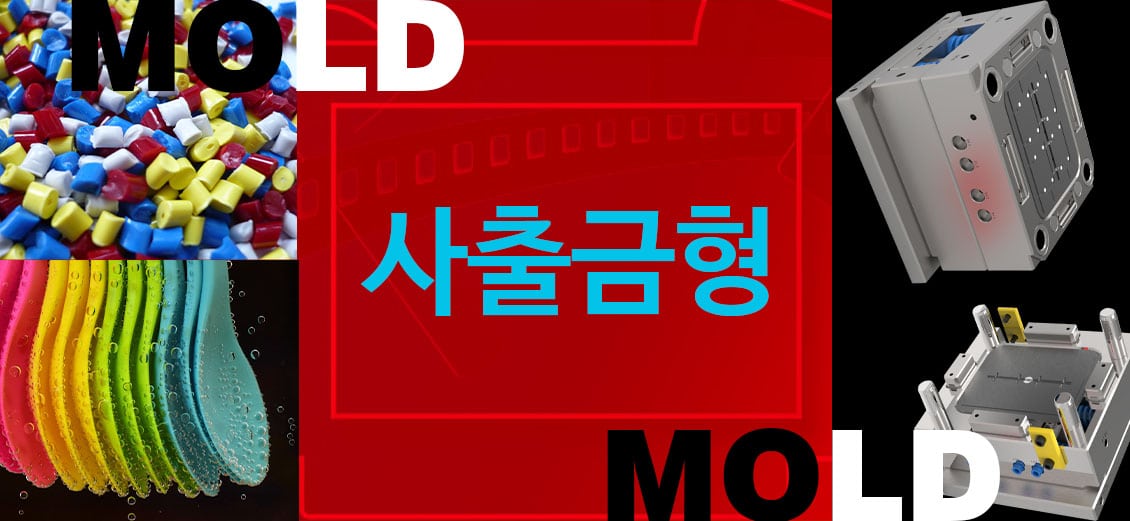
HOME → MOLD CATEGORIES →
사출 금형 9
제9장 사출 성형품 설계
사출 성형품 설계 시에는 균일한 살두께를 부여하고 모서리부에 라운드 처리를 해야 하며 합리적인 치수공차를 부여하여 사출 성형품의 변형이나 휨, 성형 수축 불량, 성형 사이클 타임의 지연, 재료의 낭비 등의 발생을 방지해야 합니다.
1. 사출 성형품 설계 원칙과 순서
(1) 사출 성형품 설계 원칙
1) 균일한 살두께 부여
사출 성형품의 살두께가 불균일하면 냉각 시 성형 수축의 차이로 인하여 잔류응력 증대, 변형, 치수 정밀도의 불균일, 싱크 마크, 성형 사이클 타임의 지연, 재료의 낭비 등이 발생함.
2) 모서리부의 라운드 처리
성형품의 예리한 모서리부는 응력의 집중으로 인하여 파괴강도가 급격히 떨어지므로 최소 반지름을 0.5mm 또는 살두께의 60%를 부여해야 함.
반면, 성형품의 모서리에 과대한 라운드 처리는 재료의 낭비, 싱크 마크, 과대한 치수 변화에 원인이 됨.
3) 합리적인 치수공차 부여
사출 성형품의 치수공차는 25mm 이하의 치수에 대해서는 ±0.05mm을 기준으로 부여해야 함.
(2) 사출 성형품 설계 순서
1) 제품의 사용 환경 정의
제품 사용 시 예측되는 하중의 종류와 크기를 가장 열악한 상황을 기준으로 정의하고 온도, 화학적 약품의 접촉 등과 같이 고려되어야 할 사용 환경을 모두 검토해야 함.
제품의 성능 테스트 규격이 있을 경우에는 테스트 상황의 물리적 의미를 상세하게 검토해야 함.
2) 초기 개념설계
제품의 개략 형상을 정의하여 기능에 적합한지를 단순화한 모델로 구현하고 이론적 수식 계산과 CAE를 적용하여 개념 설계안을 검토하며 적절한 성형 방법을 선정해야 함.
3) 1차 성형 재료 선정
사용 환경 정의와 초기 개념설계를 통하여 사용 재료의 기계적, 열적 요구 물성치를 설정하여 사용 가능한 범위를 결정함.
4) 선정 성형 재료에 적합한 설계 방안 구상
선정된 성형 재료에 알맞은 제품의 기본 살두께, 리브, 보스 등을 결정하고 내충격이나 진동 등의 특수한 기능이 있는 제품의 경우에는 시편 테스트와 CAE 적용으로 최적 설계 방안을 구상함.
5) 최종 성형 재료 선정
이전까지 검토한 내용을 종합하여 원재료 가격이 고려가 된 성형 재료의 종류와 그레이드를 결정함.
6) 상세 설계
적용 성형법을 고려하여 금형 빼기 구배를 결정하는 등 금형 제작이 가능한 상세 제품 도면 및 3차원 CAD 모델을 작성함.
7) 시제품 제작
성형 전문가와 공동으로 제품을 성형하고 조립부품이 있을 경우 제품 도면에 입각하여 조립 후 시제품을 완성함.
8) 시제품의 기능 평가
제품의 성능 테스트 규격이나 사용 환경 중 가장 열악한 상황으로 제품의 기능을 평가하여 제품의 평가 시스템을 구축하고 테스트 결과를 반영하여 제품설계를 수정하고 완료함.
2. 성형 수축률
(1) 성형 수축률의 정의
1) 개요
성형 수축은 사출 성형 공정에서 열과 압력의 변화에 의해서 생기는 것으로 성형 재료의 특성에 따라 그 범위가 정해짐.
성형 재료는 흐름방향에 방향성이 있고 성형품의 형상이나 성형 조건에 따라 고유의 성형 수축률의 범위가 결정됨.
2) 성형 수축률에 영향을 주는 요인
(가) 열적 수축
성형 재료가 가지고 있는 고유의 열팽창률에 의해 나타나는 수축.
(나) 탄성 회복에 의한 팽창
성형압력이 제거되어 원상태로 되돌아갈 때 발생되는 팽창.
(다) 결정화에 의한 수축
성형 공정에서 결정화에 따라 나타나는 체적 수축으로서 결정성 플라스틱이 비결정성 플라스틱보다 성형 수출률이 큼.
(라) 분자 배향 완화에 의한 수축
3) 금형 치수 계산
성형 수축률
위의 식에서 금형 치수를 구하면,
성형 수축률은 1보다 매우 작기 때문에 근사식을 사용하여 금형 치수를 구하기도 함.
(2) 성형 수축률의 변동 요인
1) 캐비티 내의 성형 재료의 압력
캐비티 내의 성형 재료에 가해지는 압력이 높을수록 성형 수축률은 작아짐.
2) 성형 재료의 온도
성형 재료의 온도가 높아지면 유동성이 좋아지고충전상태가 개선되며 냉각시간이 길어져서 밀도가 치밀해지므로 성형 수축률이 작아지는데 반해 열적 수축률이 커져서 냉각 후 수축량이 증가함.
달리 표현하면 성형 재료의 온도가 높아지면 금형 내에서의 흐름방향으로 각각의 층 간에 생기는 전단력이 작고 분자배향의 정도가 낮아 성형 수축률이 작아짐.
3) 스크루 전진 시간
게이트의 고화시간까지 스크루가 전진을 계속한다면 성형 수축률은 최소가 되고 제품 중량은 최대가 됨.
게이트가 고화되기 전에 스크루가 전진을 멈추면 성형 수축률이 커지는 동시에 치수의 변동도 커짐.
