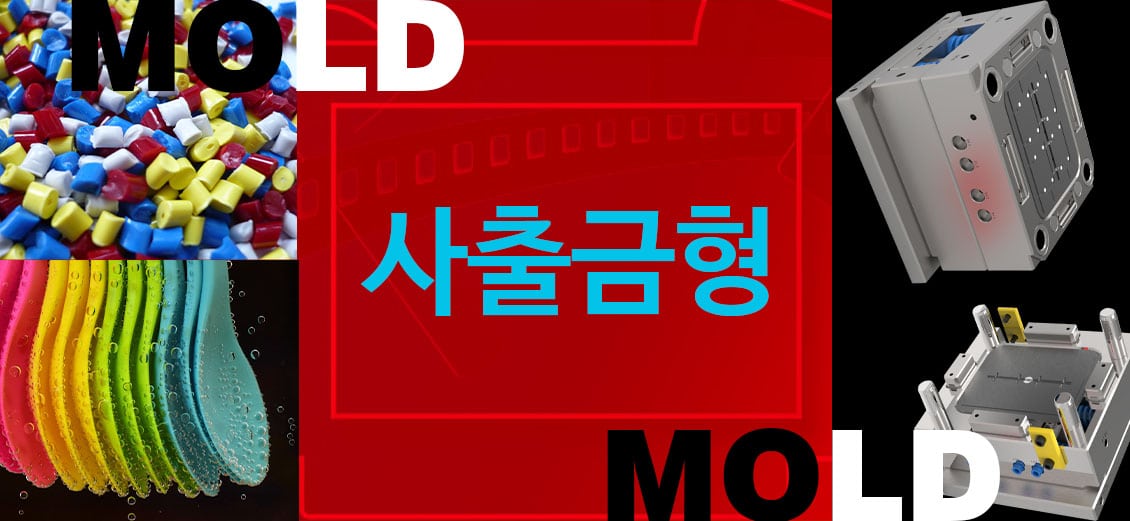
HOME → MOLD CATEGORIES →
사출 금형 11
제11장 FRP
FRP(Fiberglass Reinforced Plastic)의 개념과 성형방법에 대하여 살펴보려고 합니다.
1. FRP 개념
FRP는 불포화 폴리에스테르 수지와 유리섬유의 복합 재질로 철보다 강하고 알루미늄보다 가벼우며 내식성과 내열성 그리고 내후성이 우수한 섬유강화플라스틱임.
복합 재료로서 인공 재료라고 불리는 FRP는 여러 종류의 재료를 결합시켜 본래의 성질과는 전혀 다른 우수한 성질의 재료를 만드는 것을 목적으로 수작업에 의한 다품종 소량생산에서 기계화로 전환되어 대량생산 체계를 구축하고 있음.
80년대 경량구조재의 혁명이라고 불릴 정도로 큰 호응을 가져왔던 FRP는 향후 복합 재료 분야에서 90%이상을 차지할 정도로 전망이 밝음.
합성에 사용되는 원료와 수지는 E-유리, S-유리, 석영, 아라미드(Kevlar 49), Spectra 1000, 탄소(AS4), 탄소(IM-7), 흑연(P-100) 및 붕소, 폴리에스테르, 비닐 에스테르, 에폭시, 비스말레이미드, 폴리이미드 및 페놀이며 중합체로 이루어짐.
각각의 수지는 화학적 및 물리적 특성이 다르기 때문에 복합 구조에 다르게 기여하여 결과적으로 복합 재료의 특성도 수지에 따라 달라짐.
2. FRP 특성
(1) 단열재
상온에서 열전도율이 1.25~1.67kJ/(mhK)로 금속의 1/100~1/1,000 정도로 낮아 우수한 단열재임.
일시적인 초고온에 노출되어도 열 보호 및 내마모성에 이상적인 소재이며 2,000℃ 이상의 고속 기류를 견딜 수도 있기 때문에 우주선을 보호하기 위한 외장재로 사용됨.
(2) 높은 강도
상대 밀도는 1.5~2.0 사이로 탄소강의 1/4~1/5에 불과하지만 인장강도는 탄소강에 가깝거나 그 이상이며 비강도는 합금강과 비교할 수 있을 정도임.
☞ 비강도는 재료의 강도를 밀도로 나눈 값을 말하며 가벼우면서 튼튼한 재료는 높은 비강도를 지니고 있다고 할 수 있지만 순수 티타늄의 경우에는 높은 비강도에 비하여 강도 자체는 높지 않아서 강철에 비하여 무름.
