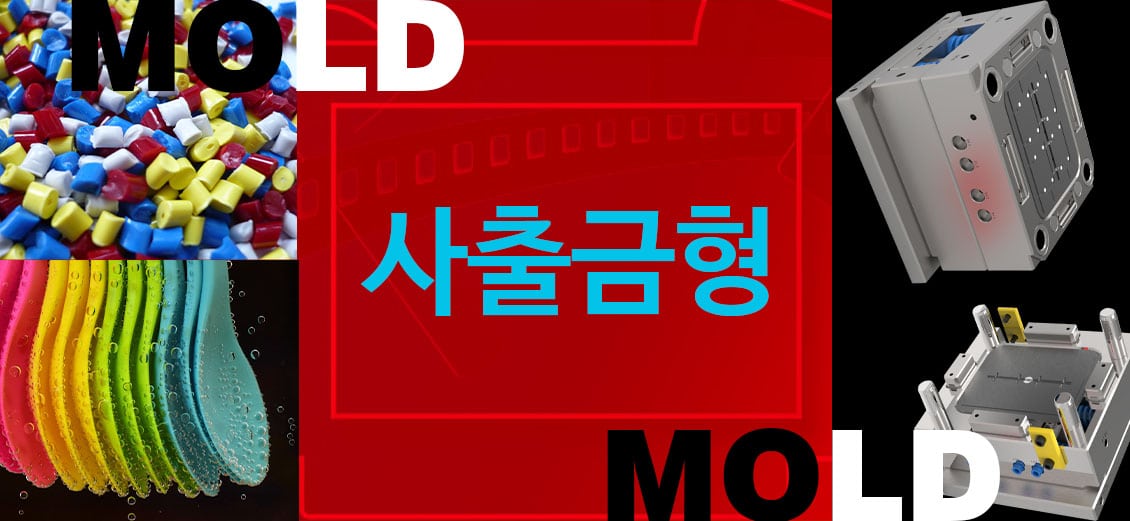
HOME → MOLD CATEGORIES →
사출 금형 5
제5장 사출 금형의 주요 부품
사출 금형의 주요 부품(PART)으로는 메인 플레이트, 유동 기구, 가이드 기구, 취출 기구 등이 있으며 각각의 부품의 규격은 KS 규격에 규정되어 있는 크기와 소요 재질, 열처리 강도 등에 준하여 제작되어야 합니다.
사출 금형의 구조와 주요 부품명을 먼저 확인해 보세요
1. 형판 코어 가이드 부품
(1) 메인 플레이트
사출 금형의 주요 부품 중 사출 금형용 메인 플레이트는 KS B 4151에 규정되어 있으며 고정측 및 가동측 형판, 받침판, 스트리퍼판이 여기에 속함
메인 플레이트는 SM50C, SM55C, SCM440, STC7 등의 재질을 사용하여 제작됨.
메인 플레이트를 가공할 경우에는 반드시 세 평면을 기준면으로 하여 표시해 놓아야 하며 외관 및 내부는 홈, 터짐, 녹 등과 같은 결함이 없고 다듬질 상태가 양호해야 함.
단위 : mm
메인 플레이트의 가공 기준면에 대한 정밀도는 다음과 같음.
항목 | 기준 | 정밀도 |
---|---|---|
평면도 | 300mm | 0.02㎛ |
평행도 | 300mm | 0.02㎛ |
직각도 | 300mm | 0.02㎛ |
표면거칠기 | – | 6.3S |
경도 | – | HB183 ~ HB235(Hs218 ~ Hs350) |
(2) 코어와 캐비티
코어와 캐비티는 성형품을 성형하는 사출 금형의 주요 부품으로서 성형품이 성형되는 개수에 따라 1 캐비티 금형, 2 캐비티 금형 등으로 지칭하기도 함.
캐비티는 유동 플라스틱이 유입되는 빈 공간이고 반대로 코어는 유동 플라스틱의 유입을 방해하는 구조물임.
캐비티를 형성하는 방식에는 일체식과 인서트식으로 나뉨.일체식은 고정측과 가동측 형판에 의해 캐비티를 이루는 것으로 성형품 한 개 뽑기 금형에 사용됨.
인서트식은 성형품을 다수 개 뽑기 금형에 사용되고 기계 가공을 간단하게 하기 위해 원형 또는 4각형으로 인서트를 제작하여 형판에 끼워맞춤하여 캐비티를 형성하는 것.
캐비티는 기계 가공이나 다듬질 가공을 쉽게 하기 위해 분할하거나 부분 입자를 사용하는 경우가 많음.
(3) 가이드 핀과 가이드 핀 부시
1) 가이드 핀
가이드 핀은 고정측과 가동측의 위치결정 및 안내와 금형을 보호하는 역할을 목적으로 하고 있고 A형과 B형으로 나뉨.
가이드 핀은 기름 홈을 만들어서 HrC 55 이상으로 열처리를 하고 가이드부의 길이는 가이드 핀 직경의 1.5 ~ 2배 정도로 하며 재질은 STC3 ~ 5, STC2, 또는 STB2 등을 사용함.
[A형]
[B형]
2) 가이드 핀 부시
가이드 핀 부시는 가이드 핀과 마찬가지로 A형과 B형으로 나뉘고 소요되는 재질은 STS3, STB2 등이 있음.
3) 금형 어긋남의 발생요인
연속 운전에 의해 맞춤 기구의 마모.
금형의 자체 중량에 의한 휨으로 특히 대형 금형에서 주로 발생.
금형 온도를 상승시킬 경우의 열팽창의 영향.
사출 압력에 의한 피로와 강도 부족.
플래시 발생에 의한 금형 손상.
☞ 금형 어긋남의 대책으로는 가이드 핀과 가이드 핀 부시를 테이퍼 맞춤을 하고 테이퍼 맞춤면의 각도는 10˚ ~ 20˚가 효과적이며 높이는 15mm 이상으로 하고 담금질을 해야 함.
2. 유동 기구 부품
(1) 로케이트 링
사출 금형의 주요 부품 중 로케트 링은 사출성형기의 노즐과 금형의 스프루 부시의 위치를 결정하는 역할을 하는 것으로 표준형인 A형과 여러 가지 특수한 형상이 있음.
소요되는 재질은 SM50C, SM55C, STC7 등이 있고 외관에 홈, 터짐, 녹 등의 결함이 없어야 하고 표면 거칠기는 6.3S로 해야 함.
[로케이트 링 적용예]
(2) 스프루 부시
1) 개요
스프루는 금형의 입구에 의하여 용용된 플라스틱을 러너 혹은 캐비티에 보내는 역할을 하고 한쪽은 사출성형기의 노즐과 연결하며 다른 한쪽은 금형의 러너 또는 성형품에 붙게 됨.
스프루의 외형은 노즐과 연결되는 부위는 부시가 되고 다른 한쪽은 고정측 형판이나 러너-스트리퍼판에 끼워 맞춰지는데 이를 스프루 부시라 함.