4) 금형온도
금형온도가 높아지면 금형 내에 있는 재료의 냉각이 늦어지기 때문에 금형 내에서의 성형 수축은 적어지나 이형이 된 이후에는 오히려 탄성 회복이 커져서 최종 성형 수축률은 커짐.
열경화성 플라스틱보다는 열가소성 플라스틱이 금형온도에 민감함.
5) 냉각시간
냉각시간이 길면 금형 내의 재료는 충분히 고화되기 때문에 이형 시에도 성형품의 치수는 금형 치수에 더욱 가깝게 되므로 성형 수축률이 작음.
결정성 플라스틱은 결정화도가 천천히 진행되어 결정화도가 높아지므로 오히려 성형 수축률이 커짐.
6) 성형품의 살두께
결정성 플라스틱에서는 살두께가 두꺼워지면 서냉되어 결정화도가 높아져서 성형 수축률이 크고 비결정성 플라스틱에서는 살두께에 상관없는 것과 살두께가 두꺼워짐에 따라 성형 수축률이 커지거나 작아지는 것 등이 있음.
7) 게이트 단면적
게이트 단면적이 작으면 게이트가 먼저 고화하여 금형 내의 재료에 충분한 성형압력이 작용하기 어려워지므로 일반적으로 성형 수축률이 커짐.
게이트에서 금형의 캐비티 내로 재료를 주입하는 속도가 빠르면 성형 수축률이 커지는데 게이트 단면적이 클수록 주입속도가 느려져서 성형 수축률이 작아짐.
8) 강화제의 함유율과 배향성
강화제를 함유한 성형 재료는 강화제의 배향이 성형 수축률의 방향성을 주는 원인이 되어 유동방향과 직각방향은 성형 수축률에 있어 큰 차이를 나타냄.
3. 사출 성형품 살두께
(1) 개요
성형품의 살두께는 균일한 것이 원칙이지만 성형품의 용도, 성형 조건, 재료의 성질 등을 고려하여 평균 살두께를 결정함.
성형품의 살두께는 기계적 강도 뿐만 아니라 유동 흐름의 난이성, 조립, 구조, 중량, 싱크 마크, 변형 등과 같이 외관상의 결점과 관련이 깊음.
(2) 성형품의 살두께 영향
1) 살두께가 너무 얇을 때
제품의 강도가 약해짐.
이형 시 파손의 우려가 있음.
성형시간이 빠름.
재료비가 절감됨.
충전 불량 방지를 위해 성형압력이 커야 함.
2) 살두께가 너무 두꺼울 때
제품의 강도가 커짐.
성형 재료의 유동성이 좋아지고 변형이 적어짐.
냉각•고화 시간이 길어져 성형 사이클 타임이 길어짐.
수축량이 커서 싱크 마크 또는 기포가 발생함.
3) 살두께가 균일할 때
성형 재료의 소모를 최소화할 수 있음.
냉각•고화 시간이 단축됨.
성형 수축률이 균일해짐
충전성이 일정함.
성형품의 내부응력 발생이 최소화됨.
(3) 성형품의 살두께 설정
1) 고려사항
구조상의 강도를 고려할 것.
이젝팅 때 파손되지 않도록 강도를 고려할 것.
성형 재료와 인서트 금속의 열팽창 차이에 의한 균열 방지를 고려할 것.
살두께가 얇은 부분에 충전 부족의 발생 여부를 고려하여 살두께를 결정할 것.
살두께가 두꺼운 부분에 싱크 마크의 발생을 고려하여 어느 한 부분만 두껍게 하지 말 것.
성형품 구멍 및 인서트 주위에 웰드 라인의 발생 여부를 고려할 것.
2) 살두께 설정 시 설계기준
살두께는 가능한 한 균일하게 할 것.
불연속 살두께 변화를 피할 것.
게이트 부근의 살두께는 약간 두껍게 할 것.
살두께 변화가 있는 단은 코너부의 라운드를 가능한 한 크게 할 것.
살두께에 대한 유동 길이의 비가 과대하지 않도록 할 것.
최소 살두께 공식
살두께의 변화를 50% 이내로 하되 그 이상에서는 리브로 보강할 것.
4. 파팅 라인
(1) 개요
파팅 라인은 성형품을 금형으로부터 이형시키기 위하여 고정측 형판과 가동측 형판이 열릴 때 분할되는 기준선을 말함.
파팅 라인의 위치에 따라 상품 가치, 금형 설계 및 제작 등에 큰 영향을 미치게 되므로 신중하게 결정되어야 함.
일반적으로 파팅 라인은 러너나 게이트가 가공되는 면이기도 함.
파팅 라인은 금형 면상 일직선이 바람직하지만 제품이 수행할 기능에 의존하며 계단 형상이나 곡선이 되는 경우도 있음.
(2) 파팅 라인 설정 시 고려 사항
눈에 잘 띄지 않는 위치 또는 형상으로 할 것
언더컷을 피할 수 있는 위치를 선택할 것.
형개 방향에 수직인 평면으로 할 것.
금형 가공이 용이한 위치와 형상으로 할 것.
게이트의 위치 및 형상을 고려할 것.
이형 후 성형품은 가동측 형판에 남도록 할 것.
5. 성형품의 빼기 구배
(1) 개요
빼기 구배는 성형품을 취출할 때 이젝팅을 쉽게 하기 위하여 파팅 라인에 수직인 제품 면에 구배를 주는 것을 말함.
빼기 구배는 가능한 한 크게 하는 것이 좋으나 경험에 의해 결정되는 경우가 많으며 고정밀도 제품은 허용되는 치수공차 내에서 부여되어야 함.
(2) 빼기 구배의 부여 기준
일반적인 빼기 구배 부여 기준식
고정밀도를 요하는 경우에 빼기 구배 부여 기준식
내•외측 빼기 구배는 내측을 외측보다 1˚ 정도 크게 할 것.
성형품에 무늬 형상이 있는 경우에는 빼기 구배를 1˚ 이상을 줄 것.
유리섬유, 탄산칼슘, 탤크 등을 포함한 성형 재료는 이형이 어려우므로 가능한 한 빼기 구배를 크게 하고 이젝팅을 에어 이젝터나 스트리퍼판을 사용할 것.
폴리스틸렌의 일반적인 빼기 구배는 2˚/25mm이어야 하고 최소 1˚/25mm로 할 것.
싱크 마크를 방지하기 위하여 리브의 밑바닥은 평균 살두께의 1/2로 하고 맨 위쪽의 두께는 금형 제작상 최소 1mm 이상으로 할 것.
창살의 피치는 3mm 이상으로 하고 창살의 전체 길이가 길면 빼기 구배를 5˚ 이상으로 할 것.
창살 높이가 8mm 이상일 경우에는 사다리꼴 모양으로 할 것.
(3) 상자 또는 덮개의 빼기 구배의 부여 기준
H가 50mm 이하일 경우에 빼기 구배
H가 100mm 이상일 경우에 빼기 구배
얇은 가죽 무늬가 있는 경우에 빼기 구배
컵과 같은 제품은 캐비티측보다 코어측에 빼기 구배를 약간 더 주는 것이 바람직함.
(4) 창살의 빼기 구배 부여 기준
일반적인 빼기 구배
창살의 피치가 4mm 이하일 경우에는 빼기 구배를 1/10 정도를 줄 것.
창살의 치수 C가 클수록 빼기 구배를 많이 줄 것.
창살의 높이(H)가 8mm 이상이거나 치수 C가 큰 경우에도 빼기 구배를 줄 수 없다면 캐비티 창살의 1/2H 이하의 창살을 붙여서 성형품을 가동측 형판에 남도록 할 것.