(3) 내식성
대기, 물, 일반적인 농도의 산, 알칼리, 염, 다양한 오일 및 용제에 대한 우수한 내식성을 가지고 있고 화학적 내식성의 모든 측면에 적용되어 탄소강, 스테인리스강, 목재, 비철금속 등을 대체하고 있음.
(4) 우수한 전기적 특성
우수한 유전 특성은 고주파에 대한 내성을 가짐.
우수한 마이크로파 투과성은 레이더의 레이돔으로 널리 사용됨.
(5) 쉬운 성형
제품의 형상, 기술 요건, 용도, 수량에 따라 유연하게 성형방법을 선택할 수 있음.
공정이 간단하고 한번에 성형이 가능하며 경제적 효과가 뛰어나서 특히 형상이 복잡하고 성형이 어려운 소량의 제품에 대한 공정 우위가 부각되기도 함.
3. FRP 성형방법
(1) 매치드 다이(Matched Die Forming)
펀치와 다이로 구성된 대칭인 형에 열가소성 수지 시트를 투입한 후 가열하여 압축하는 성형법.
이미지 출처 gptcadoor.org
① 다이와 펀치의 두 부분으로 구성된 형에 열가소성 수지 시트 투입.
② 열가소성 수지 시트가 부드러워 질 때까지 열을 가함.
③ 펀치 하강.
④ 예열된 열가소성 수지 시트가 펀치의 하강으로 다이에 밀착될 때까지 압력을 가함.
⑤ 진공 펌프로 다이와 열가소성 수지 시트 사이의 공기를 배출.
⑥ 성형이 완료된 후 제품(또는 부품)이 냉각되면 취출.
(2) 핸디 레이업(Handy Lay-up)
가장 오래된 방법의 성형법 중 하나로 모든 섬유의 형태에 사용 가능하며 일반적으로 나무나 FRP 금형을 사용함.
판재 상의 보강재를 한 장씩 금형 위에 덮어 놓고 기지 재료를 함침시키면서 적층시키는 방법.
적층 된 보강재의 개수로 제품의 두께가 결정됨.
상온 경화와 가열 장치를 통하여 경화 시간을 줄이는 방법을 병용할 수 있으며 롤러로 압착할 때 섬유의 방향이 흐트러질 가능성이 있어서 대량생산에 불리함.
이미지 출처 EPP Composites Pvt Ltd.
① 탈형을 위하여 금형의 표면에 이형 갤을 분사.
② 매트 또는 패브릭 형태의 보강재를 금형 크기에 맞게 절단하여 이형 겔이 도포된 금형의 표면에 덮음.
③ 액체 형태의 열경화성 수지를 경화제와 적절한 비율로 혼합하여 금형의 표면에 덮어 놓은 매트에 붓고 브러시로 균일하게 펴 바르면서 함침시킴.
④ 또 다른 매트를 열경화성 수지가 함침된 매트 위에 덮고 그 위를 롤러로 약한 압력을 가하여 이동하면서 공기와 과잉 도포된 열경화성 수지를 배출하고 압착.
⑤ 필요한 층이 쌓일 때까지 매트와 열경화성 수지를 번갈아 쌓기를 반복.
⑥ 실온 또는 특정 온도에서 경화시킨 후 금형을 열고 성형된 제품(또는 부품)을 꺼내어 추가 가공을 시행함.
(3) 스프레이업(Spray-up)
스프레이 건에서 로빙을 분쇄하여 열경화성 수지와 함께 동시에 분사하는 방식.
보강재는 10~30mm의 짧은 섬유만 가능하고 핸드 레이업보다 수지의 사용량이 많아서 무게는 증가하고 강도는 감소함.
핸드 레이업보다 빠른 생산이 가능하지만 숙련된 작업자가 아닌 이상 두께 조절이 어려움.
이미지 출처 근영실업(주)
① 보강 섬유의 로빙을 적당한 길이로 절단한 촙 화이버를 준비함.
② 탈형을 위하여 금형의 표면에 이형 갤을 분사.
③ 표면 코팅을 위하여 수지에 맞는 겔 코트를 도포.
④ 스프레이 건으로 수지와 함께 촙 화이버를 분사한 뒤 롤러로 기포를 제거하고 압착시킴.
⑤ 사용 수지에 맞는 시간 동안 경화시킨 후 제품(또는 부품)을 꺼냄.
(4) 필라먼트 와인딩(Filament Winding)
섬유를 감아서 제작하는 방식으로 와인딩 장력, 와인딩 각도, 섬유 종류에 따른 물성을 설계할 수 있음.
와인딩 각도가 작은 것은 성형이 어려우며 필라멘트 와인딩으로 제작한 제품의 형상은 단조로움.