사출 시 스프루 부시에 사출 압력이 가해지므로 이를 견디기 위해서는 로케이트 링을 단 붙이기를 하여 스프루 부시를 눌러줘야 함.
스프루 부시의 내부는 R부에서 끝이 퍼진 테이퍼로 되어 있고 이 테이퍼는 크기가 클수록 스프루를 취출하기가 쉬워짐.
스프루 부시의 형상은 A, B, C, D, E형으로 나뉘고 가장 많이 사용되는 것이 A형(사이드 게이트용)과 B형(다이렉트 게이트용) 임.
2) 설계 시 유의사항
스프루 부시의 R은 노즐 선단 r보다 0.5 ~ 1mm 정도 크게 할 것.
스프루 입구의 지름 D는 노즐 구멍 지름 d보다 0.5 ~ 1mm 정도 크게 할 것.
스프루 길이는 될 수 있는 대로 짧게 하고 R은 설계자가 지정해 주는 경우가 많음.
스프루 구멍의 테이퍼는 2 ~ 4˚로 할 것.
스프루 부시는 HrC 40 이상으로 열처리를 할 것.
스프루 부시의 내면 거칠기는 1S ~ 6S로 하고 끝 다듬질을 할 때는 길이 방향으로 하여야 함.
러너-스트리퍼판의 스프루 부시 섭동부에 5 ~ 15˚의 각도를 부여하면 안정성이 좋고 작동이 원활해짐.
3. 이젝터 기구 부품
(1) 개요
이젝터는 성형품의 품질을 일정하게 유지하고 자동 성형을 가능하게끔 함.
이젝터 방법의 결정 방법
① 성형 재료와 제품의 형상.
② 게이트의 종류.
③ 상품의 가치.
④ 금형 구조.
이젝터는 성형품에 변형이나 흠, 균열을 주지 않고 확실하면서도 신속하게 이형이 되고 고장이 적어야 하며 보수가 쉬어야 함.
이젝터는 성형품이 취출되고 나서 금형이 닫힐 때 다른 부품과의 간섭이 일으키지 않고 원위치로 복귀해야 하는데 통상적으로 이젝터판에 설치되어 있는 4개의 리턴 핀에 의해서 복귀가 이루어짐.
(2) 이젝터 핀(밀핀)
1) 개요
이젝터 핀은 가장 간단한 이젝팅 방식이고 성형품의 임의의 위치에 설치할 수 있음.
이젝터 핀을 사용하는 이유
① 이젝터 핀 구멍은 가공하기 쉬움.
② 끝손질이나 정밀도도 쉽게 얻을 수 있음.
③ 금형의 수명도 긺.
④ 표준품을 사용하여 호환성이 좋음.
⑤ 파손 시 보수가 쉬움.
작은 면적으로 이젝팅이 되므로 이젝터 핀의 형상, 위치, 개수가 부적당하면 성형품의 외관에 스트레인, 균열, 백화 등의 불량이 발생함.
사용하는 재질로는 STC3 ~ 5, STS2, SCM1 등이 있음.
성형품의 상부에만 이젝터 핀을 설치하면 백화 현상의 원인이 되므로 성형품의 가장자리에 이젝터 핀을 설치하는 것이 좋고 성형품과 접촉 면적을 크게 해야 함.
2) 이젝터 핀 설치 시 고려사항
이젝터 핀을 배치할 때는 성형품의 이형 저항 밸런스가 유지되도록 할 것.
게이트 하부 및 게이트와 직선 방향의 밑부분에 설치하지 않을 것.
상품의 가치를 해치지 않는 곳에 설치할 것.
가스가 모이는 곳에 설치하여 가스 빼기 대용으로 사용할 것.
이젝터 핀과 구멍의 끼워맞춤공차는 H7/g6 정도로 할 것.
단붙이 이젝터 핀의 단붙이 지름부의 길이는 가능한 한 짧게 할 것.
이젝터 핀의 끼워맞춤부의 길이 X는 최소 X ≥ 15mm로 하고 단붙이 지름부의 표준 길이는 X + Y + (5 ~6mm) 정도로 할 것.
이젝터 핀의 담금질 경도는 HrC55 이상으로 할 것.
끼워맞춤부의 표면 거칠기는 3S로 할 것.
이젝터 핀과 성형품은 될 수 있는 대로 많이 접촉하도록 할 것.
성형품에 이젝터 핀 자국이 있어서는 안 될 경우에는 오버 플로 받이부를 이젝터부로 할 것.
이젝터 핀의 직경은 ∅12 ~ ∅16mm 정도가 한도이고 그 이상을 사용할 경우에는 이젝터 핀 선단을 접시 모양으로 만들어서 사용할 것.
얇은 살두께가 있는 성형품을 이젝팅할 경우에는 블레이드 핀을 사용할 것.
(3) 슬리브 이젝터
1) 개요
슬리브는 중앙에 긴 구멍이 뚫려 있는 부시 모양의 성형품, 구멍이 뚫려 있는 보스, 빠지기 어려운 가늘고 긴 코어가 있는 성형품 등을 밀어내는데 사용함.
슬리브의 단면으로 주위를 고르게 밀어내므로 이젝터 핀보다 성형품의 균열이나 백화현상을 방지하고 원활한 이젝팅을 할 수 있음.
사용하는 재질은 STC3 ~ 5, STS3, STB2, SCM1 등을 사용하도록 규정하고 있으나 STD61을 사용하여야 원활한 섭동에 의해 금형 사고를 방지할 수 있음.
2) 슬리브 이젝터의 설계 시 고려사항
슬리브의 살두께는 0.75mm 이상이 좋으며 가늘고 긴 경우에는 단붙이 슬리브로 할 것.
담금질 경도는 HrC55 이상으로 하고 질화 또는 경질 크롬 도금을 하는 것이 좋음.
슬리브의 코어 핀의 끼워맞춤 길이는 될 수 있는 대로 짧게 하고 슬리브의 최대 길이는 7 ~ 8 mm 여유를 가질 것.
[단 붙이 슬리브]
코어 핀은 선단부가 캐비티형으로 지지되도록 설계하여 코어의 편심을 방지할 것.
끼워맞춤부는 연삭을 하여 표면 거칠기를 3S로 할 것.
(4) 스트리퍼판 이젝터
1) 개요
스트리퍼판은 성형품의 전 둘레를 파팅 라인에 두고 균일하게 밀어내는 방식으로써 살두께가 얇고 이젝터 핀의 사용이 성형품의 나쁜 영향을 주거나 밀어낼 때 큰 저항이 있는 상자 모양이나 원통 모양의 성형품에 많이 사용됨.
스트리퍼 판은 가장 넓은 면적으로 밀어내므로 성형품의 변형, 균열, 백화 등이 발생하지 않음.
스트리퍼판으로 성형품을 밀어내기 때문에 취출 후에도 외관상에 이젝터 자국이 남지 않아서 투명 성형품 성형에 유리함.
스트리퍼판의 내면과 코어의 주위가 정밀하게 조립되지 않으면 플래시가 발생할 수 있음.
