.
사면이 개방되어 있어 금형 탈부착이 용이하고 유압 유니트를 프레임 상부 또는 후면에 설치함으로써 소형화가 가능함.
(3) 구조 및 가공방법에 따른 분류
1) 슬라이드(램) 개수에 따른 분류
(가) 단동 프레스
슬라이드(램) 개수가 1개인 프레스.
(나) 복동 프레스
슬라이드(램) 개수가 2개인 프레스로 블랭킹과 드로잉을 동시에 하거나 딥 드로잉, 복잡한 굽힘 작업에 사용되는 프레스.
요즘은 복동 프레스가 점차 줄어드는 추세로 이는 드로잉 가공이 다이 쿠션의 발달로 인해 대부분의 가공을 단동 프레스에서 충분히 수행할 수 있기 때문.
(다) 3동 프레스
정밀 전단을 위한 파인 블랭킹 프레스가 여기에 속함.
(라) 4동 프레스
2) 슬라이드(램) 운동 방향에 따른 분류
(가) 수직형 프레스
(나) 수평형 프레스
(다) 경사형 프레스
(4) 특수 프레스
1) 전단기(SHEARING PRESS)
판재를 블레이드(직선 날)를 이용하여 원하는 형상으로 절단하는 프레스로 더블 크랭크 프레스가 대표적임.
2) 절곡기(PRESS BRAKE)
넓은 판재를 직선으로 굽히기 위한 전용기.
3) 파인 블랭킹 프레스(FINE BLANKING PRESS)
정밀 전단을 위한 프레스.
4) 다이 스포팅 프레스(DIE SPOTTING PRESS)
프레스 금형 제작이 완료되면 시험작업을 하면서 금형의 수정을 용이하게 하기 위한 시험작업용 프레스로 프레스에 금형이 장착된 상태에서도 수정•보완이 가능함.
5) 트랜스퍼 프레스(TRANSFER PRESS)
1대에 프레스에 여러 대의 금형을 설치하고 금형과 금형 사이를 이송 장치에 의해 소재를 자동으로 이동시키면서 연속 작업을 할 수 있도록 하는 전용의 프레스로 박판 제품 성형에 유리함.
6) 크랭크리스 프레스(CRANKLESS PRESS)
크랭크 프레스와 마찬가지로 회전운동을 직선운동으로 바꾸어 슬라이드(램)에 전달하는 방식은 동일하지만 하중 능력과 강성을 높이기 위해 크랭크가 아닌 직선의 회전축과 편심 캠으로 구성된 회전 기구를 사용한 프레스.
7) OBI 프레스(OPEN BACK INCLINABLE PRESS)
프레스의 후면이 개방되어 있어 제품 취출을 쉽게 할 수 있고 프레스 프레임을 경사지게 할 수 있어 중력에 의해 제품이 쉽게 미끄러질 수 있도록 하여 슈트(CHUTE)가 필요 없는 크랭크 프레스.
150t 이하의 중소형 프레스에 많이 사용되고 있는 단동식 C 프레임 프레스임.
8) 멀티 슬라이드 포머(MULT-SLIDE FORMER)
박판재의 스프링, 링, 전자 부품류 등 복잡한 굽힘 가공의 제품일 경우 같은 반경 방향으로 여러 개의 슬라이드(램)에 펀치를 부착시켜 순차적으로 성형하면서 완성품을 만드는 성형기.
☞ 그밖에 프레스 기계의 용어로는 마이크로 인칭이 있는데 이는 금형 교환 시 슬라이드(램)의 금형 높이를 쉽게 조절하고 미세 스트로크를 제어하는 장치입니다.
3. 프레스의 능력과 사양
(1) 능력
1) 하중(압력) 능력(t)
프레스 가공에 있어 크랭크축, 슬라이드(램), 본체 등이 안전하게 견딜 수 있는 최대 하중을 톤(t)으로 표시.
2) 토크 능력(mm)
하중 능력의 발생이 가능한 위치를 하사점으로부터 떨어진 거리.
프레스 가공을 할 때 최대 하중이 토크 능력 이내에 있도록 금형을 설치하는 것이 중요함.
3) 일의 능력(kg•m, t•mm)
1회 가공에 사용할 수 있는 최대 일의 양.
딥 드로잉의 경우에는 프레스의 능력 검토에 이용함.
(2) 사양
1) 다이 높이(DIE HEIGHT)
프레스의 슬라이드(램) 높이를 하사점으로 내리고 슬라이드(램) 조절 나사를 이용하여 슬라이드(램)의 위치를 최대로 올린 상태에서 볼스터 윗면에서부터 슬라이드(램) 밑면까지의 거리.
프레스에 금형을 실제로 설치 가능한 공간을 말함.
2) 셔트 높이(SHUT HEIGHT)
금형의 높이가 너무 높아 프레스에 설치하기 어려울 경우 볼스터를 떼고 프레스 베드 위에 직접 금형을 설치할 수 있는데 이때 슬라이드(램) 밑면에서 베드 사이의 거리를 말함.
3) 슬라이드(램) 조절량
금형을 프레스에 설치할 때 금형의 높이에 맞춰서 볼스터 윗면 사이에 거리를 조절하여 슬라이드와 금형이 접촉되도록 해야 함.
크랭크 프레스에서는 커넥팅 로드에 나사에 의한 높이 조절장치가 있고 조절할 수 있는 길이를 슬라이드(램) 조절량이라 함.
4) 스트로크수(SPM, 행정수)
슬라이드(램)가 1분 동안 상하로 움직일 수 있는 횟수.
크랭크 축의 매분 회전수와 동일하며 소형은 30~80(spm), 대형은 10~30(spm) 정도임.
5) 스트로크(행정)
슬라이드(램)의 최대 운동 거리로서 가공할 수 있는 제품의 최대 높이가 결정됨.
4. 프레스 가공의 자동화
(1) 자동화 도입 시 장•단점
1) 장점
① 생산량의 증가.
② 인건비의 절약.
③ 숙련된 작업자 불필요.
④ 동일 조건의 작업 시 제품의 정밀도 향상.
⑤ 재료의 절감.
⑥ 작업 공간의 절약.
⑦ 안전성의 향상.
⑧ 반가공품의 재고가 쌓이지 않음.
⑨ 생산관리가 용이.
⑩ 동종 업계에 대한 경쟁력의 강화.
2) 단점
① 설비가 많이 필요.
② 재료의 치수 공차가 정확해야 함.
③ 금형의 제작 비용 상승.
④ 금형 설계의 난이도가 높음.
⑤ 소량생산에 부적합.
⑥ 자동화 설비에 대한 지식이 필요.
⑦ 제품의 변화에 의한 고가 자동화 장치의 사용이 용이하지 못한 불안감.
⑧ 자동화 설비 유지 및 보수가 어려움.
(2) 자동화 설비 구성
1) 코일 소재를 이용한 자동화 구성
적재장치 ▷ 교정장치 ▷ 이송장치 ▷ 프레스 ▷ 취출장치
2) 1차 가공품을 이용한 자동화 구성
적재장치 ▷ 정돈장치 ▷ 분리장치 ▷ 이송장치 ▷ 프레스 ▷ 취출장치
3) 자동화 구성 장치
(가) 적재장치
원재료, 소재 또는 반가공 제품을 가공하기 위하여 적재하거나 투입하고 정확한 방향과 위치로 배치하거나 정렬시켜주는 장치.
ㄱ)코일 소재의 경우
① 릴 스탠드(REEK STAND)
경화중용, 코일재의 내경을 지지.
② 크레이들(CRADLE)
중하중용, 코일 소재의 외경을 지지.
③ 언코일러(UNCOILER)
중하중용, 코일재의 내경을 지지.
④ 턴테이블(TURN TABLE, ROTARIAN)
코일 소재를 수평으로 설치.
ㄴ) 스트립 소재의 경우
적층 된 판재로부터 소재를 1장씩 분리하는 장치인 디스태커(DESTACKER)를 사용함.
ㄷ) 1차 가공품의 경우
호퍼에 1차 가공품을 적재하고 컨베이어나 슈트 등에 의해 볼 피더로 이송하여 부품을 정렬하고 리니어 피더를 통해 프레스로 이송함.
(나) 교정장치
적재장치로부터 이송 된 소재를 상하로 미세한 소성변형을 주어 소재의 평면도를 교정해 주는 장치.
언코일러나 크레이들의 경우에는 교정장치를 포함하여 제작되는 추세임.
(다) 이송장치
적재 장치로부터 보내온 원재료, 소재 또는 반가공 제품을 정확한 방향으로 가공 사이클에 맞게 가공 작업 기기로 보내거나 빼내는 장치.
ㄱ) 코일 소재 이송
① 롤 피더(ROLLL FEEDER)
상하 롤러 사이의 마찰력에 의해 한쪽 방향으로만 회전하는 클러치 베어링에 의해 소재를 앞으로 이송하는 장치.