6. 성형품의 구멍
(1) 개요
성형품의 구멍은 다른 성형품과의 조립 및 장식 또는 통풍 기능을 위하여 사용됨.
성형품의 구멍은 게이트의 반대쪽에 웰드 라인이 생겨 강도가 감소되므로 강도상에 문제가 우려되는 경우에는 후가공을 하는 것이 바람직함.
이형 방향의 성형품 구멍 설계는 금형 구조상 용이하지만 측면 방향의 구멍 설계는 일반적으로 슬라이드 코어를 설치해야 하나 가능한 한 슬라이드 코어를 사용하지 않는 구조를 선택하는 것이 바람직함.
(2) 구멍 설계 시 고려 사항
구멍과 구멍의 중심거리는 구멍 지름의 2배 이상으로 할 것.
구멍 주변에 살두께는 두껍게 할 것.
구멍 중심과 제품 끝단과의 거리는 구멍 지름의 3배로 할 것.
구멍의 지름이 Φ1.5mm 이하인 경우에는 구멍 깊이는 구멍의 지름을 넘지 않도록 할 것.
핀으로 제품의 중간에 맞추어지는 구멍은 상•하 지름을 다르게 하여 단이 있는 구멍으로 할 것.
성형 재료의 흐름방향에 직각으로 막힌 구멍에서 가는 핀이 휘어질 염려가 있는 경우에는 D < 1.5mm 일 때 L ≤ D, D > 3mm 일 때 L ≤ 2D로 할 것.
다수의 구멍을 성형하는 경우에는 재질 및 성형 조건에 따라 구멍의 위치 및 간격을 다음과 같이 할 것.
구멍 지름(mm) | 단에서 구멍까지의 거리(mm) | 두 구멍간의 거리(mm) |
---|---|---|
1.5 | 2.5 | 3.5 |
2.5 | 3.0 | 5.0 |
3.0 | 4.0 | 6.5 |
5.0 | 5.5 | 8.5 |
6.5 | 6.5 | 11.0 |
8.0 | 8.0 | 14.0 |
10.0 | 10.0 | 18.0 |
12.5 | 12.5 | 22.0 |
7. 성형 나사
(1) 개요
성형품의 외측 또는 내측에 나사부를 갖는 제품을 성형하는 것으로서 성형 방향에 평행으로 성형되도록 하여야 함.
나사의 성형은 결합력이나 강도 문제 등으로 반복 사용 시 나사부가 손상될 우려가 있음.
(2) 나사 설계 시 고려사항
표준 나사로 설계할 것.
나사는 호칭 지름은 5mm, 피치는 0.75mm 이상으로 설계할 것.
길이가 긴 나사는 성형 수축으로 인하여 피치가 달라지므로 되도록이면 피할 것.
나사의 공차는 성형 재료의 성형 수축률보다 크게 설정할 것.
나사에는 반드시 1/15 ~ 1/25의 빼기 구배를 줄 것.
나사의 끼워맞춤은 지름에 따라 다르지만 0.1 ~ 0.4mm 정도의 클리어런스를 줄 것.
나사의 끝부분은 나사의 상부에서 0.8 ~ 1.0mm 정도 띄우고 시작되도록 할 것.
8mm 이하의 나사는 셀프 태핑을 하거나 인서트를 삽입할 것.
8. 인서트
(1) 개요
인서트는 나사 또는 체결 구멍과 같이 성형품 조립 시 작용하는 집중하중을 흡수하고 성형품을 조립하기 위하여 성형 공정 중에 금속재료를 삽입하는 것을 말함.
인서트 삽입 공정은 성형 사이클 타임을 길게 하고 성형 중 금형을 손상시킬 수 있으므로 가능한 한 금형상에서 인서트를 삽입하는 구조를 피하고 셀프 태핑 또는 접착하는 방법으로 하는 것이 바람직하나 강도가 저하될 우려가 있음.
(2) 인서트 설계 시 고려사항
인서트 제품에는 롤렛(널링) 또는 언더컷 등을 주어서 기계적 구속력을 갖도록 할 것.
인서트를 중심으로 축의 중심이 편심이나 기울어지지 않도록 할 것.
인서트 주변은 두께를 2mm 이상 크게 하여 보강할 것.
인서트 부위의 바깥지름은 인서트 지름의 2배 이상으로 할 것.
성형품 측벽과 인서트의 간격은 0.5mm 이상으로 할 것.
인서트 삽입 후 성형품에 균열이 발생 시 인서트를 예열하여 수축을 줄일 것.
인서트 보스 주위에는 가능한 한 보강용 리브를 설치할 것.
예리한 각 부분이 있는 곳에는 인서트를 삽입하는 구조를 피할 것.
인서트의 변형 및 인서트의 축 간 거리 등에 주의를 요할 것.
웰드 라인, 잔류응력에 의한 휨, 성형 수축 등에 의하여 국부적인 변화가 일어나지 않도록 할 것.
이상으로 사출 성형품 설계 연재를 마치고 다음에는 성형품의 보강과 불량의 원인 및 대책에 대한 연재를 시작할 예정입니다.
2020년 08월 06일
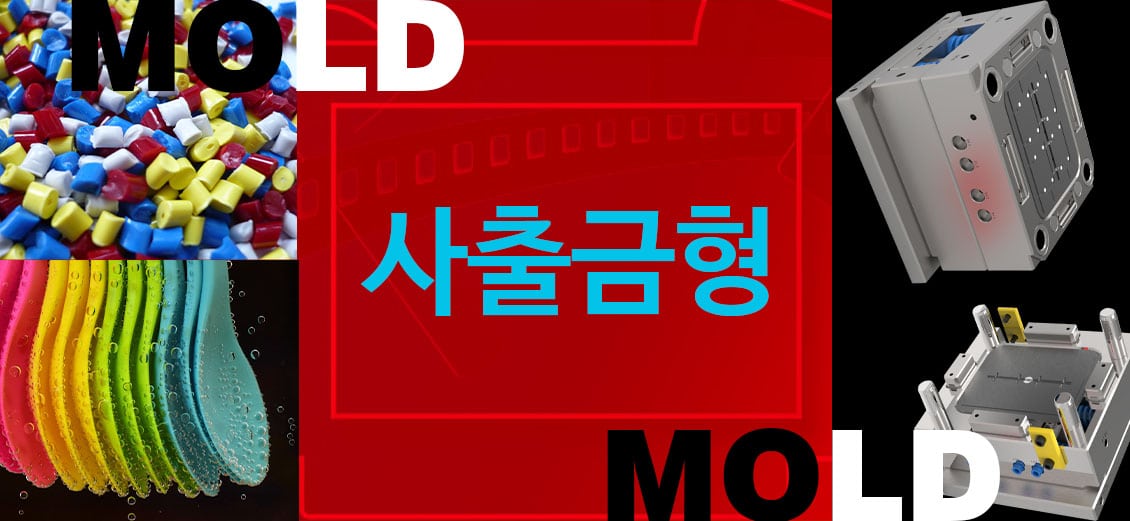
HOME → MOLD CATEGORIES →
사출 금형 9
제9장 사출 성형품 설계
사출 성형품 설계 시에는 균일한 살두께를 부여하고 모서리부에 라운드 처리를 해야 하며 합리적인 치수공차를 부여하여 사출 성형품의 변형이나 휨, 성형 수축 불량, 성형 사이클 타임의 지연, 재료의 낭비 등의 발생을 방지해야 합니다.