2) 스트리퍼 판 이젝터의 설계 시 고려사항
스트리퍼판의 내면과 코어의 외주면의 긁힘을 방지하기 위해 3˚ ~ 10˚의 구배를 줄 것.
스트리퍼판과 코어의 클리어런스는 0.02mm 정도로 할 것.
담금질 경도는 HrC55 정도로 할 것.
성형품의 파팅 라인이 복잡한 경우에는 스트리퍼판의 대용으로 링을 사용하기도 함.
(5) 에어 이젝터
1) 개요
컵과 같이 얇은 성형품은 이젝터 핀이나 스트리퍼판으로 이젝팅을 하면 성형품의 좌굴을 일으키고 성형품과 코어 사이가 진공상태가 되면 빼내기가 어려워 성형품이 파손될 수 있으므로 에어 이젝터로 빼내야 함.
특히 PE나 PP 등의 연질 재료를 사용하여 성형할 경우 더욱 두드러짐.
에어 이젝터는 성형품의 자동 낙하가 용이하여 자동 성형 작업이 가능함.
2) 에어 이젝터의 특징
리턴 핀이 필요 없어 금형 구조가 간단함.
코어형이든 캐비티형이든 어느 것에도 사용이 가능함.
형개 중의 임의의 위치에서 성형품을 밀어낼 수 있음.
이젝팅 시 성형품의 변형이 적음.
성형품과 코어 사이의 진공에 의한 문제점을 해소할 수 있음.
설치가 간단하고 공기가 누설되어도 성형품을 오염시키지 않으며 작업상에 위험이 없음.
성형품의 형상에 제약이 있지만 다른 이젝터 방식과 병행하여 사용할 수 있음.
냉각 회로를 설치할 수 없는 부위에 분사되는 공기가 냉각 효과도 겸할 수 있음.
압축 공기의 압력은 5 ~ 6(kg/㎠) 정도임.
에어 밸브의 리턴은 에어 실린더나 스프링을 이용함.
공기의 도피 회로가 있으면 이젝터 힘은 크게 감소함.
에어 밸브의 금형 접촉면은 비교적 넓어 강력한 성형압력을 받으므로 이에 대한 강도의 배려가 필요함.
4. 스프루와 러너의 이젝터 기구 부품
(1) 스프루 로크 핀
1) 개요
스프루 로크 핀은 이형 시 스프루 부시에서 스프루를 빼내기 위하여 선단부에 언더컷 형상으로 되어 있음.
스프루 로크 핀은 선단부 언더컷 형상에 따라 A형, B형, C형으로 나뉨.
사용되는 재질은 STC3 ~ STC5, SCM1 등이 있고 끼워맞춤부의 표면 거칠기는 3S로 하며 열처리 경도 HrC55 이상으로 해야 함.
2) 적용방법
(a)는 Z 핀부가 자동 낙하되도록 설치하여야 하고 주로 투명 성형품에 적합함.
(b)는 투명 성형품에 사용하지 않고 가동측 형판에 홈 가공이 필요함.
(c)도 투명 성형품에 사용하지 않고 가동측 형판에 역 테이퍼 가공이 필요함.
(d) 러너 핀을 스프루 로크 핀에 사용한 경우로써 스트리퍼판을 채택할 때 사용함.
(2) 러너 로크 핀
1) 개요
러너 로크 핀은 3매판 사출 금형에서 핀 포인트 게이트를 채택할 경우에 러너를 인장하고 성형품과 게이트를 분리하기 위해 사용함
러너 로크 핀은 선단의 형상에 따라 A형, B형, C형 등이 있고 사용되는 재질은 SRC3 ~ STC5, STS2, STS3, SCM1 이 있고 선단부 열처리 경도는 HrC50 이상임.
2) 적용방법
(a)는 가장 일반적인 사용방법으로 M5 나사는 금형 운반 중에 러너 로크 핀의 낙하를 방지함.
(b)는 러너 로크 핀을 스트리퍼판에 삽입한 경우임.
(c)는 형판의 금형 조여 붙이기용 나사 구멍에 맞을 경우에 사용됨.
(d)는 dH7부에 축은 f6 ~ f7, 구멍은 H7로써 끼워맞춤하는 것이 좋음.
(e)는 러너-스트리퍼판에 러너가 붙어서 낙하되지 않는 현상 때문에 러너 로크 핀과 러너-스트리퍼판의 섭동부는 핀 쪽으로 들어가면 안 됨.
(f)는 러너 로크 핀을 러너-스트리퍼판에서 돌출되도록 하여야 러너가 낙하될 수 있음.
이상으로 사출 금형의주요 부품 연재를 마치고 다음에는 사출 금형의 강도 계산 및 게이트와 러너에 대한 연재를 시작할 예정입니다.
2020년 07월 20일
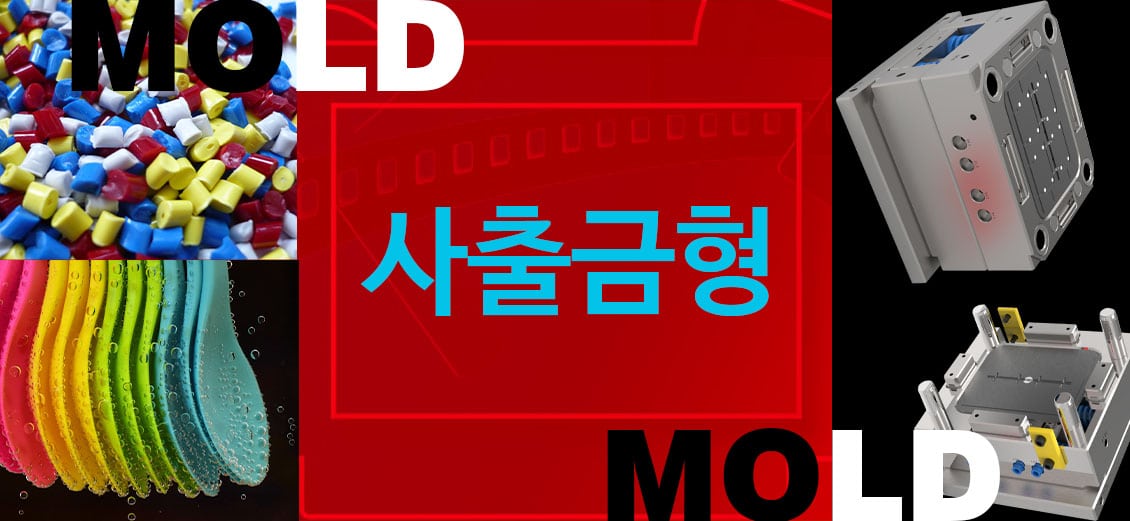
HOME → MOLD CATEGORIES →
사출 금형 5
제5장 사출 금형의 주요 부품
사출 금형의 주요 부품(PART)으로는 메인 플레이트, 유동 기구, 가이드 기구, 취출 기구 등이 있으며 각각의 부품의 규격은 KS 규격에 규정되어 있는 크기와 소요 재질, 열처리 강도 등에 준하여 제작되어야 합니다.