☞ 릴리싱이란 프레스가 소재를 누르는 순간 금형의 가이드 핀이 소재에 뚫린 가이드 구멍에 삽입되어 위치를 결정 하기 위하여 일시적으로 소재를 들어주는 것을 말합니다.
② 그리퍼 피더(GRIPPER FEEDER)
롤 피더와 방식은 유사하나 이송 길이를 조절할 수 있어 폭이 좁은 재료의 짧은 피치 이송에 사용함.
③ 에어 피더(AIR FEEDER)
공압에 의해 그리퍼(GRIPPER)가 소재를 잡아 앞으로 이송하는 장치.
④ 캠 피더(CAM FEEDER)
고속 프레스의 전용 피더로써 프레스로부터 동력을 전달받아 분할 캠의 분할수, 변환 기어 또는 변환 롤러의 선택에 따라 짧은 피치 고속 이송에 사용함.
⑤ NC 롤 피더(NC ROLL FEEDER)
NC 조작을 통한 소재의 이송량 설정이 간단하고 다품종 소량생산에서 활용성이 높으며 소재 및 이송 제약이 적어 프레스 자동화에 사용함.(NC ROLL FEEDER)
ㄴ) 1차 가공품 이송
볼 피더의 진동과 회전으로 부품을 정렬하고 리니어 피더를 통해 프레스로 이송함.
트랜스퍼 피더(TRANSFER FEEDER)
1차 가공품을 그립 장치에 의해 각각의 공정으로 이송하는 장치로 가공품의 크기가 작을 경우 1대의 트랜스퍼 피더로 소재 이송이 가능함.
가공품의 크기가 클 경우에는 여러 대의 프레스를 설치하고 프레스와 프레 사이에 있는 트랜스퍼 피더로 소재를 이송하여 작업함.
(라) 취출장치
가공이 끝난 제품을 자동으로 취출하는 장치.
(마) 급속 금형 교환장치
금형 탈•부착에 소요되는 시간과 인력의 낭비를 제거하기 위한 장치.
5. 프레스 기계 안전장치
(1) 비상 정지 스위치
누름 버튼으로 작동된 이후 수동으로 복귀시킬 때까지 회로가 자동으로 복귀되지 않고 슬라이드(램)를 시동 상태로 복귀한 것이 아니면 슬라이드(램)가 작동되지 않는 구조임.
(2) 키락(KEY LOCK)
일종의 전환 키 스위치로 주전동기의 통전을 ON/OFF.
키를 작업자가 가지고 있는 한 주전동기의 운전을 할 수 없어 안전함.
(3) 안전 블록 및 안전 플러그
슬라이드(램) 및 상부 금형 등의 무게를 지탱할 수 있는 강도 유지.
안전 블록 사용 시 슬라이드(램) 불시 작동 방지를 위한 인터 록 기능 구비.
기계 프레스에서 볼스터 각 변의 길이가 1,500mm 미만이거나 다이 높이가 700mm 미만이면 안전 플러그 또는 키락으로 대체 가능.
안전 플러그는 각 조작 위치마다 비치하고 구조상 안전 블록 설치가 곤란한 경우 슬라이드(램) 록킹 핀 방식 가능.
(4) 오버 런 감시장치
구동 장치에 결함이 발생되면 즉시 정지 신호를 보내고 결함이 제거될 때까지 가동 중지.
급정지가 필요 없는 전용 프레스, 자동 급송 프레스는 예외.
클러치, 브레이크 작동용 전환 밸브의 배기구 배출 저항 증가 시, 브레이크 패드의 마모 및 오일 등의 불순물 유입으로 브레이크 성능 저하 시 작동함.
(5) 재가동 방지 장치
1행정 후 정지가 안되고 계속해서 행정이 진행되는 것을 재가동이 된다고 하고 재가동을 멈추게 하는 장치로 연속 행정 선택 시에는 작동하지 않음.
(6) 1행정 1정지장치
프레스 작동 후 누름 버튼 등을 계속 누르고 있어도 슬라이드(램)가 1행정의 작업을 마치고 작동하기 전 위치에서 정지하는 장치이며, 상사점 정지기구와 연결하여 사용할 수 있음.
(7) 급정지 장치
위험 또는 이상을 해당 프레스가 검출하여 자동으로 슬라이드(램)의 운동을 즉시 정지시키는 장치.
급정지 장치가 작동 후에는 안전상태로 복귀하여도 재기동 조작을 하지 않으면 슬라이드(램)가 작동하지 않도록 하는 재가동 방지 장치가 구비되어야 함.
6. 프레스 기계 방호장치
(1) 게이트 가드식
슬라이드(램)의 하강 중에는 안으로 손이 들어가지 못하도록 하며 가드를 닫지 않으면 슬라이드(램)를 작동시킬 수 없는 장치.
특징
① 2차 가공에 적합함.
② 기계 고장에 의한 이상 행정, 공구 파손 시에도 안전함.
③ 금형 교환 빈도수가 적은 프레스에 적합함.
④ 게이트는 5mm 이상 두께를 갖는 투명 플라스틱을 사용할 것.
(2) 양수 조작식
2개의 누름 버튼을 위험점으로부터 안전거리 이상을 격리시켜 설치하고 양손으로 동시에 조작하지 않으면 슬라이드(램)가 작동하지 않는 장치.
특징
① 가장 많이 사용.
② 급정지 기구가 부착된 마찰식 클러치 프레스에 적합함.
③ 급정지 성능이 약화되지 않는 한 위험 구역으로부터 작업자를 보호할 수 있음.
④ 굽힘 가공 등 2차 가공에 적합함.
⑤ 급정지 기능이 양호하여 작업능률이 좋음.
(3) 손 쳐내기식
슬라이드(램)에 레버나 링크 혹은 캠으로 연결된 손 쳐내기 봉에 의해 슬라이드(램)의 하강에 앞서 위험 단계에서 손을 쳐내는 장치.
특징
① 규칙적인 프레스의 행정에 대하여 기계 고장에 의한 이상 행정 시 효과가 있음.
② 소형 프레스에 적합함.
③ 쉽게 조정할 수 있음.
④ 양측면은 무방비 상태가 되는 단점이 있음.
(4) 감응식
슬라이드(램)가 하강 중일 때 손이나 신체의 일부가 금형에 접근하는 것을 검출 기구를 통해서 감지하고 제어회로를 통하여 자동적으로 슬라이드(램)를 정지시키는 장치.
특징
① 방호장치 설치가 어려운 프레스에 적합함.
② 시계(야)가 차단되지 않음.
③ 위험 구역을 보호하려면 상당히 많은 수의 광선이 필요함.
④ 위험 구역으로부터 어느 정도 떨어진 거리에 설치되어야 효과가 있음.
⑤ 슬라이드(램) 행정기간 동안에 프레스를 정지시킬 수 있는 경우에만 사용 가능.
⑥ 기계적 고장에 의한 이상 행정에는 효과가 없음.
(5) 수인식
슬라이드(램)와 작업자 손을 끈으로 연결하여 슬라이드(램) 하강 시 작업자의 손을 당겨서 위험에 벗어날 수 있도록 하는 장치.
수인 줄의 재료는 합성 섬유이어야 하고 직경은 Φ4mm 이상, 전단 하중은 조절부를 설치한 상태에서 150kg 이상이어야 함.
리스트 밴드의 재료는 피혁 등을 사용하고 수인 줄과의 연결부는 50kg 이상의 정하중을 견딜 수 있어야 함.
특징
① 설치가 쉽고 유지 보수가 용이하며 비용이 저렴함.
② 수인 줄의 당기는 양은 볼스터의 전후 길이(세로 길이)의 ½ 이상이어야 함.
③ 슬라이드(램)가 불시에 하강할 경우에도 재해 예방이 가능함.
④ 끈의 길이를 적절하게 조절할 수 있어 수공구 사용이 필요하지 않음.
⑤ 행정수를 120spm 이하, 행정 길이는 40mm 이상으로 제한함.
⑥ 작업 반경의 제한으로 행동에 제약을 받아서 작업자를 구속할 수 있음.
⑦ 작업 변경 시 마다 수인 줄의 길이를 조절하여야 함.
7. 서보 프레스
(1) 개요
기존 기계식 프레스의 단점인 가압부의 속도나 가압 횟수 제어의 어려움을 개선한 프레스.
서보 프레스는 가압부의 작동을 CNC와 서보 모터로 제어하기 때문에 복잡한 가압이 가능하고 가공 시 속도나 위치, 가압력을 수치로 설정하여 제어가 손쉬움.
(2) 개발 배경
제조업 전반으로 환경 문제 대응을 피할 수 없어 가볍고 강한 재료를 통해 재료비와 설비비가 상승하지 않도록 하는 방법을 모색하려는 경향이 두드러지기 시작했고 거기에 고정도·고능률 프레스의 도입에 필요성이 대두되었으며 이로 인해 프레스 가공에 있어 초고장력 강판과 서보 프레스가 등장하는 계기가 됨.
