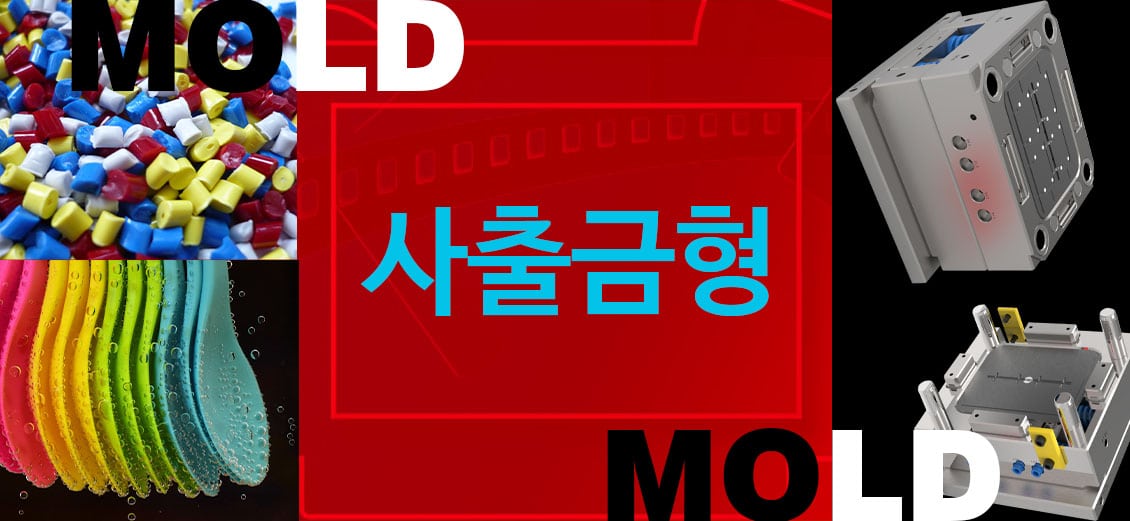
HOME → MOLD CATEGORIES →
사출 금형 7
제7장 게이트
게이트(GATE)는 충전되는 용융 재료의 흐름방향과 유량을 제어하고 성형품이 고화될 때까지 캐비티 내의 재료를 봉입하여 러너측으로 역류하는 것을 방지하며 재료에 마찰열을 발생시켜 온도를 상승시키는 역할을 하는 유동 기구입니다.
1. 게이트의 종류와 특징
(1) 비제한 게이트
1) 형상
원추 형상의 게이트로써 스프루가 그대로 게이트가 되므로 스프루 게이트 또는 다이렉트 게이트라고도 함.
비제한 게이트는 제한 게이트와는 달리 게이트가 급속하게 고화되지 않도록 단면적을 좁히지 않은 게이트를 말함.
2) 특징
성형압력의 손실이 적음.
금형 구조가 간단하고 고장이 적으며 러너가 필요 없음.
스프루의 고화시간이 길어지므로 성형 사이클 타임이 긺.
게이트를 절단하는 후가공이 필요함.
잔류응력과 충전으로 인한 변형 및 크랙이 발생하기 쉬움.
성형성이 좋아 모든 사출용 성형 재료에 적용할 수 있음.
잔류응력으로 인해 배향이 일어나기 쉬으므로 게이트 주변에 링 모양의 리브를 설치하여 보강하는 것이 좋음.
3) 설계 요점
게이트 입구의 지름은 노즐 구멍의 지름보다 0.5 ~ 1.0mm 정도 크게 할 것.
게이트의 테이퍼 각도는 2˚를 최소로 하되 고점도 플라스틱에서는 약간 굵게 저점도 플라스틱일 경우에는 약간 작게할 것.
게이트의 치수는 사용하는 성형 재료 및 성형품 중량에 따라 차이가 있지만 일반적으로 다음과 같이 사용하고 있음.
[상기 표에서 단위는 mm임.]
(2) 제한 게이트
1) 형상
비제한 게이트 이외에 모든 게이트가 해당됨.
2) 특징
게이트 부근에서 잔류응력과 변형이 감소됨.
성형품의 변형, 크랙, 뒤틀림, 굽힘 등이 감소됨.
게이트의 고화시간이 짧으므로 성형 사이클 타임을 단축시킬 수 있음.
다수 개 뽑기, 다점 게이트일 때 게이트 밸런스를 유지하기가 쉬움.
게이트 제거가 간단함.
성형 재료가 게이트를 통과할 때 압력손실이 큼.
2. 제한 게이트의 종류
(1) 표준 게이트
1) 형상
표준 게이트는 캐비티 형판(가동측 형판)에 직사각형의 홈을 파서 성형품의 측면에서 용융 재료를 주입하는 게이트로써 사이드 게이트라고도 함.
충전량을 제한하고 게이트부에서 급속히 고화시켜서 사출압력 손실을 막고자 할 때 사용함.
2) 특징
단면 형상이 간단하여 가공이 쉬움.
게이트의 치수 변경이 쉽고 정밀하게 가공할 수 있음.
충전 속도는 게이트의 고화와 관계없이 조절할 수 있음.
성형품에서 게이트를 제거하기 위해 후가공이 필요함.
거의 모든 성형 재료에 적용할 수 있음.
3) 설계 요점
게이트의 지름 또는 깊이는 성형품의 두께의 1/2 정도로 할 것.
게이트 랜드는 게이트 지름 또는 길이와 같게 할 것.
게이트 홈과 깊이의 비율은 3 : 1을 표준으로 하고 폭의 지름보다 클 때에는 팬 게이트를 사용할 것.
표준 게이트의 깊이 0.5 ~ 1.5mm, 폭 1.5 ~ 5mm, 랜드 1.5 ~ 2.5mm가 일반적이고 대형 성형품일 경우에는 게이트의 깊이 2.0 ~ 2.5mm(성형품 두께의 70 ~ 80% 수준) , 폭 7 ~ 10mm, 랜드 2.0 ~ 3.0mm 정도임.
(가) 게이트의 깊이
재료 | λ | 재료 | λ |
---|---|---|---|
PS, PE | 0.6 | PVAC, PA | 0.8 |
POM, PC, PP | 0.7 | PVC | 0.9 |
(나) 게이트의 폭
(2) 오버랩 게이트
1) 형상
오버랩 게이트는 표준 게이트와 기본적으로 동일하지만 성형품의 측면이 아닌 평면부에 설치하는 게이트임.
게이트 자국이 파팅 라인에 남게 되므로 게이트 제거 및 후가공에 유의해야 함.
두께가 두꺼운 PVC 제품에 주로 사용하는 게이트임.
2) 설계 요점
게이트 치수의 설계식은 표준 게이트와 같으며 길이는 다음과 같음.
(3) 팬 게이트
1) 형상
팬 게이트는 큰 평판의 면 및 얇은 단면에 매끄럽게 또는 균일하게 충전하는데 적합한 게이트로써 게이트 부근의 결함을 최소화 하는데 가장 효과적인 게이트임.
팬 게이트는 캐비티를 향해 게이트 끝을 부채꼴 모양으로 넓게 펼친 것으로 기포나 플로 마크의 발생이 없이 균일하게 충전할 수 있음.
팬 게이트의 위치 선정은 성형성과 후가공을 고려하여 결정해야 함.
2) 특징
게이트 부근의 결함을 최소화할 수 있음.
게이트 절단이 복잡하고 흔적이 남음.
경질 PVC를 제외한 대부분의 성형 재료에 적용할 수 있음.
3) 설계 요점
게이트 랜드(L)는 표준 게이트보다 약간 긴 6mm 전•후로 할 것.
게이트의 두께
게이트의 폭
(4) 필름 게이트
1) 형상
필름 게이트는 성형품의 폭과 게이트의 폭을 같은 길이로 하고 두께를 얇게 한 게이트로서 플래시 게이트 또는 슬릿 게이트라고도 함.
필름 게이트는 일반적으로 성형품의 폭 전체에 걸쳐서 게이트를 설치하는 경우가 많지만 성형품의 폭보다 좁게 설치해도 무방하고 게이트 절단을 고려해서 좁게 하는 것이 바람직함.
필름 게이트는 평판상의 성형품에 대한 수축 변형을 최소로 억제하려고 하는 경우에 사용함.
2) 특징
성형 재료의 주입이 쉬움.
내부응력이나 변형이 적음.
평판상의 성형품 평면도를 좋게 함.
경질 PVC 이외의 성형 재료에 적용할 수 있음.
3) 설계 요점
게이트의 설치 위치는 성형품의 폭이 좁은 곳에 할 것.
러너는 게이트 폭에 상관없이 성형품의 폭 이상으로 길게 할 수 있음.
게이트의 두께는 0.2 ~ 1.0mm, 게이트 랜드는 1mm 정도가 기준 치수임.
(5) 디스크 게이트
1) 형상
디스크 게이트는 구멍이 있는 성형품의 구멍 중앙부에 스프루를 설치하여 구멍 주위에 전면으로부터 성형 재료를 캐비티에 주입하는 앏은 원판상의 게이트이고 다이어 프레임 게이트라고도 함.
게이트 설치 시 성형품의 형상에 제약이 따르고 성형품에 웰드 라인 발생을 방지하기 위해 사용함.
게이트 설치 시 안지름이 중요할 경우에는 단면에 랩 형상으로 게이트를 설치해야 함.
2매판 사출 금형에서는 1개 뽑기 원통형에 사용되고 3매판이나 러너리스 사출 금형에서는 다수 개 뽑기도 가능함.
2) 특징
성형 재료의 주입이 쉽고 웰드 라인 발생을 방지할 수 있음.
성형품에 구멍이 두 군데 있을 경우에는 서브 러너를 설치하여 웰드 라인을 방지하고 원형 펀치나 탁상 드릴 머신으로 가공하여 성형품과 분리해야 함.
경질 PVC 이외의 모든 성형 재료에 적용할 수 있음.
3) 설계 요점
게이트의 깊이는 0.2 ~ 1.5mm, 랜드는 0.7 ~ 1.2mm가 적당함.
일반용일 경우 게이트의 깊이
정밀용일 경우 게이트의 깊이
정밀용일 경우 랜드의 길이
(6) 링 게이트
1) 형상
링 게이트는 원통형의 소형 성형품을 성형하기 위해 원통상의 외주에 러너를 링 모양으로 돌려서 원판상의 게이트로 성형 재료를 균일하게 주입하는 게이트로써 살두께가 균일한 성형품을 얻을 수 있음.
링 게이트는 러너 주입구의 반대쪽에 오버 플로를 설치하여 균형을 잡아줘야 함.
스트리퍼판이나 슬리브에 의해 성형품을 취출하므로 러너는 사다리꼴 형상을 주로 사용함.
2) 특징
성형 재료가 균일하게 주입되므로 웰드 라인의 발생이 방지됨.
코어 핀의 편심 발생이 방지됨.
3) 설계 요점
랜드의 길이는 0.7 ~ 1.2mm로 하고,
게이트의 깊이는 h = 0.7λt로 구할 것.
(7) 탭(터브) 게이트
1) 형상
오버랩 게이트를 변형시킨 것으로서 성형품의 일부에 조각 부분(TAB)을 만들어서 러너로부터 성형 재료가 직접 캐비티에 주입되지 않고 게이트를 통과하여 탭에 모인 후 충전되는 게이트임.