사출 금형의 구조와 주요 부품명을 먼저 확인해 보세요
1. 형판 코어 가이드 부품
(1) 메인 플레이트
사출 금형의 주요 부품 중 사출 금형용 메인 플레이트는 KS B 4151에 규정되어 있으며 고정측 및 가동측 형판, 받침판, 스트리퍼판이 여기에 속함
메인 플레이트는 SM50C, SM55C, SCM440, STC7 등의 재질을 사용하여 제작됨.
메인 플레이트를 가공할 경우에는 반드시 세 평면을 기준면으로 하여 표시해 놓아야 하며 외관 및 내부는 홈, 터짐, 녹 등과 같은 결함이 없고 다듬질 상태가 양호해야 함.
단위 : mm
메인 플레이트의 가공 기준면에 대한 정밀도는 다음과 같음.
항목 | 기준 | 정밀도 |
---|---|---|
평면도 | 300mm | 0.02㎛ |
평행도 | 300mm | 0.02㎛ |
직각도 | 300mm | 0.02㎛ |
표면거칠기 | – | 6.3S |
경도 | – | HB183 ~ HB235(Hs218 ~ Hs350) |
(2) 코어와 캐비티
코어와 캐비티는 성형품을 성형하는 사출 금형의 주요 부품으로서 성형품이 성형되는 개수에 따라 1 캐비티 금형, 2 캐비티 금형 등으로 지칭하기도 함.
캐비티는 유동 플라스틱이 유입되는 빈 공간이고 반대로 코어는 유동 플라스틱의 유입을 방해하는 구조물임.
캐비티를 형성하는 방식에는 일체식과 인서트식으로 나뉨.일체식은 고정측과 가동측 형판에 의해 캐비티를 이루는 것으로 성형품 한 개 뽑기 금형에 사용됨.
인서트식은 성형품을 다수 개 뽑기 금형에 사용되고 기계 가공을 간단하게 하기 위해 원형 또는 4각형으로 인서트를 제작하여 형판에 끼워맞춤하여 캐비티를 형성하는 것.
캐비티는 기계 가공이나 다듬질 가공을 쉽게 하기 위해 분할하거나 부분 입자를 사용하는 경우가 많음.
(3) 가이드 핀과 가이드 핀 부시
1) 가이드 핀
가이드 핀은 고정측과 가동측의 위치결정 및 안내와 금형을 보호하는 역할을 목적으로 하고 있고 A형과 B형으로 나뉨.
가이드 핀은 기름 홈을 만들어서 HrC 55 이상으로 열처리를 하고 가이드부의 길이는 가이드 핀 직경의 1.5 ~ 2배 정도로 하며 재질은 STC3 ~ 5, STC2, 또는 STB2 등을 사용함.
[A형]
[B형]
2) 가이드 핀 부시
가이드 핀 부시는 가이드 핀과 마찬가지로 A형과 B형으로 나뉘고 소요되는 재질은 STS3, STB2 등이 있음.
3) 금형 어긋남의 발생요인
연속 운전에 의해 맞춤 기구의 마모.
금형의 자체 중량에 의한 휨으로 특히 대형 금형에서 주로 발생.
금형 온도를 상승시킬 경우의 열팽창의 영향.
사출 압력에 의한 피로와 강도 부족.
플래시 발생에 의한 금형 손상.
☞ 금형 어긋남의 대책으로는 가이드 핀과 가이드 핀 부시를 테이퍼 맞춤을 하고 테이퍼 맞춤면의 각도는 10˚ ~ 20˚가 효과적이며 높이는 15mm 이상으로 하고 담금질을 해야 함.
2. 유동 기구 부품
(1) 로케이트 링
사출 금형의 주요 부품 중 로케트 링은 사출성형기의 노즐과 금형의 스프루 부시의 위치를 결정하는 역할을 하는 것으로 표준형인 A형과 여러 가지 특수한 형상이 있음.
소요되는 재질은 SM50C, SM55C, STC7 등이 있고 외관에 홈, 터짐, 녹 등의 결함이 없어야 하고 표면 거칠기는 6.3S로 해야 함.
[로케이트 링 적용예]
(2) 스프루 부시
1) 개요
스프루는 금형의 입구에 의하여 용용된 플라스틱을 러너 혹은 캐비티에 보내는 역할을 하고 한쪽은 사출성형기의 노즐과 연결하며 다른 한쪽은 금형의 러너 또는 성형품에 붙게 됨.
스프루의 외형은 노즐과 연결되는 부위는 부시가 되고 다른 한쪽은 고정측 형판이나 러너-스트리퍼판에 끼워 맞춰지는데 이를 스프루 부시라 함.
사출 시 스프루 부시에 사출 압력이 가해지므로 이를 견디기 위해서는 로케이트 링을 단 붙이기를 하여 스프루 부시를 눌러줘야 함.
스프루 부시의 내부는 R부에서 끝이 퍼진 테이퍼로 되어 있고 이 테이퍼는 크기가 클수록 스프루를 취출하기가 쉬워짐.
스프루 부시의 형상은 A, B, C, D, E형으로 나뉘고 가장 많이 사용되는 것이 A형(사이드 게이트용)과 B형(다이렉트 게이트용) 임.
2) 설계 시 유의사항
스프루 부시의 R은 노즐 선단 r보다 0.5 ~ 1mm 정도 크게 할 것.
스프루 입구의 지름 D는 노즐 구멍 지름 d보다 0.5 ~ 1mm 정도 크게 할 것.
스프루 길이는 될 수 있는 대로 짧게 하고 R은 설계자가 지정해 주는 경우가 많음.
스프루 구멍의 테이퍼는 2 ~ 4˚로 할 것.
스프루 부시는 HrC 40 이상으로 열처리를 할 것.
스프루 부시의 내면 거칠기는 1S ~ 6S로 하고 끝 다듬질을 할 때는 길이 방향으로 하여야 함.
러너-스트리퍼판의 스프루 부시 섭동부에 5 ~ 15˚의 각도를 부여하면 안정성이 좋고 작동이 원활해짐.
3. 이젝터 기구 부품
(1) 개요
이젝터는 성형품의 품질을 일정하게 유지하고 자동 성형을 가능하게끔 함.
이젝터 방법의 결정 방법
① 성형 재료와 제품의 형상.
② 게이트의 종류.
③ 상품의 가치.
④ 금형 구조.
이젝터는 성형품에 변형이나 흠, 균열을 주지 않고 확실하면서도 신속하게 이형이 되고 고장이 적어야 하며 보수가 쉬어야 함.
이젝터는 성형품이 취출되고 나서 금형이 닫힐 때 다른 부품과의 간섭이 일으키지 않고 원위치로 복귀해야 하는데 통상적으로 이젝터판에 설치되어 있는 4개의 리턴 핀에 의해서 복귀가 이루어짐.
(2) 이젝터 핀(밀핀)
1) 개요
이젝터 핀은 가장 간단한 이젝팅 방식이고 성형품의 임의의 위치에 설치할 수 있음.