섬유의 종류에 따라 용도가 달라지며 탄소, 케블라 섬유는 항공기 재료로 사용되고 유리섬유는 군수품에 많이 사용됨.
이미지 출처 근영실업(주)
① 길게 이어진 섬유를 크릴에 감아 섬유 공급기에 탑재.
② 섬유 견인 롤러가 회전하면 섬유가 분리기를 지나 수지 함침기에서 수지를 함침한 후 회전판에 감김.
③ 섬유는 필요한 방향으로 최대 강도를 제공하기 위하여 미리 결정된 기하학적 패턴으로 배치됨.
④ 충분한 층이 쌓이면 수지가 함침된 섬유를 회전판에서 실온 또는 고온으로 경화시킴.
⑤ 경화가 완료되면 제품(또는 부품)을 회전판에서 벗겨냄.
4. 성형방법의 비교
구분 | 메치드 다이 | 핸디 레이업 | 스프레이업 | 필라멘트 와인딩 |
---|---|---|---|---|
적용대상 | 소형이고 성형 수량이 많을 때.
제품 치수와 품질 균일성 등이 요구될 때. |
강도가 뛰어나야 할 때.
고품질을 요구하는 제품일 때. 대형 성형품일 때. |
핸드 레이업보다 복잡한 형상을 제조할 때. | 실린더 혹은 구형의 강한 압력 용기류를 제조할 때. |
용도 | 안전모, 의자, 선박 외기의 엔진 커버 | 욕조, 물탱크, 암벽, 성벽, 인조 늪 | 보트 외판, 수영장, 큰 덮개, 탱크 용기
핸디 레이업으로 제작할 수 있는 성형품 |
파이프, 튜브, 압력 탱크 |
장점 | 제품 품질이 균일함.
대량생산이 가능. 양산성이 뛰어난 FRP 성능을 발휘할 수 있음. |
작업이 간단함.
설비비와 금형비가 저렴함. 조형이 자유롭움. 대형 제품(또는 부품)의 일체 성형이 가능. |
핸디 레이업보다는 생산능률이 좋음.
현장 시공이 가능. |
유리섬유의 강도를 충분히 이용할 수 있음.
정확한 기계 성형이 가능. 내식성이 우수한 성형품을 얻을 수 있음. |
단점 | 프리 폼이 필요함.
성형 작업 시 거의 수작업임. 작업 환경과 기계 주변이 오염될 우려가 있음. |
수작업으로 인하여 생산성이 떨어짐.
품질이 불안정함. 한쪽면만 평골함. |
핸디 레이업과 유사함. | 설비비가 많이 듦.
성형 대상이 회전체에 한함. |
이외에 FRP 성형방법에는 배큠 백 몰딩(Vacuum Bag Molding), 오토클레이브(Autoclave), 인발 성형, (Resin Transfer Moding), 레진 인퓨전(Resin Infusion), SMC(Sheet Molding Compound), BMC(Bulk Molding Compound) 등이 있으며 추후에 게재할 예정입니다.
2024년 01월 09일
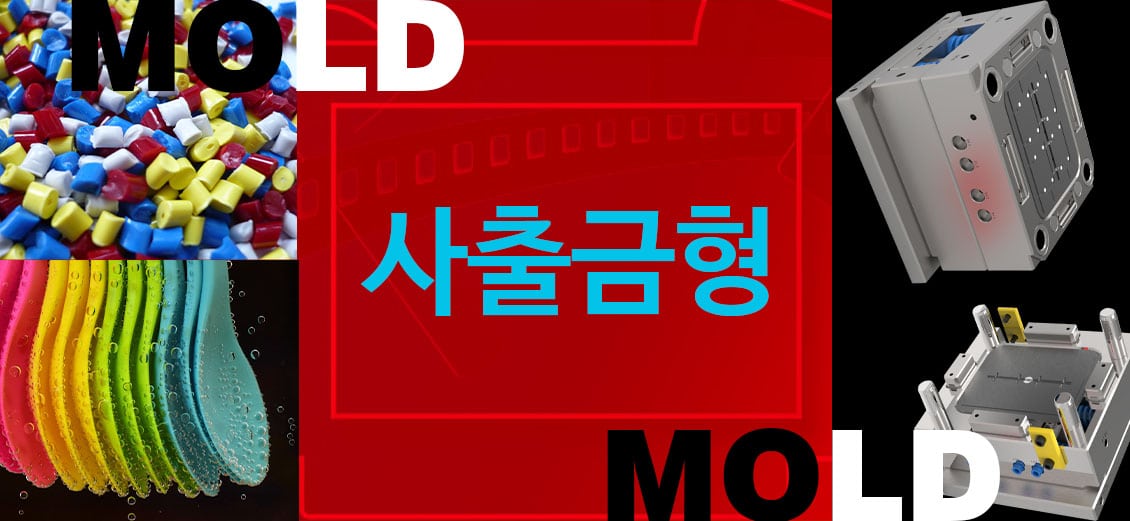
HOME → MOLD CATEGORIES →
사출 금형 11
제11장 FRP
FRP(Fiberglass Reinforced Plastic)의 개념과 성형방법에 대하여 살펴보려고 합니다.