성형품에 직접 게이트를 붙일 수 없는 경우 또는 게이트부에 변형이 생기기 쉬운 성형 재료로 성형할 때 탭 게이트를 사용함.
탭 게이트는 전형적으로 광학 제품처럼 낮은 전단 응력이 요구되는 제품 성형에 사용됨.
2) 특징
탭에서 성형압력을 완충시켜 원활한 흐름으로 캐비티에 충전되므로 잔류응력이나 변형이 없는 성형품을 얻을 수 있음.
제팅이나 싱크 마크가 방지됨.
PVC, PC, PMMA 등과 같이 유동성이 좋지 않은 경질 플라스틱 성형에 적합함.
탭 게이트는 러너에 대해서 직각으로 탭을 붙이는 것이 일반적이고 탭은 플로 마크나 웰드 라인을 피하기 위해 살두께가 두꺼운 곳에 설치해야 함.
3) 설계 요점
탭의 폭은 6mm 이상이고 깊이는 캐비티 두께의 75%이며 탭의 길이는 러너 지금의 1.5배 정도로 할 것.
게이트의 설계는 표준 게이트의 기준을 따를 것.
탭의 크기는 폭(X) = D, 깊이(Y) = 0.9t, 길이(Z) =1.5D로 할 것.
탭의 위치는 성형품 테두리에서 150mm 이내가 좋고 성형품의 폭이 넓을 경우에는 멀티 탭 게이트를 설치하며 탭 간의 거리는 300mm 이내로 해야 함.
(8) 핀포인트 게이트
1) 형상
핀포인트 게이트는 성형품의 중앙에 게이트를 설치할 경우에 사용되는 원형의 게이트로써 다점 게이트로 사용하는 경우가 많음.
핀포인트 게이트는 단면적이 작아 유동저항이 커서 저점도 플라스틱에 사용하거나 사출압력을 높여서 사출을 시행해야 함.
[핀포인트 게이트 치수]
2)특징
게이트의 설치 위치에 제한을 받지 않고 자유롭게 결정할 수 있음.
게이트 부근에 잔류응력이 적음.
투영 면적이 크거나 변형이 발생하기 쉬운 성형품에 다점 게이트를 설치하면 수축 및 변형의 발생을 줄일 수 있음.
3매판 사출 금형에 채택하면 형개력에 의해 게이트가 자동으로 절단되고 성형품과 러너를 별도로 꺼낼 수 있음.
3매판 사출 금형, 핫러너 금형, 웰타입 노즐이 설치된 2매판 사출 금형에 적용할 수 있음.
3) 설계 요점
랜드 길이(L)는 0.8 ~ 1.2mm로 할 것.
게이트 지름(d)
단위 : mm
살두께 | 0.80 | 0.90 | 1.30 | 1.50 | 1.80 | 2.00 | 2.30 | 2.50 |
---|---|---|---|---|---|---|---|---|
C | 0.036 | 0.041 | 0.047 | 0.051 | 0.055 | 0.058 | 0.062 | 0.065 |
☞ 성형품의 살두께를 0.7 ~ 2.5mm 이내로 적용하고 웰타입 노즐에서는 30% 작게 하여야 함.
(9) 서브마린 게이트
1) 형상
서브마린 게이트는 러너를 파팅 라인에 만들고 게이트는 고정측 형판이나 가동측 형판을 터널식으로 파고 들어가 성형 재료를 캐비티 안으로 주입하는 게이트로 터널 게이트라고도 함.
서브마린 게이트는 성형품 표면에 게이트 자국을 남기고 싶지 않을 때 사용되고 성형품 측면 또는 이면에 설치할 수 있음.
형개 후 이젝터 기구에 의해 성형품이 돌출됨과 동시에 게이트가 자동으로 절단됨.
게이트 자국이 성형품 표면에 남으면 안 될 경우에는 이젝터 핀에 2차 러너를 가공하고 2차 러너에 서브마린 게이트를 설치하여 2차 러너 말단부를 성형품 내측에 붙여서 성형 재료를 간접적으로 주입되도록 할 수 있는데 이때 압력손실이 크게 발생하므로 사출압력을 크게 할 필요가 있고 이젝터 핀이 회전하지 않도록 해야 함.
2) 특징
게이트는 형개 시 자동 절단됨.
핀포인트 게이트보다 금형 구조가 간단함.
압력손실이 크고 게이트 가공이 어려움.
3) 설계 요점
파팅 라인과 게이트 입구의 경사각은 25˚~40˚로 할 것.
터널 부분의 테이퍼는 15˚~45˚로 할 것. (취출을 고려할 때 30˚~40˚가 적합)
랜드 길이 및 게이트 지름은 핀포인트 게이트와 동일하게 적용할 것.
(10) 커브드 게이트
1) 형상
커브드 게이트는 2차 러너붙이 서브마린 게이트를 변형한 것으로 서브마린 게이트의 단점인 압력손실을 막고 2차 러너를 제거한 게이트로써 코끼리 게이트, 바나나 게이트, G 게이트라 불리기도 함.
2) 특징
게이트 설치 위치 선택이 유연함.
게이트는 성형품과 별로도 분리할 수 있음.
성형품 외관에 게이트 자국이 남지 않음.
성형품 표면에 응력이 발생할 수 있음.
게이트 제작 과정이 복잡함.
적절한 설계가 수반되지 않으면 형개 시 게이트가 파손될 수 있음.
3) 설계 요점
게이트 지름(d)은 Φ0.8 ~ Φ1.2mm, 게이트 길이(L)는 1.0 ~ 1.2mm로 할 것.
커브드부는 게이트부의 끝단 지름 Φ2.5mm에서 러너부의 시작단 지름 0.8D로 점진적으로 크게 제작할 것.
3. 러너리스 시스템
(1) 개요
사출 금형에서 스프루와 러너는 용융된 재료를 캐비티 내부로 안내하는 유동 기구로써 스프루와 러너는 성형품을 얻기 위한 보조물일 뿐 매사이클마다 성형품과 동시에 성형되어 취출됨.
취출 시에 성형품과 분리하고 마무리를 해야 하기 때문에 스크랩이 발생하게 되는데 러너리스 시스템은 이러한 스프루와 러너가 생성되지 않도록 하는 금형을 의미함.
러너리스 금형은 이와 같은 의미로서 러너가 없는 상태로 제품만 취출되는 구조의 금형을 말하며, 사출성형기의 노즐을 이용하여 용융 재료를 직접 캐비티에 충전하는 것을 말함.
(2) 성형방법
사출성형기의 노즐로부터 직접 캐비티에 사출하는 방법.
플라스틱의 단열성을 이용하여 스프루-러너 중심부의 성형 재료를 용융 상태로 유지하는 방법.
러너에 열을 가하여 성형 재료를 용융 상태로 유지하는 방법.
(3) 특징
① 성형품의 품질 우수
대형 성형품을 성형 시 비제한 게이트에서는 게이트 주변에 잔류응력으로 인해 발생한 변형이 성형품의 물성에 큰 영향을 주는데 이를 개선하기 위해 다점 핀포인트 게이트와 3매판 사출 금형을 채택하지만 금형의 크기가 대형이다 보니 유지•보수가 힘들어서 러너리스 금형으로 대체하고 있음.
② 재료비 절감
러너리스 성형은 스프루-러너가 배출되지 않기 때문에 재료의 손실이 발생하지 않음.
③ 성형 사이클 타임 단축
러너리스 성형은 스프루-러너의 냉각 시간이 필요 없으므로 고속 성형을 할 수 있고 사출성형기의 불필요한 다이 플레이트 운동을 수행하지 않기 때문에 생산시간이 단축됨.
④ 사양이 한 단계 낮은 사출성형기 사용 가능
스프루-러너와 관계되는 사출용량, 형체력, 3매판 사출 금형 채택 시 형개 스트로크 등이 기준치보다 작은 사출성형기를 선택해도 무방함.
⑤ 금형의 설계 및 보수에 고도의 기술 요구
⑥ 성형품의 형상 및 사용 재료의 한정
러너리스 성형에서 사용할 재료는 열안정성이 좋고 저온에서도 성형이 용이해야 함.
또한 열전도율이 높고 냉각시간이 빨라야 하며 저압에서도 성형이 용이해야 함.
(4) 러너리스 성형품의 형상과 사용 재료
1) 성형품의 형상
냉각에 소요되는 시간이 적은 성형 사이클 타임이 빠른 형상일 것.
냉각 및 단열이 어려운 게이트 부근에 요철이 있는 형상은 피할 것.
2) 사용 재료
① 열안정성이 좋을 것
저온에서 유동성이 좋은 성형 재료는 온도조절이 쉽고 게이트의 고화를 막을 수 있음.
② 유동성이 좋을 것
러너리스 성형은 게이트 부근의 단면적이 작고 저항이 커서 저압•저온에서도 유동성이 좋아아야 함.
③ 열변형 온도가 높을 것
열변형 온도가 높으면 성형품의 온도가 다소 높아도 이형이 가능하므로 성형 사이클 타임을 단축시키고 게이트의 고화를 막을 수 있음.
④ 열전도율이 높을 것
열전도율이 높으면 성형 재료에 내재되어 있는 열을 쉽게 냉각시킬 수 있어 성형 사이클 타임을 단축할 수 있음.
⑤ 비열이 낮을 것
비열이 낮으면 적은 효율로도 온도 조절이 쉬워짐.
4. 러너리스 시스템의 종류
(1) 웰타입 노즐 방식
1) 구조
웰타입 노즐 방식은 용융 재료가 잠기도록 되어 있는 공간(WELL)이 있어 외부는 냉각 고화되어 단열벽을 이루고 중심부는 항상 용융 상태가 되어 있음.
노즐에 사출압력이 작용하면 즉시 캐비티 내로 성형 재료가 충전이 됨.
2) 특징
1개 캐비티 금형에 적합함.
금형 구조가 간단하고 조작이 쉬움.
치수 정밀도가 높은 성형 재료에는 사용할 수 없음.
성형온도 범위가 좁은 성형 재료에는 사용할 수 없음.
(2) 익스텐션 노즐 방식
1) 구조
익스텐션 노즐 방식은 캐비티부터 사출성형기의 노즐을 연장하여 근접시킨 긴 노즐로써 노즐에서의 압력손실이 적음.
익스텐션 노즐 방식은 노즐 끝부분에 용융 재료가 고화되지 않도록 밴드히터를 설치하고 성형품에 스프루-러너가 남지 않음.
2) 특징
1개 캐비티 금형에 적합함.
용융 재료의 온도조절이 쉬움.
노즐의 열이 금형에 전해지기 쉬움,
(3) 인슐레이티드 러너 방식
1) 구조
인슐레이티드 러너 방식은 러너 지름을 20 ~ 25mm 정도로 크게 해서 외부는 고화된 단열층이 되고 중심부는 용융 상태가 되어 캐비티 내에 성형 재료를 쉽게 주입하도록 한 방식으로 밴드히터 등을 설치하여 게이트부의 냉각을 방지해야 함.
2) 특징
3매판 사출 금형을 러너리스 금형으로 만들 수 있음.
게이트는 뽑기 쉬운 역테이퍼로 함.