이젝터 핀을 사용하는 이유
① 이젝터 핀 구멍은 가공하기 쉬움.
② 끝손질이나 정밀도도 쉽게 얻을 수 있음.
③ 금형의 수명도 긺.
④ 표준품을 사용하여 호환성이 좋음.
⑤ 파손 시 보수가 쉬움.
작은 면적으로 이젝팅이 되므로 이젝터 핀의 형상, 위치, 개수가 부적당하면 성형품의 외관에 스트레인, 균열, 백화 등의 불량이 발생함.
사용하는 재질로는 STC3 ~ 5, STS2, SCM1 등이 있음.
성형품의 상부에만 이젝터 핀을 설치하면 백화 현상의 원인이 되므로 성형품의 가장자리에 이젝터 핀을 설치하는 것이 좋고 성형품과 접촉 면적을 크게 해야 함.
2) 이젝터 핀 설치 시 고려사항
이젝터 핀을 배치할 때는 성형품의 이형 저항 밸런스가 유지되도록 할 것.
게이트 하부 및 게이트와 직선 방향의 밑부분에 설치하지 않을 것.
상품의 가치를 해치지 않는 곳에 설치할 것.
가스가 모이는 곳에 설치하여 가스 빼기 대용으로 사용할 것.
이젝터 핀과 구멍의 끼워맞춤공차는 H7/g6 정도로 할 것.
단붙이 이젝터 핀의 단붙이 지름부의 길이는 가능한 한 짧게 할 것.
이젝터 핀의 끼워맞춤부의 길이 X는 최소 X ≥ 15mm로 하고 단붙이 지름부의 표준 길이는 X + Y + (5 ~6mm) 정도로 할 것.
이젝터 핀의 담금질 경도는 HrC55 이상으로 할 것.
끼워맞춤부의 표면 거칠기는 3S로 할 것.
이젝터 핀과 성형품은 될 수 있는 대로 많이 접촉하도록 할 것.
성형품에 이젝터 핀 자국이 있어서는 안 될 경우에는 오버 플로 받이부를 이젝터부로 할 것.
이젝터 핀의 직경은 ∅12 ~ ∅16mm 정도가 한도이고 그 이상을 사용할 경우에는 이젝터 핀 선단을 접시 모양으로 만들어서 사용할 것.
얇은 살두께가 있는 성형품을 이젝팅할 경우에는 블레이드 핀을 사용할 것.
(3) 슬리브 이젝터
1) 개요
슬리브는 중앙에 긴 구멍이 뚫려 있는 부시 모양의 성형품, 구멍이 뚫려 있는 보스, 빠지기 어려운 가늘고 긴 코어가 있는 성형품 등을 밀어내는데 사용함.
슬리브의 단면으로 주위를 고르게 밀어내므로 이젝터 핀보다 성형품의 균열이나 백화현상을 방지하고 원활한 이젝팅을 할 수 있음.
사용하는 재질은 STC3 ~ 5, STS3, STB2, SCM1 등을 사용하도록 규정하고 있으나 STD61을 사용하여야 원활한 섭동에 의해 금형 사고를 방지할 수 있음.
2) 슬리브 이젝터의 설계 시 고려사항
슬리브의 살두께는 0.75mm 이상이 좋으며 가늘고 긴 경우에는 단붙이 슬리브로 할 것.
담금질 경도는 HrC55 이상으로 하고 질화 또는 경질 크롬 도금을 하는 것이 좋음.
슬리브의 코어 핀의 끼워맞춤 길이는 될 수 있는 대로 짧게 하고 슬리브의 최대 길이는 7 ~ 8 mm 여유를 가질 것.
[단 붙이 슬리브]
코어 핀은 선단부가 캐비티형으로 지지되도록 설계하여 코어의 편심을 방지할 것.
끼워맞춤부는 연삭을 하여 표면 거칠기를 3S로 할 것.
(4) 스트리퍼판 이젝터
1) 개요
스트리퍼판은 성형품의 전 둘레를 파팅 라인에 두고 균일하게 밀어내는 방식으로써 살두께가 얇고 이젝터 핀의 사용이 성형품의 나쁜 영향을 주거나 밀어낼 때 큰 저항이 있는 상자 모양이나 원통 모양의 성형품에 많이 사용됨.
스트리퍼 판은 가장 넓은 면적으로 밀어내므로 성형품의 변형, 균열, 백화 등이 발생하지 않음.
스트리퍼판으로 성형품을 밀어내기 때문에 취출 후에도 외관상에 이젝터 자국이 남지 않아서 투명 성형품 성형에 유리함.
스트리퍼판의 내면과 코어의 주위가 정밀하게 조립되지 않으면 플래시가 발생할 수 있음.
2) 스트리퍼 판 이젝터의 설계 시 고려사항
스트리퍼판의 내면과 코어의 외주면의 긁힘을 방지하기 위해 3˚ ~ 10˚의 구배를 줄 것.
스트리퍼판과 코어의 클리어런스는 0.02mm 정도로 할 것.
담금질 경도는 HrC55 정도로 할 것.
성형품의 파팅 라인이 복잡한 경우에는 스트리퍼판의 대용으로 링을 사용하기도 함.
(5) 에어 이젝터
1) 개요
컵과 같이 얇은 성형품은 이젝터 핀이나 스트리퍼판으로 이젝팅을 하면 성형품의 좌굴을 일으키고 성형품과 코어 사이가 진공상태가 되면 빼내기가 어려워 성형품이 파손될 수 있으므로 에어 이젝터로 빼내야 함.
특히 PE나 PP 등의 연질 재료를 사용하여 성형할 경우 더욱 두드러짐.
에어 이젝터는 성형품의 자동 낙하가 용이하여 자동 성형 작업이 가능함.
2) 에어 이젝터의 특징
리턴 핀이 필요 없어 금형 구조가 간단함.
코어형이든 캐비티형이든 어느 것에도 사용이 가능함.
형개 중의 임의의 위치에서 성형품을 밀어낼 수 있음.
이젝팅 시 성형품의 변형이 적음.
성형품과 코어 사이의 진공에 의한 문제점을 해소할 수 있음.
설치가 간단하고 공기가 누설되어도 성형품을 오염시키지 않으며 작업상에 위험이 없음.
성형품의 형상에 제약이 있지만 다른 이젝터 방식과 병행하여 사용할 수 있음.
냉각 회로를 설치할 수 없는 부위에 분사되는 공기가 냉각 효과도 겸할 수 있음.
압축 공기의 압력은 5 ~ 6(kg/㎠) 정도임.
에어 밸브의 리턴은 에어 실린더나 스프링을 이용함.
공기의 도피 회로가 있으면 이젝터 힘은 크게 감소함.
에어 밸브의 금형 접촉면은 비교적 넓어 강력한 성형압력을 받으므로 이에 대한 강도의 배려가 필요함.
4. 스프루와 러너의 이젝터 기구 부품
(1) 스프루 로크 핀
1) 개요
스프루 로크 핀은 이형 시 스프루 부시에서 스프루를 빼내기 위하여 선단부에 언더컷 형상으로 되어 있음.