(3) 구조
(4) 특징
금형 수명, 가공 정도, 생산 속도의 향상 등과 같은 프레스 가공의 한계를 금형으로 극복하기 힘들어지자 마침 서보 모터가 대형화됨을 계기로 유압 프레스의 성형성과 생산성, 가공 정도의 향상을 실현시키기 위해 서보 프레스가 개발됨.
또한, 이산화탄소와 에너지 절감 효과를 창출할 수 있음.
(5) 서보 프레스 프리 모션과 기계식 프레스의 프로파일 비교
(6) 서보 프레스를 사용하는 이유
수율과 생산성을 동시에 추구.
초고장력 강판, 알루미늄, 티타늄과 같은 난가공재 가공이 가능.
저소음과 저진동.
에너지 절약.
(7) 기술동향
프레스는 압축에너지를 발생시키는 구조에 따라 기계식과 유압식으로 대별됨.
하지만 프레스에서도 에너지 및 자원절약, 이용효율, 편리성 측면에서 유압식보다 유리한 전동방식으로 바뀌는 추세.
서보 프레스는 에너지 회생 시스템을 갖추고 있어 작동유의 누설에 의한 열에너지 손실을 보완할 수 있기 때문에 프레스 기계 기술의 중요한 흐름임.
그러나 초기 투자비용, 서보 모터의 소음과 고주파 발생, 고가의 에너지 회생장치 등이 부담이나 향후 이러한 문제를 극복하면 서보 프레스가 프레스 가공에 있어 주종의 위치를 점할 수 있을 것으로 전망됨.
상당히 긴 글이 되었는데도 프레스에 대해서 다 담지 못한 것 같아 아쉬움이 큽니다.
부족한 부분은 추후에라도 채워나갈 수 있도록 노력할 예정입니다.
2020년 04월 23일
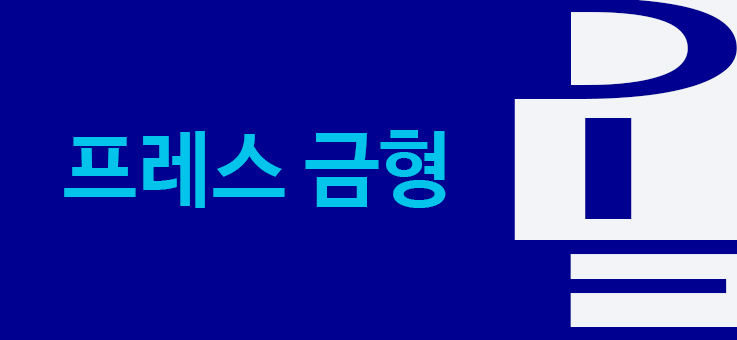
HOME → DIE CATEGORIES →
프레스 금형 2
제2장 프레스 기계
1. 프레스 기계 개요
프레스는 2개 이상의 서로 대응하는 공구를 사용하여 공구 사이에 금속 또는 비금속 판재를 놓고 강한 힘으로 가압하여 전단, 굽힘, 드로잉, 압축 가공을 하는 기계를 말합니다.
프레스는 동력원의 작동 기구에 따라, 구조 및 가공 방법에 따라, 프레임 형식에 따라 분류 기준이 다르지만 일반적으로 동력원의 작동 기구에 따라 분류하고 있습니다.
프레스의 효율은 가압 능력을 톤(ton)으로 표시합니다.
2. 종류
(1) 동력원의 작동 기구에 따른 분류
1) 인력 프레스 기계
수동 프레스로서 스크루 프레스, 수동 편심 프레스가 있으며 레버 조작 구조인 족답 프레스가 있고 얇은 판재 펀칭에 이용됨.
2) 동력 프레스 기계
(가) 기계 프레스
기계의 동력을 이용하여 크랭크 등의 기구로 슬라이드(램)를 작동시키는 프레스.
ㄱ) 크랭크 프레스(CRANK PRESS, POWER PRESS)
크랭크축과 연결봉의 조합으로 축의 회전운동을 직선운동으로 전환시켜 가압하는데 일명 파워 프레스라고도 함.
제작이 쉽고 스트로크 하단 위치가 정확하게 결정되며 슬라이드(램) 운동 곡선이 비교적 무난하고 각종 가공에 유리하여 가장 많이 사용되고 있음.
ㄴ) 편심 프레스(ECCENTRIC PRESS)
클러치의 작동에 따라 편심 주축이 회전하며 그 일단에 상하운동하는 슬라이드(램)가 있고 형틀을 고정하여 가공하는 프레스.
주용도는 뽑기 작업, 블랭킹, 펀칭 가공.
ㄷ) 토글 프레스(TOGGLE PRESS)
크랭크의 회전운동을 다수의 링크장치로 펀치에 전달하도록 한 프레스이며 순간적인 충격을 주지 않고 가공 행정의 끝에서 큰 힘을 발생시킴.
주용도는 블랭킹, 압인, 압출가공.
ㄹ) 너클 프레스(KNUCLE PRESS)
플라이휠의 회전운동을 크랭크 기구에 의해 직선운동으로 바꾸고 이를 너클 기구를 이용하여 슬라이드(램)를 상하로 직선운동시키는 프레스이며 하사점 부근에서 속도가 매우 느려지는 특징이 있음.
주용도는 압인, 냉간단조.
ㅁ) 마찰 프레스(FRICTION PRESS)
플라이휠의 회전력을 마찰차에 전달하며 나사축 바퀴를 마찰차와 접촉시켜 나사축의 회전으로 슬라이드(램)를 상하로 작동시키면서 가공력을 얻는 프레스로 가공정도가 좋지 않고 생산속도도 느림.
주용도는 굽힘, 성형 가공.
이 외에도 랙 프레스, 캠 프레스, 스크루 프레스 등이 있음.
(나) 액압 프레스
유체의 압력에 의해 슬라이드(램)를 작동시키는 프레스로 수압, 유압, 공압 프레스가 있음.
작동 행정을 임의로 조정할 수 있음.
행정에 관계없이 가공력을 가짐.
큰 용량의 가공이 가능함.
과부하가 발생하지 않음.
(다) 기계 프레스와 액압 프레스의 비교
항목 | 기계 프레스 | 액압 프레스 |
---|---|---|
생산속도 | 빠름 | 느림 |
스트로크 | 600~1000(mm) | 기계 프레스보다 제한이 적음 |
스트로크의 변화 | 변화를 주기 힘듦 | 변화를 줄 수 있음 |
스트로크 종단 위치결정 | 정확 | 부정확 |
가압 속도 조절 유무 |
무 | 유 |
가압력 조절 | 어려움 | 쉬움 |
가압력 유지 유무 |
무 | 유 |
과부하 유무 | 유 | 무 |
보수 유지 | 용이함 | 유체 누출 등에 주의가 필요함 |
프레스의 최대 능력 | 4,000t(판금), 9,000t(단조) | 200,000t(단조) |
(2) 프레임 형식에 따른 분류
1) C형 프레임 프레스 기계
프레임의 전면이 C형으로 개방되어 있으며 슬라이드(램)의 위치가 프레스 중심보다 앞쪽에 위치한 프레스.
200t 이하의 소형 프레스에 주로 사용되며 소재의 취급이 용이하나 앞 벌어짐 현상이 발생할 우려가 있음.
2) H형 프레임 프레스 기계
프레임의 형상이 상자형이며 슬라이드(램)의 위치가 프레스의 중심에 있는 프레스.
300t 이상의 중대형 프레스에 주로 사용되며 구조가 안정적이라서 앞 벌어짐이 발생하지 않음.
3) 4주형 프레임 프레스 기계
프레스의 상부구조인 크라운 부위와 하부구조인 베드 부위가 4개의 기둥에 의해 지지되는 프레스.
특수 용도로 사용하는 프레스로 주로 소형 프레스에 적용되며 금형의 취급이 용이하고 유압 성형에 적합함.
사면이 개방되어 있어 금형 탈부착이 용이하고 유압 유니트를 프레임 상부 또는 후면에 설치함으로써 소형화가 가능함.
(3) 구조 및 가공방법에 따른 분류
1) 슬라이드(램) 개수에 따른 분류
(가) 단동 프레스
슬라이드(램) 개수가 1개인 프레스.
(나) 복동 프레스
슬라이드(램) 개수가 2개인 프레스로 블랭킹과 드로잉을 동시에 하거나 딥 드로잉, 복잡한 굽힘 작업에 사용되는 프레스.
요즘은 복동 프레스가 점차 줄어드는 추세로 이는 드로잉 가공이 다이 쿠션의 발달로 인해 대부분의 가공을 단동 프레스에서 충분히 수행할 수 있기 때문.
(다) 3동 프레스
정밀 전단을 위한 파인 블랭킹 프레스가 여기에 속함.