러너부가 냉각되지 않도록 성형 사이클 타임을 빠르게 진행해야 함.
온도조절과 재료교환 등이 번거로움.
(4) 핫러너 방식
1) 구조
핫러너 방식은 게이트부에 가열 장치를 부착하여 용융 재료를 항상 캐비티 내에 주입할 수 있도록 다기관 방식으로 러너를 가열 실린더 일부분으로 취급하는 방식.
2) 특징
다점 게이트를 채택할 수 있음.
러너의 압력손실이 적음.
금형 두께가 커지고 구조가 복잡함.
게이트가 저온 캐비티와 밀착되어 있어 금형온도 조절이 까다로움.
5. 핫러너의 금형설계 시 고려 사항
(1) 매니폴드 블록
1) 가열 방식
(가) 외부 가열 방식
외부 가열 방식은 러너 채널에 평행하게 가공한 구멍에 카트리지 히터를 삽입하거나 매니폴더 외부에 히터를 부착하는 방식.
(나) 내부 가열 방식
내부 가열방식은 카트리지 히터를 러너 채널 중에 설치하여 러너 내부에서 성형 재료를 가열하는 방식임.
러너의 벽에 접촉하는 성형 재료는 냉각•고화하여 단열재의 역할을 하고 히터의 열손실을 최소화하기 때문에 외부 가열 방식에 비해 히터의 용량이 작아도 됨.
2) 매니폴드 중량
매니폴드의 중량이 작을수록 가열에 따른 소요전력이 적어지므로 강도상 허용되는 한 매니폴드의 중량을 감소시키는 것이 필요함.
3) 단열 및 열팽창
(가) 단열 대책
사출성형기의 다이 플레이트와 금형 설치판 사이의 단열에는 일반적으로 6 ~ 10mm의 석면판이 설치됨.
또한 설치판과 매니폴드, 매니폴드와 형판 사이에는 3 ~ 8mm의 에어 갭을 두어 단열하는 경우가 많음.
매니폴드와 형판은 접촉면적을 가능한 한 작게하고 재질도 18-8스테인리스강과 같이 열전도성이 낮은 것이 좋음.
(나) 열팽창 대책
열팽창에 의해 발생되는 문제는 게이트의 중심과 매니폴드 블록 중심과의 어긋남 때문임.
이에 대한 대책은 금형 구조에 따라 차이가 있으나 매니폴드 블록과 형판과의 열팽창 차이만큼 노즐의 중심거리를 짧게 하면 됨.
열팽창 대책이 불충분하면 중심이 어긋나서 성형 재료가 누출되거나 노즐에 만곡 변형이 발생됨.
(2) 노즐
1) 노즐 가열 방식
(가) 무가열 방식(완전 단열 방식)
히터에 의해 노즐을 가열하는 것이 아니고 매니폴드 블록의 열에 의해 노즐 내의 성형 재료를 용융 상태로 유지하는 방식이고 노즐의 재질은 베릴륨동(Be-Cu)이 사용됨.
(나) 내부 가열 방식
노즐 내에 카트리지 히터를 삽입하여 가열하는 방식으로 히터 주위에 성형 재료가 흐르므로 열효율이 좋고 노즐 선단부까지 가열되므로 온도조절이 우수하며 게이트의 고화를 방지할 수 있음.
(다) 외부 가열방식
노즐의 외부에 밴드히터를 장착하여 가열하는 방식으로 성형 재료의 국부적인 가열은 없으나 히터의 크기에 제약이 있음.
2) 노즐 단열방식
(가) 세미 인슐레이티드 노즐
게이트부에서 노즐과 스프루 부시가 접촉되지 않도록 노즐 선단부 위에 틈새가 있고 이곳에 성형 재료가 유입되어서 단열 작용을 하고 베릴륨동을 사용함.
(나) 완전 인슐레이티드 노즐
게이트는 0.4 ~ 0.6mm 정도로 작게 하고 게이트 랜드의 길이를 짧게 하여 스프루 부시의 살두께를 두껍게 한 것으로 강철재의 트러스팅 스페이서가 노즐 밑부분에 장착되어 노즐이 완전히 성형 재료의 중앙에 떠 있는 상태가 되고 이로 인해 스프루 부시와의 접촉에 의한 냉각을 막을 수 있음.
(다) 내부 접촉 가열 노즐
노즐의 내부에 카트리지 히터를 넣어서 특히 선단부의 내부를 가열할 수 있도록 한 것으로 온도조절기가 장착되어 있어 조절이 자유롭고 노즐 내부를 가열하므로 노즐 선단이 스프루 부시와 접촉되는 것이 허용되며 노즐 길이를 짧게 할 수 있음.
(3) 러너리스
1) 개요
핫러너 방식은 러너리스 시스템에서 가장 성형성이 좋고 형상이나 사용 성형 재료의 제한이 적은 방식임.
2) 핫러너 가열 시스템의 종류
(가) INCOE 시스템
INCOE 시스템은 유선형을 갖는 토피도 속에 카트리지 히터를 내장한 것으로 직접 금형에 조립하여 사용함.
용융된 재료가 가열된 토피도의 주위를 통해 게이트로부터 금형의 캐비티에 주입됨.
(나) DU POINT 시스템
DU POINT 시스템은 POM, PA 등과 같은 엔지니어링 플라스틱의 사출을 위해 개발된 것으로 러너는 카트리지 히터에 의해 가열되고 폐쇄 프로브는 스프링의 탄성에 의해 닫혀 있다가 러너 내의 압력이 높아지면 프로브가 뒤로 밀리면서 게이트가 열리는 구조임.
3) 핫러너 선정 시 고려사항
매니폴드 각부의 조합부에서 성형 재료의 누출이 없을 것.
게이트가 막히지 않을 것.
게이트 밸런스를 확실히 유지할 것.
시스템 전체에 걸쳐 온도가 균일할 것.
매니폴드 블록의 온도 상승 시간이 빠를 것.
(4) 밸브 게이트
1) 개요
밸브 게이트는 성형 재료가 처음부터 압축되어 있으므로 밸브가 열렸을 때 용융된 재료의 팽창이 매우 빠르고 고속 사출이 가능하며 충전까지의 용융 재료의 온도 저하가 적어 핫러너 금형에 많이 사용됨.
밸브 게이트는 니들이 가이드 부시 내를 슬라이딩하면서 성형 재료를 유출함.
2) 특징
성형 재료의 온도가 낮아도 좋으므로 성형 재료의 열화가 감소되고 성형 사이클 타임이 단축됨.
응력과 변형이 작아 성형품의 불량이 감소됨.
성형 재료의 누출이 방지되므로 핀포인트 게이트를 적용할 수 있음.
게이트 밸런스가 유지됨.
3) 종류
(가) 오픈형
오픈형은 가장 간단한 구조로서 조작이 쉬우나 게이트 랜드가 남기 쉽고 성형 재료의 누출의 우려가 있음.
(나) 고정 니들형
고정 니들형은 게이트의 폐색을 막기 위해 중앙에 히터가 설치된 니들을 삽입하고 그 선단을 게이트 입구까지 길게 한 것임.
(다) 가동 니들형
가동 니들형은 보압 완료 후 니들을 밀어내서 게이트를 완전히 밀폐하는 방식으로 게이트에서 성형 재료의 누출이 없고 게이트의 흔적이 없음.
니들의 구동은 스프링, 공압, 유압이 사용됨.
이상으로 게이트에 대한 연재를 마치고 다음에는 또 다른 유동기구인 러너와 냉각회로에 대한 연재를 시작할 예정입니다.
2020년 07월 29일
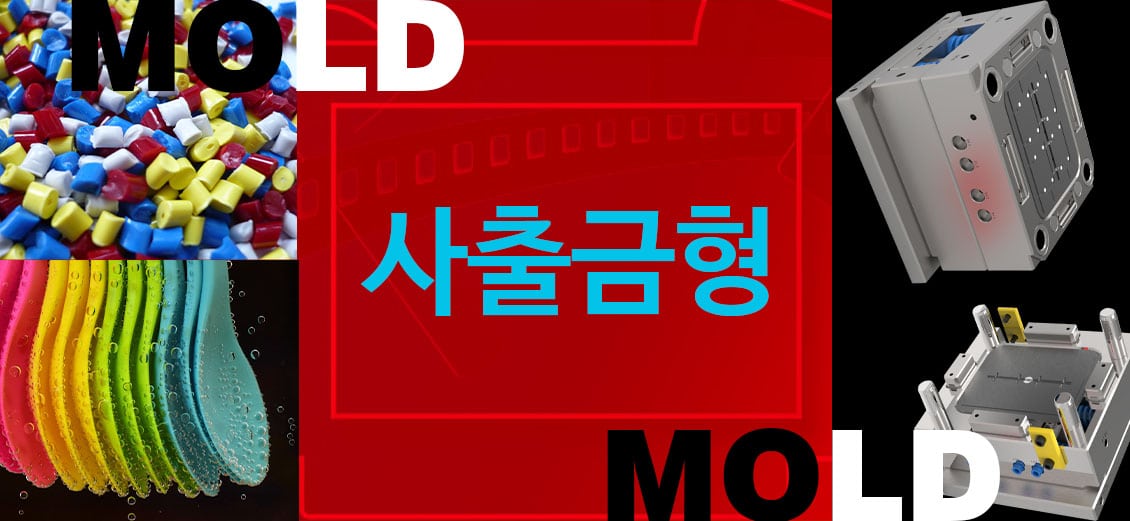
HOME → MOLD CATEGORIES →
사출 금형 7
제7장 게이트
게이트(GATE)는 충전되는 용융 재료의 흐름방향과 유량을 제어하고 성형품이 고화될 때까지 캐비티 내의 재료를 봉입하여 러너측으로 역류하는 것을 방지하며 재료에 마찰열을 발생시켜 온도를 상승시키는 역할을 하는 유동 기구입니다.
1. 게이트의 종류와 특징
(1) 비제한 게이트
1) 형상
원추 형상의 게이트로써 스프루가 그대로 게이트가 되므로 스프루 게이트 또는 다이렉트 게이트라고도 함.
비제한 게이트는 제한 게이트와는 달리 게이트가 급속하게 고화되지 않도록 단면적을 좁히지 않은 게이트를 말함.
2) 특징
성형압력의 손실이 적음.
금형 구조가 간단하고 고장이 적으며 러너가 필요 없음.
스프루의 고화시간이 길어지므로 성형 사이클 타임이 긺.
게이트를 절단하는 후가공이 필요함.
잔류응력과 충전으로 인한 변형 및 크랙이 발생하기 쉬움.
성형성이 좋아 모든 사출용 성형 재료에 적용할 수 있음.
잔류응력으로 인해 배향이 일어나기 쉬으므로 게이트 주변에 링 모양의 리브를 설치하여 보강하는 것이 좋음.
3) 설계 요점
게이트 입구의 지름은 노즐 구멍의 지름보다 0.5 ~ 1.0mm 정도 크게 할 것.
게이트의 테이퍼 각도는 2˚를 최소로 하되 고점도 플라스틱에서는 약간 굵게 저점도 플라스틱일 경우에는 약간 작게할 것.
게이트의 치수는 사용하는 성형 재료 및 성형품 중량에 따라 차이가 있지만 일반적으로 다음과 같이 사용하고 있음.