스프루 로크 핀은 선단부 언더컷 형상에 따라 A형, B형, C형으로 나뉨.
사용되는 재질은 STC3 ~ STC5, SCM1 등이 있고 끼워맞춤부의 표면 거칠기는 3S로 하며 열처리 경도 HrC55 이상으로 해야 함.
2) 적용방법
(a)는 Z 핀부가 자동 낙하되도록 설치하여야 하고 주로 투명 성형품에 적합함.
(b)는 투명 성형품에 사용하지 않고 가동측 형판에 홈 가공이 필요함.
(c)도 투명 성형품에 사용하지 않고 가동측 형판에 역 테이퍼 가공이 필요함.
(d) 러너 핀을 스프루 로크 핀에 사용한 경우로써 스트리퍼판을 채택할 때 사용함.
(2) 러너 로크 핀
1) 개요
러너 로크 핀은 3매판 사출 금형에서 핀 포인트 게이트를 채택할 경우에 러너를 인장하고 성형품과 게이트를 분리하기 위해 사용함
러너 로크 핀은 선단의 형상에 따라 A형, B형, C형 등이 있고 사용되는 재질은 SRC3 ~ STC5, STS2, STS3, SCM1 이 있고 선단부 열처리 경도는 HrC50 이상임.
2) 적용방법
(a)는 가장 일반적인 사용방법으로 M5 나사는 금형 운반 중에 러너 로크 핀의 낙하를 방지함.
(b)는 러너 로크 핀을 스트리퍼판에 삽입한 경우임.
(c)는 형판의 금형 조여 붙이기용 나사 구멍에 맞을 경우에 사용됨.
(d)는 dH7부에 축은 f6 ~ f7, 구멍은 H7로써 끼워맞춤하는 것이 좋음.
(e)는 러너-스트리퍼판에 러너가 붙어서 낙하되지 않는 현상 때문에 러너 로크 핀과 러너-스트리퍼판의 섭동부는 핀 쪽으로 들어가면 안 됨.
(f)는 러너 로크 핀을 러너-스트리퍼판에서 돌출되도록 하여야 러너가 낙하될 수 있음.
이상으로 사출 금형의주요 부품 연재를 마치고 다음에는 사출 금형의 강도 계산 및 게이트와 러너에 대한 연재를 시작할 예정입니다.
2020년 07월 20일
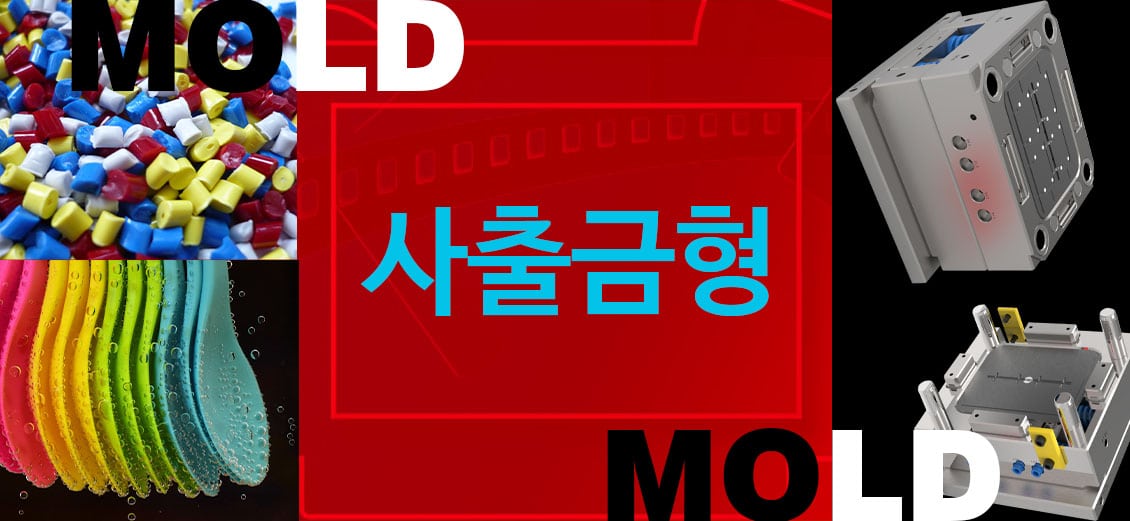
HOME → MOLD CATEGORIES →
사출 금형 5
제5장 사출 금형의 주요 부품
사출 금형의 주요 부품(PART)으로는 메인 플레이트, 유동 기구, 가이드 기구, 취출 기구 등이 있으며 각각의 부품의 규격은 KS 규격에 규정되어 있는 크기와 소요 재질, 열처리 강도 등에 준하여 제작되어야 합니다.
사출 금형의 구조와 주요 부품명을 먼저 확인해 보세요
1. 형판 코어 가이드 부품
(1) 메인 플레이트
사출 금형의 주요 부품 중 사출 금형용 메인 플레이트는 KS B 4151에 규정되어 있으며 고정측 및 가동측 형판, 받침판, 스트리퍼판이 여기에 속함
메인 플레이트는 SM50C, SM55C, SCM440, STC7 등의 재질을 사용하여 제작됨.
메인 플레이트를 가공할 경우에는 반드시 세 평면을 기준면으로 하여 표시해 놓아야 하며 외관 및 내부는 홈, 터짐, 녹 등과 같은 결함이 없고 다듬질 상태가 양호해야 함.
단위 : mm
메인 플레이트의 가공 기준면에 대한 정밀도는 다음과 같음.
항목 | 기준 | 정밀도 |
---|---|---|
평면도 | 300mm | 0.02㎛ |
평행도 | 300mm | 0.02㎛ |
직각도 | 300mm | 0.02㎛ |
표면거칠기 | – | 6.3S |
경도 | – | HB183 ~ HB235(Hs218 ~ Hs350) |
(2) 코어와 캐비티
코어와 캐비티는 성형품을 성형하는 사출 금형의 주요 부품으로서 성형품이 성형되는 개수에 따라 1 캐비티 금형, 2 캐비티 금형 등으로 지칭하기도 함.
캐비티는 유동 플라스틱이 유입되는 빈 공간이고 반대로 코어는 유동 플라스틱의 유입을 방해하는 구조물임.
캐비티를 형성하는 방식에는 일체식과 인서트식으로 나뉨.일체식은 고정측과 가동측 형판에 의해 캐비티를 이루는 것으로 성형품 한 개 뽑기 금형에 사용됨.
인서트식은 성형품을 다수 개 뽑기 금형에 사용되고 기계 가공을 간단하게 하기 위해 원형 또는 4각형으로 인서트를 제작하여 형판에 끼워맞춤하여 캐비티를 형성하는 것.
캐비티는 기계 가공이나 다듬질 가공을 쉽게 하기 위해 분할하거나 부분 입자를 사용하는 경우가 많음.
(3) 가이드 핀과 가이드 핀 부시
1) 가이드 핀
가이드 핀은 고정측과 가동측의 위치결정 및 안내와 금형을 보호하는 역할을 목적으로 하고 있고 A형과 B형으로 나뉨.