1. 사출 성형품 설계 원칙과 순서
(1) 사출 성형품 설계 원칙
1) 균일한 살두께 부여
사출 성형품의 살두께가 불균일하면 냉각 시 성형 수축의 차이로 인하여 잔류응력 증대, 변형, 치수 정밀도의 불균일, 싱크 마크, 성형 사이클 타임의 지연, 재료의 낭비 등이 발생함.
2) 모서리부의 라운드 처리
성형품의 예리한 모서리부는 응력의 집중으로 인하여 파괴강도가 급격히 떨어지므로 최소 반지름을 0.5mm 또는 살두께의 60%를 부여해야 함.
반면, 성형품의 모서리에 과대한 라운드 처리는 재료의 낭비, 싱크 마크, 과대한 치수 변화에 원인이 됨.
3) 합리적인 치수공차 부여
사출 성형품의 치수공차는 25mm 이하의 치수에 대해서는 ±0.05mm을 기준으로 부여해야 함.
(2) 사출 성형품 설계 순서
1) 제품의 사용 환경 정의
제품 사용 시 예측되는 하중의 종류와 크기를 가장 열악한 상황을 기준으로 정의하고 온도, 화학적 약품의 접촉 등과 같이 고려되어야 할 사용 환경을 모두 검토해야 함.
제품의 성능 테스트 규격이 있을 경우에는 테스트 상황의 물리적 의미를 상세하게 검토해야 함.
2) 초기 개념설계
제품의 개략 형상을 정의하여 기능에 적합한지를 단순화한 모델로 구현하고 이론적 수식 계산과 CAE를 적용하여 개념 설계안을 검토하며 적절한 성형 방법을 선정해야 함.
3) 1차 성형 재료 선정
사용 환경 정의와 초기 개념설계를 통하여 사용 재료의 기계적, 열적 요구 물성치를 설정하여 사용 가능한 범위를 결정함.
4) 선정 성형 재료에 적합한 설계 방안 구상
선정된 성형 재료에 알맞은 제품의 기본 살두께, 리브, 보스 등을 결정하고 내충격이나 진동 등의 특수한 기능이 있는 제품의 경우에는 시편 테스트와 CAE 적용으로 최적 설계 방안을 구상함.
5) 최종 성형 재료 선정
이전까지 검토한 내용을 종합하여 원재료 가격이 고려가 된 성형 재료의 종류와 그레이드를 결정함.
6) 상세 설계
적용 성형법을 고려하여 금형 빼기 구배를 결정하는 등 금형 제작이 가능한 상세 제품 도면 및 3차원 CAD 모델을 작성함.
7) 시제품 제작
성형 전문가와 공동으로 제품을 성형하고 조립부품이 있을 경우 제품 도면에 입각하여 조립 후 시제품을 완성함.
8) 시제품의 기능 평가
제품의 성능 테스트 규격이나 사용 환경 중 가장 열악한 상황으로 제품의 기능을 평가하여 제품의 평가 시스템을 구축하고 테스트 결과를 반영하여 제품설계를 수정하고 완료함.
2. 성형 수축률
(1) 성형 수축률의 정의
1) 개요
성형 수축은 사출 성형 공정에서 열과 압력의 변화에 의해서 생기는 것으로 성형 재료의 특성에 따라 그 범위가 정해짐.
성형 재료는 흐름방향에 방향성이 있고 성형품의 형상이나 성형 조건에 따라 고유의 성형 수축률의 범위가 결정됨.
2) 성형 수축률에 영향을 주는 요인
(가) 열적 수축
성형 재료가 가지고 있는 고유의 열팽창률에 의해 나타나는 수축.
(나) 탄성 회복에 의한 팽창
성형압력이 제거되어 원상태로 되돌아갈 때 발생되는 팽창.
(다) 결정화에 의한 수축
성형 공정에서 결정화에 따라 나타나는 체적 수축으로서 결정성 플라스틱이 비결정성 플라스틱보다 성형 수출률이 큼.
(라) 분자 배향 완화에 의한 수축
3) 금형 치수 계산
성형 수축률
위의 식에서 금형 치수를 구하면,
성형 수축률은 1보다 매우 작기 때문에 근사식을 사용하여 금형 치수를 구하기도 함.
(2) 성형 수축률의 변동 요인
1) 캐비티 내의 성형 재료의 압력
캐비티 내의 성형 재료에 가해지는 압력이 높을수록 성형 수축률은 작아짐.
2) 성형 재료의 온도
성형 재료의 온도가 높아지면 유동성이 좋아지고충전상태가 개선되며 냉각시간이 길어져서 밀도가 치밀해지므로 성형 수축률이 작아지는데 반해 열적 수축률이 커져서 냉각 후 수축량이 증가함.
달리 표현하면 성형 재료의 온도가 높아지면 금형 내에서의 흐름방향으로 각각의 층 간에 생기는 전단력이 작고 분자배향의 정도가 낮아 성형 수축률이 작아짐.
3) 스크루 전진 시간
게이트의 고화시간까지 스크루가 전진을 계속한다면 성형 수축률은 최소가 되고 제품 중량은 최대가 됨.
게이트가 고화되기 전에 스크루가 전진을 멈추면 성형 수축률이 커지는 동시에 치수의 변동도 커짐.
4) 금형온도
금형온도가 높아지면 금형 내에 있는 재료의 냉각이 늦어지기 때문에 금형 내에서의 성형 수축은 적어지나 이형이 된 이후에는 오히려 탄성 회복이 커져서 최종 성형 수축률은 커짐.
열경화성 플라스틱보다는 열가소성 플라스틱이 금형온도에 민감함.
5) 냉각시간
냉각시간이 길면 금형 내의 재료는 충분히 고화되기 때문에 이형 시에도 성형품의 치수는 금형 치수에 더욱 가깝게 되므로 성형 수축률이 작음.
결정성 플라스틱은 결정화도가 천천히 진행되어 결정화도가 높아지므로 오히려 성형 수축률이 커짐.
6) 성형품의 살두께
결정성 플라스틱에서는 살두께가 두꺼워지면 서냉되어 결정화도가 높아져서 성형 수축률이 크고 비결정성 플라스틱에서는 살두께에 상관없는 것과 살두께가 두꺼워짐에 따라 성형 수축률이 커지거나 작아지는 것 등이 있음.
7) 게이트 단면적
게이트 단면적이 작으면 게이트가 먼저 고화하여 금형 내의 재료에 충분한 성형압력이 작용하기 어려워지므로 일반적으로 성형 수축률이 커짐.
게이트에서 금형의 캐비티 내로 재료를 주입하는 속도가 빠르면 성형 수축률이 커지는데 게이트 단면적이 클수록 주입속도가 느려져서 성형 수축률이 작아짐.
8) 강화제의 함유율과 배향성
강화제를 함유한 성형 재료는 강화제의 배향이 성형 수축률의 방향성을 주는 원인이 되어 유동방향과 직각방향은 성형 수축률에 있어 큰 차이를 나타냄.
3. 사출 성형품 살두께
(1) 개요
성형품의 살두께는 균일한 것이 원칙이지만 성형품의 용도, 성형 조건, 재료의 성질 등을 고려하여 평균 살두께를 결정함.
성형품의 살두께는 기계적 강도 뿐만 아니라 유동 흐름의 난이성, 조립, 구조, 중량, 싱크 마크, 변형 등과 같이 외관상의 결점과 관련이 깊음.
(2) 성형품의 살두께 영향
1) 살두께가 너무 얇을 때
제품의 강도가 약해짐.
이형 시 파손의 우려가 있음.
성형시간이 빠름.
재료비가 절감됨.
충전 불량 방지를 위해 성형압력이 커야 함.
2) 살두께가 너무 두꺼울 때
제품의 강도가 커짐.