[상기 표에서 단위는 mm임.]
(2) 제한 게이트
1) 형상
비제한 게이트 이외에 모든 게이트가 해당됨.
2) 특징
게이트 부근에서 잔류응력과 변형이 감소됨.
성형품의 변형, 크랙, 뒤틀림, 굽힘 등이 감소됨.
게이트의 고화시간이 짧으므로 성형 사이클 타임을 단축시킬 수 있음.
다수 개 뽑기, 다점 게이트일 때 게이트 밸런스를 유지하기가 쉬움.
게이트 제거가 간단함.
성형 재료가 게이트를 통과할 때 압력손실이 큼.
2. 제한 게이트의 종류
(1) 표준 게이트
1) 형상
표준 게이트는 캐비티 형판(가동측 형판)에 직사각형의 홈을 파서 성형품의 측면에서 용융 재료를 주입하는 게이트로써 사이드 게이트라고도 함.
충전량을 제한하고 게이트부에서 급속히 고화시켜서 사출압력 손실을 막고자 할 때 사용함.
2) 특징
단면 형상이 간단하여 가공이 쉬움.
게이트의 치수 변경이 쉽고 정밀하게 가공할 수 있음.
충전 속도는 게이트의 고화와 관계없이 조절할 수 있음.
성형품에서 게이트를 제거하기 위해 후가공이 필요함.
거의 모든 성형 재료에 적용할 수 있음.
3) 설계 요점
게이트의 지름 또는 깊이는 성형품의 두께의 1/2 정도로 할 것.
게이트 랜드는 게이트 지름 또는 길이와 같게 할 것.
게이트 홈과 깊이의 비율은 3 : 1을 표준으로 하고 폭의 지름보다 클 때에는 팬 게이트를 사용할 것.
표준 게이트의 깊이 0.5 ~ 1.5mm, 폭 1.5 ~ 5mm, 랜드 1.5 ~ 2.5mm가 일반적이고 대형 성형품일 경우에는 게이트의 깊이 2.0 ~ 2.5mm(성형품 두께의 70 ~ 80% 수준) , 폭 7 ~ 10mm, 랜드 2.0 ~ 3.0mm 정도임.
(가) 게이트의 깊이
재료 | λ | 재료 | λ |
---|---|---|---|
PS, PE | 0.6 | PVAC, PA | 0.8 |
POM, PC, PP | 0.7 | PVC | 0.9 |
(나) 게이트의 폭
(2) 오버랩 게이트
1) 형상
오버랩 게이트는 표준 게이트와 기본적으로 동일하지만 성형품의 측면이 아닌 평면부에 설치하는 게이트임.
게이트 자국이 파팅 라인에 남게 되므로 게이트 제거 및 후가공에 유의해야 함.
두께가 두꺼운 PVC 제품에 주로 사용하는 게이트임.
2) 설계 요점
게이트 치수의 설계식은 표준 게이트와 같으며 길이는 다음과 같음.
(3) 팬 게이트
1) 형상
팬 게이트는 큰 평판의 면 및 얇은 단면에 매끄럽게 또는 균일하게 충전하는데 적합한 게이트로써 게이트 부근의 결함을 최소화 하는데 가장 효과적인 게이트임.
팬 게이트는 캐비티를 향해 게이트 끝을 부채꼴 모양으로 넓게 펼친 것으로 기포나 플로 마크의 발생이 없이 균일하게 충전할 수 있음.
팬 게이트의 위치 선정은 성형성과 후가공을 고려하여 결정해야 함.
2) 특징
게이트 부근의 결함을 최소화할 수 있음.
게이트 절단이 복잡하고 흔적이 남음.
경질 PVC를 제외한 대부분의 성형 재료에 적용할 수 있음.
3) 설계 요점
게이트 랜드(L)는 표준 게이트보다 약간 긴 6mm 전•후로 할 것.
게이트의 두께
게이트의 폭
(4) 필름 게이트
1) 형상
필름 게이트는 성형품의 폭과 게이트의 폭을 같은 길이로 하고 두께를 얇게 한 게이트로서 플래시 게이트 또는 슬릿 게이트라고도 함.
필름 게이트는 일반적으로 성형품의 폭 전체에 걸쳐서 게이트를 설치하는 경우가 많지만 성형품의 폭보다 좁게 설치해도 무방하고 게이트 절단을 고려해서 좁게 하는 것이 바람직함.
필름 게이트는 평판상의 성형품에 대한 수축 변형을 최소로 억제하려고 하는 경우에 사용함.
2) 특징
성형 재료의 주입이 쉬움.
내부응력이나 변형이 적음.
평판상의 성형품 평면도를 좋게 함.
경질 PVC 이외의 성형 재료에 적용할 수 있음.
3) 설계 요점
게이트의 설치 위치는 성형품의 폭이 좁은 곳에 할 것.
러너는 게이트 폭에 상관없이 성형품의 폭 이상으로 길게 할 수 있음.
게이트의 두께는 0.2 ~ 1.0mm, 게이트 랜드는 1mm 정도가 기준 치수임.
(5) 디스크 게이트
1) 형상
디스크 게이트는 구멍이 있는 성형품의 구멍 중앙부에 스프루를 설치하여 구멍 주위에 전면으로부터 성형 재료를 캐비티에 주입하는 앏은 원판상의 게이트이고 다이어 프레임 게이트라고도 함.
게이트 설치 시 성형품의 형상에 제약이 따르고 성형품에 웰드 라인 발생을 방지하기 위해 사용함.
게이트 설치 시 안지름이 중요할 경우에는 단면에 랩 형상으로 게이트를 설치해야 함.
2매판 사출 금형에서는 1개 뽑기 원통형에 사용되고 3매판이나 러너리스 사출 금형에서는 다수 개 뽑기도 가능함.
2) 특징
성형 재료의 주입이 쉽고 웰드 라인 발생을 방지할 수 있음.
성형품에 구멍이 두 군데 있을 경우에는 서브 러너를 설치하여 웰드 라인을 방지하고 원형 펀치나 탁상 드릴 머신으로 가공하여 성형품과 분리해야 함.
경질 PVC 이외의 모든 성형 재료에 적용할 수 있음.
3) 설계 요점
게이트의 깊이는 0.2 ~ 1.5mm, 랜드는 0.7 ~ 1.2mm가 적당함.
일반용일 경우 게이트의 깊이
정밀용일 경우 게이트의 깊이
정밀용일 경우 랜드의 길이
(6) 링 게이트
1) 형상
링 게이트는 원통형의 소형 성형품을 성형하기 위해 원통상의 외주에 러너를 링 모양으로 돌려서 원판상의 게이트로 성형 재료를 균일하게 주입하는 게이트로써 살두께가 균일한 성형품을 얻을 수 있음.
링 게이트는 러너 주입구의 반대쪽에 오버 플로를 설치하여 균형을 잡아줘야 함.
스트리퍼판이나 슬리브에 의해 성형품을 취출하므로 러너는 사다리꼴 형상을 주로 사용함.
2) 특징
성형 재료가 균일하게 주입되므로 웰드 라인의 발생이 방지됨.
코어 핀의 편심 발생이 방지됨.
3) 설계 요점
랜드의 길이는 0.7 ~ 1.2mm로 하고,
게이트의 깊이는 h = 0.7λt로 구할 것.
(7) 탭(터브) 게이트
1) 형상
오버랩 게이트를 변형시킨 것으로서 성형품의 일부에 조각 부분(TAB)을 만들어서 러너로부터 성형 재료가 직접 캐비티에 주입되지 않고 게이트를 통과하여 탭에 모인 후 충전되는 게이트임.
성형품에 직접 게이트를 붙일 수 없는 경우 또는 게이트부에 변형이 생기기 쉬운 성형 재료로 성형할 때 탭 게이트를 사용함.
탭 게이트는 전형적으로 광학 제품처럼 낮은 전단 응력이 요구되는 제품 성형에 사용됨.
2) 특징
탭에서 성형압력을 완충시켜 원활한 흐름으로 캐비티에 충전되므로 잔류응력이나 변형이 없는 성형품을 얻을 수 있음.
제팅이나 싱크 마크가 방지됨.
PVC, PC, PMMA 등과 같이 유동성이 좋지 않은 경질 플라스틱 성형에 적합함.
탭 게이트는 러너에 대해서 직각으로 탭을 붙이는 것이 일반적이고 탭은 플로 마크나 웰드 라인을 피하기 위해 살두께가 두꺼운 곳에 설치해야 함.
3) 설계 요점
탭의 폭은 6mm 이상이고 깊이는 캐비티 두께의 75%이며 탭의 길이는 러너 지금의 1.5배 정도로 할 것.
게이트의 설계는 표준 게이트의 기준을 따를 것.
탭의 크기는 폭(X) = D, 깊이(Y) = 0.9t, 길이(Z) =1.5D로 할 것.
탭의 위치는 성형품 테두리에서 150mm 이내가 좋고 성형품의 폭이 넓을 경우에는 멀티 탭 게이트를 설치하며 탭 간의 거리는 300mm 이내로 해야 함.
(8) 핀포인트 게이트
1) 형상
핀포인트 게이트는 성형품의 중앙에 게이트를 설치할 경우에 사용되는 원형의 게이트로써 다점 게이트로 사용하는 경우가 많음.
핀포인트 게이트는 단면적이 작아 유동저항이 커서 저점도 플라스틱에 사용하거나 사출압력을 높여서 사출을 시행해야 함.
[핀포인트 게이트 치수]
2)특징
게이트의 설치 위치에 제한을 받지 않고 자유롭게 결정할 수 있음.
게이트 부근에 잔류응력이 적음.
투영 면적이 크거나 변형이 발생하기 쉬운 성형품에 다점 게이트를 설치하면 수축 및 변형의 발생을 줄일 수 있음.
3매판 사출 금형에 채택하면 형개력에 의해 게이트가 자동으로 절단되고 성형품과 러너를 별도로 꺼낼 수 있음.
3매판 사출 금형, 핫러너 금형, 웰타입 노즐이 설치된 2매판 사출 금형에 적용할 수 있음.
3) 설계 요점
랜드 길이(L)는 0.8 ~ 1.2mm로 할 것.
게이트 지름(d)
단위 : mm
살두께 | 0.80 | 0.90 | 1.30 | 1.50 | 1.80 | 2.00 | 2.30 | 2.50 |
---|---|---|---|---|---|---|---|---|
C | 0.036 | 0.041 | 0.047 | 0.051 | 0.055 | 0.058 | 0.062 | 0.065 |
☞ 성형품의 살두께를 0.7 ~ 2.5mm 이내로 적용하고 웰타입 노즐에서는 30% 작게 하여야 함.
(9) 서브마린 게이트
1) 형상
서브마린 게이트는 러너를 파팅 라인에 만들고 게이트는 고정측 형판이나 가동측 형판을 터널식으로 파고 들어가 성형 재료를 캐비티 안으로 주입하는 게이트로 터널 게이트라고도 함.
서브마린 게이트는 성형품 표면에 게이트 자국을 남기고 싶지 않을 때 사용되고 성형품 측면 또는 이면에 설치할 수 있음.
형개 후 이젝터 기구에 의해 성형품이 돌출됨과 동시에 게이트가 자동으로 절단됨.