1. FRP 개념
FRP는 불포화 폴리에스테르 수지와 유리섬유의 복합 재질로 철보다 강하고 알루미늄보다 가벼우며 내식성과 내열성 그리고 내후성이 우수한 섬유강화플라스틱임.
복합 재료로서 인공 재료라고 불리는 FRP는 여러 종류의 재료를 결합시켜 본래의 성질과는 전혀 다른 우수한 성질의 재료를 만드는 것을 목적으로 수작업에 의한 다품종 소량생산에서 기계화로 전환되어 대량생산 체계를 구축하고 있음.
80년대 경량구조재의 혁명이라고 불릴 정도로 큰 호응을 가져왔던 FRP는 향후 복합 재료 분야에서 90%이상을 차지할 정도로 전망이 밝음.
합성에 사용되는 원료와 수지는 E-유리, S-유리, 석영, 아라미드(Kevlar 49), Spectra 1000, 탄소(AS4), 탄소(IM-7), 흑연(P-100) 및 붕소, 폴리에스테르, 비닐 에스테르, 에폭시, 비스말레이미드, 폴리이미드 및 페놀이며 중합체로 이루어짐.
각각의 수지는 화학적 및 물리적 특성이 다르기 때문에 복합 구조에 다르게 기여하여 결과적으로 복합 재료의 특성도 수지에 따라 달라짐.
2. FRP 특성
(1) 단열재
상온에서 열전도율이 1.25~1.67kJ/(mhK)로 금속의 1/100~1/1,000 정도로 낮아 우수한 단열재임.
일시적인 초고온에 노출되어도 열 보호 및 내마모성에 이상적인 소재이며 2,000℃ 이상의 고속 기류를 견딜 수도 있기 때문에 우주선을 보호하기 위한 외장재로 사용됨.
(2) 높은 강도
상대 밀도는 1.5~2.0 사이로 탄소강의 1/4~1/5에 불과하지만 인장강도는 탄소강에 가깝거나 그 이상이며 비강도는 합금강과 비교할 수 있을 정도임.
☞ 비강도는 재료의 강도를 밀도로 나눈 값을 말하며 가벼우면서 튼튼한 재료는 높은 비강도를 지니고 있다고 할 수 있지만 순수 티타늄의 경우에는 높은 비강도에 비하여 강도 자체는 높지 않아서 강철에 비하여 무름.
(3) 내식성
대기, 물, 일반적인 농도의 산, 알칼리, 염, 다양한 오일 및 용제에 대한 우수한 내식성을 가지고 있고 화학적 내식성의 모든 측면에 적용되어 탄소강, 스테인리스강, 목재, 비철금속 등을 대체하고 있음.
(4) 우수한 전기적 특성
우수한 유전 특성은 고주파에 대한 내성을 가짐.
우수한 마이크로파 투과성은 레이더의 레이돔으로 널리 사용됨.
(5) 쉬운 성형
제품의 형상, 기술 요건, 용도, 수량에 따라 유연하게 성형방법을 선택할 수 있음.
공정이 간단하고 한번에 성형이 가능하며 경제적 효과가 뛰어나서 특히 형상이 복잡하고 성형이 어려운 소량의 제품에 대한 공정 우위가 부각되기도 함.
3. FRP 성형방법
(1) 매치드 다이(Matched Die Forming)
펀치와 다이로 구성된 대칭인 형에 열가소성 수지 시트를 투입한 후 가열하여 압축하는 성형법.
이미지 출처 gptcadoor.org
① 다이와 펀치의 두 부분으로 구성된 형에 열가소성 수지 시트 투입.
② 열가소성 수지 시트가 부드러워 질 때까지 열을 가함.
③ 펀치 하강.
④ 예열된 열가소성 수지 시트가 펀치의 하강으로 다이에 밀착될 때까지 압력을 가함.
⑤ 진공 펌프로 다이와 열가소성 수지 시트 사이의 공기를 배출.