성형 재료의 유동성이 좋아지고 변형이 적어짐.
냉각•고화 시간이 길어져 성형 사이클 타임이 길어짐.
수축량이 커서 싱크 마크 또는 기포가 발생함.
3) 살두께가 균일할 때
성형 재료의 소모를 최소화할 수 있음.
냉각•고화 시간이 단축됨.
성형 수축률이 균일해짐
충전성이 일정함.
성형품의 내부응력 발생이 최소화됨.
(3) 성형품의 살두께 설정
1) 고려사항
구조상의 강도를 고려할 것.
이젝팅 때 파손되지 않도록 강도를 고려할 것.
성형 재료와 인서트 금속의 열팽창 차이에 의한 균열 방지를 고려할 것.
살두께가 얇은 부분에 충전 부족의 발생 여부를 고려하여 살두께를 결정할 것.
살두께가 두꺼운 부분에 싱크 마크의 발생을 고려하여 어느 한 부분만 두껍게 하지 말 것.
성형품 구멍 및 인서트 주위에 웰드 라인의 발생 여부를 고려할 것.
2) 살두께 설정 시 설계기준
살두께는 가능한 한 균일하게 할 것.
불연속 살두께 변화를 피할 것.
게이트 부근의 살두께는 약간 두껍게 할 것.
살두께 변화가 있는 단은 코너부의 라운드를 가능한 한 크게 할 것.
살두께에 대한 유동 길이의 비가 과대하지 않도록 할 것.
최소 살두께 공식
살두께의 변화를 50% 이내로 하되 그 이상에서는 리브로 보강할 것.
4. 파팅 라인
(1) 개요
파팅 라인은 성형품을 금형으로부터 이형시키기 위하여 고정측 형판과 가동측 형판이 열릴 때 분할되는 기준선을 말함.
파팅 라인의 위치에 따라 상품 가치, 금형 설계 및 제작 등에 큰 영향을 미치게 되므로 신중하게 결정되어야 함.
일반적으로 파팅 라인은 러너나 게이트가 가공되는 면이기도 함.
파팅 라인은 금형 면상 일직선이 바람직하지만 제품이 수행할 기능에 의존하며 계단 형상이나 곡선이 되는 경우도 있음.
(2) 파팅 라인 설정 시 고려 사항
눈에 잘 띄지 않는 위치 또는 형상으로 할 것
언더컷을 피할 수 있는 위치를 선택할 것.
형개 방향에 수직인 평면으로 할 것.
금형 가공이 용이한 위치와 형상으로 할 것.
게이트의 위치 및 형상을 고려할 것.
이형 후 성형품은 가동측 형판에 남도록 할 것.
5. 성형품의 빼기 구배
(1) 개요
빼기 구배는 성형품을 취출할 때 이젝팅을 쉽게 하기 위하여 파팅 라인에 수직인 제품 면에 구배를 주는 것을 말함.
빼기 구배는 가능한 한 크게 하는 것이 좋으나 경험에 의해 결정되는 경우가 많으며 고정밀도 제품은 허용되는 치수공차 내에서 부여되어야 함.
(2) 빼기 구배의 부여 기준
일반적인 빼기 구배 부여 기준식
고정밀도를 요하는 경우에 빼기 구배 부여 기준식
내•외측 빼기 구배는 내측을 외측보다 1˚ 정도 크게 할 것.
성형품에 무늬 형상이 있는 경우에는 빼기 구배를 1˚ 이상을 줄 것.
유리섬유, 탄산칼슘, 탤크 등을 포함한 성형 재료는 이형이 어려우므로 가능한 한 빼기 구배를 크게 하고 이젝팅을 에어 이젝터나 스트리퍼판을 사용할 것.
폴리스틸렌의 일반적인 빼기 구배는 2˚/25mm이어야 하고 최소 1˚/25mm로 할 것.
싱크 마크를 방지하기 위하여 리브의 밑바닥은 평균 살두께의 1/2로 하고 맨 위쪽의 두께는 금형 제작상 최소 1mm 이상으로 할 것.
창살의 피치는 3mm 이상으로 하고 창살의 전체 길이가 길면 빼기 구배를 5˚ 이상으로 할 것.
창살 높이가 8mm 이상일 경우에는 사다리꼴 모양으로 할 것.
(3) 상자 또는 덮개의 빼기 구배의 부여 기준
H가 50mm 이하일 경우에 빼기 구배
H가 100mm 이상일 경우에 빼기 구배
얇은 가죽 무늬가 있는 경우에 빼기 구배
컵과 같은 제품은 캐비티측보다 코어측에 빼기 구배를 약간 더 주는 것이 바람직함.
(4) 창살의 빼기 구배 부여 기준
일반적인 빼기 구배
창살의 피치가 4mm 이하일 경우에는 빼기 구배를 1/10 정도를 줄 것.
창살의 치수 C가 클수록 빼기 구배를 많이 줄 것.
창살의 높이(H)가 8mm 이상이거나 치수 C가 큰 경우에도 빼기 구배를 줄 수 없다면 캐비티 창살의 1/2H 이하의 창살을 붙여서 성형품을 가동측 형판에 남도록 할 것.
6. 성형품의 구멍
(1) 개요
성형품의 구멍은 다른 성형품과의 조립 및 장식 또는 통풍 기능을 위하여 사용됨.
성형품의 구멍은 게이트의 반대쪽에 웰드 라인이 생겨 강도가 감소되므로 강도상에 문제가 우려되는 경우에는 후가공을 하는 것이 바람직함.
이형 방향의 성형품 구멍 설계는 금형 구조상 용이하지만 측면 방향의 구멍 설계는 일반적으로 슬라이드 코어를 설치해야 하나 가능한 한 슬라이드 코어를 사용하지 않는 구조를 선택하는 것이 바람직함.
(2) 구멍 설계 시 고려 사항
구멍과 구멍의 중심거리는 구멍 지름의 2배 이상으로 할 것.
구멍 주변에 살두께는 두껍게 할 것.
구멍 중심과 제품 끝단과의 거리는 구멍 지름의 3배로 할 것.
구멍의 지름이 Φ1.5mm 이하인 경우에는 구멍 깊이는 구멍의 지름을 넘지 않도록 할 것.
핀으로 제품의 중간에 맞추어지는 구멍은 상•하 지름을 다르게 하여 단이 있는 구멍으로 할 것.
성형 재료의 흐름방향에 직각으로 막힌 구멍에서 가는 핀이 휘어질 염려가 있는 경우에는 D < 1.5mm 일 때 L ≤ D, D > 3mm 일 때 L ≤ 2D로 할 것.
다수의 구멍을 성형하는 경우에는 재질 및 성형 조건에 따라 구멍의 위치 및 간격을 다음과 같이 할 것.
구멍 지름(mm) | 단에서 구멍까지의 거리(mm) | 두 구멍간의 거리(mm) |
---|---|---|
1.5 | 2.5 | 3.5 |
2.5 | 3.0 | 5.0 |
3.0 | 4.0 | 6.5 |
5.0 | 5.5 | 8.5 |
6.5 | 6.5 | 11.0 |
8.0 | 8.0 | 14.0 |
10.0 | 10.0 | 18.0 |
12.5 | 12.5 | 22.0 |
7. 성형 나사
(1) 개요
성형품의 외측 또는 내측에 나사부를 갖는 제품을 성형하는 것으로서 성형 방향에 평행으로 성형되도록 하여야 함.
나사의 성형은 결합력이나 강도 문제 등으로 반복 사용 시 나사부가 손상될 우려가 있음.
(2) 나사 설계 시 고려사항
표준 나사로 설계할 것.