가이드 핀은 기름 홈을 만들어서 HrC 55 이상으로 열처리를 하고 가이드부의 길이는 가이드 핀 직경의 1.5 ~ 2배 정도로 하며 재질은 STC3 ~ 5, STC2, 또는 STB2 등을 사용함.
[A형]
[B형]
2) 가이드 핀 부시
가이드 핀 부시는 가이드 핀과 마찬가지로 A형과 B형으로 나뉘고 소요되는 재질은 STS3, STB2 등이 있음.
3) 금형 어긋남의 발생요인
연속 운전에 의해 맞춤 기구의 마모.
금형의 자체 중량에 의한 휨으로 특히 대형 금형에서 주로 발생.
금형 온도를 상승시킬 경우의 열팽창의 영향.
사출 압력에 의한 피로와 강도 부족.
플래시 발생에 의한 금형 손상.
☞ 금형 어긋남의 대책으로는 가이드 핀과 가이드 핀 부시를 테이퍼 맞춤을 하고 테이퍼 맞춤면의 각도는 10˚ ~ 20˚가 효과적이며 높이는 15mm 이상으로 하고 담금질을 해야 함.
2. 유동 기구 부품
(1) 로케이트 링
사출 금형의 주요 부품 중 로케트 링은 사출성형기의 노즐과 금형의 스프루 부시의 위치를 결정하는 역할을 하는 것으로 표준형인 A형과 여러 가지 특수한 형상이 있음.
소요되는 재질은 SM50C, SM55C, STC7 등이 있고 외관에 홈, 터짐, 녹 등의 결함이 없어야 하고 표면 거칠기는 6.3S로 해야 함.
[로케이트 링 적용예]
(2) 스프루 부시
1) 개요
스프루는 금형의 입구에 의하여 용용된 플라스틱을 러너 혹은 캐비티에 보내는 역할을 하고 한쪽은 사출성형기의 노즐과 연결하며 다른 한쪽은 금형의 러너 또는 성형품에 붙게 됨.
스프루의 외형은 노즐과 연결되는 부위는 부시가 되고 다른 한쪽은 고정측 형판이나 러너-스트리퍼판에 끼워 맞춰지는데 이를 스프루 부시라 함.
사출 시 스프루 부시에 사출 압력이 가해지므로 이를 견디기 위해서는 로케이트 링을 단 붙이기를 하여 스프루 부시를 눌러줘야 함.
스프루 부시의 내부는 R부에서 끝이 퍼진 테이퍼로 되어 있고 이 테이퍼는 크기가 클수록 스프루를 취출하기가 쉬워짐.
스프루 부시의 형상은 A, B, C, D, E형으로 나뉘고 가장 많이 사용되는 것이 A형(사이드 게이트용)과 B형(다이렉트 게이트용) 임.
2) 설계 시 유의사항
스프루 부시의 R은 노즐 선단 r보다 0.5 ~ 1mm 정도 크게 할 것.
스프루 입구의 지름 D는 노즐 구멍 지름 d보다 0.5 ~ 1mm 정도 크게 할 것.
스프루 길이는 될 수 있는 대로 짧게 하고 R은 설계자가 지정해 주는 경우가 많음.
스프루 구멍의 테이퍼는 2 ~ 4˚로 할 것.
스프루 부시는 HrC 40 이상으로 열처리를 할 것.
스프루 부시의 내면 거칠기는 1S ~ 6S로 하고 끝 다듬질을 할 때는 길이 방향으로 하여야 함.
러너-스트리퍼판의 스프루 부시 섭동부에 5 ~ 15˚의 각도를 부여하면 안정성이 좋고 작동이 원활해짐.
3. 이젝터 기구 부품
(1) 개요
이젝터는 성형품의 품질을 일정하게 유지하고 자동 성형을 가능하게끔 함.
이젝터 방법의 결정 방법
① 성형 재료와 제품의 형상.
② 게이트의 종류.
③ 상품의 가치.
④ 금형 구조.
이젝터는 성형품에 변형이나 흠, 균열을 주지 않고 확실하면서도 신속하게 이형이 되고 고장이 적어야 하며 보수가 쉬어야 함.
이젝터는 성형품이 취출되고 나서 금형이 닫힐 때 다른 부품과의 간섭이 일으키지 않고 원위치로 복귀해야 하는데 통상적으로 이젝터판에 설치되어 있는 4개의 리턴 핀에 의해서 복귀가 이루어짐.
(2) 이젝터 핀(밀핀)
1) 개요
이젝터 핀은 가장 간단한 이젝팅 방식이고 성형품의 임의의 위치에 설치할 수 있음.
이젝터 핀을 사용하는 이유
① 이젝터 핀 구멍은 가공하기 쉬움.
② 끝손질이나 정밀도도 쉽게 얻을 수 있음.
③ 금형의 수명도 긺.
④ 표준품을 사용하여 호환성이 좋음.
⑤ 파손 시 보수가 쉬움.
작은 면적으로 이젝팅이 되므로 이젝터 핀의 형상, 위치, 개수가 부적당하면 성형품의 외관에 스트레인, 균열, 백화 등의 불량이 발생함.
사용하는 재질로는 STC3 ~ 5, STS2, SCM1 등이 있음.
성형품의 상부에만 이젝터 핀을 설치하면 백화 현상의 원인이 되므로 성형품의 가장자리에 이젝터 핀을 설치하는 것이 좋고 성형품과 접촉 면적을 크게 해야 함.
2) 이젝터 핀 설치 시 고려사항
이젝터 핀을 배치할 때는 성형품의 이형 저항 밸런스가 유지되도록 할 것.
게이트 하부 및 게이트와 직선 방향의 밑부분에 설치하지 않을 것.
상품의 가치를 해치지 않는 곳에 설치할 것.
가스가 모이는 곳에 설치하여 가스 빼기 대용으로 사용할 것.
이젝터 핀과 구멍의 끼워맞춤공차는 H7/g6 정도로 할 것.
단붙이 이젝터 핀의 단붙이 지름부의 길이는 가능한 한 짧게 할 것.
이젝터 핀의 끼워맞춤부의 길이 X는 최소 X ≥ 15mm로 하고 단붙이 지름부의 표준 길이는 X + Y + (5 ~6mm) 정도로 할 것.
이젝터 핀의 담금질 경도는 HrC55 이상으로 할 것.
끼워맞춤부의 표면 거칠기는 3S로 할 것.
이젝터 핀과 성형품은 될 수 있는 대로 많이 접촉하도록 할 것.
성형품에 이젝터 핀 자국이 있어서는 안 될 경우에는 오버 플로 받이부를 이젝터부로 할 것.
이젝터 핀의 직경은 ∅12 ~ ∅16mm 정도가 한도이고 그 이상을 사용할 경우에는 이젝터 핀 선단을 접시 모양으로 만들어서 사용할 것.
얇은 살두께가 있는 성형품을 이젝팅할 경우에는 블레이드 핀을 사용할 것.