⑥ 성형이 완료된 후 제품(또는 부품)이 냉각되면 취출.
(2) 핸디 레이업(Handy Lay-up)
가장 오래된 방법의 성형법 중 하나로 모든 섬유의 형태에 사용 가능하며 일반적으로 나무나 FRP 금형을 사용함.
판재 상의 보강재를 한 장씩 금형 위에 덮어 놓고 기지 재료를 함침시키면서 적층시키는 방법.
적층 된 보강재의 개수로 제품의 두께가 결정됨.
상온 경화와 가열 장치를 통하여 경화 시간을 줄이는 방법을 병용할 수 있으며 롤러로 압착할 때 섬유의 방향이 흐트러질 가능성이 있어서 대량생산에 불리함.
이미지 출처 EPP Composites Pvt Ltd.
① 탈형을 위하여 금형의 표면에 이형 갤을 분사.
② 매트 또는 패브릭 형태의 보강재를 금형 크기에 맞게 절단하여 이형 겔이 도포된 금형의 표면에 덮음.
③ 액체 형태의 열경화성 수지를 경화제와 적절한 비율로 혼합하여 금형의 표면에 덮어 놓은 매트에 붓고 브러시로 균일하게 펴 바르면서 함침시킴.
④ 또 다른 매트를 열경화성 수지가 함침된 매트 위에 덮고 그 위를 롤러로 약한 압력을 가하여 이동하면서 공기와 과잉 도포된 열경화성 수지를 배출하고 압착.
⑤ 필요한 층이 쌓일 때까지 매트와 열경화성 수지를 번갈아 쌓기를 반복.
⑥ 실온 또는 특정 온도에서 경화시킨 후 금형을 열고 성형된 제품(또는 부품)을 꺼내어 추가 가공을 시행함.
(3) 스프레이업(Spray-up)
스프레이 건에서 로빙을 분쇄하여 열경화성 수지와 함께 동시에 분사하는 방식.
보강재는 10~30mm의 짧은 섬유만 가능하고 핸드 레이업보다 수지의 사용량이 많아서 무게는 증가하고 강도는 감소함.
핸드 레이업보다 빠른 생산이 가능하지만 숙련된 작업자가 아닌 이상 두께 조절이 어려움.
이미지 출처 근영실업(주)
① 보강 섬유의 로빙을 적당한 길이로 절단한 촙 화이버를 준비함.
② 탈형을 위하여 금형의 표면에 이형 갤을 분사.
③ 표면 코팅을 위하여 수지에 맞는 겔 코트를 도포.
④ 스프레이 건으로 수지와 함께 촙 화이버를 분사한 뒤 롤러로 기포를 제거하고 압착시킴.
⑤ 사용 수지에 맞는 시간 동안 경화시킨 후 제품(또는 부품)을 꺼냄.
(4) 필라먼트 와인딩(Filament Winding)
섬유를 감아서 제작하는 방식으로 와인딩 장력, 와인딩 각도, 섬유 종류에 따른 물성을 설계할 수 있음.
와인딩 각도가 작은 것은 성형이 어려우며 필라멘트 와인딩으로 제작한 제품의 형상은 단조로움.
섬유의 종류에 따라 용도가 달라지며 탄소, 케블라 섬유는 항공기 재료로 사용되고 유리섬유는 군수품에 많이 사용됨.
이미지 출처 근영실업(주)
① 길게 이어진 섬유를 크릴에 감아 섬유 공급기에 탑재.
② 섬유 견인 롤러가 회전하면 섬유가 분리기를 지나 수지 함침기에서 수지를 함침한 후 회전판에 감김.
③ 섬유는 필요한 방향으로 최대 강도를 제공하기 위하여 미리 결정된 기하학적 패턴으로 배치됨.
④ 충분한 층이 쌓이면 수지가 함침된 섬유를 회전판에서 실온 또는 고온으로 경화시킴.
⑤ 경화가 완료되면 제품(또는 부품)을 회전판에서 벗겨냄.
4. 성형방법의 비교
구분 | 메치드 다이 | 핸디 레이업 | 스프레이업 | 필라멘트 와인딩 |
---|---|---|---|---|
적용대상 | 소형이고 성형 수량이 많을 때.
제품 치수와 품질 균일성 등이 요구될 때. |
강도가 뛰어나야 할 때.
고품질을 요구하는 제품일 때. 대형 성형품일 때. |
핸드 레이업보다 복잡한 형상을 제조할 때. | 실린더 혹은 구형의 강한 압력 용기류를 제조할 때. |
용도 | 안전모, 의자, 선박 외기의 엔진 커버 | 욕조, 물탱크, 암벽, 성벽, 인조 늪 | 보트 외판, 수영장, 큰 덮개, 탱크 용기
핸디 레이업으로 제작할 수 있는 성형품 |
파이프, 튜브, 압력 탱크 |
장점 | 제품 품질이 균일함.