나사는 호칭 지름은 5mm, 피치는 0.75mm 이상으로 설계할 것.
길이가 긴 나사는 성형 수축으로 인하여 피치가 달라지므로 되도록이면 피할 것.
나사의 공차는 성형 재료의 성형 수축률보다 크게 설정할 것.
나사에는 반드시 1/15 ~ 1/25의 빼기 구배를 줄 것.
나사의 끼워맞춤은 지름에 따라 다르지만 0.1 ~ 0.4mm 정도의 클리어런스를 줄 것.
나사의 끝부분은 나사의 상부에서 0.8 ~ 1.0mm 정도 띄우고 시작되도록 할 것.
8mm 이하의 나사는 셀프 태핑을 하거나 인서트를 삽입할 것.
8. 인서트
(1) 개요
인서트는 나사 또는 체결 구멍과 같이 성형품 조립 시 작용하는 집중하중을 흡수하고 성형품을 조립하기 위하여 성형 공정 중에 금속재료를 삽입하는 것을 말함.
인서트 삽입 공정은 성형 사이클 타임을 길게 하고 성형 중 금형을 손상시킬 수 있으므로 가능한 한 금형상에서 인서트를 삽입하는 구조를 피하고 셀프 태핑 또는 접착하는 방법으로 하는 것이 바람직하나 강도가 저하될 우려가 있음.
(2) 인서트 설계 시 고려사항
인서트 제품에는 롤렛(널링) 또는 언더컷 등을 주어서 기계적 구속력을 갖도록 할 것.
인서트를 중심으로 축의 중심이 편심이나 기울어지지 않도록 할 것.
인서트 주변은 두께를 2mm 이상 크게 하여 보강할 것.
인서트 부위의 바깥지름은 인서트 지름의 2배 이상으로 할 것.
성형품 측벽과 인서트의 간격은 0.5mm 이상으로 할 것.
인서트 삽입 후 성형품에 균열이 발생 시 인서트를 예열하여 수축을 줄일 것.
인서트 보스 주위에는 가능한 한 보강용 리브를 설치할 것.
예리한 각 부분이 있는 곳에는 인서트를 삽입하는 구조를 피할 것.
인서트의 변형 및 인서트의 축 간 거리 등에 주의를 요할 것.
웰드 라인, 잔류응력에 의한 휨, 성형 수축 등에 의하여 국부적인 변화가 일어나지 않도록 할 것.
이상으로 사출 성형품 설계 연재를 마치고 다음에는 성형품의 보강과 불량의 원인 및 대책에 대한 연재를 시작할 예정입니다.
2020년 08월 06일
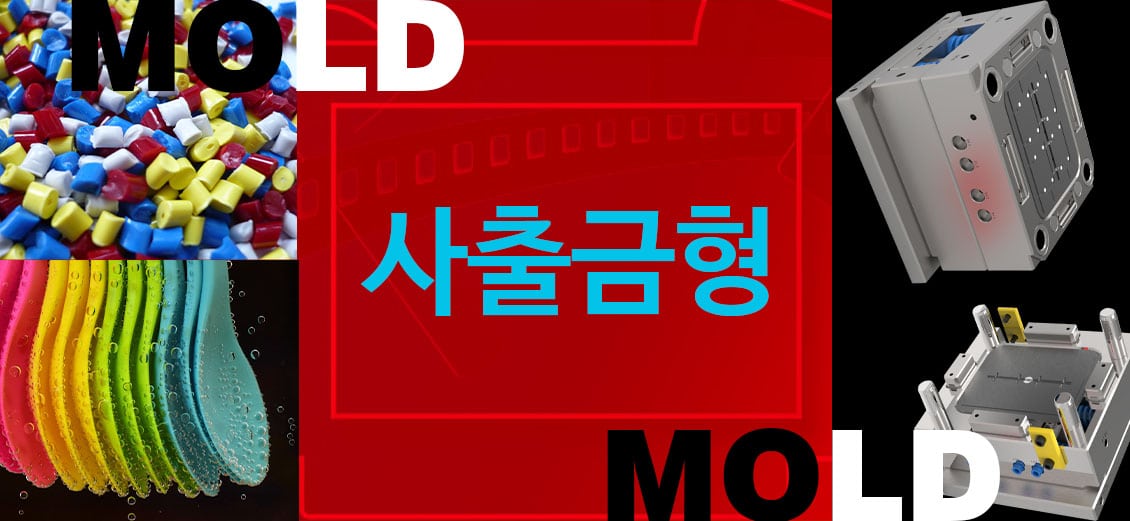
HOME → MOLD CATEGORIES →
사출 금형 9
제9장 사출 성형품 설계
사출 성형품 설계 시에는 균일한 살두께를 부여하고 모서리부에 라운드 처리를 해야 하며 합리적인 치수공차를 부여하여 사출 성형품의 변형이나 휨, 성형 수축 불량, 성형 사이클 타임의 지연, 재료의 낭비 등의 발생을 방지해야 합니다.
1. 사출 성형품 설계 원칙과 순서
(1) 사출 성형품 설계 원칙
1) 균일한 살두께 부여
사출 성형품의 살두께가 불균일하면 냉각 시 성형 수축의 차이로 인하여 잔류응력 증대, 변형, 치수 정밀도의 불균일, 싱크 마크, 성형 사이클 타임의 지연, 재료의 낭비 등이 발생함.
2) 모서리부의 라운드 처리
성형품의 예리한 모서리부는 응력의 집중으로 인하여 파괴강도가 급격히 떨어지므로 최소 반지름을 0.5mm 또는 살두께의 60%를 부여해야 함.
반면, 성형품의 모서리에 과대한 라운드 처리는 재료의 낭비, 싱크 마크, 과대한 치수 변화에 원인이 됨.
3) 합리적인 치수공차 부여
사출 성형품의 치수공차는 25mm 이하의 치수에 대해서는 ±0.05mm을 기준으로 부여해야 함.
(2) 사출 성형품 설계 순서
1) 제품의 사용 환경 정의
제품 사용 시 예측되는 하중의 종류와 크기를 가장 열악한 상황을 기준으로 정의하고 온도, 화학적 약품의 접촉 등과 같이 고려되어야 할 사용 환경을 모두 검토해야 함.
제품의 성능 테스트 규격이 있을 경우에는 테스트 상황의 물리적 의미를 상세하게 검토해야 함.
2) 초기 개념설계
제품의 개략 형상을 정의하여 기능에 적합한지를 단순화한 모델로 구현하고 이론적 수식 계산과 CAE를 적용하여 개념 설계안을 검토하며 적절한 성형 방법을 선정해야 함.
3) 1차 성형 재료 선정
사용 환경 정의와 초기 개념설계를 통하여 사용 재료의 기계적, 열적 요구 물성치를 설정하여 사용 가능한 범위를 결정함.
4) 선정 성형 재료에 적합한 설계 방안 구상
선정된 성형 재료에 알맞은 제품의 기본 살두께, 리브, 보스 등을 결정하고 내충격이나 진동 등의 특수한 기능이 있는 제품의 경우에는 시편 테스트와 CAE 적용으로 최적 설계 방안을 구상함.
5) 최종 성형 재료 선정
이전까지 검토한 내용을 종합하여 원재료 가격이 고려가 된 성형 재료의 종류와 그레이드를 결정함.
6) 상세 설계
적용 성형법을 고려하여 금형 빼기 구배를 결정하는 등 금형 제작이 가능한 상세 제품 도면 및 3차원 CAD 모델을 작성함.
7) 시제품 제작
성형 전문가와 공동으로 제품을 성형하고 조립부품이 있을 경우 제품 도면에 입각하여 조립 후 시제품을 완성함.