(라) 4동 프레스
2) 슬라이드(램) 운동 방향에 따른 분류
(가) 수직형 프레스
(나) 수평형 프레스
(다) 경사형 프레스
(4) 특수 프레스
1) 전단기(SHEARING PRESS)
판재를 블레이드(직선 날)를 이용하여 원하는 형상으로 절단하는 프레스로 더블 크랭크 프레스가 대표적임.
2) 절곡기(PRESS BRAKE)
넓은 판재를 직선으로 굽히기 위한 전용기.
3) 파인 블랭킹 프레스(FINE BLANKING PRESS)
정밀 전단을 위한 프레스.
4) 다이 스포팅 프레스(DIE SPOTTING PRESS)
프레스 금형 제작이 완료되면 시험작업을 하면서 금형의 수정을 용이하게 하기 위한 시험작업용 프레스로 프레스에 금형이 장착된 상태에서도 수정•보완이 가능함.
5) 트랜스퍼 프레스(TRANSFER PRESS)
1대에 프레스에 여러 대의 금형을 설치하고 금형과 금형 사이를 이송 장치에 의해 소재를 자동으로 이동시키면서 연속 작업을 할 수 있도록 하는 전용의 프레스로 박판 제품 성형에 유리함.
6) 크랭크리스 프레스(CRANKLESS PRESS)
크랭크 프레스와 마찬가지로 회전운동을 직선운동으로 바꾸어 슬라이드(램)에 전달하는 방식은 동일하지만 하중 능력과 강성을 높이기 위해 크랭크가 아닌 직선의 회전축과 편심 캠으로 구성된 회전 기구를 사용한 프레스.
7) OBI 프레스(OPEN BACK INCLINABLE PRESS)
프레스의 후면이 개방되어 있어 제품 취출을 쉽게 할 수 있고 프레스 프레임을 경사지게 할 수 있어 중력에 의해 제품이 쉽게 미끄러질 수 있도록 하여 슈트(CHUTE)가 필요 없는 크랭크 프레스.
150t 이하의 중소형 프레스에 많이 사용되고 있는 단동식 C 프레임 프레스임.
8) 멀티 슬라이드 포머(MULT-SLIDE FORMER)
박판재의 스프링, 링, 전자 부품류 등 복잡한 굽힘 가공의 제품일 경우 같은 반경 방향으로 여러 개의 슬라이드(램)에 펀치를 부착시켜 순차적으로 성형하면서 완성품을 만드는 성형기.
☞ 그밖에 프레스 기계의 용어로는 마이크로 인칭이 있는데 이는 금형 교환 시 슬라이드(램)의 금형 높이를 쉽게 조절하고 미세 스트로크를 제어하는 장치입니다.
3. 프레스의 능력과 사양
(1) 능력
1) 하중(압력) 능력(t)
프레스 가공에 있어 크랭크축, 슬라이드(램), 본체 등이 안전하게 견딜 수 있는 최대 하중을 톤(t)으로 표시.
2) 토크 능력(mm)
하중 능력의 발생이 가능한 위치를 하사점으로부터 떨어진 거리.
프레스 가공을 할 때 최대 하중이 토크 능력 이내에 있도록 금형을 설치하는 것이 중요함.
3) 일의 능력(kg•m, t•mm)
1회 가공에 사용할 수 있는 최대 일의 양.
딥 드로잉의 경우에는 프레스의 능력 검토에 이용함.
(2) 사양
1) 다이 높이(DIE HEIGHT)
프레스의 슬라이드(램) 높이를 하사점으로 내리고 슬라이드(램) 조절 나사를 이용하여 슬라이드(램)의 위치를 최대로 올린 상태에서 볼스터 윗면에서부터 슬라이드(램) 밑면까지의 거리.
프레스에 금형을 실제로 설치 가능한 공간을 말함.
2) 셔트 높이(SHUT HEIGHT)
금형의 높이가 너무 높아 프레스에 설치하기 어려울 경우 볼스터를 떼고 프레스 베드 위에 직접 금형을 설치할 수 있는데 이때 슬라이드(램) 밑면에서 베드 사이의 거리를 말함.
3) 슬라이드(램) 조절량
금형을 프레스에 설치할 때 금형의 높이에 맞춰서 볼스터 윗면 사이에 거리를 조절하여 슬라이드와 금형이 접촉되도록 해야 함.
크랭크 프레스에서는 커넥팅 로드에 나사에 의한 높이 조절장치가 있고 조절할 수 있는 길이를 슬라이드(램) 조절량이라 함.
4) 스트로크수(SPM, 행정수)
슬라이드(램)가 1분 동안 상하로 움직일 수 있는 횟수.
크랭크 축의 매분 회전수와 동일하며 소형은 30~80(spm), 대형은 10~30(spm) 정도임.
5) 스트로크(행정)
슬라이드(램)의 최대 운동 거리로서 가공할 수 있는 제품의 최대 높이가 결정됨.
4. 프레스 가공의 자동화
(1) 자동화 도입 시 장•단점
1) 장점
① 생산량의 증가.
② 인건비의 절약.
③ 숙련된 작업자 불필요.
④ 동일 조건의 작업 시 제품의 정밀도 향상.
⑤ 재료의 절감.
⑥ 작업 공간의 절약.
⑦ 안전성의 향상.
⑧ 반가공품의 재고가 쌓이지 않음.
⑨ 생산관리가 용이.
⑩ 동종 업계에 대한 경쟁력의 강화.
2) 단점
① 설비가 많이 필요.
② 재료의 치수 공차가 정확해야 함.
③ 금형의 제작 비용 상승.
④ 금형 설계의 난이도가 높음.
⑤ 소량생산에 부적합.
⑥ 자동화 설비에 대한 지식이 필요.
⑦ 제품의 변화에 의한 고가 자동화 장치의 사용이 용이하지 못한 불안감.
⑧ 자동화 설비 유지 및 보수가 어려움.
(2) 자동화 설비 구성
1) 코일 소재를 이용한 자동화 구성
적재장치 ▷ 교정장치 ▷ 이송장치 ▷ 프레스 ▷ 취출장치
2) 1차 가공품을 이용한 자동화 구성
적재장치 ▷ 정돈장치 ▷ 분리장치 ▷ 이송장치 ▷ 프레스 ▷ 취출장치
3) 자동화 구성 장치
(가) 적재장치
원재료, 소재 또는 반가공 제품을 가공하기 위하여 적재하거나 투입하고 정확한 방향과 위치로 배치하거나 정렬시켜주는 장치.
ㄱ)코일 소재의 경우
① 릴 스탠드(REEK STAND)
경화중용, 코일재의 내경을 지지.
② 크레이들(CRADLE)
중하중용, 코일 소재의 외경을 지지.
③ 언코일러(UNCOILER)
중하중용, 코일재의 내경을 지지.
④ 턴테이블(TURN TABLE, ROTARIAN)
코일 소재를 수평으로 설치.
ㄴ) 스트립 소재의 경우
적층 된 판재로부터 소재를 1장씩 분리하는 장치인 디스태커(DESTACKER)를 사용함.
ㄷ) 1차 가공품의 경우
호퍼에 1차 가공품을 적재하고 컨베이어나 슈트 등에 의해 볼 피더로 이송하여 부품을 정렬하고 리니어 피더를 통해 프레스로 이송함.
(나) 교정장치
적재장치로부터 이송 된 소재를 상하로 미세한 소성변형을 주어 소재의 평면도를 교정해 주는 장치.
언코일러나 크레이들의 경우에는 교정장치를 포함하여 제작되는 추세임.
(다) 이송장치
적재 장치로부터 보내온 원재료, 소재 또는 반가공 제품을 정확한 방향으로 가공 사이클에 맞게 가공 작업 기기로 보내거나 빼내는 장치.
ㄱ) 코일 소재 이송
① 롤 피더(ROLLL FEEDER)
상하 롤러 사이의 마찰력에 의해 한쪽 방향으로만 회전하는 클러치 베어링에 의해 소재를 앞으로 이송하는 장치.
☞ 릴리싱이란 프레스가 소재를 누르는 순간 금형의 가이드 핀이 소재에 뚫린 가이드 구멍에 삽입되어 위치를 결정 하기 위하여 일시적으로 소재를 들어주는 것을 말합니다.
② 그리퍼 피더(GRIPPER FEEDER)
롤 피더와 방식은 유사하나 이송 길이를 조절할 수 있어 폭이 좁은 재료의 짧은 피치 이송에 사용함.
③ 에어 피더(AIR FEEDER)
공압에 의해 그리퍼(GRIPPER)가 소재를 잡아 앞으로 이송하는 장치.
④ 캠 피더(CAM FEEDER)
고속 프레스의 전용 피더로써 프레스로부터 동력을 전달받아 분할 캠의 분할수, 변환 기어 또는 변환 롤러의 선택에 따라 짧은 피치 고속 이송에 사용함.