대량생산이 가능. 양산성이 뛰어난 FRP 성능을 발휘할 수 있음. |
작업이 간단함.
설비비와 금형비가 저렴함. 조형이 자유롭움. 대형 제품(또는 부품)의 일체 성형이 가능. |
핸디 레이업보다는 생산능률이 좋음.
현장 시공이 가능. |
유리섬유의 강도를 충분히 이용할 수 있음.
정확한 기계 성형이 가능. 내식성이 우수한 성형품을 얻을 수 있음. |
단점 | 프리 폼이 필요함.
성형 작업 시 거의 수작업임. 작업 환경과 기계 주변이 오염될 우려가 있음. |
수작업으로 인하여 생산성이 떨어짐.
품질이 불안정함. 한쪽면만 평골함. |
핸디 레이업과 유사함. | 설비비가 많이 듦.
성형 대상이 회전체에 한함. |
이외에 FRP 성형방법에는 배큠 백 몰딩(Vacuum Bag Molding), 오토클레이브(Autoclave), 인발 성형, (Resin Transfer Moding), 레진 인퓨전(Resin Infusion), SMC(Sheet Molding Compound), BMC(Bulk Molding Compound) 등이 있으며 추후에 게재할 예정입니다.
2024년 01월 09일
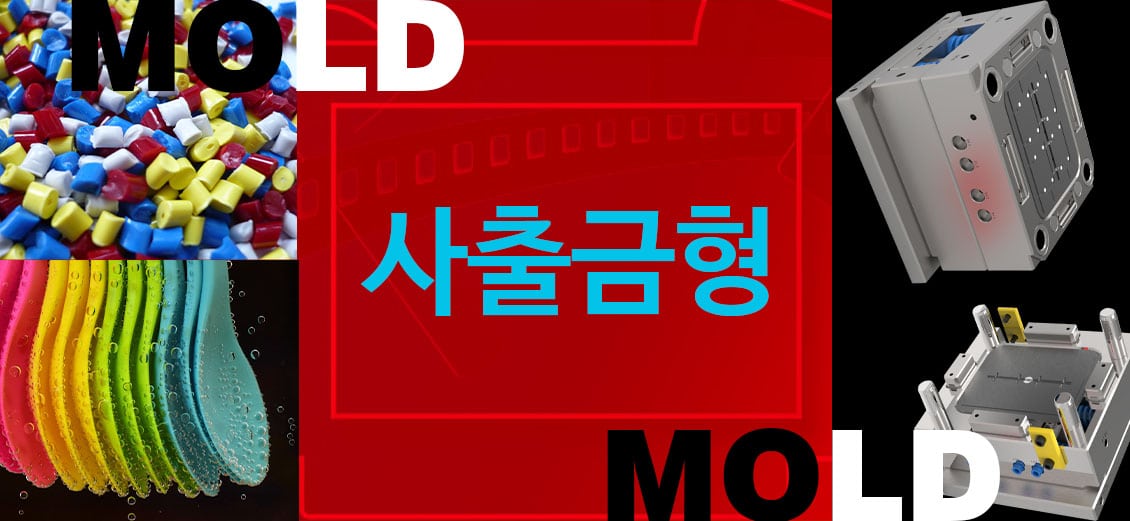
HOME → MOLD CATEGORIES →
사출 금형 11
제11장 FRP
FRP(Fiberglass Reinforced Plastic)의 개념과 성형방법에 대하여 살펴보려고 합니다.
1. FRP 개념
FRP는 불포화 폴리에스테르 수지와 유리섬유의 복합 재질로 철보다 강하고 알루미늄보다 가벼우며 내식성과 내열성 그리고 내후성이 우수한 섬유강화플라스틱임.
복합 재료로서 인공 재료라고 불리는 FRP는 여러 종류의 재료를 결합시켜 본래의 성질과는 전혀 다른 우수한 성질의 재료를 만드는 것을 목적으로 수작업에 의한 다품종 소량생산에서 기계화로 전환되어 대량생산 체계를 구축하고 있음.
80년대 경량구조재의 혁명이라고 불릴 정도로 큰 호응을 가져왔던 FRP는 향후 복합 재료 분야에서 90%이상을 차지할 정도로 전망이 밝음.