게이트 자국이 성형품 표면에 남으면 안 될 경우에는 이젝터 핀에 2차 러너를 가공하고 2차 러너에 서브마린 게이트를 설치하여 2차 러너 말단부를 성형품 내측에 붙여서 성형 재료를 간접적으로 주입되도록 할 수 있는데 이때 압력손실이 크게 발생하므로 사출압력을 크게 할 필요가 있고 이젝터 핀이 회전하지 않도록 해야 함.
2) 특징
게이트는 형개 시 자동 절단됨.
핀포인트 게이트보다 금형 구조가 간단함.
압력손실이 크고 게이트 가공이 어려움.
3) 설계 요점
파팅 라인과 게이트 입구의 경사각은 25˚~40˚로 할 것.
터널 부분의 테이퍼는 15˚~45˚로 할 것. (취출을 고려할 때 30˚~40˚가 적합)
랜드 길이 및 게이트 지름은 핀포인트 게이트와 동일하게 적용할 것.
(10) 커브드 게이트
1) 형상
커브드 게이트는 2차 러너붙이 서브마린 게이트를 변형한 것으로 서브마린 게이트의 단점인 압력손실을 막고 2차 러너를 제거한 게이트로써 코끼리 게이트, 바나나 게이트, G 게이트라 불리기도 함.
2) 특징
게이트 설치 위치 선택이 유연함.
게이트는 성형품과 별로도 분리할 수 있음.
성형품 외관에 게이트 자국이 남지 않음.
성형품 표면에 응력이 발생할 수 있음.
게이트 제작 과정이 복잡함.
적절한 설계가 수반되지 않으면 형개 시 게이트가 파손될 수 있음.
3) 설계 요점
게이트 지름(d)은 Φ0.8 ~ Φ1.2mm, 게이트 길이(L)는 1.0 ~ 1.2mm로 할 것.
커브드부는 게이트부의 끝단 지름 Φ2.5mm에서 러너부의 시작단 지름 0.8D로 점진적으로 크게 제작할 것.
3. 러너리스 시스템
(1) 개요
사출 금형에서 스프루와 러너는 용융된 재료를 캐비티 내부로 안내하는 유동 기구로써 스프루와 러너는 성형품을 얻기 위한 보조물일 뿐 매사이클마다 성형품과 동시에 성형되어 취출됨.
취출 시에 성형품과 분리하고 마무리를 해야 하기 때문에 스크랩이 발생하게 되는데 러너리스 시스템은 이러한 스프루와 러너가 생성되지 않도록 하는 금형을 의미함.
러너리스 금형은 이와 같은 의미로서 러너가 없는 상태로 제품만 취출되는 구조의 금형을 말하며, 사출성형기의 노즐을 이용하여 용융 재료를 직접 캐비티에 충전하는 것을 말함.
(2) 성형방법
사출성형기의 노즐로부터 직접 캐비티에 사출하는 방법.
플라스틱의 단열성을 이용하여 스프루-러너 중심부의 성형 재료를 용융 상태로 유지하는 방법.
러너에 열을 가하여 성형 재료를 용융 상태로 유지하는 방법.
(3) 특징
① 성형품의 품질 우수
대형 성형품을 성형 시 비제한 게이트에서는 게이트 주변에 잔류응력으로 인해 발생한 변형이 성형품의 물성에 큰 영향을 주는데 이를 개선하기 위해 다점 핀포인트 게이트와 3매판 사출 금형을 채택하지만 금형의 크기가 대형이다 보니 유지•보수가 힘들어서 러너리스 금형으로 대체하고 있음.
② 재료비 절감
러너리스 성형은 스프루-러너가 배출되지 않기 때문에 재료의 손실이 발생하지 않음.
③ 성형 사이클 타임 단축
러너리스 성형은 스프루-러너의 냉각 시간이 필요 없으므로 고속 성형을 할 수 있고 사출성형기의 불필요한 다이 플레이트 운동을 수행하지 않기 때문에 생산시간이 단축됨.
④ 사양이 한 단계 낮은 사출성형기 사용 가능
스프루-러너와 관계되는 사출용량, 형체력, 3매판 사출 금형 채택 시 형개 스트로크 등이 기준치보다 작은 사출성형기를 선택해도 무방함.
⑤ 금형의 설계 및 보수에 고도의 기술 요구
⑥ 성형품의 형상 및 사용 재료의 한정
러너리스 성형에서 사용할 재료는 열안정성이 좋고 저온에서도 성형이 용이해야 함.
또한 열전도율이 높고 냉각시간이 빨라야 하며 저압에서도 성형이 용이해야 함.
(4) 러너리스 성형품의 형상과 사용 재료
1) 성형품의 형상
냉각에 소요되는 시간이 적은 성형 사이클 타임이 빠른 형상일 것.
냉각 및 단열이 어려운 게이트 부근에 요철이 있는 형상은 피할 것.
2) 사용 재료
① 열안정성이 좋을 것
저온에서 유동성이 좋은 성형 재료는 온도조절이 쉽고 게이트의 고화를 막을 수 있음.
② 유동성이 좋을 것
러너리스 성형은 게이트 부근의 단면적이 작고 저항이 커서 저압•저온에서도 유동성이 좋아아야 함.
③ 열변형 온도가 높을 것
열변형 온도가 높으면 성형품의 온도가 다소 높아도 이형이 가능하므로 성형 사이클 타임을 단축시키고 게이트의 고화를 막을 수 있음.
④ 열전도율이 높을 것
열전도율이 높으면 성형 재료에 내재되어 있는 열을 쉽게 냉각시킬 수 있어 성형 사이클 타임을 단축할 수 있음.
⑤ 비열이 낮을 것
비열이 낮으면 적은 효율로도 온도 조절이 쉬워짐.
4. 러너리스 시스템의 종류
(1) 웰타입 노즐 방식
1) 구조
웰타입 노즐 방식은 용융 재료가 잠기도록 되어 있는 공간(WELL)이 있어 외부는 냉각 고화되어 단열벽을 이루고 중심부는 항상 용융 상태가 되어 있음.
노즐에 사출압력이 작용하면 즉시 캐비티 내로 성형 재료가 충전이 됨.
2) 특징
1개 캐비티 금형에 적합함.
금형 구조가 간단하고 조작이 쉬움.
치수 정밀도가 높은 성형 재료에는 사용할 수 없음.
성형온도 범위가 좁은 성형 재료에는 사용할 수 없음.
(2) 익스텐션 노즐 방식
1) 구조
익스텐션 노즐 방식은 캐비티부터 사출성형기의 노즐을 연장하여 근접시킨 긴 노즐로써 노즐에서의 압력손실이 적음.
익스텐션 노즐 방식은 노즐 끝부분에 용융 재료가 고화되지 않도록 밴드히터를 설치하고 성형품에 스프루-러너가 남지 않음.
2) 특징
1개 캐비티 금형에 적합함.
용융 재료의 온도조절이 쉬움.
노즐의 열이 금형에 전해지기 쉬움,
(3) 인슐레이티드 러너 방식
1) 구조
인슐레이티드 러너 방식은 러너 지름을 20 ~ 25mm 정도로 크게 해서 외부는 고화된 단열층이 되고 중심부는 용융 상태가 되어 캐비티 내에 성형 재료를 쉽게 주입하도록 한 방식으로 밴드히터 등을 설치하여 게이트부의 냉각을 방지해야 함.
2) 특징
3매판 사출 금형을 러너리스 금형으로 만들 수 있음.
게이트는 뽑기 쉬운 역테이퍼로 함.
러너부가 냉각되지 않도록 성형 사이클 타임을 빠르게 진행해야 함.
온도조절과 재료교환 등이 번거로움.
(4) 핫러너 방식
1) 구조
핫러너 방식은 게이트부에 가열 장치를 부착하여 용융 재료를 항상 캐비티 내에 주입할 수 있도록 다기관 방식으로 러너를 가열 실린더 일부분으로 취급하는 방식.
2) 특징
다점 게이트를 채택할 수 있음.
러너의 압력손실이 적음.
금형 두께가 커지고 구조가 복잡함.
게이트가 저온 캐비티와 밀착되어 있어 금형온도 조절이 까다로움.
5. 핫러너의 금형설계 시 고려 사항
(1) 매니폴드 블록
1) 가열 방식
(가) 외부 가열 방식
외부 가열 방식은 러너 채널에 평행하게 가공한 구멍에 카트리지 히터를 삽입하거나 매니폴더 외부에 히터를 부착하는 방식.
(나) 내부 가열 방식
내부 가열방식은 카트리지 히터를 러너 채널 중에 설치하여 러너 내부에서 성형 재료를 가열하는 방식임.
러너의 벽에 접촉하는 성형 재료는 냉각•고화하여 단열재의 역할을 하고 히터의 열손실을 최소화하기 때문에 외부 가열 방식에 비해 히터의 용량이 작아도 됨.
2) 매니폴드 중량
매니폴드의 중량이 작을수록 가열에 따른 소요전력이 적어지므로 강도상 허용되는 한 매니폴드의 중량을 감소시키는 것이 필요함.
3) 단열 및 열팽창
(가) 단열 대책
사출성형기의 다이 플레이트와 금형 설치판 사이의 단열에는 일반적으로 6 ~ 10mm의 석면판이 설치됨.
또한 설치판과 매니폴드, 매니폴드와 형판 사이에는 3 ~ 8mm의 에어 갭을 두어 단열하는 경우가 많음.
매니폴드와 형판은 접촉면적을 가능한 한 작게하고 재질도 18-8스테인리스강과 같이 열전도성이 낮은 것이 좋음.
(나) 열팽창 대책
열팽창에 의해 발생되는 문제는 게이트의 중심과 매니폴드 블록 중심과의 어긋남 때문임.
이에 대한 대책은 금형 구조에 따라 차이가 있으나 매니폴드 블록과 형판과의 열팽창 차이만큼 노즐의 중심거리를 짧게 하면 됨.
열팽창 대책이 불충분하면 중심이 어긋나서 성형 재료가 누출되거나 노즐에 만곡 변형이 발생됨.
(2) 노즐
1) 노즐 가열 방식
(가) 무가열 방식(완전 단열 방식)
히터에 의해 노즐을 가열하는 것이 아니고 매니폴드 블록의 열에 의해 노즐 내의 성형 재료를 용융 상태로 유지하는 방식이고 노즐의 재질은 베릴륨동(Be-Cu)이 사용됨.
(나) 내부 가열 방식
노즐 내에 카트리지 히터를 삽입하여 가열하는 방식으로 히터 주위에 성형 재료가 흐르므로 열효율이 좋고 노즐 선단부까지 가열되므로 온도조절이 우수하며 게이트의 고화를 방지할 수 있음.
(다) 외부 가열방식
노즐의 외부에 밴드히터를 장착하여 가열하는 방식으로 성형 재료의 국부적인 가열은 없으나 히터의 크기에 제약이 있음.
2) 노즐 단열방식
(가) 세미 인슐레이티드 노즐
게이트부에서 노즐과 스프루 부시가 접촉되지 않도록 노즐 선단부 위에 틈새가 있고 이곳에 성형 재료가 유입되어서 단열 작용을 하고 베릴륨동을 사용함.