⑤ NC 롤 피더(NC ROLL FEEDER)
NC 조작을 통한 소재의 이송량 설정이 간단하고 다품종 소량생산에서 활용성이 높으며 소재 및 이송 제약이 적어 프레스 자동화에 사용함.(NC ROLL FEEDER)
ㄴ) 1차 가공품 이송
볼 피더의 진동과 회전으로 부품을 정렬하고 리니어 피더를 통해 프레스로 이송함.
트랜스퍼 피더(TRANSFER FEEDER)
1차 가공품을 그립 장치에 의해 각각의 공정으로 이송하는 장치로 가공품의 크기가 작을 경우 1대의 트랜스퍼 피더로 소재 이송이 가능함.
가공품의 크기가 클 경우에는 여러 대의 프레스를 설치하고 프레스와 프레 사이에 있는 트랜스퍼 피더로 소재를 이송하여 작업함.
(라) 취출장치
가공이 끝난 제품을 자동으로 취출하는 장치.
(마) 급속 금형 교환장치
금형 탈•부착에 소요되는 시간과 인력의 낭비를 제거하기 위한 장치.
5. 프레스 기계 안전장치
(1) 비상 정지 스위치
누름 버튼으로 작동된 이후 수동으로 복귀시킬 때까지 회로가 자동으로 복귀되지 않고 슬라이드(램)를 시동 상태로 복귀한 것이 아니면 슬라이드(램)가 작동되지 않는 구조임.
(2) 키락(KEY LOCK)
일종의 전환 키 스위치로 주전동기의 통전을 ON/OFF.
키를 작업자가 가지고 있는 한 주전동기의 운전을 할 수 없어 안전함.
(3) 안전 블록 및 안전 플러그
슬라이드(램) 및 상부 금형 등의 무게를 지탱할 수 있는 강도 유지.
안전 블록 사용 시 슬라이드(램) 불시 작동 방지를 위한 인터 록 기능 구비.
기계 프레스에서 볼스터 각 변의 길이가 1,500mm 미만이거나 다이 높이가 700mm 미만이면 안전 플러그 또는 키락으로 대체 가능.
안전 플러그는 각 조작 위치마다 비치하고 구조상 안전 블록 설치가 곤란한 경우 슬라이드(램) 록킹 핀 방식 가능.
(4) 오버 런 감시장치
구동 장치에 결함이 발생되면 즉시 정지 신호를 보내고 결함이 제거될 때까지 가동 중지.
급정지가 필요 없는 전용 프레스, 자동 급송 프레스는 예외.
클러치, 브레이크 작동용 전환 밸브의 배기구 배출 저항 증가 시, 브레이크 패드의 마모 및 오일 등의 불순물 유입으로 브레이크 성능 저하 시 작동함.
(5) 재가동 방지 장치
1행정 후 정지가 안되고 계속해서 행정이 진행되는 것을 재가동이 된다고 하고 재가동을 멈추게 하는 장치로 연속 행정 선택 시에는 작동하지 않음.
(6) 1행정 1정지장치
프레스 작동 후 누름 버튼 등을 계속 누르고 있어도 슬라이드(램)가 1행정의 작업을 마치고 작동하기 전 위치에서 정지하는 장치이며, 상사점 정지기구와 연결하여 사용할 수 있음.
(7) 급정지 장치
위험 또는 이상을 해당 프레스가 검출하여 자동으로 슬라이드(램)의 운동을 즉시 정지시키는 장치.
급정지 장치가 작동 후에는 안전상태로 복귀하여도 재기동 조작을 하지 않으면 슬라이드(램)가 작동하지 않도록 하는 재가동 방지 장치가 구비되어야 함.
6. 프레스 기계 방호장치
(1) 게이트 가드식
슬라이드(램)의 하강 중에는 안으로 손이 들어가지 못하도록 하며 가드를 닫지 않으면 슬라이드(램)를 작동시킬 수 없는 장치.
특징
① 2차 가공에 적합함.
② 기계 고장에 의한 이상 행정, 공구 파손 시에도 안전함.
③ 금형 교환 빈도수가 적은 프레스에 적합함.
④ 게이트는 5mm 이상 두께를 갖는 투명 플라스틱을 사용할 것.
(2) 양수 조작식
2개의 누름 버튼을 위험점으로부터 안전거리 이상을 격리시켜 설치하고 양손으로 동시에 조작하지 않으면 슬라이드(램)가 작동하지 않는 장치.
특징
① 가장 많이 사용.
② 급정지 기구가 부착된 마찰식 클러치 프레스에 적합함.
③ 급정지 성능이 약화되지 않는 한 위험 구역으로부터 작업자를 보호할 수 있음.
④ 굽힘 가공 등 2차 가공에 적합함.
⑤ 급정지 기능이 양호하여 작업능률이 좋음.
(3) 손 쳐내기식
슬라이드(램)에 레버나 링크 혹은 캠으로 연결된 손 쳐내기 봉에 의해 슬라이드(램)의 하강에 앞서 위험 단계에서 손을 쳐내는 장치.
특징
① 규칙적인 프레스의 행정에 대하여 기계 고장에 의한 이상 행정 시 효과가 있음.
② 소형 프레스에 적합함.
③ 쉽게 조정할 수 있음.
④ 양측면은 무방비 상태가 되는 단점이 있음.
(4) 감응식
슬라이드(램)가 하강 중일 때 손이나 신체의 일부가 금형에 접근하는 것을 검출 기구를 통해서 감지하고 제어회로를 통하여 자동적으로 슬라이드(램)를 정지시키는 장치.
특징
① 방호장치 설치가 어려운 프레스에 적합함.
② 시계(야)가 차단되지 않음.
③ 위험 구역을 보호하려면 상당히 많은 수의 광선이 필요함.
④ 위험 구역으로부터 어느 정도 떨어진 거리에 설치되어야 효과가 있음.
⑤ 슬라이드(램) 행정기간 동안에 프레스를 정지시킬 수 있는 경우에만 사용 가능.
⑥ 기계적 고장에 의한 이상 행정에는 효과가 없음.
(5) 수인식
슬라이드(램)와 작업자 손을 끈으로 연결하여 슬라이드(램) 하강 시 작업자의 손을 당겨서 위험에 벗어날 수 있도록 하는 장치.
수인 줄의 재료는 합성 섬유이어야 하고 직경은 Φ4mm 이상, 전단 하중은 조절부를 설치한 상태에서 150kg 이상이어야 함.
리스트 밴드의 재료는 피혁 등을 사용하고 수인 줄과의 연결부는 50kg 이상의 정하중을 견딜 수 있어야 함.
특징
① 설치가 쉽고 유지 보수가 용이하며 비용이 저렴함.
② 수인 줄의 당기는 양은 볼스터의 전후 길이(세로 길이)의 ½ 이상이어야 함.
③ 슬라이드(램)가 불시에 하강할 경우에도 재해 예방이 가능함.
④ 끈의 길이를 적절하게 조절할 수 있어 수공구 사용이 필요하지 않음.
⑤ 행정수를 120spm 이하, 행정 길이는 40mm 이상으로 제한함.
⑥ 작업 반경의 제한으로 행동에 제약을 받아서 작업자를 구속할 수 있음.
⑦ 작업 변경 시 마다 수인 줄의 길이를 조절하여야 함.
7. 서보 프레스
(1) 개요
기존 기계식 프레스의 단점인 가압부의 속도나 가압 횟수 제어의 어려움을 개선한 프레스.
서보 프레스는 가압부의 작동을 CNC와 서보 모터로 제어하기 때문에 복잡한 가압이 가능하고 가공 시 속도나 위치, 가압력을 수치로 설정하여 제어가 손쉬움.
(2) 개발 배경
제조업 전반으로 환경 문제 대응을 피할 수 없어 가볍고 강한 재료를 통해 재료비와 설비비가 상승하지 않도록 하는 방법을 모색하려는 경향이 두드러지기 시작했고 거기에 고정도·고능률 프레스의 도입에 필요성이 대두되었으며 이로 인해 프레스 가공에 있어 초고장력 강판과 서보 프레스가 등장하는 계기가 됨.
(3) 구조
(4) 특징
금형 수명, 가공 정도, 생산 속도의 향상 등과 같은 프레스 가공의 한계를 금형으로 극복하기 힘들어지자 마침 서보 모터가 대형화됨을 계기로 유압 프레스의 성형성과 생산성, 가공 정도의 향상을 실현시키기 위해 서보 프레스가 개발됨.
또한, 이산화탄소와 에너지 절감 효과를 창출할 수 있음.
(5) 서보 프레스 프리 모션과 기계식 프레스의 프로파일 비교
(6) 서보 프레스를 사용하는 이유
수율과 생산성을 동시에 추구.
초고장력 강판, 알루미늄, 티타늄과 같은 난가공재 가공이 가능.
저소음과 저진동.
에너지 절약.
(7) 기술동향
프레스는 압축에너지를 발생시키는 구조에 따라 기계식과 유압식으로 대별됨.