합성에 사용되는 원료와 수지는 E-유리, S-유리, 석영, 아라미드(Kevlar 49), Spectra 1000, 탄소(AS4), 탄소(IM-7), 흑연(P-100) 및 붕소, 폴리에스테르, 비닐 에스테르, 에폭시, 비스말레이미드, 폴리이미드 및 페놀이며 중합체로 이루어짐.
각각의 수지는 화학적 및 물리적 특성이 다르기 때문에 복합 구조에 다르게 기여하여 결과적으로 복합 재료의 특성도 수지에 따라 달라짐.
2. FRP 특성
(1) 단열재
상온에서 열전도율이 1.25~1.67kJ/(mhK)로 금속의 1/100~1/1,000 정도로 낮아 우수한 단열재임.
일시적인 초고온에 노출되어도 열 보호 및 내마모성에 이상적인 소재이며 2,000℃ 이상의 고속 기류를 견딜 수도 있기 때문에 우주선을 보호하기 위한 외장재로 사용됨.
(2) 높은 강도
상대 밀도는 1.5~2.0 사이로 탄소강의 1/4~1/5에 불과하지만 인장강도는 탄소강에 가깝거나 그 이상이며 비강도는 합금강과 비교할 수 있을 정도임.
☞ 비강도는 재료의 강도를 밀도로 나눈 값을 말하며 가벼우면서 튼튼한 재료는 높은 비강도를 지니고 있다고 할 수 있지만 순수 티타늄의 경우에는 높은 비강도에 비하여 강도 자체는 높지 않아서 강철에 비하여 무름.
(3) 내식성
대기, 물, 일반적인 농도의 산, 알칼리, 염, 다양한 오일 및 용제에 대한 우수한 내식성을 가지고 있고 화학적 내식성의 모든 측면에 적용되어 탄소강, 스테인리스강, 목재, 비철금속 등을 대체하고 있음.
(4) 우수한 전기적 특성
우수한 유전 특성은 고주파에 대한 내성을 가짐.
우수한 마이크로파 투과성은 레이더의 레이돔으로 널리 사용됨.
(5) 쉬운 성형
제품의 형상, 기술 요건, 용도, 수량에 따라 유연하게 성형방법을 선택할 수 있음.
공정이 간단하고 한번에 성형이 가능하며 경제적 효과가 뛰어나서 특히 형상이 복잡하고 성형이 어려운 소량의 제품에 대한 공정 우위가 부각되기도 함.
3. FRP 성형방법
(1) 매치드 다이(Matched Die Forming)
펀치와 다이로 구성된 대칭인 형에 열가소성 수지 시트를 투입한 후 가열하여 압축하는 성형법.
이미지 출처 gptcadoor.org
① 다이와 펀치의 두 부분으로 구성된 형에 열가소성 수지 시트 투입.
② 열가소성 수지 시트가 부드러워 질 때까지 열을 가함.
③ 펀치 하강.
④ 예열된 열가소성 수지 시트가 펀치의 하강으로 다이에 밀착될 때까지 압력을 가함.
⑤ 진공 펌프로 다이와 열가소성 수지 시트 사이의 공기를 배출.
⑥ 성형이 완료된 후 제품(또는 부품)이 냉각되면 취출.
(2) 핸디 레이업(Handy Lay-up)
가장 오래된 방법의 성형법 중 하나로 모든 섬유의 형태에 사용 가능하며 일반적으로 나무나 FRP 금형을 사용함.
판재 상의 보강재를 한 장씩 금형 위에 덮어 놓고 기지 재료를 함침시키면서 적층시키는 방법.
적층 된 보강재의 개수로 제품의 두께가 결정됨.
상온 경화와 가열 장치를 통하여 경화 시간을 줄이는 방법을 병용할 수 있으며 롤러로 압착할 때 섬유의 방향이 흐트러질 가능성이 있어서 대량생산에 불리함.
이미지 출처 EPP Composites Pvt Ltd.
① 탈형을 위하여 금형의 표면에 이형 갤을 분사.
② 매트 또는 패브릭 형태의 보강재를 금형 크기에 맞게 절단하여 이형 겔이 도포된 금형의 표면에 덮음.
③ 액체 형태의 열경화성 수지를 경화제와 적절한 비율로 혼합하여 금형의 표면에 덮어 놓은 매트에 붓고 브러시로 균일하게 펴 바르면서 함침시킴.
④ 또 다른 매트를 열경화성 수지가 함침된 매트 위에 덮고 그 위를 롤러로 약한 압력을 가하여 이동하면서 공기와 과잉 도포된 열경화성 수지를 배출하고 압착.
⑤ 필요한 층이 쌓일 때까지 매트와 열경화성 수지를 번갈아 쌓기를 반복.