8) 시제품의 기능 평가
제품의 성능 테스트 규격이나 사용 환경 중 가장 열악한 상황으로 제품의 기능을 평가하여 제품의 평가 시스템을 구축하고 테스트 결과를 반영하여 제품설계를 수정하고 완료함.
2. 성형 수축률
(1) 성형 수축률의 정의
1) 개요
성형 수축은 사출 성형 공정에서 열과 압력의 변화에 의해서 생기는 것으로 성형 재료의 특성에 따라 그 범위가 정해짐.
성형 재료는 흐름방향에 방향성이 있고 성형품의 형상이나 성형 조건에 따라 고유의 성형 수축률의 범위가 결정됨.
2) 성형 수축률에 영향을 주는 요인
(가) 열적 수축
성형 재료가 가지고 있는 고유의 열팽창률에 의해 나타나는 수축.
(나) 탄성 회복에 의한 팽창
성형압력이 제거되어 원상태로 되돌아갈 때 발생되는 팽창.
(다) 결정화에 의한 수축
성형 공정에서 결정화에 따라 나타나는 체적 수축으로서 결정성 플라스틱이 비결정성 플라스틱보다 성형 수출률이 큼.
(라) 분자 배향 완화에 의한 수축
3) 금형 치수 계산
성형 수축률
위의 식에서 금형 치수를 구하면,
성형 수축률은 1보다 매우 작기 때문에 근사식을 사용하여 금형 치수를 구하기도 함.
(2) 성형 수축률의 변동 요인
1) 캐비티 내의 성형 재료의 압력
캐비티 내의 성형 재료에 가해지는 압력이 높을수록 성형 수축률은 작아짐.
2) 성형 재료의 온도
성형 재료의 온도가 높아지면 유동성이 좋아지고충전상태가 개선되며 냉각시간이 길어져서 밀도가 치밀해지므로 성형 수축률이 작아지는데 반해 열적 수축률이 커져서 냉각 후 수축량이 증가함.
달리 표현하면 성형 재료의 온도가 높아지면 금형 내에서의 흐름방향으로 각각의 층 간에 생기는 전단력이 작고 분자배향의 정도가 낮아 성형 수축률이 작아짐.
3) 스크루 전진 시간
게이트의 고화시간까지 스크루가 전진을 계속한다면 성형 수축률은 최소가 되고 제품 중량은 최대가 됨.
게이트가 고화되기 전에 스크루가 전진을 멈추면 성형 수축률이 커지는 동시에 치수의 변동도 커짐.
4) 금형온도
금형온도가 높아지면 금형 내에 있는 재료의 냉각이 늦어지기 때문에 금형 내에서의 성형 수축은 적어지나 이형이 된 이후에는 오히려 탄성 회복이 커져서 최종 성형 수축률은 커짐.
열경화성 플라스틱보다는 열가소성 플라스틱이 금형온도에 민감함.
5) 냉각시간
냉각시간이 길면 금형 내의 재료는 충분히 고화되기 때문에 이형 시에도 성형품의 치수는 금형 치수에 더욱 가깝게 되므로 성형 수축률이 작음.
결정성 플라스틱은 결정화도가 천천히 진행되어 결정화도가 높아지므로 오히려 성형 수축률이 커짐.
6) 성형품의 살두께
결정성 플라스틱에서는 살두께가 두꺼워지면 서냉되어 결정화도가 높아져서 성형 수축률이 크고 비결정성 플라스틱에서는 살두께에 상관없는 것과 살두께가 두꺼워짐에 따라 성형 수축률이 커지거나 작아지는 것 등이 있음.
7) 게이트 단면적
게이트 단면적이 작으면 게이트가 먼저 고화하여 금형 내의 재료에 충분한 성형압력이 작용하기 어려워지므로 일반적으로 성형 수축률이 커짐.
게이트에서 금형의 캐비티 내로 재료를 주입하는 속도가 빠르면 성형 수축률이 커지는데 게이트 단면적이 클수록 주입속도가 느려져서 성형 수축률이 작아짐.
8) 강화제의 함유율과 배향성
강화제를 함유한 성형 재료는 강화제의 배향이 성형 수축률의 방향성을 주는 원인이 되어 유동방향과 직각방향은 성형 수축률에 있어 큰 차이를 나타냄.
3. 사출 성형품 살두께
(1) 개요
성형품의 살두께는 균일한 것이 원칙이지만 성형품의 용도, 성형 조건, 재료의 성질 등을 고려하여 평균 살두께를 결정함.
성형품의 살두께는 기계적 강도 뿐만 아니라 유동 흐름의 난이성, 조립, 구조, 중량, 싱크 마크, 변형 등과 같이 외관상의 결점과 관련이 깊음.
(2) 성형품의 살두께 영향
1) 살두께가 너무 얇을 때
제품의 강도가 약해짐.
이형 시 파손의 우려가 있음.
성형시간이 빠름.
재료비가 절감됨.
충전 불량 방지를 위해 성형압력이 커야 함.
2) 살두께가 너무 두꺼울 때
제품의 강도가 커짐.
성형 재료의 유동성이 좋아지고 변형이 적어짐.
냉각•고화 시간이 길어져 성형 사이클 타임이 길어짐.
수축량이 커서 싱크 마크 또는 기포가 발생함.
3) 살두께가 균일할 때
성형 재료의 소모를 최소화할 수 있음.
냉각•고화 시간이 단축됨.
성형 수축률이 균일해짐
충전성이 일정함.
성형품의 내부응력 발생이 최소화됨.
(3) 성형품의 살두께 설정
1) 고려사항
구조상의 강도를 고려할 것.
이젝팅 때 파손되지 않도록 강도를 고려할 것.
성형 재료와 인서트 금속의 열팽창 차이에 의한 균열 방지를 고려할 것.
살두께가 얇은 부분에 충전 부족의 발생 여부를 고려하여 살두께를 결정할 것.
살두께가 두꺼운 부분에 싱크 마크의 발생을 고려하여 어느 한 부분만 두껍게 하지 말 것.
성형품 구멍 및 인서트 주위에 웰드 라인의 발생 여부를 고려할 것.
2) 살두께 설정 시 설계기준
살두께는 가능한 한 균일하게 할 것.
불연속 살두께 변화를 피할 것.
게이트 부근의 살두께는 약간 두껍게 할 것.
살두께 변화가 있는 단은 코너부의 라운드를 가능한 한 크게 할 것.
살두께에 대한 유동 길이의 비가 과대하지 않도록 할 것.
최소 살두께 공식
살두께의 변화를 50% 이내로 하되 그 이상에서는 리브로 보강할 것.
4. 파팅 라인
(1) 개요
파팅 라인은 성형품을 금형으로부터 이형시키기 위하여 고정측 형판과 가동측 형판이 열릴 때 분할되는 기준선을 말함.
파팅 라인의 위치에 따라 상품 가치, 금형 설계 및 제작 등에 큰 영향을 미치게 되므로 신중하게 결정되어야 함.
일반적으로 파팅 라인은 러너나 게이트가 가공되는 면이기도 함.
파팅 라인은 금형 면상 일직선이 바람직하지만 제품이 수행할 기능에 의존하며 계단 형상이나 곡선이 되는 경우도 있음.
(2) 파팅 라인 설정 시 고려 사항
눈에 잘 띄지 않는 위치 또는 형상으로 할 것
언더컷을 피할 수 있는 위치를 선택할 것.
형개 방향에 수직인 평면으로 할 것.
금형 가공이 용이한 위치와 형상으로 할 것.
게이트의 위치 및 형상을 고려할 것.