(나) 완전 인슐레이티드 노즐
게이트는 0.4 ~ 0.6mm 정도로 작게 하고 게이트 랜드의 길이를 짧게 하여 스프루 부시의 살두께를 두껍게 한 것으로 강철재의 트러스팅 스페이서가 노즐 밑부분에 장착되어 노즐이 완전히 성형 재료의 중앙에 떠 있는 상태가 되고 이로 인해 스프루 부시와의 접촉에 의한 냉각을 막을 수 있음.
(다) 내부 접촉 가열 노즐
노즐의 내부에 카트리지 히터를 넣어서 특히 선단부의 내부를 가열할 수 있도록 한 것으로 온도조절기가 장착되어 있어 조절이 자유롭고 노즐 내부를 가열하므로 노즐 선단이 스프루 부시와 접촉되는 것이 허용되며 노즐 길이를 짧게 할 수 있음.
(3) 러너리스
1) 개요
핫러너 방식은 러너리스 시스템에서 가장 성형성이 좋고 형상이나 사용 성형 재료의 제한이 적은 방식임.
2) 핫러너 가열 시스템의 종류
(가) INCOE 시스템
INCOE 시스템은 유선형을 갖는 토피도 속에 카트리지 히터를 내장한 것으로 직접 금형에 조립하여 사용함.
용융된 재료가 가열된 토피도의 주위를 통해 게이트로부터 금형의 캐비티에 주입됨.
(나) DU POINT 시스템
DU POINT 시스템은 POM, PA 등과 같은 엔지니어링 플라스틱의 사출을 위해 개발된 것으로 러너는 카트리지 히터에 의해 가열되고 폐쇄 프로브는 스프링의 탄성에 의해 닫혀 있다가 러너 내의 압력이 높아지면 프로브가 뒤로 밀리면서 게이트가 열리는 구조임.
3) 핫러너 선정 시 고려사항
매니폴드 각부의 조합부에서 성형 재료의 누출이 없을 것.
게이트가 막히지 않을 것.
게이트 밸런스를 확실히 유지할 것.
시스템 전체에 걸쳐 온도가 균일할 것.
매니폴드 블록의 온도 상승 시간이 빠를 것.
(4) 밸브 게이트
1) 개요
밸브 게이트는 성형 재료가 처음부터 압축되어 있으므로 밸브가 열렸을 때 용융된 재료의 팽창이 매우 빠르고 고속 사출이 가능하며 충전까지의 용융 재료의 온도 저하가 적어 핫러너 금형에 많이 사용됨.
밸브 게이트는 니들이 가이드 부시 내를 슬라이딩하면서 성형 재료를 유출함.
2) 특징
성형 재료의 온도가 낮아도 좋으므로 성형 재료의 열화가 감소되고 성형 사이클 타임이 단축됨.
응력과 변형이 작아 성형품의 불량이 감소됨.
성형 재료의 누출이 방지되므로 핀포인트 게이트를 적용할 수 있음.
게이트 밸런스가 유지됨.
3) 종류
(가) 오픈형
오픈형은 가장 간단한 구조로서 조작이 쉬우나 게이트 랜드가 남기 쉽고 성형 재료의 누출의 우려가 있음.
(나) 고정 니들형
고정 니들형은 게이트의 폐색을 막기 위해 중앙에 히터가 설치된 니들을 삽입하고 그 선단을 게이트 입구까지 길게 한 것임.
(다) 가동 니들형
가동 니들형은 보압 완료 후 니들을 밀어내서 게이트를 완전히 밀폐하는 방식으로 게이트에서 성형 재료의 누출이 없고 게이트의 흔적이 없음.
니들의 구동은 스프링, 공압, 유압이 사용됨.
이상으로 게이트에 대한 연재를 마치고 다음에는 또 다른 유동기구인 러너와 냉각회로에 대한 연재를 시작할 예정입니다.
2020년 07월 29일
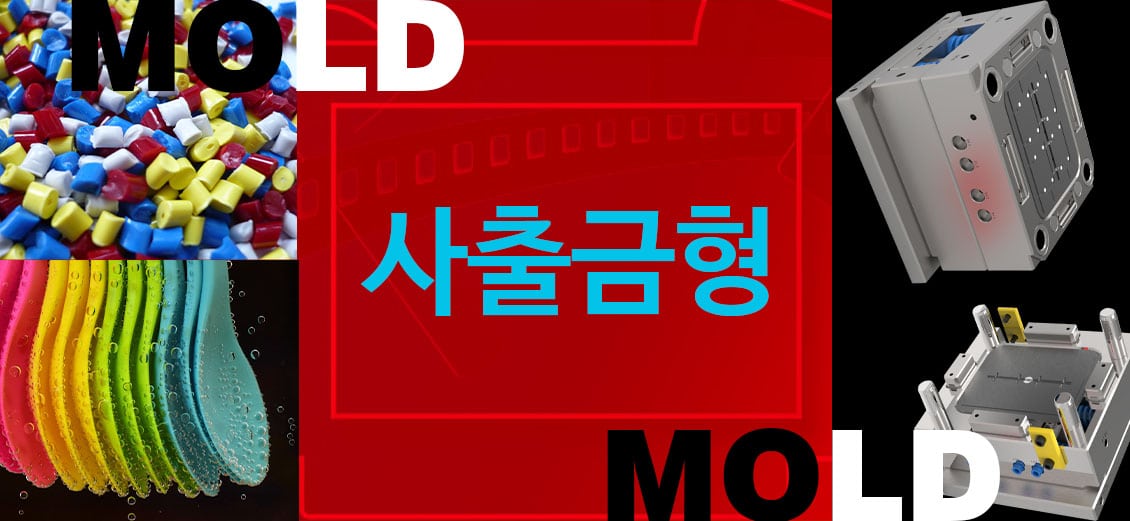
HOME → MOLD CATEGORIES →
사출 금형 7
제7장 게이트
게이트(GATE)는 충전되는 용융 재료의 흐름방향과 유량을 제어하고 성형품이 고화될 때까지 캐비티 내의 재료를 봉입하여 러너측으로 역류하는 것을 방지하며 재료에 마찰열을 발생시켜 온도를 상승시키는 역할을 하는 유동 기구입니다.
1. 게이트의 종류와 특징
(1) 비제한 게이트
1) 형상
원추 형상의 게이트로써 스프루가 그대로 게이트가 되므로 스프루 게이트 또는 다이렉트 게이트라고도 함.
비제한 게이트는 제한 게이트와는 달리 게이트가 급속하게 고화되지 않도록 단면적을 좁히지 않은 게이트를 말함.
2) 특징
성형압력의 손실이 적음.
금형 구조가 간단하고 고장이 적으며 러너가 필요 없음.
스프루의 고화시간이 길어지므로 성형 사이클 타임이 긺.
게이트를 절단하는 후가공이 필요함.
잔류응력과 충전으로 인한 변형 및 크랙이 발생하기 쉬움.
성형성이 좋아 모든 사출용 성형 재료에 적용할 수 있음.
잔류응력으로 인해 배향이 일어나기 쉬으므로 게이트 주변에 링 모양의 리브를 설치하여 보강하는 것이 좋음.
3) 설계 요점
게이트 입구의 지름은 노즐 구멍의 지름보다 0.5 ~ 1.0mm 정도 크게 할 것.
게이트의 테이퍼 각도는 2˚를 최소로 하되 고점도 플라스틱에서는 약간 굵게 저점도 플라스틱일 경우에는 약간 작게할 것.
게이트의 치수는 사용하는 성형 재료 및 성형품 중량에 따라 차이가 있지만 일반적으로 다음과 같이 사용하고 있음.
[상기 표에서 단위는 mm임.]
(2) 제한 게이트
1) 형상
비제한 게이트 이외에 모든 게이트가 해당됨.
2) 특징
게이트 부근에서 잔류응력과 변형이 감소됨.
성형품의 변형, 크랙, 뒤틀림, 굽힘 등이 감소됨.
게이트의 고화시간이 짧으므로 성형 사이클 타임을 단축시킬 수 있음.
다수 개 뽑기, 다점 게이트일 때 게이트 밸런스를 유지하기가 쉬움.
게이트 제거가 간단함.
성형 재료가 게이트를 통과할 때 압력손실이 큼.
2. 제한 게이트의 종류
(1) 표준 게이트
1) 형상
표준 게이트는 캐비티 형판(가동측 형판)에 직사각형의 홈을 파서 성형품의 측면에서 용융 재료를 주입하는 게이트로써 사이드 게이트라고도 함.
충전량을 제한하고 게이트부에서 급속히 고화시켜서 사출압력 손실을 막고자 할 때 사용함.
2) 특징
단면 형상이 간단하여 가공이 쉬움.
게이트의 치수 변경이 쉽고 정밀하게 가공할 수 있음.
충전 속도는 게이트의 고화와 관계없이 조절할 수 있음.
성형품에서 게이트를 제거하기 위해 후가공이 필요함.
거의 모든 성형 재료에 적용할 수 있음.
3) 설계 요점
게이트의 지름 또는 깊이는 성형품의 두께의 1/2 정도로 할 것.
게이트 랜드는 게이트 지름 또는 길이와 같게 할 것.
게이트 홈과 깊이의 비율은 3 : 1을 표준으로 하고 폭의 지름보다 클 때에는 팬 게이트를 사용할 것.
표준 게이트의 깊이 0.5 ~ 1.5mm, 폭 1.5 ~ 5mm, 랜드 1.5 ~ 2.5mm가 일반적이고 대형 성형품일 경우에는 게이트의 깊이 2.0 ~ 2.5mm(성형품 두께의 70 ~ 80% 수준) , 폭 7 ~ 10mm, 랜드 2.0 ~ 3.0mm 정도임.
(가) 게이트의 깊이
재료 | λ | 재료 | λ |
---|---|---|---|
PS, PE | 0.6 | PVAC, PA | 0.8 |
POM, PC, PP | 0.7 | PVC | 0.9 |
(나) 게이트의 폭
(2) 오버랩 게이트
1) 형상
오버랩 게이트는 표준 게이트와 기본적으로 동일하지만 성형품의 측면이 아닌 평면부에 설치하는 게이트임.
게이트 자국이 파팅 라인에 남게 되므로 게이트 제거 및 후가공에 유의해야 함.
두께가 두꺼운 PVC 제품에 주로 사용하는 게이트임.
2) 설계 요점
게이트 치수의 설계식은 표준 게이트와 같으며 길이는 다음과 같음.
(3) 팬 게이트
1) 형상
팬 게이트는 큰 평판의 면 및 얇은 단면에 매끄럽게 또는 균일하게 충전하는데 적합한 게이트로써 게이트 부근의 결함을 최소화 하는데 가장 효과적인 게이트임.
팬 게이트는 캐비티를 향해 게이트 끝을 부채꼴 모양으로 넓게 펼친 것으로 기포나 플로 마크의 발생이 없이 균일하게 충전할 수 있음.
팬 게이트의 위치 선정은 성형성과 후가공을 고려하여 결정해야 함.
2) 특징
게이트 부근의 결함을 최소화할 수 있음.
게이트 절단이 복잡하고 흔적이 남음.
경질 PVC를 제외한 대부분의 성형 재료에 적용할 수 있음.
3) 설계 요점
게이트 랜드(L)는 표준 게이트보다 약간 긴 6mm 전•후로 할 것.