하지만 프레스에서도 에너지 및 자원절약, 이용효율, 편리성 측면에서 유압식보다 유리한 전동방식으로 바뀌는 추세.
서보 프레스는 에너지 회생 시스템을 갖추고 있어 작동유의 누설에 의한 열에너지 손실을 보완할 수 있기 때문에 프레스 기계 기술의 중요한 흐름임.
그러나 초기 투자비용, 서보 모터의 소음과 고주파 발생, 고가의 에너지 회생장치 등이 부담이나 향후 이러한 문제를 극복하면 서보 프레스가 프레스 가공에 있어 주종의 위치를 점할 수 있을 것으로 전망됨.
상당히 긴 글이 되었는데도 프레스에 대해서 다 담지 못한 것 같아 아쉬움이 큽니다.
부족한 부분은 추후에라도 채워나갈 수 있도록 노력할 예정입니다.
2020년 04월 23일
-
감사합니다. 전문지식이 출중하십니다.
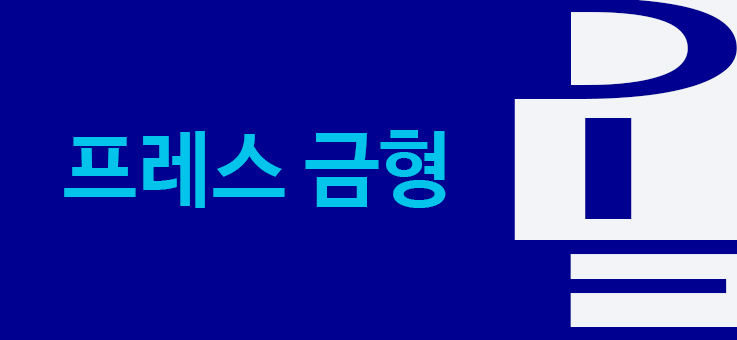
HOME → DIE CATEGORIES →
프레스 금형 2
제2장 프레스 기계
1. 프레스 기계 개요
프레스는 2개 이상의 서로 대응하는 공구를 사용하여 공구 사이에 금속 또는 비금속 판재를 놓고 강한 힘으로 가압하여 전단, 굽힘, 드로잉, 압축 가공을 하는 기계를 말합니다.
프레스는 동력원의 작동 기구에 따라, 구조 및 가공 방법에 따라, 프레임 형식에 따라 분류 기준이 다르지만 일반적으로 동력원의 작동 기구에 따라 분류하고 있습니다.
프레스의 효율은 가압 능력을 톤(ton)으로 표시합니다.
2. 종류
(1) 동력원의 작동 기구에 따른 분류
1) 인력 프레스 기계
수동 프레스로서 스크루 프레스, 수동 편심 프레스가 있으며 레버 조작 구조인 족답 프레스가 있고 얇은 판재 펀칭에 이용됨.
2) 동력 프레스 기계
(가) 기계 프레스
기계의 동력을 이용하여 크랭크 등의 기구로 슬라이드(램)를 작동시키는 프레스.
ㄱ) 크랭크 프레스(CRANK PRESS, POWER PRESS)
크랭크축과 연결봉의 조합으로 축의 회전운동을 직선운동으로 전환시켜 가압하는데 일명 파워 프레스라고도 함.
제작이 쉽고 스트로크 하단 위치가 정확하게 결정되며 슬라이드(램) 운동 곡선이 비교적 무난하고 각종 가공에 유리하여 가장 많이 사용되고 있음.
ㄴ) 편심 프레스(ECCENTRIC PRESS)
클러치의 작동에 따라 편심 주축이 회전하며 그 일단에 상하운동하는 슬라이드(램)가 있고 형틀을 고정하여 가공하는 프레스.
주용도는 뽑기 작업, 블랭킹, 펀칭 가공.
ㄷ) 토글 프레스(TOGGLE PRESS)
크랭크의 회전운동을 다수의 링크장치로 펀치에 전달하도록 한 프레스이며 순간적인 충격을 주지 않고 가공 행정의 끝에서 큰 힘을 발생시킴.
주용도는 블랭킹, 압인, 압출가공.
ㄹ) 너클 프레스(KNUCLE PRESS)
플라이휠의 회전운동을 크랭크 기구에 의해 직선운동으로 바꾸고 이를 너클 기구를 이용하여 슬라이드(램)를 상하로 직선운동시키는 프레스이며 하사점 부근에서 속도가 매우 느려지는 특징이 있음.
주용도는 압인, 냉간단조.
ㅁ) 마찰 프레스(FRICTION PRESS)
플라이휠의 회전력을 마찰차에 전달하며 나사축 바퀴를 마찰차와 접촉시켜 나사축의 회전으로 슬라이드(램)를 상하로 작동시키면서 가공력을 얻는 프레스로 가공정도가 좋지 않고 생산속도도 느림.
주용도는 굽힘, 성형 가공.
이 외에도 랙 프레스, 캠 프레스, 스크루 프레스 등이 있음.
(나) 액압 프레스
유체의 압력에 의해 슬라이드(램)를 작동시키는 프레스로 수압, 유압, 공압 프레스가 있음.
작동 행정을 임의로 조정할 수 있음.
행정에 관계없이 가공력을 가짐.
큰 용량의 가공이 가능함.
과부하가 발생하지 않음.
(다) 기계 프레스와 액압 프레스의 비교
항목 | 기계 프레스 | 액압 프레스 |
---|---|---|
생산속도 | 빠름 | 느림 |
스트로크 | 600~1000(mm) | 기계 프레스보다 제한이 적음 |
스트로크의 변화 | 변화를 주기 힘듦 | 변화를 줄 수 있음 |
스트로크 종단 위치결정 | 정확 | 부정확 |
가압 속도 조절 유무 |
무 | 유 |
가압력 조절 | 어려움 | 쉬움 |
가압력 유지 유무 |
무 | 유 |
과부하 유무 | 유 | 무 |
보수 유지 | 용이함 | 유체 누출 등에 주의가 필요함 |
프레스의 최대 능력 | 4,000t(판금), 9,000t(단조) | 200,000t(단조) |
(2) 프레임 형식에 따른 분류
1) C형 프레임 프레스 기계
프레임의 전면이 C형으로 개방되어 있으며 슬라이드(램)의 위치가 프레스 중심보다 앞쪽에 위치한 프레스.
200t 이하의 소형 프레스에 주로 사용되며 소재의 취급이 용이하나 앞 벌어짐 현상이 발생할 우려가 있음.
2) H형 프레임 프레스 기계
프레임의 형상이 상자형이며 슬라이드(램)의 위치가 프레스의 중심에 있는 프레스.
300t 이상의 중대형 프레스에 주로 사용되며 구조가 안정적이라서 앞 벌어짐이 발생하지 않음.
3) 4주형 프레임 프레스 기계
프레스의 상부구조인 크라운 부위와 하부구조인 베드 부위가 4개의 기둥에 의해 지지되는 프레스.
특수 용도로 사용하는 프레스로 주로 소형 프레스에 적용되며 금형의 취급이 용이하고 유압 성형에 적합함.
사면이 개방되어 있어 금형 탈부착이 용이하고 유압 유니트를 프레임 상부 또는 후면에 설치함으로써 소형화가 가능함.
(3) 구조 및 가공방법에 따른 분류
1) 슬라이드(램) 개수에 따른 분류
(가) 단동 프레스
슬라이드(램) 개수가 1개인 프레스.
(나) 복동 프레스
슬라이드(램) 개수가 2개인 프레스로 블랭킹과 드로잉을 동시에 하거나 딥 드로잉, 복잡한 굽힘 작업에 사용되는 프레스.
요즘은 복동 프레스가 점차 줄어드는 추세로 이는 드로잉 가공이 다이 쿠션의 발달로 인해 대부분의 가공을 단동 프레스에서 충분히 수행할 수 있기 때문.
(다) 3동 프레스
정밀 전단을 위한 파인 블랭킹 프레스가 여기에 속함.
(라) 4동 프레스
2) 슬라이드(램) 운동 방향에 따른 분류
(가) 수직형 프레스
(나) 수평형 프레스
(다) 경사형 프레스
(4) 특수 프레스
1) 전단기(SHEARING PRESS)
판재를 블레이드(직선 날)를 이용하여 원하는 형상으로 절단하는 프레스로 더블 크랭크 프레스가 대표적임.
2) 절곡기(PRESS BRAKE)
넓은 판재를 직선으로 굽히기 위한 전용기.
3) 파인 블랭킹 프레스(FINE BLANKING PRESS)
정밀 전단을 위한 프레스.
4) 다이 스포팅 프레스(DIE SPOTTING PRESS)
프레스 금형 제작이 완료되면 시험작업을 하면서 금형의 수정을 용이하게 하기 위한 시험작업용 프레스로 프레스에 금형이 장착된 상태에서도 수정•보완이 가능함.