⑥ 실온 또는 특정 온도에서 경화시킨 후 금형을 열고 성형된 제품(또는 부품)을 꺼내어 추가 가공을 시행함.
(3) 스프레이업(Spray-up)
스프레이 건에서 로빙을 분쇄하여 열경화성 수지와 함께 동시에 분사하는 방식.
보강재는 10~30mm의 짧은 섬유만 가능하고 핸드 레이업보다 수지의 사용량이 많아서 무게는 증가하고 강도는 감소함.
핸드 레이업보다 빠른 생산이 가능하지만 숙련된 작업자가 아닌 이상 두께 조절이 어려움.
이미지 출처 근영실업(주)
① 보강 섬유의 로빙을 적당한 길이로 절단한 촙 화이버를 준비함.
② 탈형을 위하여 금형의 표면에 이형 갤을 분사.
③ 표면 코팅을 위하여 수지에 맞는 겔 코트를 도포.
④ 스프레이 건으로 수지와 함께 촙 화이버를 분사한 뒤 롤러로 기포를 제거하고 압착시킴.
⑤ 사용 수지에 맞는 시간 동안 경화시킨 후 제품(또는 부품)을 꺼냄.
(4) 필라먼트 와인딩(Filament Winding)
섬유를 감아서 제작하는 방식으로 와인딩 장력, 와인딩 각도, 섬유 종류에 따른 물성을 설계할 수 있음.
와인딩 각도가 작은 것은 성형이 어려우며 필라멘트 와인딩으로 제작한 제품의 형상은 단조로움.
섬유의 종류에 따라 용도가 달라지며 탄소, 케블라 섬유는 항공기 재료로 사용되고 유리섬유는 군수품에 많이 사용됨.
이미지 출처 근영실업(주)
① 길게 이어진 섬유를 크릴에 감아 섬유 공급기에 탑재.
② 섬유 견인 롤러가 회전하면 섬유가 분리기를 지나 수지 함침기에서 수지를 함침한 후 회전판에 감김.
③ 섬유는 필요한 방향으로 최대 강도를 제공하기 위하여 미리 결정된 기하학적 패턴으로 배치됨.
④ 충분한 층이 쌓이면 수지가 함침된 섬유를 회전판에서 실온 또는 고온으로 경화시킴.
⑤ 경화가 완료되면 제품(또는 부품)을 회전판에서 벗겨냄.
4. 성형방법의 비교
구분 | 메치드 다이 | 핸디 레이업 | 스프레이업 | 필라멘트 와인딩 |
---|---|---|---|---|
적용대상 | 소형이고 성형 수량이 많을 때.
제품 치수와 품질 균일성 등이 요구될 때. |
강도가 뛰어나야 할 때.
고품질을 요구하는 제품일 때. 대형 성형품일 때. |
핸드 레이업보다 복잡한 형상을 제조할 때. | 실린더 혹은 구형의 강한 압력 용기류를 제조할 때. |
용도 | 안전모, 의자, 선박 외기의 엔진 커버 | 욕조, 물탱크, 암벽, 성벽, 인조 늪 | 보트 외판, 수영장, 큰 덮개, 탱크 용기
핸디 레이업으로 제작할 수 있는 성형품 |
파이프, 튜브, 압력 탱크 |
장점 | 제품 품질이 균일함.
대량생산이 가능. 양산성이 뛰어난 FRP 성능을 발휘할 수 있음. |
작업이 간단함.
설비비와 금형비가 저렴함. 조형이 자유롭움. 대형 제품(또는 부품)의 일체 성형이 가능. |
핸디 레이업보다는 생산능률이 좋음.
현장 시공이 가능. |
유리섬유의 강도를 충분히 이용할 수 있음.
정확한 기계 성형이 가능. 내식성이 우수한 성형품을 얻을 수 있음. |
단점 | 프리 폼이 필요함.
성형 작업 시 거의 수작업임. 작업 환경과 기계 주변이 오염될 우려가 있음. |
수작업으로 인하여 생산성이 떨어짐.
품질이 불안정함. 한쪽면만 평골함. |
핸디 레이업과 유사함. | 설비비가 많이 듦.
성형 대상이 회전체에 한함. |
이외에 FRP 성형방법에는 배큠 백 몰딩(Vacuum Bag Molding), 오토클레이브(Autoclave), 인발 성형, (Resin Transfer Moding), 레진 인퓨전(Resin Infusion), SMC(Sheet Molding Compound), BMC(Bulk Molding Compound) 등이 있으며 추후에 게재할 예정입니다.
2024년 01월 09일