게이트의 두께
게이트의 폭
(4) 필름 게이트
1) 형상
필름 게이트는 성형품의 폭과 게이트의 폭을 같은 길이로 하고 두께를 얇게 한 게이트로서 플래시 게이트 또는 슬릿 게이트라고도 함.
필름 게이트는 일반적으로 성형품의 폭 전체에 걸쳐서 게이트를 설치하는 경우가 많지만 성형품의 폭보다 좁게 설치해도 무방하고 게이트 절단을 고려해서 좁게 하는 것이 바람직함.
필름 게이트는 평판상의 성형품에 대한 수축 변형을 최소로 억제하려고 하는 경우에 사용함.
2) 특징
성형 재료의 주입이 쉬움.
내부응력이나 변형이 적음.
평판상의 성형품 평면도를 좋게 함.
경질 PVC 이외의 성형 재료에 적용할 수 있음.
3) 설계 요점
게이트의 설치 위치는 성형품의 폭이 좁은 곳에 할 것.
러너는 게이트 폭에 상관없이 성형품의 폭 이상으로 길게 할 수 있음.
게이트의 두께는 0.2 ~ 1.0mm, 게이트 랜드는 1mm 정도가 기준 치수임.
(5) 디스크 게이트
1) 형상
디스크 게이트는 구멍이 있는 성형품의 구멍 중앙부에 스프루를 설치하여 구멍 주위에 전면으로부터 성형 재료를 캐비티에 주입하는 앏은 원판상의 게이트이고 다이어 프레임 게이트라고도 함.
게이트 설치 시 성형품의 형상에 제약이 따르고 성형품에 웰드 라인 발생을 방지하기 위해 사용함.
게이트 설치 시 안지름이 중요할 경우에는 단면에 랩 형상으로 게이트를 설치해야 함.
2매판 사출 금형에서는 1개 뽑기 원통형에 사용되고 3매판이나 러너리스 사출 금형에서는 다수 개 뽑기도 가능함.
2) 특징
성형 재료의 주입이 쉽고 웰드 라인 발생을 방지할 수 있음.
성형품에 구멍이 두 군데 있을 경우에는 서브 러너를 설치하여 웰드 라인을 방지하고 원형 펀치나 탁상 드릴 머신으로 가공하여 성형품과 분리해야 함.
경질 PVC 이외의 모든 성형 재료에 적용할 수 있음.
3) 설계 요점
게이트의 깊이는 0.2 ~ 1.5mm, 랜드는 0.7 ~ 1.2mm가 적당함.
일반용일 경우 게이트의 깊이
정밀용일 경우 게이트의 깊이
정밀용일 경우 랜드의 길이
(6) 링 게이트
1) 형상
링 게이트는 원통형의 소형 성형품을 성형하기 위해 원통상의 외주에 러너를 링 모양으로 돌려서 원판상의 게이트로 성형 재료를 균일하게 주입하는 게이트로써 살두께가 균일한 성형품을 얻을 수 있음.
링 게이트는 러너 주입구의 반대쪽에 오버 플로를 설치하여 균형을 잡아줘야 함.
스트리퍼판이나 슬리브에 의해 성형품을 취출하므로 러너는 사다리꼴 형상을 주로 사용함.
2) 특징
성형 재료가 균일하게 주입되므로 웰드 라인의 발생이 방지됨.
코어 핀의 편심 발생이 방지됨.
3) 설계 요점
랜드의 길이는 0.7 ~ 1.2mm로 하고,
게이트의 깊이는 h = 0.7λt로 구할 것.
(7) 탭(터브) 게이트
1) 형상
오버랩 게이트를 변형시킨 것으로서 성형품의 일부에 조각 부분(TAB)을 만들어서 러너로부터 성형 재료가 직접 캐비티에 주입되지 않고 게이트를 통과하여 탭에 모인 후 충전되는 게이트임.
성형품에 직접 게이트를 붙일 수 없는 경우 또는 게이트부에 변형이 생기기 쉬운 성형 재료로 성형할 때 탭 게이트를 사용함.
탭 게이트는 전형적으로 광학 제품처럼 낮은 전단 응력이 요구되는 제품 성형에 사용됨.
2) 특징
탭에서 성형압력을 완충시켜 원활한 흐름으로 캐비티에 충전되므로 잔류응력이나 변형이 없는 성형품을 얻을 수 있음.
제팅이나 싱크 마크가 방지됨.
PVC, PC, PMMA 등과 같이 유동성이 좋지 않은 경질 플라스틱 성형에 적합함.
탭 게이트는 러너에 대해서 직각으로 탭을 붙이는 것이 일반적이고 탭은 플로 마크나 웰드 라인을 피하기 위해 살두께가 두꺼운 곳에 설치해야 함.
3) 설계 요점
탭의 폭은 6mm 이상이고 깊이는 캐비티 두께의 75%이며 탭의 길이는 러너 지금의 1.5배 정도로 할 것.
게이트의 설계는 표준 게이트의 기준을 따를 것.
탭의 크기는 폭(X) = D, 깊이(Y) = 0.9t, 길이(Z) =1.5D로 할 것.
탭의 위치는 성형품 테두리에서 150mm 이내가 좋고 성형품의 폭이 넓을 경우에는 멀티 탭 게이트를 설치하며 탭 간의 거리는 300mm 이내로 해야 함.
(8) 핀포인트 게이트
1) 형상
핀포인트 게이트는 성형품의 중앙에 게이트를 설치할 경우에 사용되는 원형의 게이트로써 다점 게이트로 사용하는 경우가 많음.
핀포인트 게이트는 단면적이 작아 유동저항이 커서 저점도 플라스틱에 사용하거나 사출압력을 높여서 사출을 시행해야 함.
[핀포인트 게이트 치수]
2)특징
게이트의 설치 위치에 제한을 받지 않고 자유롭게 결정할 수 있음.
게이트 부근에 잔류응력이 적음.
투영 면적이 크거나 변형이 발생하기 쉬운 성형품에 다점 게이트를 설치하면 수축 및 변형의 발생을 줄일 수 있음.
3매판 사출 금형에 채택하면 형개력에 의해 게이트가 자동으로 절단되고 성형품과 러너를 별도로 꺼낼 수 있음.
3매판 사출 금형, 핫러너 금형, 웰타입 노즐이 설치된 2매판 사출 금형에 적용할 수 있음.
3) 설계 요점
랜드 길이(L)는 0.8 ~ 1.2mm로 할 것.
게이트 지름(d)
단위 : mm
살두께 | 0.80 | 0.90 | 1.30 | 1.50 | 1.80 | 2.00 | 2.30 | 2.50 |
---|---|---|---|---|---|---|---|---|
C | 0.036 | 0.041 | 0.047 | 0.051 | 0.055 | 0.058 | 0.062 | 0.065 |
☞ 성형품의 살두께를 0.7 ~ 2.5mm 이내로 적용하고 웰타입 노즐에서는 30% 작게 하여야 함.
(9) 서브마린 게이트
1) 형상
서브마린 게이트는 러너를 파팅 라인에 만들고 게이트는 고정측 형판이나 가동측 형판을 터널식으로 파고 들어가 성형 재료를 캐비티 안으로 주입하는 게이트로 터널 게이트라고도 함.
서브마린 게이트는 성형품 표면에 게이트 자국을 남기고 싶지 않을 때 사용되고 성형품 측면 또는 이면에 설치할 수 있음.
형개 후 이젝터 기구에 의해 성형품이 돌출됨과 동시에 게이트가 자동으로 절단됨.
게이트 자국이 성형품 표면에 남으면 안 될 경우에는 이젝터 핀에 2차 러너를 가공하고 2차 러너에 서브마린 게이트를 설치하여 2차 러너 말단부를 성형품 내측에 붙여서 성형 재료를 간접적으로 주입되도록 할 수 있는데 이때 압력손실이 크게 발생하므로 사출압력을 크게 할 필요가 있고 이젝터 핀이 회전하지 않도록 해야 함.
2) 특징
게이트는 형개 시 자동 절단됨.
핀포인트 게이트보다 금형 구조가 간단함.
압력손실이 크고 게이트 가공이 어려움.
3) 설계 요점
파팅 라인과 게이트 입구의 경사각은 25˚~40˚로 할 것.
터널 부분의 테이퍼는 15˚~45˚로 할 것. (취출을 고려할 때 30˚~40˚가 적합)
랜드 길이 및 게이트 지름은 핀포인트 게이트와 동일하게 적용할 것.
(10) 커브드 게이트
1) 형상
커브드 게이트는 2차 러너붙이 서브마린 게이트를 변형한 것으로 서브마린 게이트의 단점인 압력손실을 막고 2차 러너를 제거한 게이트로써 코끼리 게이트, 바나나 게이트, G 게이트라 불리기도 함.
2) 특징
게이트 설치 위치 선택이 유연함.
게이트는 성형품과 별로도 분리할 수 있음.
성형품 외관에 게이트 자국이 남지 않음.
성형품 표면에 응력이 발생할 수 있음.
게이트 제작 과정이 복잡함.
적절한 설계가 수반되지 않으면 형개 시 게이트가 파손될 수 있음.
3) 설계 요점
게이트 지름(d)은 Φ0.8 ~ Φ1.2mm, 게이트 길이(L)는 1.0 ~ 1.2mm로 할 것.
커브드부는 게이트부의 끝단 지름 Φ2.5mm에서 러너부의 시작단 지름 0.8D로 점진적으로 크게 제작할 것.
3. 러너리스 시스템
(1) 개요
사출 금형에서 스프루와 러너는 용융된 재료를 캐비티 내부로 안내하는 유동 기구로써 스프루와 러너는 성형품을 얻기 위한 보조물일 뿐 매사이클마다 성형품과 동시에 성형되어 취출됨.
취출 시에 성형품과 분리하고 마무리를 해야 하기 때문에 스크랩이 발생하게 되는데 러너리스 시스템은 이러한 스프루와 러너가 생성되지 않도록 하는 금형을 의미함.
러너리스 금형은 이와 같은 의미로서 러너가 없는 상태로 제품만 취출되는 구조의 금형을 말하며, 사출성형기의 노즐을 이용하여 용융 재료를 직접 캐비티에 충전하는 것을 말함.
(2) 성형방법
사출성형기의 노즐로부터 직접 캐비티에 사출하는 방법.
플라스틱의 단열성을 이용하여 스프루-러너 중심부의 성형 재료를 용융 상태로 유지하는 방법.
러너에 열을 가하여 성형 재료를 용융 상태로 유지하는 방법.
(3) 특징
① 성형품의 품질 우수
대형 성형품을 성형 시 비제한 게이트에서는 게이트 주변에 잔류응력으로 인해 발생한 변형이 성형품의 물성에 큰 영향을 주는데 이를 개선하기 위해 다점 핀포인트 게이트와 3매판 사출 금형을 채택하지만 금형의 크기가 대형이다 보니 유지•보수가 힘들어서 러너리스 금형으로 대체하고 있음.
② 재료비 절감
러너리스 성형은 스프루-러너가 배출되지 않기 때문에 재료의 손실이 발생하지 않음.