5) 트랜스퍼 프레스(TRANSFER PRESS)
1대에 프레스에 여러 대의 금형을 설치하고 금형과 금형 사이를 이송 장치에 의해 소재를 자동으로 이동시키면서 연속 작업을 할 수 있도록 하는 전용의 프레스로 박판 제품 성형에 유리함.
6) 크랭크리스 프레스(CRANKLESS PRESS)
크랭크 프레스와 마찬가지로 회전운동을 직선운동으로 바꾸어 슬라이드(램)에 전달하는 방식은 동일하지만 하중 능력과 강성을 높이기 위해 크랭크가 아닌 직선의 회전축과 편심 캠으로 구성된 회전 기구를 사용한 프레스.
7) OBI 프레스(OPEN BACK INCLINABLE PRESS)
프레스의 후면이 개방되어 있어 제품 취출을 쉽게 할 수 있고 프레스 프레임을 경사지게 할 수 있어 중력에 의해 제품이 쉽게 미끄러질 수 있도록 하여 슈트(CHUTE)가 필요 없는 크랭크 프레스.
150t 이하의 중소형 프레스에 많이 사용되고 있는 단동식 C 프레임 프레스임.
8) 멀티 슬라이드 포머(MULT-SLIDE FORMER)
박판재의 스프링, 링, 전자 부품류 등 복잡한 굽힘 가공의 제품일 경우 같은 반경 방향으로 여러 개의 슬라이드(램)에 펀치를 부착시켜 순차적으로 성형하면서 완성품을 만드는 성형기.
☞ 그밖에 프레스 기계의 용어로는 마이크로 인칭이 있는데 이는 금형 교환 시 슬라이드(램)의 금형 높이를 쉽게 조절하고 미세 스트로크를 제어하는 장치입니다.
3. 프레스의 능력과 사양
(1) 능력
1) 하중(압력) 능력(t)
프레스 가공에 있어 크랭크축, 슬라이드(램), 본체 등이 안전하게 견딜 수 있는 최대 하중을 톤(t)으로 표시.
2) 토크 능력(mm)
하중 능력의 발생이 가능한 위치를 하사점으로부터 떨어진 거리.
프레스 가공을 할 때 최대 하중이 토크 능력 이내에 있도록 금형을 설치하는 것이 중요함.
3) 일의 능력(kg•m, t•mm)
1회 가공에 사용할 수 있는 최대 일의 양.
딥 드로잉의 경우에는 프레스의 능력 검토에 이용함.
(2) 사양
1) 다이 높이(DIE HEIGHT)
프레스의 슬라이드(램) 높이를 하사점으로 내리고 슬라이드(램) 조절 나사를 이용하여 슬라이드(램)의 위치를 최대로 올린 상태에서 볼스터 윗면에서부터 슬라이드(램) 밑면까지의 거리.
프레스에 금형을 실제로 설치 가능한 공간을 말함.
2) 셔트 높이(SHUT HEIGHT)
금형의 높이가 너무 높아 프레스에 설치하기 어려울 경우 볼스터를 떼고 프레스 베드 위에 직접 금형을 설치할 수 있는데 이때 슬라이드(램) 밑면에서 베드 사이의 거리를 말함.
3) 슬라이드(램) 조절량
금형을 프레스에 설치할 때 금형의 높이에 맞춰서 볼스터 윗면 사이에 거리를 조절하여 슬라이드와 금형이 접촉되도록 해야 함.
크랭크 프레스에서는 커넥팅 로드에 나사에 의한 높이 조절장치가 있고 조절할 수 있는 길이를 슬라이드(램) 조절량이라 함.
4) 스트로크수(SPM, 행정수)
슬라이드(램)가 1분 동안 상하로 움직일 수 있는 횟수.
크랭크 축의 매분 회전수와 동일하며 소형은 30~80(spm), 대형은 10~30(spm) 정도임.
5) 스트로크(행정)
슬라이드(램)의 최대 운동 거리로서 가공할 수 있는 제품의 최대 높이가 결정됨.
4. 프레스 가공의 자동화
(1) 자동화 도입 시 장•단점
1) 장점
① 생산량의 증가.
② 인건비의 절약.
③ 숙련된 작업자 불필요.
④ 동일 조건의 작업 시 제품의 정밀도 향상.
⑤ 재료의 절감.
⑥ 작업 공간의 절약.
⑦ 안전성의 향상.
⑧ 반가공품의 재고가 쌓이지 않음.
⑨ 생산관리가 용이.
⑩ 동종 업계에 대한 경쟁력의 강화.
2) 단점
① 설비가 많이 필요.
② 재료의 치수 공차가 정확해야 함.
③ 금형의 제작 비용 상승.
④ 금형 설계의 난이도가 높음.
⑤ 소량생산에 부적합.
⑥ 자동화 설비에 대한 지식이 필요.
⑦ 제품의 변화에 의한 고가 자동화 장치의 사용이 용이하지 못한 불안감.
⑧ 자동화 설비 유지 및 보수가 어려움.
(2) 자동화 설비 구성
1) 코일 소재를 이용한 자동화 구성
적재장치 ▷ 교정장치 ▷ 이송장치 ▷ 프레스 ▷ 취출장치
2) 1차 가공품을 이용한 자동화 구성
적재장치 ▷ 정돈장치 ▷ 분리장치 ▷ 이송장치 ▷ 프레스 ▷ 취출장치
3) 자동화 구성 장치
(가) 적재장치
원재료, 소재 또는 반가공 제품을 가공하기 위하여 적재하거나 투입하고 정확한 방향과 위치로 배치하거나 정렬시켜주는 장치.
ㄱ)코일 소재의 경우
① 릴 스탠드(REEK STAND)
경화중용, 코일재의 내경을 지지.
② 크레이들(CRADLE)
중하중용, 코일 소재의 외경을 지지.
③ 언코일러(UNCOILER)
중하중용, 코일재의 내경을 지지.
④ 턴테이블(TURN TABLE, ROTARIAN)
코일 소재를 수평으로 설치.
ㄴ) 스트립 소재의 경우
적층 된 판재로부터 소재를 1장씩 분리하는 장치인 디스태커(DESTACKER)를 사용함.
ㄷ) 1차 가공품의 경우
호퍼에 1차 가공품을 적재하고 컨베이어나 슈트 등에 의해 볼 피더로 이송하여 부품을 정렬하고 리니어 피더를 통해 프레스로 이송함.
(나) 교정장치
적재장치로부터 이송 된 소재를 상하로 미세한 소성변형을 주어 소재의 평면도를 교정해 주는 장치.
언코일러나 크레이들의 경우에는 교정장치를 포함하여 제작되는 추세임.
(다) 이송장치
적재 장치로부터 보내온 원재료, 소재 또는 반가공 제품을 정확한 방향으로 가공 사이클에 맞게 가공 작업 기기로 보내거나 빼내는 장치.
ㄱ) 코일 소재 이송
① 롤 피더(ROLLL FEEDER)
상하 롤러 사이의 마찰력에 의해 한쪽 방향으로만 회전하는 클러치 베어링에 의해 소재를 앞으로 이송하는 장치.
☞ 릴리싱이란 프레스가 소재를 누르는 순간 금형의 가이드 핀이 소재에 뚫린 가이드 구멍에 삽입되어 위치를 결정 하기 위하여 일시적으로 소재를 들어주는 것을 말합니다.
② 그리퍼 피더(GRIPPER FEEDER)
롤 피더와 방식은 유사하나 이송 길이를 조절할 수 있어 폭이 좁은 재료의 짧은 피치 이송에 사용함.
③ 에어 피더(AIR FEEDER)
공압에 의해 그리퍼(GRIPPER)가 소재를 잡아 앞으로 이송하는 장치.
④ 캠 피더(CAM FEEDER)
고속 프레스의 전용 피더로써 프레스로부터 동력을 전달받아 분할 캠의 분할수, 변환 기어 또는 변환 롤러의 선택에 따라 짧은 피치 고속 이송에 사용함.
⑤ NC 롤 피더(NC ROLL FEEDER)
NC 조작을 통한 소재의 이송량 설정이 간단하고 다품종 소량생산에서 활용성이 높으며 소재 및 이송 제약이 적어 프레스 자동화에 사용함.(NC ROLL FEEDER)
ㄴ) 1차 가공품 이송
볼 피더의 진동과 회전으로 부품을 정렬하고 리니어 피더를 통해 프레스로 이송함.
트랜스퍼 피더(TRANSFER FEEDER)
1차 가공품을 그립 장치에 의해 각각의 공정으로 이송하는 장치로 가공품의 크기가 작을 경우 1대의 트랜스퍼 피더로 소재 이송이 가능함.
가공품의 크기가 클 경우에는 여러 대의 프레스를 설치하고 프레스와 프레 사이에 있는 트랜스퍼 피더로 소재를 이송하여 작업함.
(라) 취출장치
가공이 끝난 제품을 자동으로 취출하는 장치.
(마) 급속 금형 교환장치
금형 탈•부착에 소요되는 시간과 인력의 낭비를 제거하기 위한 장치.