이형 후 성형품은 가동측 형판에 남도록 할 것.
5. 성형품의 빼기 구배
(1) 개요
빼기 구배는 성형품을 취출할 때 이젝팅을 쉽게 하기 위하여 파팅 라인에 수직인 제품 면에 구배를 주는 것을 말함.
빼기 구배는 가능한 한 크게 하는 것이 좋으나 경험에 의해 결정되는 경우가 많으며 고정밀도 제품은 허용되는 치수공차 내에서 부여되어야 함.
(2) 빼기 구배의 부여 기준
일반적인 빼기 구배 부여 기준식
고정밀도를 요하는 경우에 빼기 구배 부여 기준식
내•외측 빼기 구배는 내측을 외측보다 1˚ 정도 크게 할 것.
성형품에 무늬 형상이 있는 경우에는 빼기 구배를 1˚ 이상을 줄 것.
유리섬유, 탄산칼슘, 탤크 등을 포함한 성형 재료는 이형이 어려우므로 가능한 한 빼기 구배를 크게 하고 이젝팅을 에어 이젝터나 스트리퍼판을 사용할 것.
폴리스틸렌의 일반적인 빼기 구배는 2˚/25mm이어야 하고 최소 1˚/25mm로 할 것.
싱크 마크를 방지하기 위하여 리브의 밑바닥은 평균 살두께의 1/2로 하고 맨 위쪽의 두께는 금형 제작상 최소 1mm 이상으로 할 것.
창살의 피치는 3mm 이상으로 하고 창살의 전체 길이가 길면 빼기 구배를 5˚ 이상으로 할 것.
창살 높이가 8mm 이상일 경우에는 사다리꼴 모양으로 할 것.
(3) 상자 또는 덮개의 빼기 구배의 부여 기준
H가 50mm 이하일 경우에 빼기 구배
H가 100mm 이상일 경우에 빼기 구배
얇은 가죽 무늬가 있는 경우에 빼기 구배
컵과 같은 제품은 캐비티측보다 코어측에 빼기 구배를 약간 더 주는 것이 바람직함.
(4) 창살의 빼기 구배 부여 기준
일반적인 빼기 구배
창살의 피치가 4mm 이하일 경우에는 빼기 구배를 1/10 정도를 줄 것.
창살의 치수 C가 클수록 빼기 구배를 많이 줄 것.
창살의 높이(H)가 8mm 이상이거나 치수 C가 큰 경우에도 빼기 구배를 줄 수 없다면 캐비티 창살의 1/2H 이하의 창살을 붙여서 성형품을 가동측 형판에 남도록 할 것.
6. 성형품의 구멍
(1) 개요
성형품의 구멍은 다른 성형품과의 조립 및 장식 또는 통풍 기능을 위하여 사용됨.
성형품의 구멍은 게이트의 반대쪽에 웰드 라인이 생겨 강도가 감소되므로 강도상에 문제가 우려되는 경우에는 후가공을 하는 것이 바람직함.
이형 방향의 성형품 구멍 설계는 금형 구조상 용이하지만 측면 방향의 구멍 설계는 일반적으로 슬라이드 코어를 설치해야 하나 가능한 한 슬라이드 코어를 사용하지 않는 구조를 선택하는 것이 바람직함.
(2) 구멍 설계 시 고려 사항
구멍과 구멍의 중심거리는 구멍 지름의 2배 이상으로 할 것.
구멍 주변에 살두께는 두껍게 할 것.
구멍 중심과 제품 끝단과의 거리는 구멍 지름의 3배로 할 것.
구멍의 지름이 Φ1.5mm 이하인 경우에는 구멍 깊이는 구멍의 지름을 넘지 않도록 할 것.
핀으로 제품의 중간에 맞추어지는 구멍은 상•하 지름을 다르게 하여 단이 있는 구멍으로 할 것.
성형 재료의 흐름방향에 직각으로 막힌 구멍에서 가는 핀이 휘어질 염려가 있는 경우에는 D < 1.5mm 일 때 L ≤ D, D > 3mm 일 때 L ≤ 2D로 할 것.
다수의 구멍을 성형하는 경우에는 재질 및 성형 조건에 따라 구멍의 위치 및 간격을 다음과 같이 할 것.
구멍 지름(mm) | 단에서 구멍까지의 거리(mm) | 두 구멍간의 거리(mm) |
---|---|---|
1.5 | 2.5 | 3.5 |
2.5 | 3.0 | 5.0 |
3.0 | 4.0 | 6.5 |
5.0 | 5.5 | 8.5 |
6.5 | 6.5 | 11.0 |
8.0 | 8.0 | 14.0 |
10.0 | 10.0 | 18.0 |
12.5 | 12.5 | 22.0 |
7. 성형 나사
(1) 개요
성형품의 외측 또는 내측에 나사부를 갖는 제품을 성형하는 것으로서 성형 방향에 평행으로 성형되도록 하여야 함.
나사의 성형은 결합력이나 강도 문제 등으로 반복 사용 시 나사부가 손상될 우려가 있음.
(2) 나사 설계 시 고려사항
표준 나사로 설계할 것.
나사는 호칭 지름은 5mm, 피치는 0.75mm 이상으로 설계할 것.
길이가 긴 나사는 성형 수축으로 인하여 피치가 달라지므로 되도록이면 피할 것.
나사의 공차는 성형 재료의 성형 수축률보다 크게 설정할 것.
나사에는 반드시 1/15 ~ 1/25의 빼기 구배를 줄 것.
나사의 끼워맞춤은 지름에 따라 다르지만 0.1 ~ 0.4mm 정도의 클리어런스를 줄 것.
나사의 끝부분은 나사의 상부에서 0.8 ~ 1.0mm 정도 띄우고 시작되도록 할 것.
8mm 이하의 나사는 셀프 태핑을 하거나 인서트를 삽입할 것.
8. 인서트
(1) 개요
인서트는 나사 또는 체결 구멍과 같이 성형품 조립 시 작용하는 집중하중을 흡수하고 성형품을 조립하기 위하여 성형 공정 중에 금속재료를 삽입하는 것을 말함.
인서트 삽입 공정은 성형 사이클 타임을 길게 하고 성형 중 금형을 손상시킬 수 있으므로 가능한 한 금형상에서 인서트를 삽입하는 구조를 피하고 셀프 태핑 또는 접착하는 방법으로 하는 것이 바람직하나 강도가 저하될 우려가 있음.
(2) 인서트 설계 시 고려사항
인서트 제품에는 롤렛(널링) 또는 언더컷 등을 주어서 기계적 구속력을 갖도록 할 것.
인서트를 중심으로 축의 중심이 편심이나 기울어지지 않도록 할 것.
인서트 주변은 두께를 2mm 이상 크게 하여 보강할 것.
인서트 부위의 바깥지름은 인서트 지름의 2배 이상으로 할 것.
성형품 측벽과 인서트의 간격은 0.5mm 이상으로 할 것.
인서트 삽입 후 성형품에 균열이 발생 시 인서트를 예열하여 수축을 줄일 것.
인서트 보스 주위에는 가능한 한 보강용 리브를 설치할 것.
예리한 각 부분이 있는 곳에는 인서트를 삽입하는 구조를 피할 것.
인서트의 변형 및 인서트의 축 간 거리 등에 주의를 요할 것.
웰드 라인, 잔류응력에 의한 휨, 성형 수축 등에 의하여 국부적인 변화가 일어나지 않도록 할 것.
이상으로 사출 성형품 설계 연재를 마치고 다음에는 성형품의 보강과 불량의 원인 및 대책에 대한 연재를 시작할 예정입니다.
2020년 08월 06일