③ 성형 사이클 타임 단축
러너리스 성형은 스프루-러너의 냉각 시간이 필요 없으므로 고속 성형을 할 수 있고 사출성형기의 불필요한 다이 플레이트 운동을 수행하지 않기 때문에 생산시간이 단축됨.
④ 사양이 한 단계 낮은 사출성형기 사용 가능
스프루-러너와 관계되는 사출용량, 형체력, 3매판 사출 금형 채택 시 형개 스트로크 등이 기준치보다 작은 사출성형기를 선택해도 무방함.
⑤ 금형의 설계 및 보수에 고도의 기술 요구
⑥ 성형품의 형상 및 사용 재료의 한정
러너리스 성형에서 사용할 재료는 열안정성이 좋고 저온에서도 성형이 용이해야 함.
또한 열전도율이 높고 냉각시간이 빨라야 하며 저압에서도 성형이 용이해야 함.
(4) 러너리스 성형품의 형상과 사용 재료
1) 성형품의 형상
냉각에 소요되는 시간이 적은 성형 사이클 타임이 빠른 형상일 것.
냉각 및 단열이 어려운 게이트 부근에 요철이 있는 형상은 피할 것.
2) 사용 재료
① 열안정성이 좋을 것
저온에서 유동성이 좋은 성형 재료는 온도조절이 쉽고 게이트의 고화를 막을 수 있음.
② 유동성이 좋을 것
러너리스 성형은 게이트 부근의 단면적이 작고 저항이 커서 저압•저온에서도 유동성이 좋아아야 함.
③ 열변형 온도가 높을 것
열변형 온도가 높으면 성형품의 온도가 다소 높아도 이형이 가능하므로 성형 사이클 타임을 단축시키고 게이트의 고화를 막을 수 있음.
④ 열전도율이 높을 것
열전도율이 높으면 성형 재료에 내재되어 있는 열을 쉽게 냉각시킬 수 있어 성형 사이클 타임을 단축할 수 있음.
⑤ 비열이 낮을 것
비열이 낮으면 적은 효율로도 온도 조절이 쉬워짐.
4. 러너리스 시스템의 종류
(1) 웰타입 노즐 방식
1) 구조
웰타입 노즐 방식은 용융 재료가 잠기도록 되어 있는 공간(WELL)이 있어 외부는 냉각 고화되어 단열벽을 이루고 중심부는 항상 용융 상태가 되어 있음.
노즐에 사출압력이 작용하면 즉시 캐비티 내로 성형 재료가 충전이 됨.
2) 특징
1개 캐비티 금형에 적합함.
금형 구조가 간단하고 조작이 쉬움.
치수 정밀도가 높은 성형 재료에는 사용할 수 없음.
성형온도 범위가 좁은 성형 재료에는 사용할 수 없음.
(2) 익스텐션 노즐 방식
1) 구조
익스텐션 노즐 방식은 캐비티부터 사출성형기의 노즐을 연장하여 근접시킨 긴 노즐로써 노즐에서의 압력손실이 적음.
익스텐션 노즐 방식은 노즐 끝부분에 용융 재료가 고화되지 않도록 밴드히터를 설치하고 성형품에 스프루-러너가 남지 않음.
2) 특징
1개 캐비티 금형에 적합함.
용융 재료의 온도조절이 쉬움.
노즐의 열이 금형에 전해지기 쉬움,
(3) 인슐레이티드 러너 방식
1) 구조
인슐레이티드 러너 방식은 러너 지름을 20 ~ 25mm 정도로 크게 해서 외부는 고화된 단열층이 되고 중심부는 용융 상태가 되어 캐비티 내에 성형 재료를 쉽게 주입하도록 한 방식으로 밴드히터 등을 설치하여 게이트부의 냉각을 방지해야 함.
2) 특징
3매판 사출 금형을 러너리스 금형으로 만들 수 있음.
게이트는 뽑기 쉬운 역테이퍼로 함.
러너부가 냉각되지 않도록 성형 사이클 타임을 빠르게 진행해야 함.
온도조절과 재료교환 등이 번거로움.
(4) 핫러너 방식
1) 구조
핫러너 방식은 게이트부에 가열 장치를 부착하여 용융 재료를 항상 캐비티 내에 주입할 수 있도록 다기관 방식으로 러너를 가열 실린더 일부분으로 취급하는 방식.
2) 특징
다점 게이트를 채택할 수 있음.
러너의 압력손실이 적음.
금형 두께가 커지고 구조가 복잡함.
게이트가 저온 캐비티와 밀착되어 있어 금형온도 조절이 까다로움.
5. 핫러너의 금형설계 시 고려 사항
(1) 매니폴드 블록
1) 가열 방식
(가) 외부 가열 방식
외부 가열 방식은 러너 채널에 평행하게 가공한 구멍에 카트리지 히터를 삽입하거나 매니폴더 외부에 히터를 부착하는 방식.
(나) 내부 가열 방식
내부 가열방식은 카트리지 히터를 러너 채널 중에 설치하여 러너 내부에서 성형 재료를 가열하는 방식임.
러너의 벽에 접촉하는 성형 재료는 냉각•고화하여 단열재의 역할을 하고 히터의 열손실을 최소화하기 때문에 외부 가열 방식에 비해 히터의 용량이 작아도 됨.
2) 매니폴드 중량
매니폴드의 중량이 작을수록 가열에 따른 소요전력이 적어지므로 강도상 허용되는 한 매니폴드의 중량을 감소시키는 것이 필요함.
3) 단열 및 열팽창
(가) 단열 대책
사출성형기의 다이 플레이트와 금형 설치판 사이의 단열에는 일반적으로 6 ~ 10mm의 석면판이 설치됨.
또한 설치판과 매니폴드, 매니폴드와 형판 사이에는 3 ~ 8mm의 에어 갭을 두어 단열하는 경우가 많음.
매니폴드와 형판은 접촉면적을 가능한 한 작게하고 재질도 18-8스테인리스강과 같이 열전도성이 낮은 것이 좋음.
(나) 열팽창 대책
열팽창에 의해 발생되는 문제는 게이트의 중심과 매니폴드 블록 중심과의 어긋남 때문임.
이에 대한 대책은 금형 구조에 따라 차이가 있으나 매니폴드 블록과 형판과의 열팽창 차이만큼 노즐의 중심거리를 짧게 하면 됨.
열팽창 대책이 불충분하면 중심이 어긋나서 성형 재료가 누출되거나 노즐에 만곡 변형이 발생됨.
(2) 노즐
1) 노즐 가열 방식
(가) 무가열 방식(완전 단열 방식)
히터에 의해 노즐을 가열하는 것이 아니고 매니폴드 블록의 열에 의해 노즐 내의 성형 재료를 용융 상태로 유지하는 방식이고 노즐의 재질은 베릴륨동(Be-Cu)이 사용됨.
(나) 내부 가열 방식
노즐 내에 카트리지 히터를 삽입하여 가열하는 방식으로 히터 주위에 성형 재료가 흐르므로 열효율이 좋고 노즐 선단부까지 가열되므로 온도조절이 우수하며 게이트의 고화를 방지할 수 있음.
(다) 외부 가열방식
노즐의 외부에 밴드히터를 장착하여 가열하는 방식으로 성형 재료의 국부적인 가열은 없으나 히터의 크기에 제약이 있음.
2) 노즐 단열방식
(가) 세미 인슐레이티드 노즐
게이트부에서 노즐과 스프루 부시가 접촉되지 않도록 노즐 선단부 위에 틈새가 있고 이곳에 성형 재료가 유입되어서 단열 작용을 하고 베릴륨동을 사용함.
(나) 완전 인슐레이티드 노즐
게이트는 0.4 ~ 0.6mm 정도로 작게 하고 게이트 랜드의 길이를 짧게 하여 스프루 부시의 살두께를 두껍게 한 것으로 강철재의 트러스팅 스페이서가 노즐 밑부분에 장착되어 노즐이 완전히 성형 재료의 중앙에 떠 있는 상태가 되고 이로 인해 스프루 부시와의 접촉에 의한 냉각을 막을 수 있음.
(다) 내부 접촉 가열 노즐
노즐의 내부에 카트리지 히터를 넣어서 특히 선단부의 내부를 가열할 수 있도록 한 것으로 온도조절기가 장착되어 있어 조절이 자유롭고 노즐 내부를 가열하므로 노즐 선단이 스프루 부시와 접촉되는 것이 허용되며 노즐 길이를 짧게 할 수 있음.
(3) 러너리스
1) 개요
핫러너 방식은 러너리스 시스템에서 가장 성형성이 좋고 형상이나 사용 성형 재료의 제한이 적은 방식임.
2) 핫러너 가열 시스템의 종류
(가) INCOE 시스템
INCOE 시스템은 유선형을 갖는 토피도 속에 카트리지 히터를 내장한 것으로 직접 금형에 조립하여 사용함.
용융된 재료가 가열된 토피도의 주위를 통해 게이트로부터 금형의 캐비티에 주입됨.
(나) DU POINT 시스템
DU POINT 시스템은 POM, PA 등과 같은 엔지니어링 플라스틱의 사출을 위해 개발된 것으로 러너는 카트리지 히터에 의해 가열되고 폐쇄 프로브는 스프링의 탄성에 의해 닫혀 있다가 러너 내의 압력이 높아지면 프로브가 뒤로 밀리면서 게이트가 열리는 구조임.
3) 핫러너 선정 시 고려사항
매니폴드 각부의 조합부에서 성형 재료의 누출이 없을 것.
게이트가 막히지 않을 것.
게이트 밸런스를 확실히 유지할 것.
시스템 전체에 걸쳐 온도가 균일할 것.
매니폴드 블록의 온도 상승 시간이 빠를 것.
(4) 밸브 게이트
1) 개요
밸브 게이트는 성형 재료가 처음부터 압축되어 있으므로 밸브가 열렸을 때 용융된 재료의 팽창이 매우 빠르고 고속 사출이 가능하며 충전까지의 용융 재료의 온도 저하가 적어 핫러너 금형에 많이 사용됨.
밸브 게이트는 니들이 가이드 부시 내를 슬라이딩하면서 성형 재료를 유출함.
2) 특징
성형 재료의 온도가 낮아도 좋으므로 성형 재료의 열화가 감소되고 성형 사이클 타임이 단축됨.
응력과 변형이 작아 성형품의 불량이 감소됨.
성형 재료의 누출이 방지되므로 핀포인트 게이트를 적용할 수 있음.
게이트 밸런스가 유지됨.
3) 종류
(가) 오픈형
오픈형은 가장 간단한 구조로서 조작이 쉬우나 게이트 랜드가 남기 쉽고 성형 재료의 누출의 우려가 있음.
(나) 고정 니들형
고정 니들형은 게이트의 폐색을 막기 위해 중앙에 히터가 설치된 니들을 삽입하고 그 선단을 게이트 입구까지 길게 한 것임.
(다) 가동 니들형
가동 니들형은 보압 완료 후 니들을 밀어내서 게이트를 완전히 밀폐하는 방식으로 게이트에서 성형 재료의 누출이 없고 게이트의 흔적이 없음.
니들의 구동은 스프링, 공압, 유압이 사용됨.
이상으로 게이트에 대한 연재를 마치고 다음에는 또 다른 유동기구인 러너와 냉각회로에 대한 연재를 시작할 예정입니다.
2020년 07월 29일