5. 프레스 기계 안전장치
(1) 비상 정지 스위치
누름 버튼으로 작동된 이후 수동으로 복귀시킬 때까지 회로가 자동으로 복귀되지 않고 슬라이드(램)를 시동 상태로 복귀한 것이 아니면 슬라이드(램)가 작동되지 않는 구조임.
(2) 키락(KEY LOCK)
일종의 전환 키 스위치로 주전동기의 통전을 ON/OFF.
키를 작업자가 가지고 있는 한 주전동기의 운전을 할 수 없어 안전함.
(3) 안전 블록 및 안전 플러그
슬라이드(램) 및 상부 금형 등의 무게를 지탱할 수 있는 강도 유지.
안전 블록 사용 시 슬라이드(램) 불시 작동 방지를 위한 인터 록 기능 구비.
기계 프레스에서 볼스터 각 변의 길이가 1,500mm 미만이거나 다이 높이가 700mm 미만이면 안전 플러그 또는 키락으로 대체 가능.
안전 플러그는 각 조작 위치마다 비치하고 구조상 안전 블록 설치가 곤란한 경우 슬라이드(램) 록킹 핀 방식 가능.
(4) 오버 런 감시장치
구동 장치에 결함이 발생되면 즉시 정지 신호를 보내고 결함이 제거될 때까지 가동 중지.
급정지가 필요 없는 전용 프레스, 자동 급송 프레스는 예외.
클러치, 브레이크 작동용 전환 밸브의 배기구 배출 저항 증가 시, 브레이크 패드의 마모 및 오일 등의 불순물 유입으로 브레이크 성능 저하 시 작동함.
(5) 재가동 방지 장치
1행정 후 정지가 안되고 계속해서 행정이 진행되는 것을 재가동이 된다고 하고 재가동을 멈추게 하는 장치로 연속 행정 선택 시에는 작동하지 않음.
(6) 1행정 1정지장치
프레스 작동 후 누름 버튼 등을 계속 누르고 있어도 슬라이드(램)가 1행정의 작업을 마치고 작동하기 전 위치에서 정지하는 장치이며, 상사점 정지기구와 연결하여 사용할 수 있음.
(7) 급정지 장치
위험 또는 이상을 해당 프레스가 검출하여 자동으로 슬라이드(램)의 운동을 즉시 정지시키는 장치.
급정지 장치가 작동 후에는 안전상태로 복귀하여도 재기동 조작을 하지 않으면 슬라이드(램)가 작동하지 않도록 하는 재가동 방지 장치가 구비되어야 함.
6. 프레스 기계 방호장치
(1) 게이트 가드식
슬라이드(램)의 하강 중에는 안으로 손이 들어가지 못하도록 하며 가드를 닫지 않으면 슬라이드(램)를 작동시킬 수 없는 장치.
특징
① 2차 가공에 적합함.
② 기계 고장에 의한 이상 행정, 공구 파손 시에도 안전함.
③ 금형 교환 빈도수가 적은 프레스에 적합함.
④ 게이트는 5mm 이상 두께를 갖는 투명 플라스틱을 사용할 것.
(2) 양수 조작식
2개의 누름 버튼을 위험점으로부터 안전거리 이상을 격리시켜 설치하고 양손으로 동시에 조작하지 않으면 슬라이드(램)가 작동하지 않는 장치.
특징
① 가장 많이 사용.
② 급정지 기구가 부착된 마찰식 클러치 프레스에 적합함.
③ 급정지 성능이 약화되지 않는 한 위험 구역으로부터 작업자를 보호할 수 있음.
④ 굽힘 가공 등 2차 가공에 적합함.
⑤ 급정지 기능이 양호하여 작업능률이 좋음.
(3) 손 쳐내기식
슬라이드(램)에 레버나 링크 혹은 캠으로 연결된 손 쳐내기 봉에 의해 슬라이드(램)의 하강에 앞서 위험 단계에서 손을 쳐내는 장치.
특징
① 규칙적인 프레스의 행정에 대하여 기계 고장에 의한 이상 행정 시 효과가 있음.
② 소형 프레스에 적합함.
③ 쉽게 조정할 수 있음.
④ 양측면은 무방비 상태가 되는 단점이 있음.
(4) 감응식
슬라이드(램)가 하강 중일 때 손이나 신체의 일부가 금형에 접근하는 것을 검출 기구를 통해서 감지하고 제어회로를 통하여 자동적으로 슬라이드(램)를 정지시키는 장치.
특징
① 방호장치 설치가 어려운 프레스에 적합함.
② 시계(야)가 차단되지 않음.
③ 위험 구역을 보호하려면 상당히 많은 수의 광선이 필요함.
④ 위험 구역으로부터 어느 정도 떨어진 거리에 설치되어야 효과가 있음.
⑤ 슬라이드(램) 행정기간 동안에 프레스를 정지시킬 수 있는 경우에만 사용 가능.
⑥ 기계적 고장에 의한 이상 행정에는 효과가 없음.
(5) 수인식
슬라이드(램)와 작업자 손을 끈으로 연결하여 슬라이드(램) 하강 시 작업자의 손을 당겨서 위험에 벗어날 수 있도록 하는 장치.
수인 줄의 재료는 합성 섬유이어야 하고 직경은 Φ4mm 이상, 전단 하중은 조절부를 설치한 상태에서 150kg 이상이어야 함.
리스트 밴드의 재료는 피혁 등을 사용하고 수인 줄과의 연결부는 50kg 이상의 정하중을 견딜 수 있어야 함.
특징
① 설치가 쉽고 유지 보수가 용이하며 비용이 저렴함.
② 수인 줄의 당기는 양은 볼스터의 전후 길이(세로 길이)의 ½ 이상이어야 함.
③ 슬라이드(램)가 불시에 하강할 경우에도 재해 예방이 가능함.
④ 끈의 길이를 적절하게 조절할 수 있어 수공구 사용이 필요하지 않음.
⑤ 행정수를 120spm 이하, 행정 길이는 40mm 이상으로 제한함.
⑥ 작업 반경의 제한으로 행동에 제약을 받아서 작업자를 구속할 수 있음.
⑦ 작업 변경 시 마다 수인 줄의 길이를 조절하여야 함.
7. 서보 프레스
(1) 개요
기존 기계식 프레스의 단점인 가압부의 속도나 가압 횟수 제어의 어려움을 개선한 프레스.
서보 프레스는 가압부의 작동을 CNC와 서보 모터로 제어하기 때문에 복잡한 가압이 가능하고 가공 시 속도나 위치, 가압력을 수치로 설정하여 제어가 손쉬움.
(2) 개발 배경
제조업 전반으로 환경 문제 대응을 피할 수 없어 가볍고 강한 재료를 통해 재료비와 설비비가 상승하지 않도록 하는 방법을 모색하려는 경향이 두드러지기 시작했고 거기에 고정도·고능률 프레스의 도입에 필요성이 대두되었으며 이로 인해 프레스 가공에 있어 초고장력 강판과 서보 프레스가 등장하는 계기가 됨.
(3) 구조
(4) 특징
금형 수명, 가공 정도, 생산 속도의 향상 등과 같은 프레스 가공의 한계를 금형으로 극복하기 힘들어지자 마침 서보 모터가 대형화됨을 계기로 유압 프레스의 성형성과 생산성, 가공 정도의 향상을 실현시키기 위해 서보 프레스가 개발됨.
또한, 이산화탄소와 에너지 절감 효과를 창출할 수 있음.
(5) 서보 프레스 프리 모션과 기계식 프레스의 프로파일 비교
(6) 서보 프레스를 사용하는 이유
수율과 생산성을 동시에 추구.
초고장력 강판, 알루미늄, 티타늄과 같은 난가공재 가공이 가능.
저소음과 저진동.
에너지 절약.
(7) 기술동향
프레스는 압축에너지를 발생시키는 구조에 따라 기계식과 유압식으로 대별됨.
하지만 프레스에서도 에너지 및 자원절약, 이용효율, 편리성 측면에서 유압식보다 유리한 전동방식으로 바뀌는 추세.
서보 프레스는 에너지 회생 시스템을 갖추고 있어 작동유의 누설에 의한 열에너지 손실을 보완할 수 있기 때문에 프레스 기계 기술의 중요한 흐름임.
그러나 초기 투자비용, 서보 모터의 소음과 고주파 발생, 고가의 에너지 회생장치 등이 부담이나 향후 이러한 문제를 극복하면 서보 프레스가 프레스 가공에 있어 주종의 위치를 점할 수 있을 것으로 전망됨.
상당히 긴 글이 되었는데도 프레스에 대해서 다 담지 못한 것 같아 아쉬움이 큽니다.
부족한 부분은 추후에라도 채워나갈 수 있도록 노력할 예정입니다.
2020년 04월 23일
-
감사합니다. 전문지식이 출중하십니다.
감사합니다
감사합니다. 전문지식이 출중하십니다.
감사합니다