(3) 슬리브 이젝터
1) 개요
슬리브는 중앙에 긴 구멍이 뚫려 있는 부시 모양의 성형품, 구멍이 뚫려 있는 보스, 빠지기 어려운 가늘고 긴 코어가 있는 성형품 등을 밀어내는데 사용함.
슬리브의 단면으로 주위를 고르게 밀어내므로 이젝터 핀보다 성형품의 균열이나 백화현상을 방지하고 원활한 이젝팅을 할 수 있음.
사용하는 재질은 STC3 ~ 5, STS3, STB2, SCM1 등을 사용하도록 규정하고 있으나 STD61을 사용하여야 원활한 섭동에 의해 금형 사고를 방지할 수 있음.
2) 슬리브 이젝터의 설계 시 고려사항
슬리브의 살두께는 0.75mm 이상이 좋으며 가늘고 긴 경우에는 단붙이 슬리브로 할 것.
담금질 경도는 HrC55 이상으로 하고 질화 또는 경질 크롬 도금을 하는 것이 좋음.
슬리브의 코어 핀의 끼워맞춤 길이는 될 수 있는 대로 짧게 하고 슬리브의 최대 길이는 7 ~ 8 mm 여유를 가질 것.
[단 붙이 슬리브]
코어 핀은 선단부가 캐비티형으로 지지되도록 설계하여 코어의 편심을 방지할 것.
끼워맞춤부는 연삭을 하여 표면 거칠기를 3S로 할 것.
(4) 스트리퍼판 이젝터
1) 개요
스트리퍼판은 성형품의 전 둘레를 파팅 라인에 두고 균일하게 밀어내는 방식으로써 살두께가 얇고 이젝터 핀의 사용이 성형품의 나쁜 영향을 주거나 밀어낼 때 큰 저항이 있는 상자 모양이나 원통 모양의 성형품에 많이 사용됨.
스트리퍼 판은 가장 넓은 면적으로 밀어내므로 성형품의 변형, 균열, 백화 등이 발생하지 않음.
스트리퍼판으로 성형품을 밀어내기 때문에 취출 후에도 외관상에 이젝터 자국이 남지 않아서 투명 성형품 성형에 유리함.
스트리퍼판의 내면과 코어의 주위가 정밀하게 조립되지 않으면 플래시가 발생할 수 있음.
2) 스트리퍼 판 이젝터의 설계 시 고려사항
스트리퍼판의 내면과 코어의 외주면의 긁힘을 방지하기 위해 3˚ ~ 10˚의 구배를 줄 것.
스트리퍼판과 코어의 클리어런스는 0.02mm 정도로 할 것.
담금질 경도는 HrC55 정도로 할 것.
성형품의 파팅 라인이 복잡한 경우에는 스트리퍼판의 대용으로 링을 사용하기도 함.
(5) 에어 이젝터
1) 개요
컵과 같이 얇은 성형품은 이젝터 핀이나 스트리퍼판으로 이젝팅을 하면 성형품의 좌굴을 일으키고 성형품과 코어 사이가 진공상태가 되면 빼내기가 어려워 성형품이 파손될 수 있으므로 에어 이젝터로 빼내야 함.
특히 PE나 PP 등의 연질 재료를 사용하여 성형할 경우 더욱 두드러짐.
에어 이젝터는 성형품의 자동 낙하가 용이하여 자동 성형 작업이 가능함.
2) 에어 이젝터의 특징
리턴 핀이 필요 없어 금형 구조가 간단함.
코어형이든 캐비티형이든 어느 것에도 사용이 가능함.
형개 중의 임의의 위치에서 성형품을 밀어낼 수 있음.
이젝팅 시 성형품의 변형이 적음.
성형품과 코어 사이의 진공에 의한 문제점을 해소할 수 있음.
설치가 간단하고 공기가 누설되어도 성형품을 오염시키지 않으며 작업상에 위험이 없음.
성형품의 형상에 제약이 있지만 다른 이젝터 방식과 병행하여 사용할 수 있음.
냉각 회로를 설치할 수 없는 부위에 분사되는 공기가 냉각 효과도 겸할 수 있음.
압축 공기의 압력은 5 ~ 6(kg/㎠) 정도임.
에어 밸브의 리턴은 에어 실린더나 스프링을 이용함.
공기의 도피 회로가 있으면 이젝터 힘은 크게 감소함.
에어 밸브의 금형 접촉면은 비교적 넓어 강력한 성형압력을 받으므로 이에 대한 강도의 배려가 필요함.
4. 스프루와 러너의 이젝터 기구 부품
(1) 스프루 로크 핀
1) 개요
스프루 로크 핀은 이형 시 스프루 부시에서 스프루를 빼내기 위하여 선단부에 언더컷 형상으로 되어 있음.
스프루 로크 핀은 선단부 언더컷 형상에 따라 A형, B형, C형으로 나뉨.
사용되는 재질은 STC3 ~ STC5, SCM1 등이 있고 끼워맞춤부의 표면 거칠기는 3S로 하며 열처리 경도 HrC55 이상으로 해야 함.
2) 적용방법
(a)는 Z 핀부가 자동 낙하되도록 설치하여야 하고 주로 투명 성형품에 적합함.
(b)는 투명 성형품에 사용하지 않고 가동측 형판에 홈 가공이 필요함.
(c)도 투명 성형품에 사용하지 않고 가동측 형판에 역 테이퍼 가공이 필요함.
(d) 러너 핀을 스프루 로크 핀에 사용한 경우로써 스트리퍼판을 채택할 때 사용함.
(2) 러너 로크 핀
1) 개요
러너 로크 핀은 3매판 사출 금형에서 핀 포인트 게이트를 채택할 경우에 러너를 인장하고 성형품과 게이트를 분리하기 위해 사용함
러너 로크 핀은 선단의 형상에 따라 A형, B형, C형 등이 있고 사용되는 재질은 SRC3 ~ STC5, STS2, STS3, SCM1 이 있고 선단부 열처리 경도는 HrC50 이상임.
2) 적용방법
(a)는 가장 일반적인 사용방법으로 M5 나사는 금형 운반 중에 러너 로크 핀의 낙하를 방지함.
(b)는 러너 로크 핀을 스트리퍼판에 삽입한 경우임.
(c)는 형판의 금형 조여 붙이기용 나사 구멍에 맞을 경우에 사용됨.
(d)는 dH7부에 축은 f6 ~ f7, 구멍은 H7로써 끼워맞춤하는 것이 좋음.
(e)는 러너-스트리퍼판에 러너가 붙어서 낙하되지 않는 현상 때문에 러너 로크 핀과 러너-스트리퍼판의 섭동부는 핀 쪽으로 들어가면 안 됨.
(f)는 러너 로크 핀을 러너-스트리퍼판에서 돌출되도록 하여야 러너가 낙하될 수 있음.
이상으로 사출 금형의주요 부품 연재를 마치고 다음에는 사출 금형의 강도 계산 및 게이트와 러너에 대한 연재를 시작할 예정입니다.
2020년 07월 20일